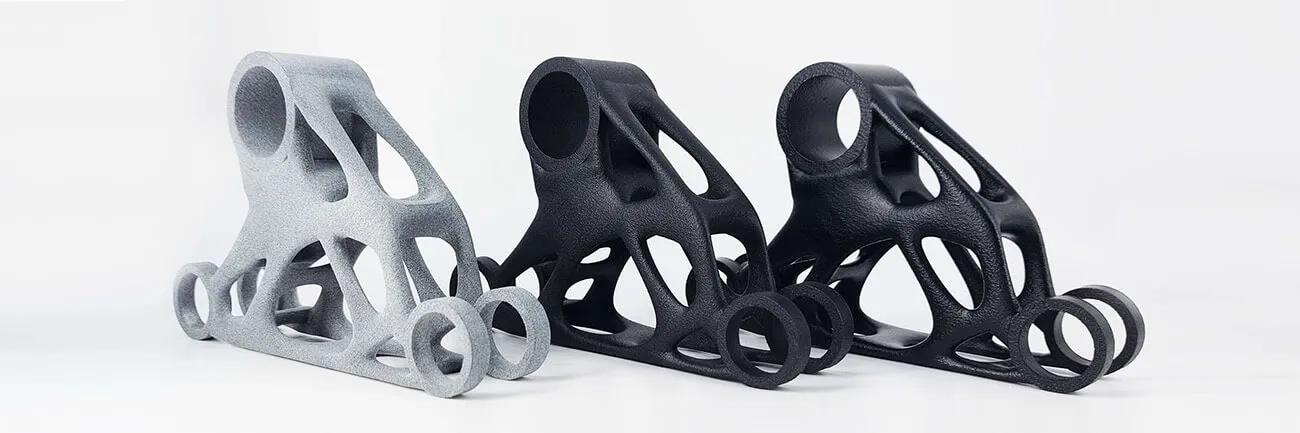
ABS, PLA, PA11, PA12, ASA, PP, TPU, Accura Xtreme, PEEK, ULTEM – wissen Sie was damit gemeint ist? Ja, dann kennen Sie sich super aus! Wenn nicht, bringen wir in diesem Artikel Licht ins Dunkle und erklären Ihnen auch, wie diese Materialien mit verschiedenen 3D-Druck Verfahren wie dem Lasersintern, der Schmelzschichtung (FDM, FFF, etc.) oder Multi Jet Fusion zusammenhängen.
Übersicht Kunststoffe (Beispiele) im 3D-Druckverfahren
Arten von Kunststoffen Thermoplaste 3D-Druck amorpher Thermoplasten 3D-Druck teilkristalliner Thermoplasten 3D-Druck Duroplasten
Grundlage – die Arten von Kunststoffen
Um zu verstehen, wie Kunststoffe im 3D-Druck verarbeitet werden, muss man zunächst die unterschiedlichen Arten von Kunststoffen kennenlernen.
Kunststoffe werden in Thermoplaste, Duroplaste und Elastomere unterschieden. Letztere spielen in der additiven Fertigung (noch) eine untergeordnete Rolle. Thermoplaste und Duroplaste machen mit rund 75 Prozent für Thermoplaste und rd. 25 Prozent Duroplaste (Wohlers Report 2022) den Löwenanteil in der additiven Fertigung aus.
Übersicht Molekülstrukturen Kunststoffe
Thermoplaste werden bei Erhitzung weich und bei Abkühlung wieder verhärtet. Diese Prozesse können wiederholt werden. In Thermoplasten sind die Molekülketten nicht vernetzt, sondern liegen größtenteils parallel zueinander. Anstatt durch chemische Bindungen zusammengehalten zu werden, verbinden intermolekulare Kräfte, auch Van-der-Waals-Kräfte genannt, diese Ketten. Wenn eine hohe Energiemenge, wie Wärme, zugeführt wird, können diese Ketten leicht gegeneinander verschoben werden. Dies führt dazu, dass der Kunststoff verformbar wird und bei weiterer Erhitzung beginnt, sich zu zersetzen. Damit können Thermoplaste recycelt werden, in dem Sie aufgeschmolzen und neu verformt werden.
