Multi Jet Fusion (MJF) ist ein pulverbasiertes 3D-Druckverfahren. Aufgrund der hohen Bauteilqualität, des hohen Durchsatzes und der niedrigen Stückkosten ist diese additive Fertigungstechnologie insbesondere für Funktionsteile und (Klein-)Serienbauteile geeignet. Multi Jet Fusion ermöglicht die Produktion von langlebigem und widerstandsfähigem Polyamid 12, elastischem TPU und dem flexiblen Polyamid 11 in kurzen Vorlaufzeiten, auch für höhere Stückzahlen.
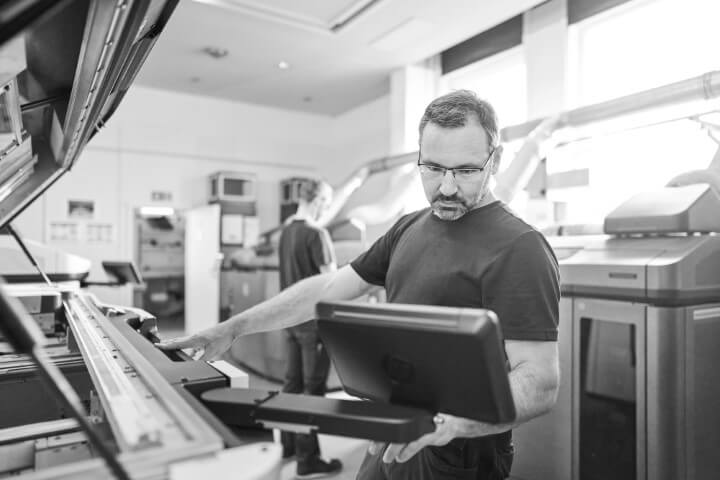
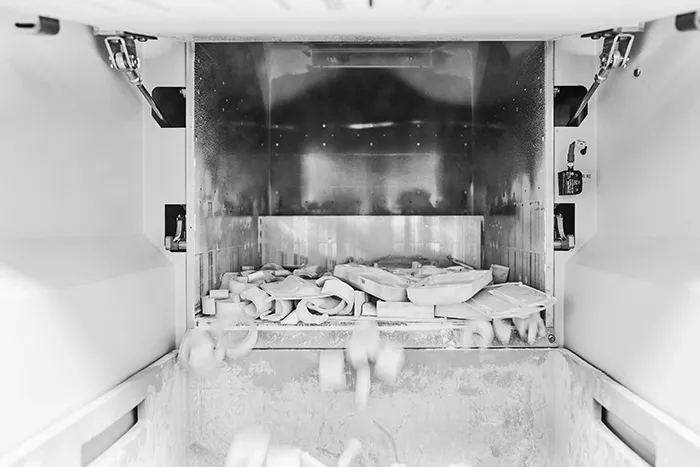
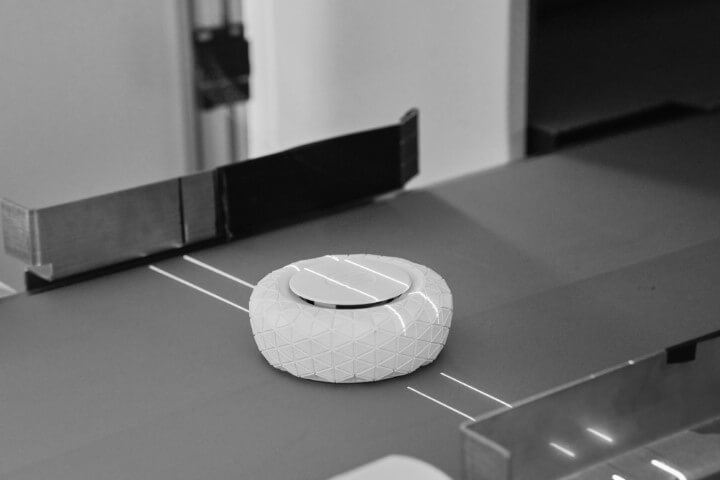
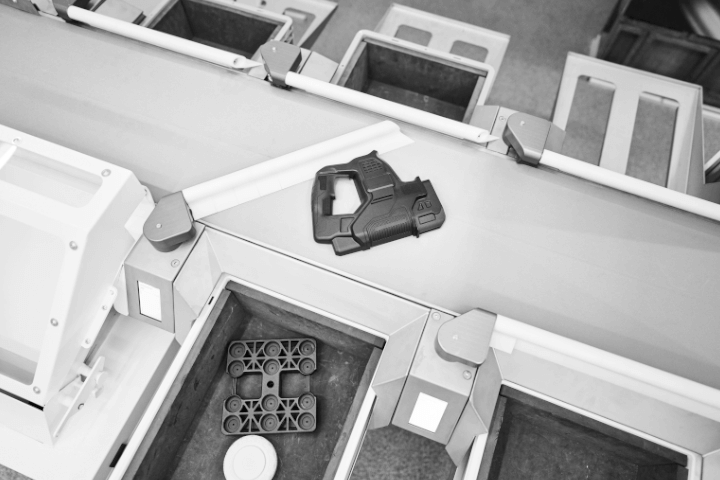
Kurzinfos
Materialien
PA 12, TPU, PA 11
Farben
grau, schwarz, weiß, farbig
Bauraum
mind. 10 mm
max. 380 mm
Produktionszeit
ab 3 Arbeitstage
Genauigkeit
materialabhängig
Das Druckverfahren Multi Jet Fusion
Multi Jet Fusion ist ein pulverbettbasiertes, additives Produktionsverfahren. Konkret erfolgt im ersten Prozessschritt zunächst das Auftragen einer geschlossenen Pulverschicht. Das Rohmaterial ist weiß und hat eine mittlere Korngröße von ca. 60 µm bei Polyamid.
