3Faktur ist auf die additive Serienfertigung spezialisiert. Wir setzen ausschließlich auf das Multi Jet Fusion-Verfahren. Unsere Spezialisierung erlaubt uns einen sehr hohen Grad an Optimierung und Effizienz. Dabei werden wir auch höchsten Qualitätsansprüchen gerecht und sind u.a. als industrielle additive Fertigungsstätte vom TÜV Süd zertifiziert.
Für Sie bedeutet dies verlässliche Qualität, Replizierbarkeit und Lieferzeit zu höchstkompetitiven Preisen.
Arbeitsvorbereitung
Die Arbeitsvorbereitung bildet die Grundlage für eine erfolgreiche Produktion. Ihre Werkstücke durchlaufen einen aufwändigen Prozess, bevor die Produktion gestartet wird. Unsere Arbeitsvorbereitung baut dabei auf die Erfahrung von hunderttausenden Bauteilen, um Ihr Projekt optimal vorzubereiten.
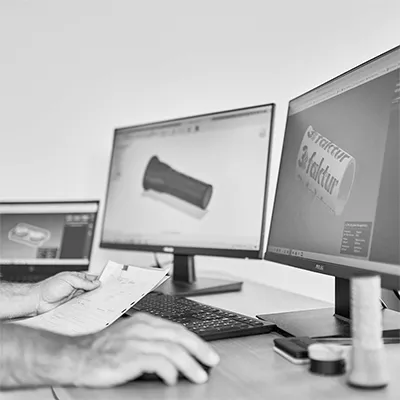
Bauteil – Orientierung
Die Bauteil-Orientierung beeinflusst maßgeblich die Maßgenauigkeit und Oberflächenqualität. Jedes Bauteil wird von unseren erfahrenen Arbeitsvorbereitern individuell analysiert und so orientiert, um eine möglichst optimale Balance zwischen Oberflächenqualität und Maßgenauigkeit in allen Dimensionen zu gewährleisten.
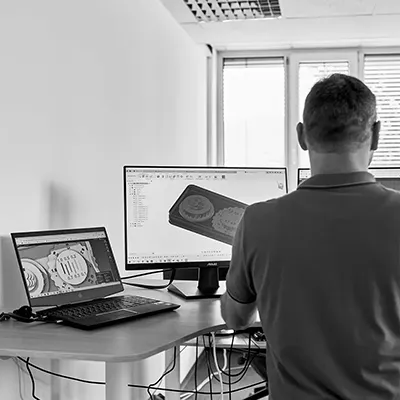
Fertigungs – Analyse
Alle Bauteile werden einer grundsätzlichen Analyse unterzogen, ob diese gefertigt werden können oder ob potenzielle Probleme vorliegen können. Beispielsweise wird das Bauteil hinsichtlich Wandstärken oder potenziell problematischer Geometrien, wie innenliegende schmale Kanäle, verzugsgefährdete Geometrien oder ähnliches, untersucht.
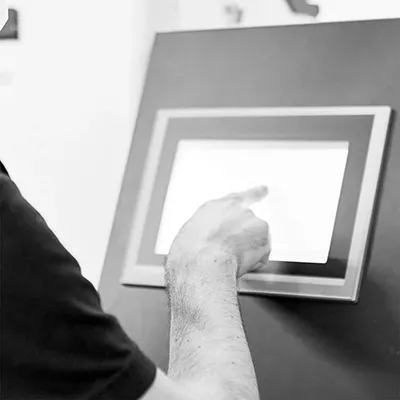
Individuelle Produktionsparameter
Für jedes Modell werden individuelle Produktionsparameter definiert, um ein bestmögliches Ergebnis zu erzielen. Beispielsweise werden die Distanz zu anderen Bauteilen sowie die Lage im Bauraum individuell definiert.