Thermoplaste im 3D-Druck sind z.B. Polyamid mit einem Marktanteil von fast 50 Prozent an allen 3D-gedruckten Kunststoffen (Wohlers 2022), gefolgt von bekannten Polymeren wie ABS (Acrylnitril-Butadien-Styrol), PLA (Polylactid, vereinfacht auch „Polymilchsäure“) oder PP (Polypropylen).
Ein Duroplast hingegen kann nur einmal geformt, anschließend aber nicht wieder verflüssigt oder reformiert werden. Sie sind aufgrund ihrer chemischen Struktur nicht gut recycelbar. Bei ihrer Erhitzung kommt es eher zu einer Zersetzung und Verbrennung als zu einem Recyclingprozess. Das liegt daran, dass Duroplaste ein dichtes Netzwerk von chemischen Bindungen aufweisen, das sogenannte „Cross-Linking“, was ihre Struktur dauerhaft und hitzebeständig macht. Duroplaste werden vereinfacht (und chemisch nicht ganz korrekt) auch als „Kunstharze“ bezeichnet. Beispiele für Duroplasten sind Epoxidharze und viele Polyurethane.
Arten von Kunststoffen Thermoplaste 3D-Druck amorpher Thermoplasten 3D-Druck teilkristalliner Thermoplasten 3D-Druck Duroplasten
Thermoplaste
Thermoplaste – Unterscheidung nach der Molekülstruktur
Thermoplaste werden in der Regel in zwei Hauptklassen unterteilt: amorph und teilkristallin. Diese Klassifizierung bezieht sich auf die Anordnung der Polymere auf mikroskopischer Ebene. Die unterschiedlichen Eigenschaften werden bei einigen 3D-Druckverfahren gezielt ausgenutzt.
Amorphe Thermoplaste haben eine zufällige, ungeordnete Struktur, die dazu führt, dass sie eher transparent sind und eine geringere chemische Beständigkeit und geringere Wärmeformbeständigkeit aufweisen als teilkristalline Thermoplaste. Sie haben keinen festen Schmelzpunkt. Bei bestimmten Temperaturen wechseln sie von einer starren zu einer biegsamen Form, weil ihre Molekülketten anfangen, sich zu bewegen („Glasübergangstemperatur“). Der Kunststoff wird jedoch nicht sofort flüssig, dies passiert erst, wenn die Temperatur noch weiter steigt.
Teilkristalline Thermoplaste haben sowohl geordnete (kristalline) als auch ungeordnete (amorphe) Bereiche in ihrer Struktur. Sie sind in der Regel undurchsichtig und haben eine höhere chemische Beständigkeit und höhere Wärmeformbeständigkeit als amorphe Thermoplaste. Auch diese Kunststoffe ändern ihre Form bei bestimmten Temperaturen, aber das betrifft nur die ungeordneten (amorphen) Teile. Oft ist diese Temperatur niedriger als der Schmelzpunkt. Daher können diese Kunststoffe zwischen diesen beiden Temperaturen sowohl steif als auch biegsam sein. Sie sind bekannt dafür, dass sie sich biegen, aber nicht brechen, was als „duktil“ bezeichnet wird. Teilkristalline Thermoplaste haben damit i.d.R. einen festen Schmelzpunkt.
Es gibt auch Elastomere, eine Unterklasse von Thermoplasten, die auch als thermoplastische Elastomere (TPEs) bezeichnet werden. Diese Materialien kombinieren die elastischen Eigenschaften von Gummi mit der Verarbeitbarkeit von Thermoplasten, was bedeutet, dass sie sich wie Gummi dehnen und verformen können, aber auch geformt und recycelt werden können wie andere Thermoplaste.
Thermoplaste – Unterscheidung nach Anwendungen
Vergleich Thermoplaste
VERGLEICH HOCHLEISTUNGSKUNSTSTOFFE
Man kann Thermoplaste auch nach der Leistungsfähigkeit unterteilen, wie in der Abbildung die so genannte Polymerpyramide.
Standardthermoplaste wie ABS oder Polypropylen sind vielseitig und leicht zu verarbeiten. Sie eignen sich für Produkte, die keine hohen Leistungsanforderungen stellen – wie Verpackungen und Spielzeug.