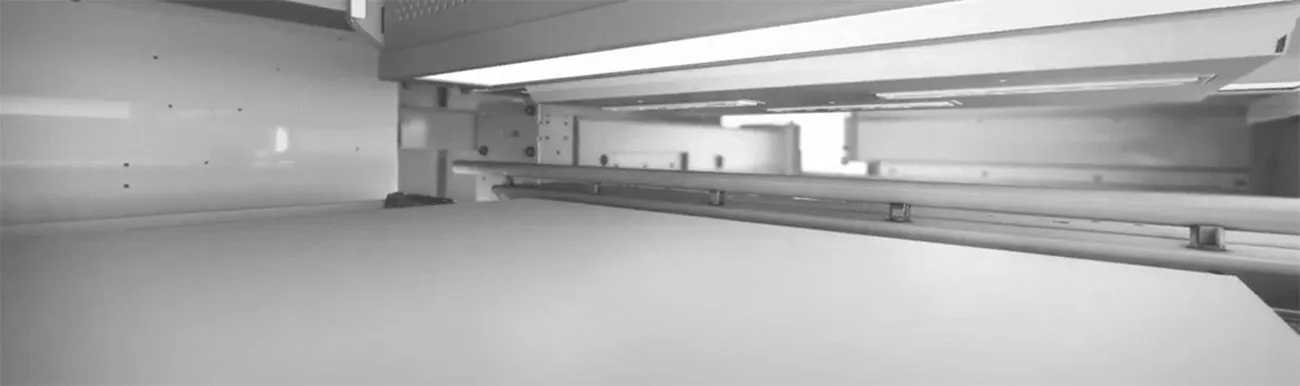
Im zweiten Schritt werden auf die Pulverschicht die zu schmelzenden Bereiche mit einer schwarzen Flüssigkeit bzw. Tinte, dem „Fusing Agent“, bedruckt. Am Druckkopf befinden sich integrierte Heizquellen (Infrarot-Licht), die das Pulverbett direkt nach dem Auftrag der Tinte erhitzen. Die schwarzen, mit dem Fusing Agent bedruckten Bereiche absorbieren dabei mehr Energie als die unbedruckten weißen Bereiche und schmelzen und erstarren, sobald die Hitzequelle entfernt wurde.
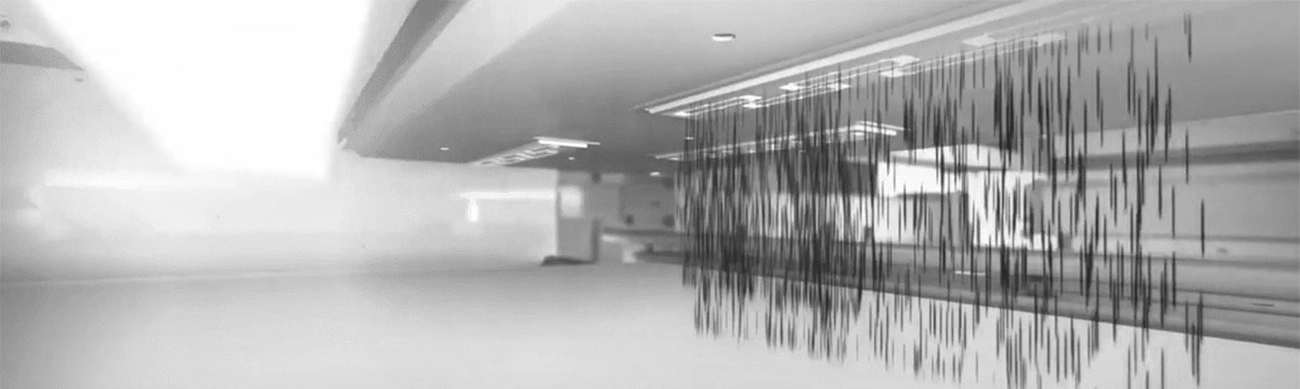
Ein weiterer Wirkstoff, der „Detailing Agent“, wird zum Isolieren genutzt. Er wird um die mit dem Fusing Agent bedruckten Bereiche herum aufgetragen. Der „Detailing-Agent“ ist erforderlich, um an den Übergangsbereichen als thermischer Isolator zu fungieren und damit die Detailauflösung zu maximieren.
