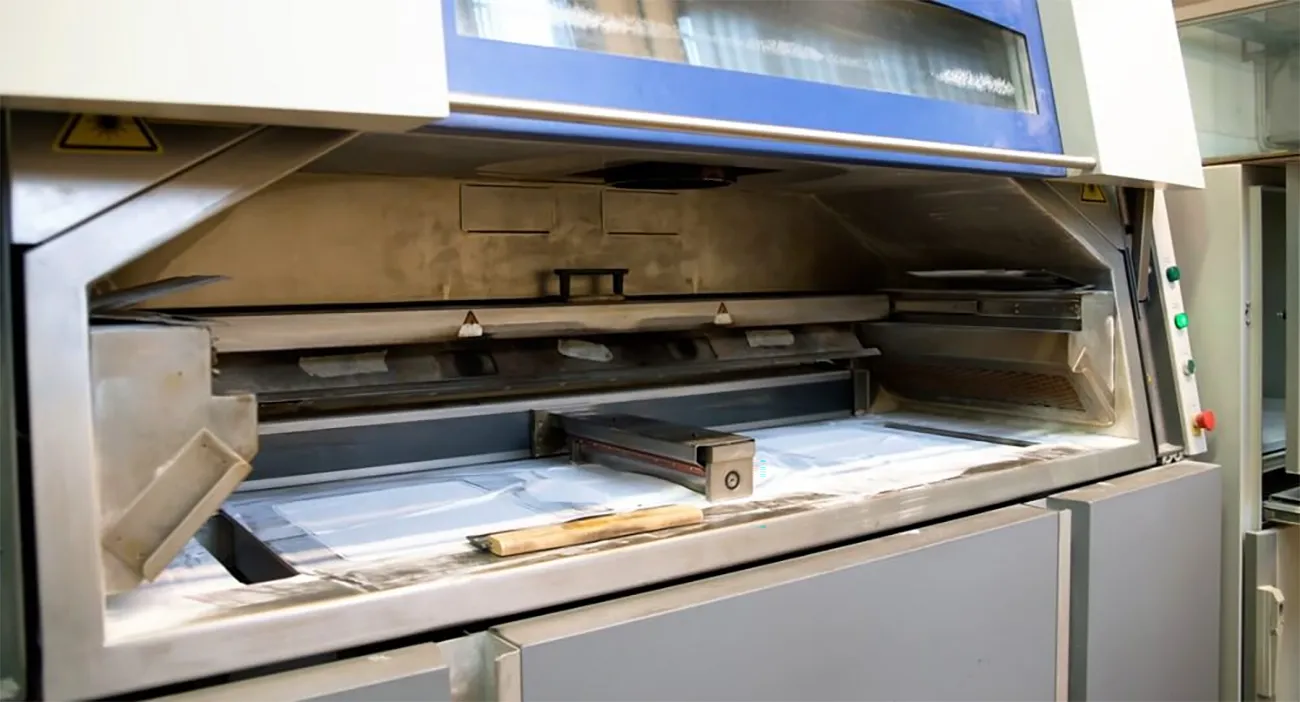
In unserem Artikel Toleranzen und Genauigkeiten im 3D-Druck haben wir allgemeine Hinweise gegeben, was in Punkto Toleranz beim 3D-Druck zu beachten ist. Da insbesondere beim Lasersintern bei Toleranzen und Genauigkeit immer wieder Fragen auftauchen, möchten wir uns in diesem Beitrag ganz diesem Thema widmen.
Erfahren Sie in diesem Beitrag:
- Wann Schrumpfungen auftreten und wie sich diese auswirken
- Mit welchen Krümmungen beim Lasersintern zu rechnen ist
- Rundungen insbesodnere bei Löchern ung Öffnungen
- Was bei der Oberfläche zu beachten ist
- Wie sich spitze Winkel beim Lasersintern (SLS) verhalten
Haben Sie Anmerkungen oder Fragen? Kontaktieren Sie uns über unser Formular oder Telefonisch unter +49 (0) 3641 22591 000.
Schrumpfungen
Bereits vor dem Lasersinter-Druck wird berechnet, um welches Maß das Werkstück schrumpfen könnte. Bei größeren Modellen kann dies sehr komplex sein, da nicht alle Bereiche des Modells gleich lang erhitzt werden. Generell hat die obere Seite weniger Zeit zum Abkühlen als die untere. Deswegen sind v.a. dicke solide Objekte mit einem Durchmesser von mehr als 10 cm von Schrumpfungen betroffen.
Dadurch können zweierlei Probleme entstehen:
Schrumpfungen bei massiven Objekten (große solide Bauteile, > 10 cm Durchmesser)
Wenn pro Schicht die Fläche des Modells zu groß ist (mehr als 8-10 cm Durchmesser), ist dementsprechend auch mehr gesintertes Pulver vorhanden. Diese Objekte ziehen sich eher zusammen als dünnere Objekte. Um dem entgegenzuwirken, werden die Werkstücke ausgehöhlt und das ungesinterte Pulver im Inneren belassen. Das Ergebnis hat dieselben Eigenschaften wie ein ausgefülltes solides Teil, aber den Vorteil, dass es nicht so sehr schrumpft.