Technische Thermoplaste wie PA (Polyamid) und PC (Poylcarbonat) bieten mehr Festigkeit und Steifheit als Standardthermoplaste, sind aber weniger widerstandsfähig als Hochleistungsthermoplaste. Sie sind ideal für Anwendungen, die eine erhöhte Beständigkeit, aber nicht unbedingt extreme Härte oder Hitzebeständigkeit erfordern.
Hochleistungsthermoplaste wie PEEK zeichnen sich durch hohe Wärme- und mechanische Beständigkeit aus. Sie werden in anspruchsvollen Bereichen wie der Automobil-, Elektronik- und Raumfahrtindustrie eingesetzt.
Arten von Kunststoffen Thermoplaste 3D-Druck amorpher Thermoplasten 3D-Druck teilkristalliner Thermoplasten 3D-Druck Duroplasten
Der 3D-Druck von amorphen Thermoplasten
Die mit Abstand wichtigste Technologie für den 3D-Druck von amorphen Thermoplasten ist das Schmelzschichtverfahren, auch genannt FDM (Fused Deposition Modeling), FFF (Fused Filament Fabrication) oder einfach Schmelzschichtung genannt. Dabei wird ein Filament in einer Düse erhitzt und schichtweise aufgetragen. Dies ist zunehmend auch mit Granulaten anstatt von Filamenten möglich.
Als Beispiele für Polymere für das FDM Verfahren sind zu nennen:
PLA: Polylactid (PLA) ist ein biologisch abbaubarer Thermoplast, der aus nachwachsenden Rohstoffen wie Maisstärke oder Zuckerrohr hergestellt wird. Aufgrund seiner guten Verarbeitbarkeit und biologischen Abbaubarkeit wird es im 3D-Druck v.a. im privaten Bereich eingesetzt. Das Material ist in Punkto mechanischer und thermischer Belastbarkeit in aller Regel jedoch nicht für den industriellen Einsatz geeignet.
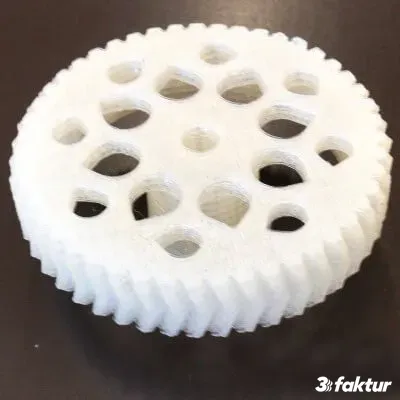
ABS: Acrylnitril-Butadien-Styrol (ABS) ist ein starkes und flexibles thermoplastisches Polymer, das in vielen Bereichen wie Automobil, Elektronik und Spielzeugindustrie (z.B. Legosteine, Playmobilfiguren) eingesetzt wird. Aufgrund seiner hohen Festigkeit, Hitzebeständigkeit und einfachen Verarbeitbarkeit ist es auch ein beliebtes Material für den 3D-Druck.
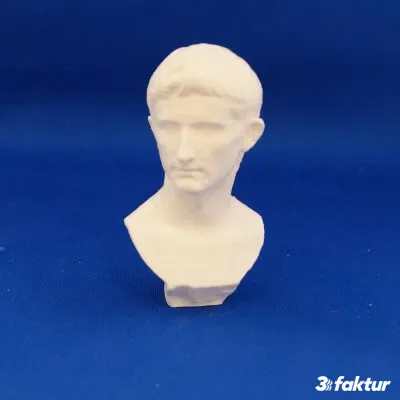
ASA: Acrylnitril-Styrol-Acrylat (ASA) ist ein thermoplastisches Polymer, das ähnlich wie ABS eine hohe Festigkeit und Flexibilität aufweist, aber zusätzlich eine ausgezeichnete UV- und Witterungsbeständigkeit besitzt. Es wird oft in Anwendungen eingesetzt, die einer langen Exposition gegenüber Wetterbedingungen standhalten müssen, wie in der Automobil- und Bauindustrie. Gegenüber ABS ist es meist etwas teurer, was seinen Einsatz auf Bereiche beschränkt, bei denen Wetterfestigkeit eine große Rolle spielt.