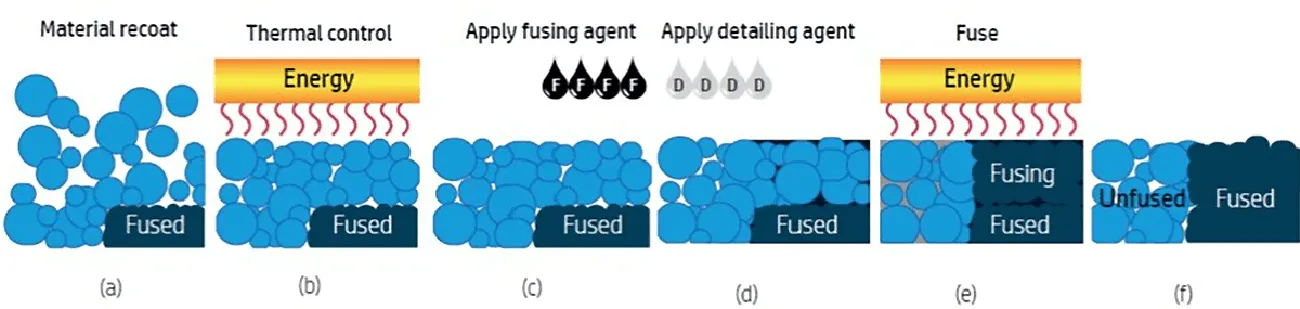
Das Leistungsvermögen dieses Systems ist erstaunlich. Pro Sekunde werden 300 Millionen Tropfen Flüssigkeit mit einer Genauigkeit von 21 µm abgegeben. Obwohl diese Technologie sehr komplex ist, hat sie signifikante Vorteile:
- Isotropie: Im Gegensatz zu den meisten anderen additiven Fertigungsverfahren sind die 3D-gedruckten Objekte weitgehend isotrop. Das bedeutet, die mechanischen Kennzahlen eines Bauteils sind (weitgehend) unabhängig von seiner Richtung.
- Geschwindigkeit: Typischerweise fertigen wir 180 bis 200 Bauteile in einem Druckgang von 12 Stunden. Damit ist MJF mit einem Schnitt von 3 bis 4 Minuten pro Bauteil eines der produktivsten additiven Fertigungsverfahren.
- Auflösung: Durch die kleinen Tropfen hat das Multi Jet Fusion System eine Auflösung von 1.200 dpi entlang der X-Y-Achse. Dank des schnellen Druckprozesses können auch kleinere Schichthöhen von nur 80 µm wirtschaftlich verwendet werden.
- Dichte: Die „Agents“ decken den gesamten Modellbereich ab und verschmelzen gleichmäßig. Nach dem Verschmelzen haben die Bauteile eine nahezu 100%ige Materialdichte, lediglich die Oberfläche ist leicht porös. Durch die Oberflächenversiegelung mit Vapor Smoothing können die Bauteile vollständig abgedichtet und auch für gas- und flüssigkeitsführende Systeme eingesetzt werden.
Prozesskette
Die industrielle additive Fertigung umfasst vor und nach dem eigentlichen 3D-Druck zahlreiche Prozessschritte. Jeder dieser Schritte ist qualitätsoptimiert: eine Übersicht dazu finden Sie auf der Seite „Zertifizierte additive Fertigung bei 3Faktur“.
Wir halten europaweit eine der umfangreichsten Prozessketten für diese Technologie vor. Neben den hier genannten Anlagen arbeiten wir mit zahlreichen weiteren Komponenten in der Peripherie: beispielsweise KI-basierte Bauteilsortierung, automatisierte Qualitätskontrollen sowie proprietäre IT-Systeme zur Produktionssteuerung und Automatisierung von Geschäfts- und Produktionsprozessen.