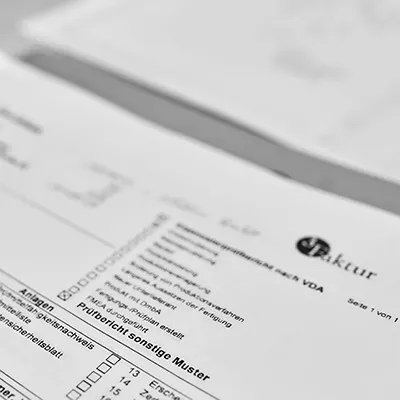
Angepasster Prozesslauf
Jedes Bauteil ist anders und jedes Projekt hat seine ganz bestimmten Anforderungen. Für jeden Auftrag wird ein individueller Prozesslauf (‚Pathway‘) definiert, der neben grundsätzlichen Bearbeitungsschritten auch geometriespezifische Hinweise für den Werker enthält.
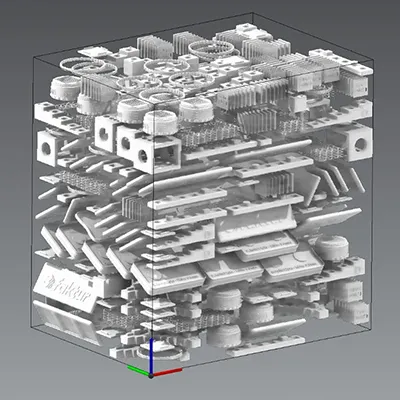
Nesting
Sind alle Parameter definiert, geht es ans „Nesting“. Dabei werden alle Bauteile eines Produktionszyklus‘ (typischerweise 50 – 300 Bauteile) so ineinander verschachtelt, dass ein optimaler ‚Job‘ entsteht. Ziel ist es dabei, ein möglichst ausgeglichenes Hitzeprofil zu erhalten. Je gleichmäßiger die Hitzeverteilung im Drucker ist, desto besser werden Maßgenauigkeit, Oberfläche und mechanische Eigenschaften. Die Kunst besteht darin, die Bauteile für einen Job möglichst optimal vorzubereiten und die Anzahl und Art der Bauteile auszuwählen. Dafür ist viel Fingerspitzengefühl und vor allem Erfahrung notwendig.
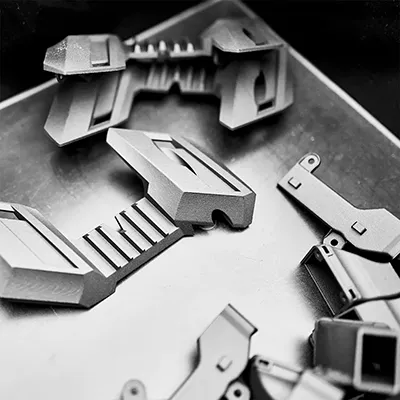
Definierte Produktionszyklen für Serienbauteile
Werden Bauteile zu hunderten oder tausenden produziert und regelmäßig abgerufen, entstehen individuelle Produktionsprofile. Die erzielte Qualität wird nach dem ersten Lauf intensiv evaluiert und gegebenenfalls die Parameter weiter optimiert. Ziel ist hierbei, die bestmögliche Replizierbarkeit und Qualität sicherzustellen. Dies schließt neben allgemeinen Produktionsparametern auch ein, dass Serienbauteile stets mit einer identischen Hardware-Kombination produziert werden.
3D-Druck
Die industrielle Produktion ist anspruchsvoll und der Unterschied zwischen Erfolg und Misserfolg liegt meist im Detail. Da unterscheidet sich die additive Fertigung nicht von konventionellen Produktionsverfahren.
Unser hoher Grad an Spezialisierung erlaubt es uns, bis ins kleinste Detail zu optimieren und so sicherzustellen, dass auch Ihre höchsten Ansprüche erfüllt werden.