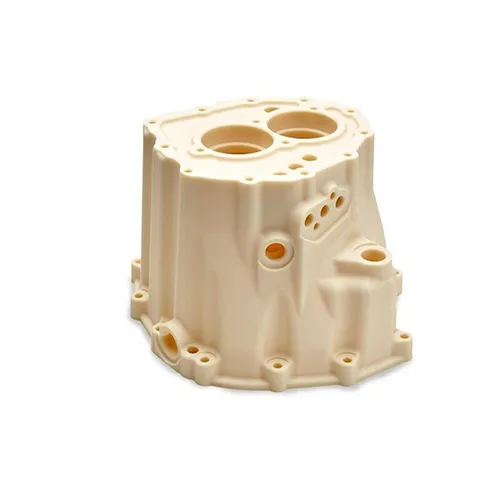
PETG: Polyethylenterephthalatglykol (PETG) ist ein thermoplastisches Polymer, das für seine hervorragende Druckbarkeit, Transparenz und chemische Beständigkeit bekannt ist.
ABS/PC: ABS/PC ist eine Materialmischung aus Acrylnitril-Butadien-Styrol (ABS) und Polycarbonat (PC), die die Vorteile beider Materialien vereint. Es bietet die hohe Festigkeit und einfache Verarbeitbarkeit von ABS zusammen mit der erhöhten Wärmebeständigkeit und Schlagfestigkeit von PC, und wird oft in anspruchsvollen Anwendungen wie im Automobil- und Elektronikbereich eingesetzt.
ULTEM: ULTEM, auch bekannt als Polyetherimid (PEI), ist ein Hochleistungsthermoplast mit hoher Wärmebeständigkeit, hervorragender mechanischer Festigkeit, guter chemischer Beständigkeit, geringer Entflammbarkeit und Toxizität. Es wird häufig in anspruchsvollen Anwendungen wie der Luft- und Raumfahrt, der Medizintechnik und der Elektronikindustrie eingesetzt.
PEEK: Polyetheretherketon (PEEK) ist ein Hochleistungsthermoplast, der sich durch eine außerordentlich hohe Temperaturbeständigkeit, mechanische Festigkeit und chemische Beständigkeit auszeichnet. Dieses Material widersteht Hitze und Abrieb und kann aufgrund seines Verhältnisses von Gewicht zu Festigkeit als Ersatz für bestimmte Metalle dienen. Auch PEEK findet Anwendung in (äußerst) anspruchsvollen Umgebungen.
Arten von Kunststoffen Thermoplaste 3D-Druck amorpher Thermoplasten 3D-Druck teilkristalliner Thermoplasten 3D-Druck Duroplasten
Der 3D-Druck von teilkristalline Thermoplasten
Teilkristalline Thermoplasten können als Pulver verarbeitet werden. Konkret geschieht dies im 3D-Druck im Lasersintern (SLS) oder im Multi Jet Fusion (MJF) Verfahren, auf welches 3Faktur spezialisiert ist.
Bei SLS und MJF handelt es sich um so genannte Pulverbettverfahren. Dabei wird eine geschlossene Pulverschicht aufgetragen und diese an den gewünschten Stellen geschmolzen. Beim Lasersintern geschieht dies mittels eines Lasers, beim Multi Jet Fusion Verfahren mit Hilfe von Infrarotlicht. Genaueres über das Multi Jet Fusion Verfahren finden Sie auf unserer Seite: Multi Jet Fusion – das Verfahren.
Dieser Prozess funktioniert jedoch nur bei hohen Prozesstemperaturen, nur wenige °C (korrekt Kelvin) unterhalb des Schmelzpunktes. Damit kommen für diese Verfahrensklasse nur teilkristalline Polymere in Frage, da amorphe bei solchen Temperaturen die Glasübergangstemperatur erreichen. Dies hätte zur Folge, dass das Material ineinander verschmilzt und das Restmaterial nicht vom gewünschten Bauteil zu trennen wäre.