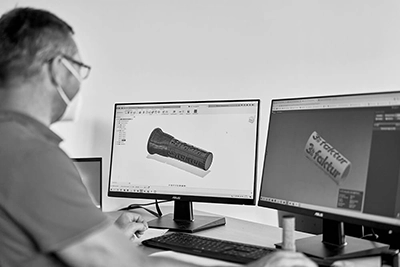
1 / Datenprüfung
Die CAD Daten werden individuell auf ihre Produzierbarkeit geprüft und ggf. Verbesserungsmöglichkeiten mit unseren Kunden besprochen.
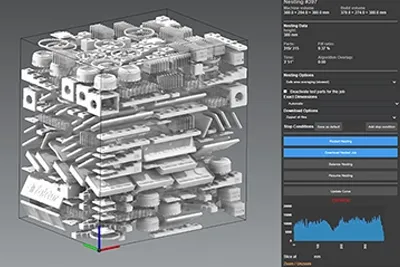
2 / Datenvorbereitung
Für jedes Bauteil werden individuelle Produktionsschritte und -parameter definiert. Nach diesem Vorgang erfolgt das „Nesting“, bei dem die Bauteile ineinander verschachtelt werden. Dies ergibt den sogenannten Printjob, der an die Maschine übertragen wird.
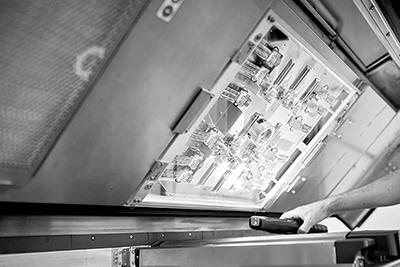
3 / 3D-Druck
Der eigentliche 3D-Druck nimmt je nach Material und Anlage 12 bis 16 Stunden in Anspruch. Wir arbeiten mit vier Multi Jet Fusion 3D-Druckern (1 x 4210, 2 x 5210 und 1 x 5420 W) von HP.
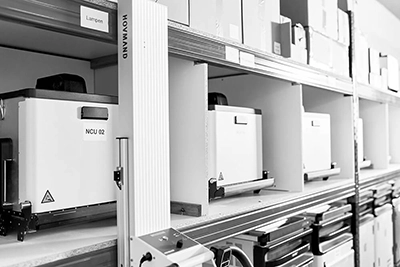
4 / Abkühlen
Die Bauräume werden nach erfolgtem Druck aus dem Drucker entfernt und kühlen langsam 36 bis 72 Stunden von > 150 °C auf Raumtemperatur ab. Dadurch werden Bauteilschäden (z.B. Schrumpfungen, Verzug, Oberflächenschäden) reduziert.
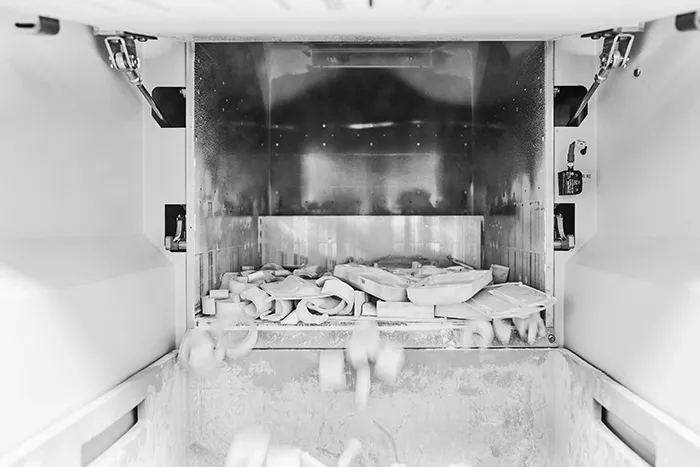
5 / Entpacken
Der Bauraum ist nach dem Druck vollständig mit Pulver gefüllt. Die Bauteile müssen aus diesem sogenannten „Pulverkuchen“ entfernt werden. Dieser Prozessschritt erfolgt inzwischen überwiegend automatisiert.

6 / Reinigen
Durch die hohen Temperaturen ist Restpulver an den Bauteilen „angesintert“. Dieses wird mechanisch und weitgehend automatisiert per Glasperlenstrahlen entfernt.
