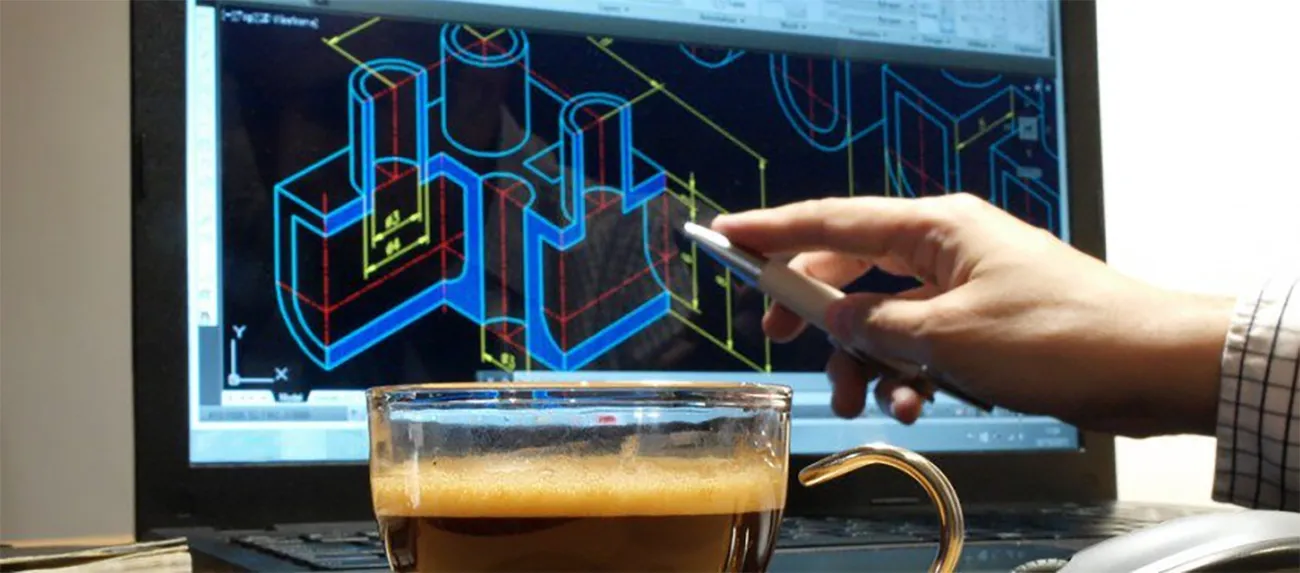
Wenn wir uns mit dem 3D-Druck beschäftigen, fällt unweigerlich irgendwann der Begriff des „Reverse Engineering“. Etwas simpel übersetzt heißt es so viel wie „umgekehrtes Entwickeln“. In diesem Beitrag wollen wir uns etwas genauer mit diesem Begriff befassen und die besondere Stellung der 3D-Drucktechnologien beim Prozess des Reverse Engineering erläutern.
Zum Begriff des Reverse Engineering
Grundsätzlich wird unter Reverse Engineering (RE) der Prozess verstanden, ein Objekt durch Untersuchung des Aufbaus, der Zustände und Reaktion auf Umweltveränderungen wieder in einen Konstruktionsplan zu „verwandeln“. Also den ursprünglichen Konstruktionsablauf umzudrehen.
Anwendung findet das Reverse Engineering bspw. zur Analyse von Abnutzungen stark beanspruchter Bauteile oder zur Replikation von Teilen, bei denen keine Konstruktionsdaten (mehr) vorliegen, insbesondere bei älteren Anlagen oder Fahrzeugen.
Ziel hierbei ist es, das bestehende Objekt möglichst genau darzustellen, meist in Form eines 3D-Modells des Ursprungsgegenstandes. Dazu ist meist eine teilweise oder annähernd komplette Demontage des Objekts notwendig. Für einige Objekte kann auch schon ein professioneller 3D-Scan ausreichen.
Der Beitrag der 3D-Drucktechnologien zum Reverse Engineering
Die Technologien, die sich rund um den 3D-Druck (weiter-)entwickelt haben, haben die Möglichkeiten des Reverse Engineering nochmals vorangetrieben. Durch die Perspektiven, die die 3D-Scantechnologien bieten, kann nicht nur der Demontageaufwand reduziert, sondern auch der Prozess enorm beschleunigt werden.