Teilkristalline Polymere lassen sich auch mit dem FDM Verfahren verarbeiten. Die Leistungsfähigkeit von Pulverbettverfahren ist jedoch im Allgemeinen höher, weshalb v.a. Polyamid in höherer Menge als Pulver verarbeitet wird.
Typische Polymere für Pulverbettverfahren:
Polyamid: PA wird aufgrund seiner hohen mechanischen Festigkeit, Abriebfestigkeit und chemischen Beständigkeit häufig in Industrieanwendungen eingesetzt. Es ist das meist verarbeitete Polymer im 3D-Druck. Es gibt mehrere Polyamide, z.B. PA 12, PA 11 und PA 6. Das beliebteste Polymer in der additiven Fertigung ist Polyamid 12, ein industrieller Kunststoff mit hervorragenden thermischen und mechanischen Eigenschaften und einem sehr breiten industriellem Einsatz. PA 11 ist flexibler, meist etwas teurer und findet Anwendungen z.B. bei Orthesen. PA 6 wiederum benötigt höhere Prozesstemperaturen und wird damit häufig im FDM Verfahren verarbeitet, jedoch sind auch einige Lasersinteranlagen fähig, dieses Material zu verarbeiten.
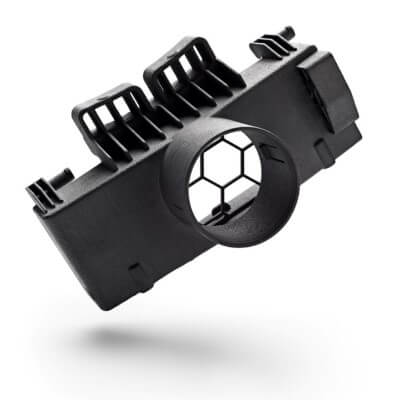
TPU: Thermoplastisches Polyurethan (TPU) ist ein vielseitiger thermoplastischer Elastomer, der hohe Flexibilität, Abrieb- und Schlagfestigkeit bietet. 3D gedrucktes TPU wird häufig in der Medizin (z.B. Orthesen) und Industrie (z.B. Schutzhüllen, Dämpfung, Faltenbalge) verwendet.
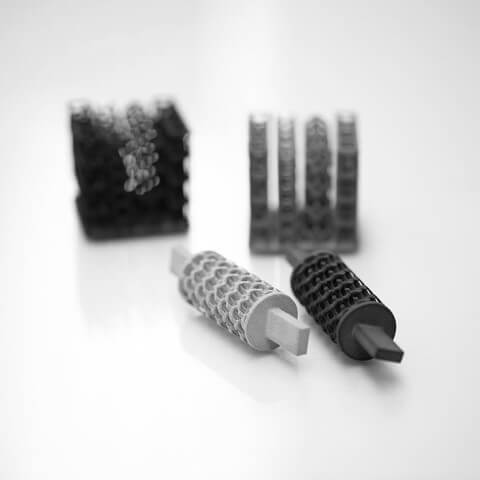
PP: Polypropylen (PP) ist ein leichtes, hitzebeständiges und chemisch widerstandsfähiges thermoplastisches Polymer. Es wird in einer Vielzahl von Anwendungen verwendet, darunter Verpackungen, Textilien, Automobilteile und Haushaltsgeräte. Das im Pulverbett 3D-Druck verarbeitete PP unterscheidet sich stark von spritzgegossenem PP und ist weniger flexibel. Es wird damit weniger für typische PP Anwendungen wie Filmscharniere verwendet und findet im 3D-Druck v.a. Einsatz wegen der hohen chemischen Resistenz.
Arten von Kunststoffen Thermoplaste 3D-Druck amorpher Thermoplasten 3D-Druck teilkristalliner Thermoplasten 3D-Druck Duroplasten
Der 3D-Druck von Duroplasten
Duroplaste werden aus flüssigen Ausgangsmaterialien hergestellt. Im 3D Druck kommen v.a. Photopolymere zum Einsatz. Dabei handelt es sich um lichtempfindliche Kunststoffe, die ihre Eigenschaften unter Einwirkung von Licht, typischerweise ultraviolettem Licht, ändern. Wesentliche Verfahren in dieser Klasse sind Stereolithografie (SLA), Digital Light Processing (DLP) und Material Jetting (z.B. „Polyjet“ von Stratasys), bei denen UV-Licht dazu verwendet wird, die flüssige Harzform des Photopolymers in einen festen Zustand zu überführen. Es gibt im 3D-Druck verschiedene Verfahren zur Verarbeitung von Photopolymeren.