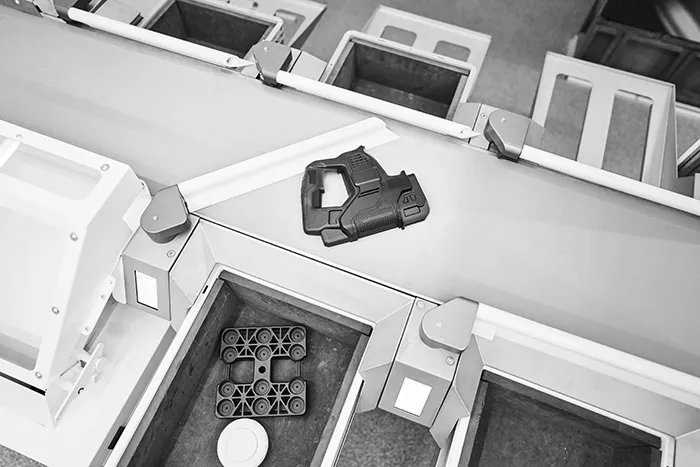
7 / Sortieren
In jedem Printjob werden mehrere Dutzend bis tausende Bauteile produziert. Aus Qualitätsgründen ist dabei eine Durchmischung verschiedener Teile sinnvoll, um ein möglichst gleichmäßiges Hitzeprofil während des 3D-Drucks zu erreichen. Die vielen Bauteile nach dem Druck auf die nachfolgenden Schritte bzw. Aufträge zuzuordnen, ist arbeitsintensiv und fehleranfällig. Daher setzen wir modernste KI-basierte Automatisierungstechnik ein, um diesen Prozess effizient und fehlerfrei zu erledigen.
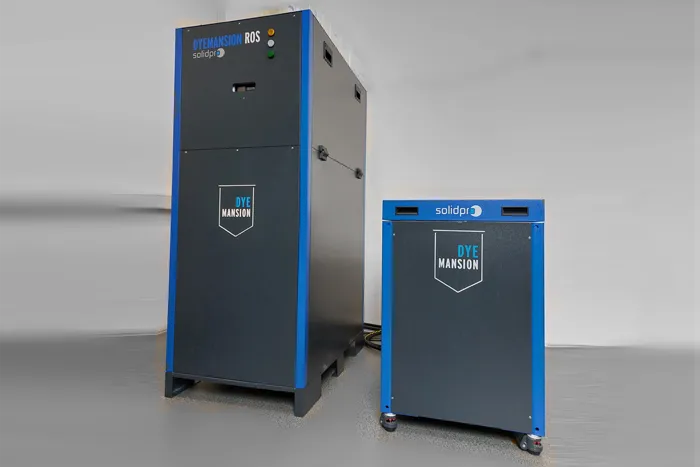
8 / [Optional] Färben
Bei schwarzen Bauteilen erfolgt eine Tauchfärbung der Bauteile. Die weißen Bauteilen (PA 12 W) werden in der Anlage von DyeMansion gefärbt.
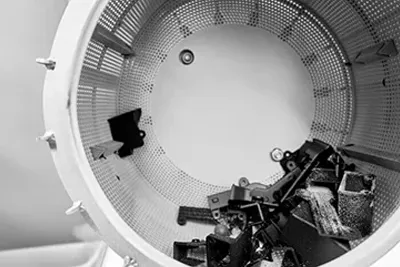
9 / [Optional] Shot Peening
Alle gefärbten Bauteile durchlaufen einen zweiten Strahlgang mit einem anderen Strahlmedium, bei dem die Oberfläche verdichtet wird („Shot Peening“ bzw. „Verdichtungsstrahlen“). Der Vorgang findet in einer dafür optimierten Strahlkabine teilautomatisiert statt.
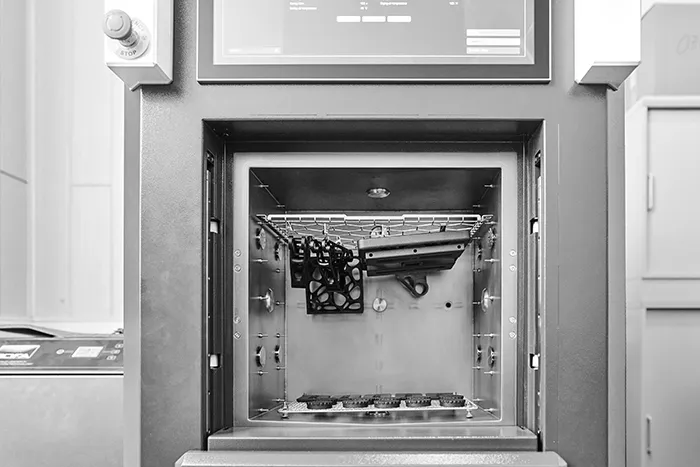
10 / [Optional] Vapor Smoothing
Auf Wunsch kann eine chemische Glättung erfolgen, um eine glatte, porenfreie Oberfläche zu erhalten. (AMT SF 50 Anlage zum Vapor Smooting).