Krümmungen bei großen, flachen und rechteckigen Bauteilen (größer als 10 cm)
Außenflächen kühlen nach dem Lasersinter-Prozess schneller als der Kern des Bauteils und kontrahieren früher. Somit schrumpfen die Ecken auf den unteren Bereichen mehr als in der Mitte, wodurch kleine Kurven am unteren Ende entstehen. Bei kleineren Werkstücken merkt man dies kaum. Um dies bei größeren Objekten zu vermeiden, können Platzhalter an den Ecken der Teile platziert werden. Diese sind solide und somit heiß, wodurch das Material weniger schrumpft. Dadurch können genauere Ergebnisse erzielt werden.
Krümmungen
Wie bei jedem Wärmeprozess, kann es auch beim 3D-Druck von flachen Werkstücken, zu Krümmungen kommen. Als Beispiel könnte man ein 1 mm DIN-A4-Blatt nehmen, das nach dem Vorgang womöglich an den Enden gekrümmt sein würde. Um dies zu verhindern, können die Objekte wieder erwärmt und kalt geklemmt werden. Jedoch sollte beachtet werden, dass dieser Vorgang nicht bei allen Werkstücken vorgenommen werden kann, da sich nicht alle Objekte klemmen lassen.
Löcher und Rundungen
Rundheit
Löcher, die der Z-Achse zugewandt sind, sind generell rund, da der Laser einen ziemlich genauen Kreis zeichnen kann. Bei Löchern, kleiner als 2 mm, kann Pulver im Inneren eingeschlossen werden. Selbst wenn es nicht dazu kommt, dass das Pulver gesintert wird, kann es sein, dass es so sehr erhitzt wurde, dass es fest wird. Damit ist es schwierig zu entfernen. Hier empfiehlt es sich mit einem feinen Bohrer zu arbeiten.
Löcher, die die Z-Achse kreuzen, sind elliptisch, insbesondere, wenn sie klein sind (kleiner als 5 mm). Weil das Loch von geraden Linien (den Schichten) aufgebaut wird und somit kein vollkommener Kreis entstehen kann (vergleichbar mit dem Versuch, aus geraden rechteckigen Bausteinen einen Kreis aufzubauen). Die Löcher sind oben elliptischer als unten, da der Laser tiefer durch neues Pulver schneidet, als durch gesintertes. Durch einen sogenannten Z-Ausgleichkönnen, die nach unten gerichteten Flächen, um einige Zehntel Millimeter erhöht werden. Da es dadurch aber immer noch nicht perfekt ist, sollte auch hier wieder mit einem Bohrer nachgearbeitet werden.
Tiefe Löcher
Löcher mit kleinem Durchmesser, die tief in einem festen Teil verlaufen, werden oft mit Pulver verstopft. Die soliden Bereiche strahlen dann Wärme aus, woraufhin das Pulver fest wird und nur schwer entfernt werden kann.
Vor allem bei Löchern, die < 5 mm Durchmesser aufweisen, kann dies ein größeres Problem darstellen. Hier gibt es leider nicht viel zu tun, als wieder am Ende mit einem Bohrer nachzuarbeiten.
Oberfläche
Oberflächenpulver
Die Werkstücke kommen zusammen mit einem Pulvermantel aus der Maschine. Mit Hilfe einer Bürste und eines Luftkompressors kann dieses Pulver entfernt werden. Falls an einigen kleinen Stellen Pulver in Löchern übriggeblieben sein sollte, kann man es mit warmem Seifenwasser abgespülen, oder es aus den Vertiefungen herausgekratzen.
Oberflächendetails
Es kann sein, dass zu filigrane Oberflächendetails, beim Druck nicht umgesetzt werden können. Deswegen sollte für Details ein Minimum zwischen 0,4 mm und 0,5 mm eingehalten werden.
Winkel
Bei einem Modell mit scharfen Kanten, kann es zu Ungenauigkeiten bei der Darstellung kommen. Der Grund dafür ist, dass das zu druckende Objekt in 0,1 mm dicke Querschnitte unterteilt werden muss. So kann es vorkommen, dass sehr spitze Winkel nicht vollständig dargestellt werden können. Dies können Sie vermeiden, wenn Sie die Kante in ein flaches Ende umformen, es sollte mindestens 0,4 mm stark sein.
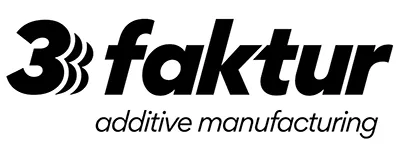
Über 3Faktur: 3Faktur ist Spezialist für 3D-Druck, Rapid Prototyping und Rapid Manufacturing. Wir arbeiten mit dem Multi Jet Fusion-Verfahren von HP und bieten unterschiedliche Materialien für den Prototypenbau und die Serienproduktion an. Sollten Sie Fragen zu Ihrem Projekt haben, können Sie uns gern kontaktieren.