Epoxide: Epoxyharze sind die am häufigsten verwendete Materialgruppe in der Stereolithografie. Dieses synthetische Harz, mit guten elektrischen Isolationseigenschaften und hoher Hitzebeständigkeit, wird auch als Reaktionsharz bezeichnet. Dank seiner Produkteigenschaften wie variabler Flexibilität, geringer Empfindlichkeit gegenüber Stoßeinwirkungen, hoher dimensionaler Genauigkeit der Endprodukte und hoher chemischer Beständigkeit, eignet sich das Photopolymer zur Herstellung von komplexen, detailreichen Prototypen, die auch initialen Funktionalitätstests standhalten können. Ein berühmtes Material in dem Bereich ist z.B. Accura Xtreme (3D Systems), welches weit verbreitet in der Erstellung von Prototypen ist.
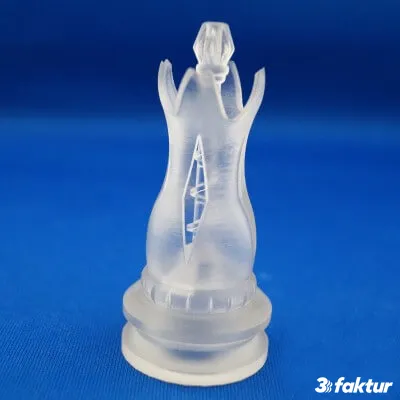
Auch im DLP Verfahren werden Epoxide verwendet. Bei DLP kommen jedoch auch noch weitere Materialklassen zum Einsatz, z.B.
Acrylate: Diese Harze basieren auf Acrylat-Monomeren und bieten eine gute Kombination aus Festigkeit, Präzision und Detailgenauigkeit. Sie werden oft für allgemeine Anwendungen im Prototypenbau eingesetzt. Acrylate werden auch in Materialjetting Verfahren wie z.B. Polyjet verwendet. Im Polyjet Verfahren können auch mehrere unterschiedliche Acrylate gleichzeitig verwendet werden, so dass Multi-Material Prototypen entstehen.
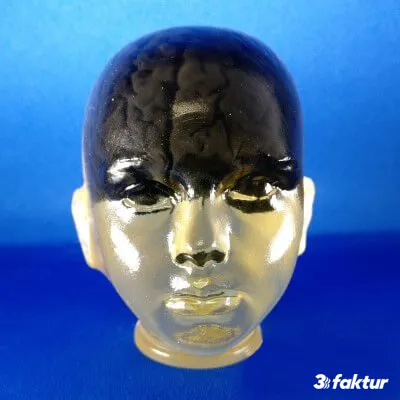
Polyurethane: Diese Harze basieren auf Polyurethanen und bieten eine gute Flexibilität und Elastizität. Sie werden oft für Anwendungen eingesetzt, bei denen eine gewisse Biegsamkeit erforderlich ist, wie zum Beispiel in der Medizintechnik bzw. im Dentalbereich.
Insgesamt ist die Materialbreite bei Duroplasten sehr hoch und durch Eigennamen geprägt. Mehr Informationen zu den Materialien erhalten Sie am besten direkt bei den Materialherstellern, z.B.
Henkel, Evonik, BASF
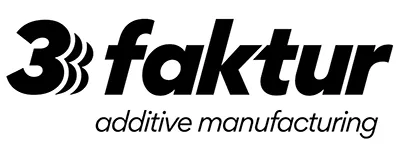
3Faktur ist ein 3D-Druck Dienstleister, spezialisiert auf die additive Fertigung industrieller Kunststoffbauteile. Die Firma ist auf das Multi Jet Fusion Verfahren spezialisiert und fertigt wöchentlich bis zu 5.000 additive Serienbauteile für den Maschinenbau, die Automobilindustrie, Medizintechnik und den High-Tech Bereich. Mehr Informationen zu unserem Angebot.