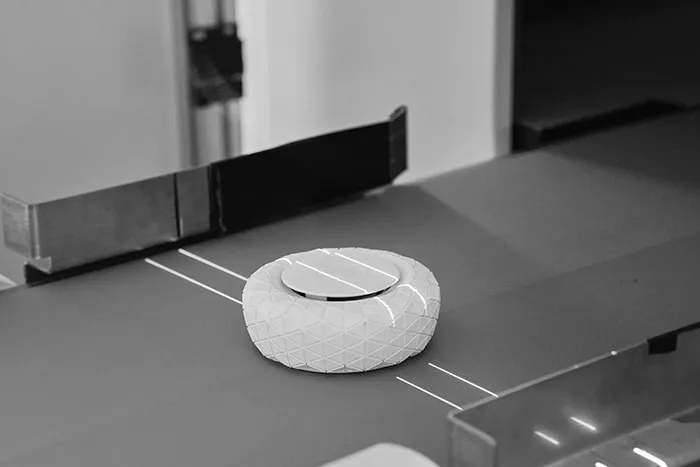
11 / Qualitätskontrolle
Die Qualitätskontrolle ist einer unserer aufwändigsten Arbeitsgänge. Neben den eigentlichen Bauteilen werden auch Fertigungsbegleitproben bei jedem Zyklus produziert und ausgewertet. Dies ermöglicht uns ein frühes Eingreifen, beispielsweise bei sich andeutendem Verbrauchsmaterialverschleiß, und stellt eine höchstmögliche Replizierbarkeit sicher.
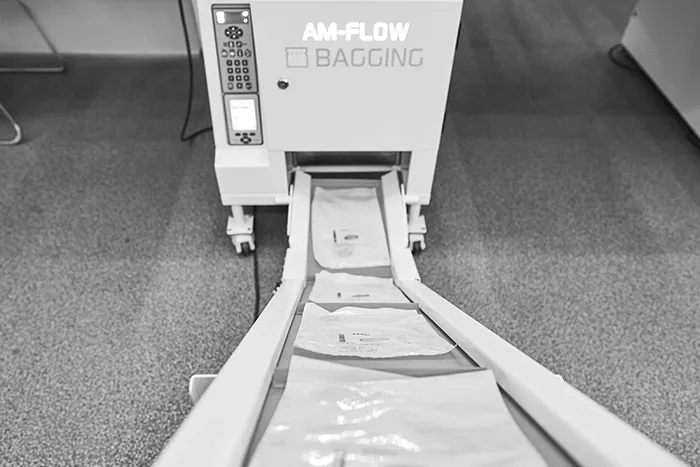
12 / Verpackung & Versand
Nach Freigabe der Bauteile erfolgen finale Zuordnung, Verpackung und Versand. Auch dieser Prozess verläuft teilweise automatisiert.
Materialien für Multi Jet Fusion
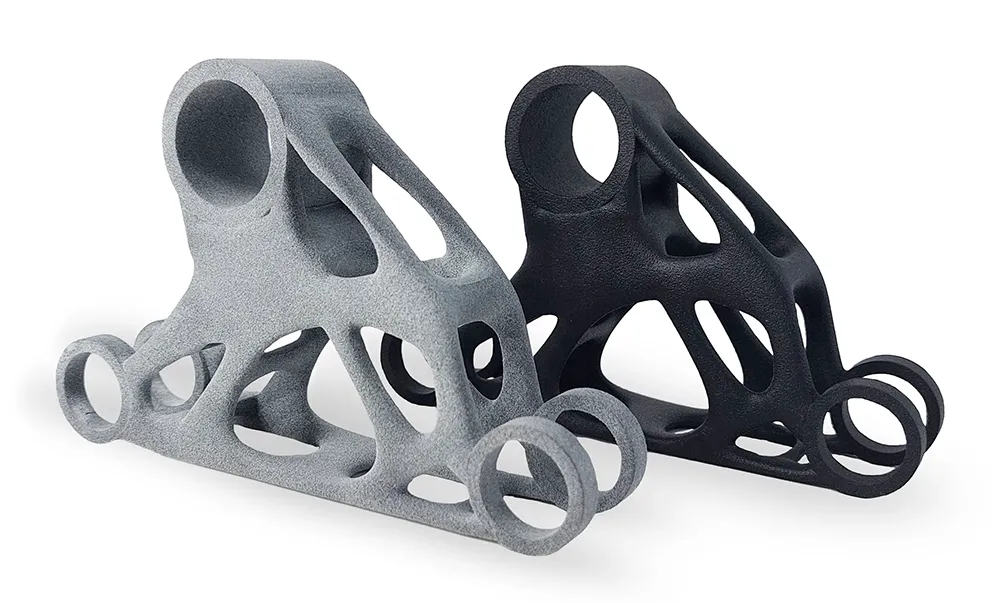
Der Allrounder „PA 12“ für einen vielseitigen industriellen Einsatz ist sehr belastbar und langlebig. Erhältlich in fünf Varianten.