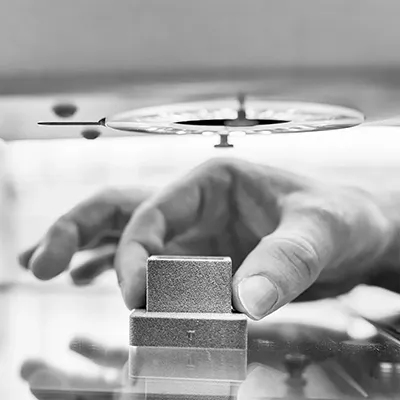
Qualitätsorientierte Druck-Parameter
Der Druck erfolgt im „Balanced Mode“ (Schichtstärke für Polyamid 12: 80 µm). Der Modus bietet eine optimale Balance aus mechanischer Belastbarkeit, Oberflächengüte und Maßhaltigkeit. Für jeden Produktionszyklus wird ein individueller Parametersatz definiert, der auf der Erfahrung von tausenden Zyklen basiert.
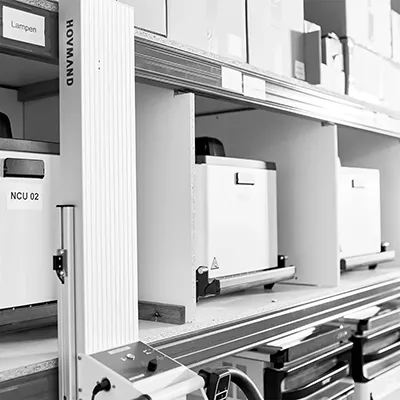
Langsamer Abkühlprozess
Während des Druckes heizt sich der Bauraum im Drucker sehr stark auf. Die Abkühlphase setzen wir sehr lang an (mindestens 2 Tage) und verzichten ausdrücklich auf eine Beschleunigung der Abkühlphase („Fast Cooling“). Dadurch können Maßhaltigkeit, mechanische Eigenschaften und Oberflächengüte deutlich verbessert werden.
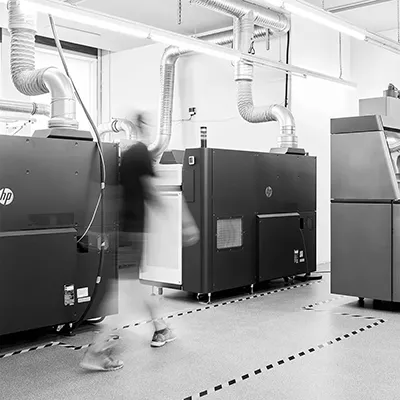
Kontrollierte Produktionsumgebung
Das thermische Verarbeiten von Polymeren stellt hohe Ansprüche an die Produktionsumgebung. Unsere Produktionsräume sind voll klimatisiert, so dass Temperatur und Luftfeuchtigkeit stets konstant gehalten werden, um eine maximale Replizierbarkeit in der Serienfertigung zu gewährleisten.
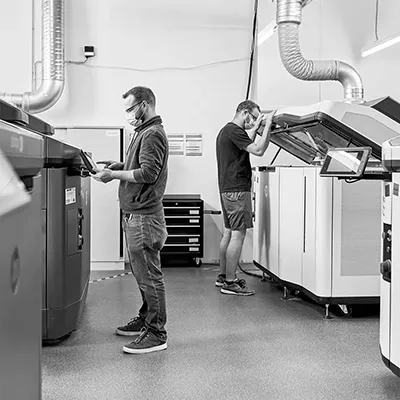
Industrielle Produktionstechnik
Unser Maschinenpark umfasst modernste Produktionsanlagen, die vor jedem Produktionszyklus gewartet und kalibriert werden. Eine hohe Replizierbarkeit ist für uns das Maß aller Dinge, weshalb auch Verschleißteile meist schon vor dem Ablauf erneuert werden, um mögliche Qualitätsauswirkungen zum Ende der Lebenszeit zu vermeiden.
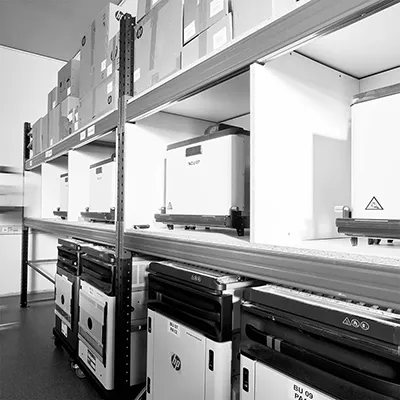
Hohe Kapazität
Durch die hohe Spezialisierung verfügen wir sowohl in der Produktionstechnik als auch in der Nacharbeit über ausreichend Kapazität, um auch große Stückzahlen zu bewältigen. Im Mehrschicht- und Wochenendbetrieb fangen wir auch Auslastungsspitzen ab und erreichen so seit 2020 eine „On time Delivery“ Quote von konstant über 98 %.