Der 3D-Druck wiederum ermöglicht es, leicht und kostengünstig weitere Modelle herzustellen und diese mit dem Original zu vergleichen oder dies zu ‚kopieren‘. Ersteres wird häufig verwendet, um die Abnutzung stark beanspruchte Teile zu analysieren. Bspw. untersuchen Hersteller, an welchen Stellen sich ein mechanisches Bauteil in einem Motor am stärksten abnutzt. Die daraus gewonnenen Daten können direkt verwendet werden, um überarbeitete Teile mittels additiver Fertigungsverfahren zu produzieren. Mit den Teilen werden entweder weitere Tests durchgeführt oder in einigen Fällen werden die optimierten Teile auch direkt verarbeitet. Der 3D-Druck bietet dabei die Möglichkeit, sehr komplexe Geometrien zu erstellen, die in anderen Fertigungsverfahren nicht oder nur sehr aufwändig realisiert werden können.
Das ‚Kopieren‘ kommt zum Einsatz, wenn Bauteile benötigt werden für die keine Konstruktionsdaten vorliegen. Häufig handelt es sich dabei um ältere Anlagen, insbesondere aus dem Bereich des Sondermaschinenbaus. Eine weitere zunehmend populäre Anwendung ist die Produktion von Ersatzteilen von Fahrzeugen oder sogar Flugzeugen.
Verwendete Methoden
Für das Reverse Engineering ist eine besonders genaue Vermessung des Originals vonnöten. Es haben sich dabei zwei Herangehensweisen etabliert: der 3D-Scan und die direkte physische („taktile“) Messung. Die Wahl der Methode ist dabei von der geometrischen Komplexität des Objektes und der geplanten Verwendung der gewonnenen Daten abhängig .
3D-Scanning
1. 3D-SCAN
Beim 3D-Scan wird entweder ein Laserstrahl („Laser-Scan“) oder ein Muster („strukturiertes Licht“) auf die Oberfläche des Objektes projiziert. Da daraus entstehenden Muster auf dem Objekt werden von Kameras aufgenommen und von einer Software mittels eines Algorithmus zu einem 3D-Modell zusammengesetzt.
Die Vorteile dieser Methode sind:
- Kein direkter Kontakt mit dem Objekt notwendig.
- Sehr hohe Geschwindigkeit der Messung (insbesondere bei strukturiertem Licht)
- Freiflächen sind problemlos messbar.
Dadurch, dass die Kameras Licht auf die Oberfläche des Objektes projizieren, ergeben sich allerdings auch zwei Nachteile:
- Oberflächeneigenschaften: Je nach Material wird Licht unterschiedlich reflektiert, dadurch kann es zu Ungenauigkeiten kommen. Daher sollten alle Objekte mit einer matten Schicht überzogen werden (bspw. Kreidespray). Bei einigen Objekten ist dies aufgrund der Materialbeschaffenheit allerdings nicht möglich.
- Hinterschneidungen: Bereiche, die nicht vollständig ausgeleuchtet werden können, können von den Kameras nicht erfasst werden und fehlen im finalen Modell.
2. COMPUTERTOMOGRAPHIE (CT-SCAN)
Beim CT-Scan wird das Objekt, mit Hilfe von Röntgenstrahlen, gescannt. Dabei werden die äußere und die innere Struktur sowie die Dichte der Objektwände vermessen. Dabei dreht sich das Objekt um 360°. So entsteht eine Vielzahl an 2D-Bildern („Ebenen“ oder „Slices“), die mittels eines Algorithmus in ein 3D-Volumenmodell umgewandelt werden. Vorteile dieser Methode sind:
- Untersuchung der Oberflächen und nicht zugänglicher Bereiche (Hinterschneidungen, Hohlräume, etc.) möglich.
- Auf Demontage des Objekts kann oftmals verzichtet werden.
- Sichtbarkeit von Objektteilen in ihrer Funktion.
- Soll-Ist-Vergleiche von Original und Replik möglich.
- Materialzustand (bzw. -ermüdung) kann analysiert werden.
Allerdings sind die CT-Scanner sehr kostenintensiv und benötigen sehr viel Platz (Abschirmung der Röntgenstrahlung). Ein 3D-Scanner hingegen hat oftmals nur die Ausmaße eines Wasserkochers.
Direkte physische („taktile“) Messungen
Im Gegensatz zum 3D-Scan ist bei der taktilen Messung ein direkter Kontakt mit dem Objekt notwendig. Wir können dabei zwei grundlegende Herangehensweisen unterscheiden: 1. Messungen mit einem Koordinatenmessgerät (CMM); 2. Manuelle Messung. Meist sind direkte physische Messungen noch genauer als ein 3D-Scan, dies hängt aber in starkem Maße vom Ausführenden und den verwendeten Instrumenten der Messung ab.
1. MESSUNGEN MIT CMM (COORDINATE MEASURING MACHINE)
Die CMM sind ursprünglich nicht für die Erstellung von 3D-Modellen konzipiert worden, sondern für die Überprüfung von Abmessungen. Trotzdem ist es möglich aus den gewonnenen Daten eine s. g. Punktewolke zu erstellen. Um für den 3D-Druck nutzbar zu sein, wird diese Punktewolke mithilfe von Algorithmen zuerst in ein Flächenmodell und anschließend in ein Volumenmodell umgewandelt. Diese Herangehensweise eignet sich insbesondere für Objekte mit einfacher Geometrie, bei denen aber eine hohe Genauigkeit benötigt wird.