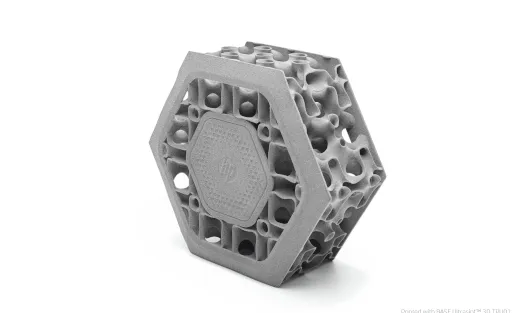
Das elastische TPU ist für Dämpfung, Bauteilen mit hohe mechanische Belastungen und Orthesen geeignet.
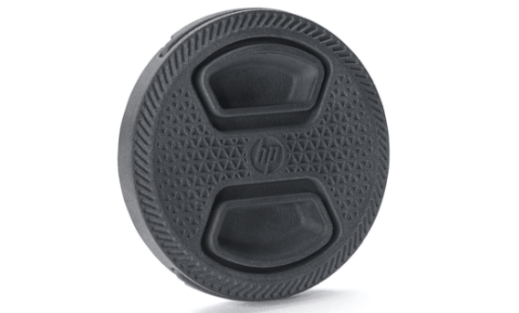
Das flexible PA 11 ist für Bauteile mit Schnappverbindungen, Filmscharnieren o.ä. Elementen geeignet.
Nachbearbeitung
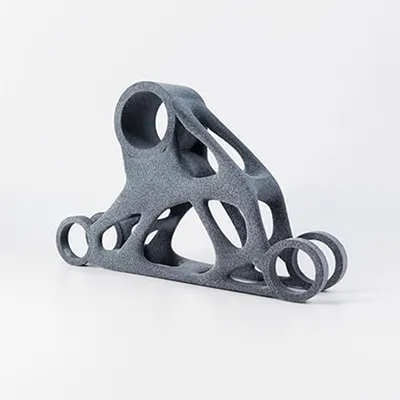
Unbearbeitet
Graue Bauteile, die bei nicht sichtbaren Komponenten zum Einsatz kommen.
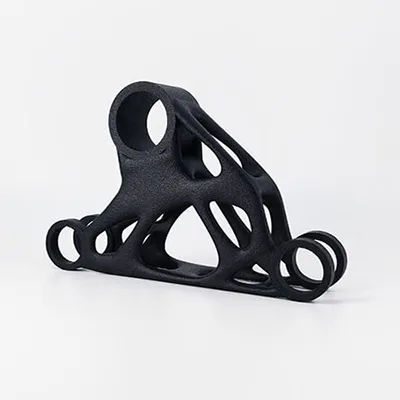
Färbung & Shot Peening
Gefärbte und oberflächenbearbeitete Bauteile, die v.a. bei Sichtteilen eingesetzt werden.
Mehr Infos zur Färbung
Mehr Infos zum Shot Peening
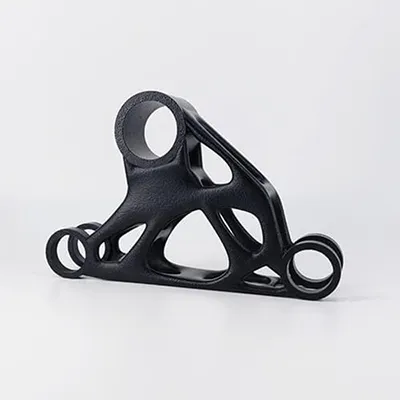
Vapor Smoothing (chemisches Glätten)
Gefärbte, chemisch geglättete und versiegelte Oberflächen für zahlreiche Anwendungen.
Mehr Infos zum Vapor Smoothing
Anwendungen
Mit Multi Jet Fusion (MJF) können stabile, langlebige Kunststoffbauteile additiv gefertigt werden. Die Anwendungen erstrecken sich über alle Industrien, z.B.
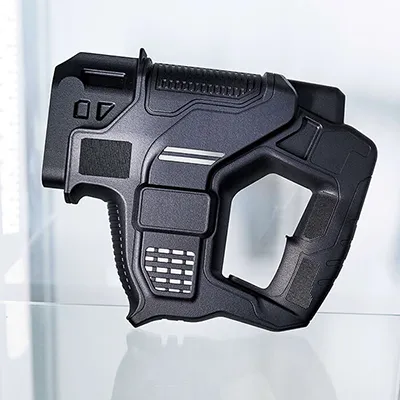
Gehäuse
Mechanisch, thermisch und chemisch belastbare Gehäuse können schnell und effizient gefertigt werden.