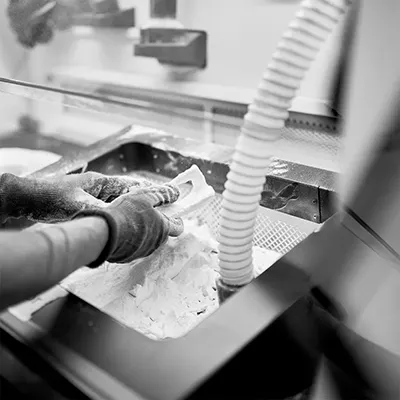
Hochwertige Rohmaterialien
Wir verwenden ausschließlich zertifizierte, qualitativ hochwertige Rohmaterialien zur Produktion und in der Nacharbeit. Jede neue Charge an Material wird geprüft und auch vor jedem Produktionszyklus wird kontrolliert, dass das Ausgangsmaterial unseren hohen Qualitätsansprüchen genügt.
Nacharbeit
Der eigentliche Druck ist nur ein Teil der Produktionskette. Für das fertige Produkt sind weitere Bearbeitungsschritte erforderlich. Dabei setzen wir auf dokumentierte, hochgradig optimierte Prozesse, um Ihnen stets qualitativ hochwertige und replizierbare Bauteile zu liefern.
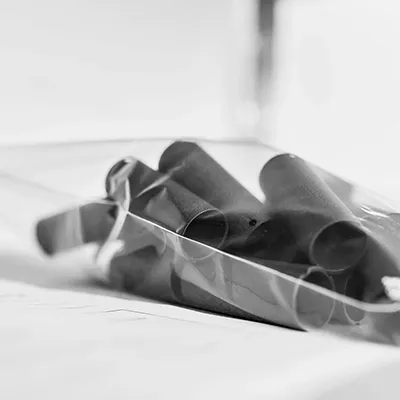
Replizierbare Prozesse
Als spezialisierter Anbieter können wir alle Ressourcen auf einen Fertigungsprozess konzentrieren. Tausende Bauteile durchlaufen diesen Prozess jede Woche unter konstanten und optimierten Bedingungen. Jeder Zyklus wird protokolliert, kontrolliert und kontinuierlich verbessert.
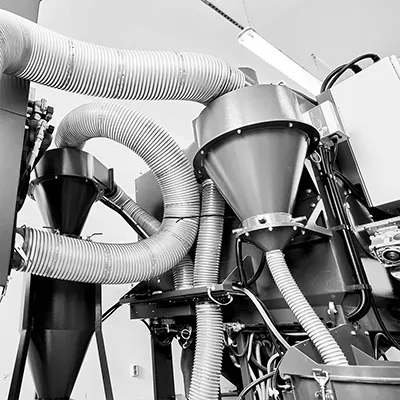
Optimierte Anlagentechnik
Um die Qualität, Replizierbarkeit und Effizienz der Fertigungsprozesse zu optimieren, setzen wir auch auf Spezialmaschinen, die für unsere Anforderungen entwickelt und gefertigt wurden und uns dabei helfen, unsere Produktionsprozesse noch besser zu machen.
