Die bisherigen Kapitel beschäftigten sich mit dem DfMJF unter dem Aspekt der Optimierung der Funktionalitäten der Bauteile und den grundsätzlichen Anforderungen an die 3D-Modelle, um die Vorteile der additiven Fertigung optimal auszunutzen. Dieses Kapitel befasst sich damit, wie ein gezieltes DfMJF die Kosten für den 3D-Druck reduzieren kann.
Kapitel 7: Optimierung der Kosten
7.1 Reduzierung des Volumens eines Bauteils
Die wesentlichen Preisfaktoren beim MJF-Verfahren sind der Materialeinsatz und der in der Maschine eingenommene Raum („Maschinenvolumen“ – siehe nächster Abschnitt). Dank einer zielgerichteten Konstruktionsoptimierung für die additive Fertigung können sowohl das Volumen (Materialverbrauch) und damit die Produktionszeit als auch die Produktionskosten reduziert werden.
Zur Reduktion des Materialvolumens können folgende Strategien angewendet werden:
- Entfernen überflüssiger Elemente: Strukturen, die nicht zwingend notwendig sind, können entfernt werden. Häufig werden Kunststoffteile für guss- oder spanabhebende Verfahren konzipiert und enthalten Flächen, die beim 3D-Druck nicht mehr erforderlich sind. Die durch das Entfernen dieser Flächen entstehenden Geometrien mit hoher Komplexität, wie bspw. Hinterschneidungen oder Freiflächen, können mit dem 3D-Druck problemfrei umgesetzt werden. Siehe dazu auch: Topologieoptimierung.
- Aushöhlen massiver Strukturen: Ab einer Wandstärke von 10 mm empfehlen wir, das Modell auszuhöhlen. Sie haben dabei folgende Optionen:
- Aushöhlen mit Öffnung: Es wird überschüssiges Material aus dem Hohlraum entfernt.
- Aushöhlen ohne Öffnung: Überschüssiges Material verbleibt im Innenraum. Die kann auf Wunsch durch uns geschehen.
- Aushöhlen mit Gitternetzstruktur: Es verbleibt Material im Innenraum, außerdem werden Stützstrukturen eingezogen, die dem Innenraum zusätzliche Stabilität verleihen. Die Gitternetzstruktur kann auf Ihren Wunsch durch uns eingefügt werden.
- Die Gitternetzstruktur ist unser Standardprozess, wenn Sie die Option „Aushöhlen erlauben“ anwählen. Sollten Sie reines Aushöhlen wünschen, teilen Sie uns das gern bei der Bestellung in den Messages mit.
- Das Aushöhlen unsererseits hat keinen Einfluss auf die Kosten! Es dient der Qualitätsverbesserung!
7.2 Reduzierung des benötigten Bauraums
Im Multi Jet Fusion Verfahren lässt sich der Bauraum nahezu vollständig mit Bauteilen auslasten – typischerweise zwischen 50 und 250 Stück. Sperrige Bauteile beanspruchen mehr Raum und erhöhen daher den Preis pro Teil, da ungenutzter Raum kostspielig ist. Ein kostenoptimiertes Design für Additive Manufacturing (DfAM) verzichtet daher auf voluminöse Strukturen.
Abstehende oder hervorstehende Elemente vergrößern die „Bounding-Box“ eines Objekts teils deutlich, so dass der Bauraum ineffektiv genutzt wird und die Druckkosten erheblich steigen. Oft können solche Elemente sinnvoll entfernt bzw. separat gedruckt und später zugefügt werden. Abhängig von ihrer Funktion könnten auch klappbare Elemente in Betracht gezogen werden, die in einer zusammengeklappten Position gedruckt und anschließend aufgerichtet werden (siehe Kapitel 4). Diese Vorgehensweisen können erheblich zur Kostensenkung des 3D-Drucks beitragen.
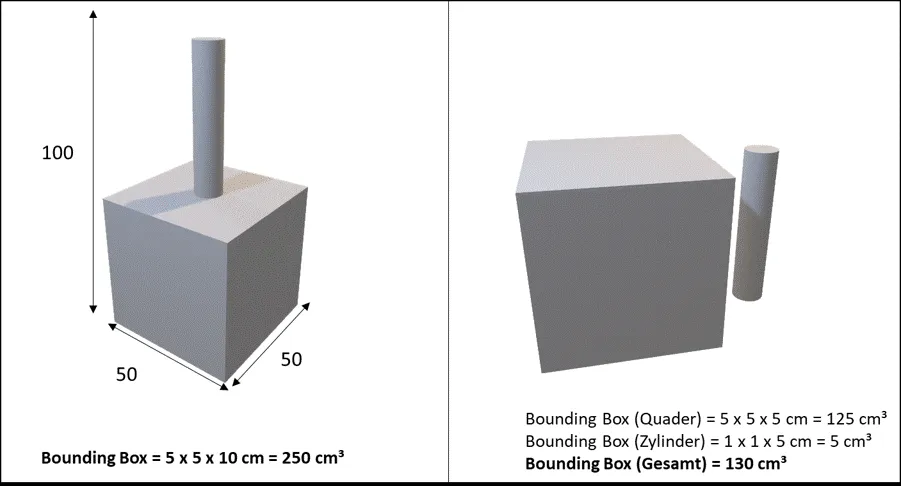
7.3 Verwendung von Baugruppen
Die fast grenzenlose Designfreiheit des MJF-Verfahrens ermöglicht es Ihnen, die Anzahl der benötigten Bauteile entscheidend zu reduzieren. Dies erreichen Sie, indem Sie verschiedene Bauteile zu wenigen (bis zu einem einzigen) zusammenfassen, ohne dass die Funktionalität reduziert wird. Damit verringert sich die Komplexität und Sie sparen gleichzeitig oftmals noch Gewicht und Kosten. Weitere Kostenreduktionen ergeben sich dadurch, dass weniger Bauteile bearbeitet werden müssen.