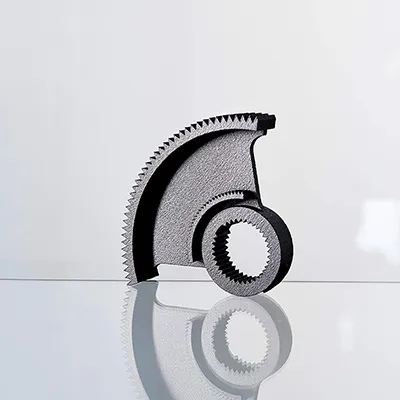
Strukturelle Elemente
Komponenten aus dem „Innenleben“ von Maschinen und Anlagen können auch mit sehr komplexen Geometrien hergestellt werden.
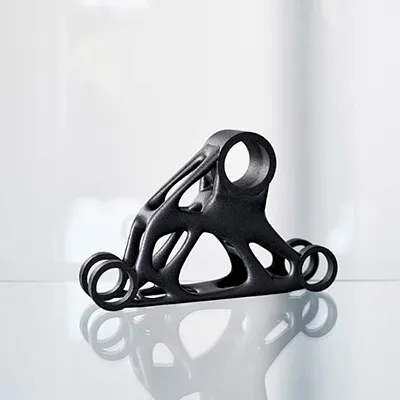
Gewichts- bzw. topologieoptimierte Bauteile
Durch die Möglichkeit Hinterschneidungen bzw. Gitternetzstrukturen zu drucken, ist Multi Jet Fusion für den Leichtbau optimal.
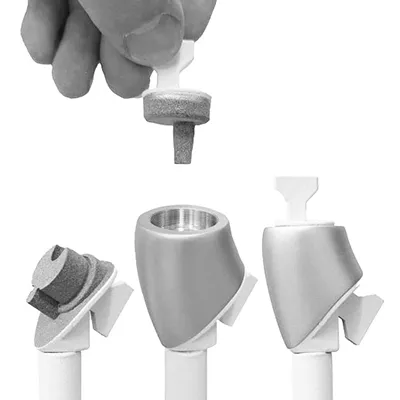
Vorrichtungen
Stabile Materialien mit unendlicher geometrischer Komplexität: Multi Jet Fusion ist hervorragend für den Bau von Vorrichtungen geeignet.
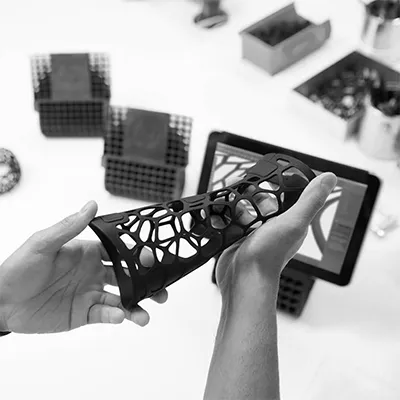
Orthesen
Insbesondere das Material TPU findet inzwischen großen Einsatz bei der Produktion von patientenspezifischen Orthesen.
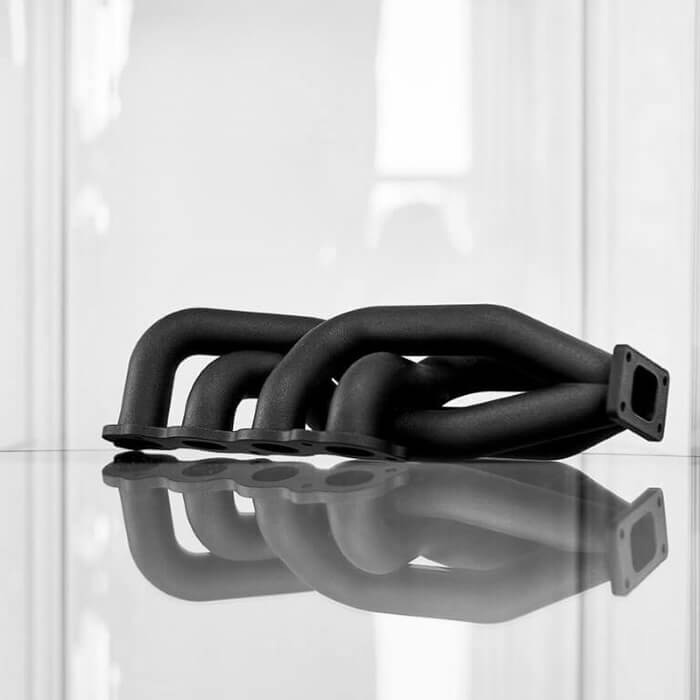
Gas- und flüssigkeitsführende Komponenten
Durch das Finishing mit Vapor Smoothing können vollständig dichte Bauteile erstellt werden.