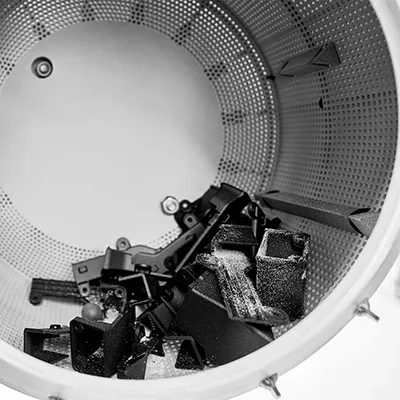
Großer Erfahrungsschatz
Als einer der ersten Anbieter der Multi Jet Fusion Technologie in Deutschland können wir auf einen großen Erfahrungsschatz bauen. Unsere Prozesse sind dokumentiert, kontrolliert und auch bei Belastungsspitzen oder unvorhergesehenen Ereignissen (z.B. Maschinenausfall) stabil und zuverlässig. Das heißt nicht, dass wir nicht noch besser werden können: Wir setzen auf kontinuierliche Verbesserung, um Ihre hohen Ansprüche jeden Tag aufs Neue zu übertreffen.
Qualitätskontrolle
Die Qualitätssicherung beginnt bereits beim Eingang Ihrer Bestellung. An jedem Schritt in der Produktionskette finden diverse Kontrollen statt, um mögliche Probleme frühzeitig zu identifizieren und abzustellen. Die eigentliche Qualitätskontrolle stellt dabei den finalen Schritt dar und umfasst neben individuellen Vereinbarungen zahlreiche Prüfungen an Ihren Bauteilen und Fertigungsbegleitproben.
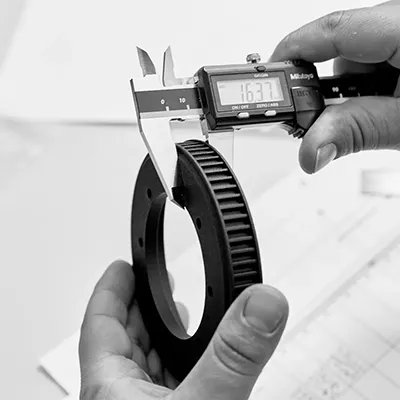
Systematisches
Prüfverfahren
An allen Produktionsschritten werden in unserer Fertigung Qualitäts-Checks durchgeführt. In der finalen Qualitätskontrolle werden verschiedene Kontroll- und Messschritte durchgeführt. Dies schließt u.a. individuell vereinbarte Messprotokolle, verschiedene Stichprobenprüfungen sowie eine intensive Prüfung von Fertigungsbegleitproben ein.
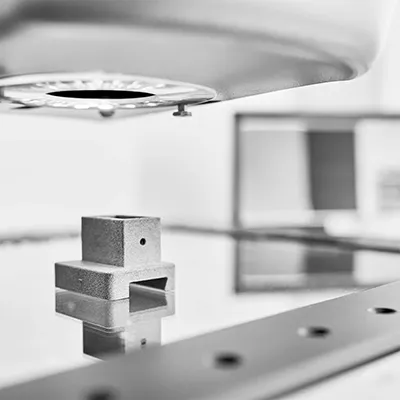
Moderne Prüftechnik
Die additive Fertigung erlaubt die Produktion sehr komplexer Geometrien. Die meisten Geometrien können wir in unserem QM-Labor mit moderner Messtechnik prüfen.
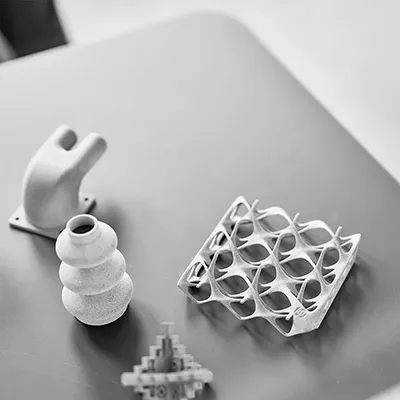
Individuelle Prüfpläne
In der additiven Serienfertigung kommen bei uns häufig individuelle d.h. bauteilspezifische, Messprotokolle zum Einsatz. Dabei werden spezifische, für die Funktion der Bauteile essenzielle Messpunkte geprüft bzw. Funktionsprüfungen durchgeführt. Neben der Art der Prüfungen wird auch die individuell vereinbarte Stichprobenanzahl, bis hin zur 100 % Prüfung, festgelegt.