2. MANUELLE MESSUNG
Hierbei werden die Daten der manuellen Messungen verwendet, um ein 3D-Modell mittels CAD-Software zu erstellen. Dieser Prozess benötigt verglichen mit einem 3D-Scan viel Zeit, da das Objekt vermessen, modelliert und überprüft werden muss.
Bei einfachen Geometrien, bspw. bei Bauteilen die hauptsächlich aus geometrischen Grundkörpern bestehen, ist dieses Verfahren allerdings häufig schneller und kostengünstiger. Wohingegen beim Scan die Daten in einer sehr aufwändigen Prozedur in Volumenmodelle umgewandelt werden müssen (Flächenrückführung bzw. Volumenrückführung), wird beim manuellen Vermessen das Objekt direkt in CAD Daten erstellt.
Von der Punktewolke zur STEP Datei
Dabei sind folgende Schritte notwendig:
- Generieren von ausreichend Messdaten. → Punktewolke
- Definierung der Flächen zwischen den Punkten zu MESH-Modellen (oder NURBS-Flächen). → Manipulationen möglich
- Überführung in das .STL-Format (STereoLithografie). → notwendig für 3D-Druck
- Umwandeln in den STandard for the Exchange of Product model data (STEP). → kompatibel für andere CAx-Systeme
Beim 3D-Scan und der taktilen Messung entstehen sehr viele Messpunkte. Diese werden in einer Punktewolke dargestellt. Allerdings hat diese Punktewolke noch keine Flächeneigenschaften. Algorithmen erkennen die Zusammenhänge zwischen den Messpunkten und verbinden diese (mithilfe von Vektoren) zu komplexeren geometrischen Formen (meist Dreiecke oder Vierecke). Das Ergebnis sind Gitternetzmodelle (MESH-Modelle). Diese Modelle sind nun fast beliebig manipulierbar und somit für den Prozess des Reverse Engineering von entscheidender Bedeutung. Die Gitternetzmodelle werden meist als Dateiformat .STL gespeichert, welches direkt für den 3D-Druck genutzt werden kann. Um die so gewonnenen Daten auf andere CAx-Systeme zu übertragen, ist eine Umwandlung nach dem STandard for the Exchange of Product model data, notwendig. Dazu bedarf es zuerst einer Flächenrückführung (exakt/parametrisch), d. h. die einzelnen Flächen/Regionen werden definiert, verbunden oder zusammenfasst. Mithilfe einer Volumenrückführung werden aus diesen Flächen nun Körper erstellt und in den Formaten .STEP;.STP;.IGES gespeichert. Mit diesen Formaten können die Daten nun auf die meisten 3D-Systeme übertragen werden.
Anwendungen
Das Reverse Engineering und der 3D-Druck werden häufig in einem Atemzug verwendet. Oftmals werden die Techniken des RE benutzt, um die Daten für die Erstellung eines genauen 3D-Oberflächenmodells zu gewinnen. Dies kann dazu verwendet werden, ein Negativ des Objekts zu erstellen, um es dann mit dem Original zu vergleichen und die Genauigkeit zu überprüfen. Ebenso schnell wie kostengünstig können auch die manipulierten Varianten des Originals 3D-gedruckt werden, um schnell die Auswirkungen der Manipulationen testen zu können.
Weitere Anwendungsfelder ergeben sich für die Herstellung von Gussformen. Dies kann zum einen der direkte 3D-Druck einer Gussform sein. Oder es werden Werkzeuge die speziell für dieses Objekt passen, gefertigt.
Wird CT-Scanning für das Reverse Engineering verwendet, können auch komplexe innere Strukturen der Objekte vermessen werden (bspw. zur Analyse von Materialermüdungen).
Zusammenfassung
Der 3D-Druck und die dazugehörigen Technologien können einen spürbaren Beitrag zum Reverse Engineering leisten. Insbesondere die 3D-Scantechnologien vereinfachen die Digitalisierung von Gegenständen. Und mithilfe des 3D-Drucks können (manipulierte) Modelle sehr schnell und mit einer hohen Genauigkeit hergestellt werden, um den Vergleich mit dem Ursprungsgegenstand zu ermöglichen.
Über 3Faktur: 3Faktur ist Spezialist für 3D-Druck, Rapid Prototyping und Rapid Manufacturing. Wir arbeiten mit dem Multi Jet Fusion-Verfahren von HP und bieten unterschiedliche Materialien für den Prototypenbau und die Serienproduktion an. Sollten Sie Fragen zu Ihrem Projekt haben, können Sie uns gern kontaktieren.