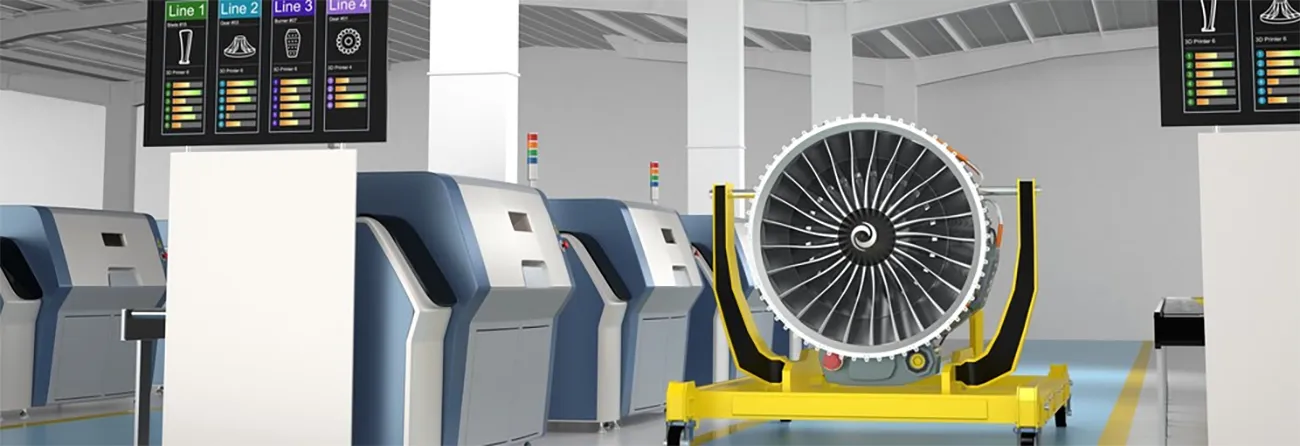
Die Industrielle Fertigung beruhte bis jetzt auf den Bausteinen: Ausgangstoffe, Maschinen/Werkzeuge, Fertigung und dem Prinzip der Skaleneffekte (economies of scale). Bislang haben sich die Infrastruktur und der Zeitaufwand zu großen Teilen an der Fertigung ausgerichtet. In der Modernen Fertigung orientierte man sich meist an den Erkenntnissen von Henry Ford, der es schaffte die Massenfertigung auf völlig neue Grundlagen (Fordismus) zu stellen. Durch die Einführung der „Fließbandfertigung“ wurde die Produktionszeit des einzelnen Produktes radikal reduziert.
Mit der Verbreitung von 3D-Drucktechnologien scheint sich nun eine weitere Revolution anzubahnen. Der 3D-Druck ist in der Lage die benötigte Anzahl an Baugruppen zu reduzieren und die Notwendigkeit Bauteile zusammenzuschweißen zu minimieren, um damit einen enormen Zeitgewinn und damit verbunden natürlich auch eine Kostenreduktion, zu erzielen.
Welchen Einfluss und welche Möglichkeiten der 3D-Druck für die Integrierte Fertigung hat, können Sie im folgenden Artikel nachlesen.
Was ist Integrierte Fertigung?
Grundsätzlich kann man unter Integrierter Fertigung, das Bestreben verstehen, die notwendigen Schritte zur Herstellung eines Produktes zu minimieren. Dieser Prozess beginnt schon beim Design/Erstellung eines Produktes oder von Bestandteilen des Produktes. Die Ingenieure/Designer sind bestrebt die Bauteile (auch wenn diese aus mehreren Bestandteilen bestehen) in einem Objekt zu drucken, sodass ein Zusammenfügen nicht mehr notwendig ist. Die damit verbundene Ersparnis an Produktionszeit schlägt sich auch in einer signifikanten Reduzierung der Produktionskosten nieder.
Populäre Beispiele für den Einsatz des 3D-Drucks, um Fertigungsschritte einzusparen, sind: Ketten, hinterschneidende Bauteile und mittlerweile auch Getriebe, die in einem Stück gedruckt werden können.
Umdenken in der Produktion
Natürlich fallen die Einsparungen in der Produktion nicht vom Himmel. Die Reduzierung der Produktionszeit setzt einen erhöhten Zeiteinsatz in der Design-/Produktentwicklungsphase voraus. Aber dieser Einsatz zahlt sich in aller Regel aus. Die Erstellung integrierter Baugruppen ist grundsätzlich für eine Vielzahl von 3D-Druckmaterialien und -verfahren möglich. Allerdings ist der Prozess für die Verfahren, die Supportstrukturen benötigen (FFF, SLA, Polyjet) etwas schwieriger, als für die pulverbettbasierten Verfahren (Multi Jet Fusion, Colorjet, SLS, SLM). Bei den erstgenannten müssen, um ein funktionstüchtiges Bauteil zu erhalten, die Stützstrukturen entfernt werden. Dies muss beim Entwurf der Bauteile und bei Wahl des 3D-Druckmaterials beachtet werden.
Hier einige Designtipps, die Sie beachten sollten (ausführliche Hinweise finden Sie auf unseren Materialseiten):
- Werden Sie sich im Klaren darüber, welche physische Eigenschaften Ihr Bauteil haben muss.
- Finden Sie heraus, welches Material für Ihr Produkt/ Ihre Anwendung die entsprechenden Eigenschaften aufweist.
- Nachdem Sie sich für ein 3D-Druckmaterial entschieden haben, beachten Sie die Designhinweise auf den Materialseiten.
Wo überall 3D-Druck schon in der Fertigung verwendet wird
Mit der wachsenden Verwendung von Metallen im 3D-Druck interessieren sich auch immer mehr traditionelle Industrieunternehmen für diese Technologie. In der Luftfahrt- und Automobilindustrie beginnt bereits ein Umdenken und immer mehr Firmen setzen den 3D-Druck ein, um Entwicklungszeiten und Kosten zu reduzieren.
- Siemens konnte durch den Einsatz von 3D-Drucktechnologien die Entwicklungszeit ihrer Gasturbinen um sagenhafte 90 % reduzieren. Der 3D-Druck ermöglicht es Siemens, mittlerweile auch Ersatzteile „on demand“ herzustellen. Mehr darüber können Sie hier in der Pressemitteilung von Siemens lesen.
- Die Firma Local Motors aus den USA, hat es geschafft ein funktionstüchtiges Auto aus 49 Teilen herzustellen, für ein traditionell hergestelltes Auto werden etwa 5000-6000 Teile benötigt.
- General Electric hat es dank 3D-Druck geschafft die Anzahl der benötigten nichtbeweglichen Bauteile für einen Turboprop Motor von 900 auf 16 zu reduzieren. Damit einher ging eine Gewichtsreduktion um 35 %.
- Bei Opel hat man einen etwas anderen Weg eingeschlagen. Dort wurde der 3D-Druck für die Herstellung von Werkzeugen verwendet und dabei wurden die Produktionskosten dieser um 90 % reduziert.
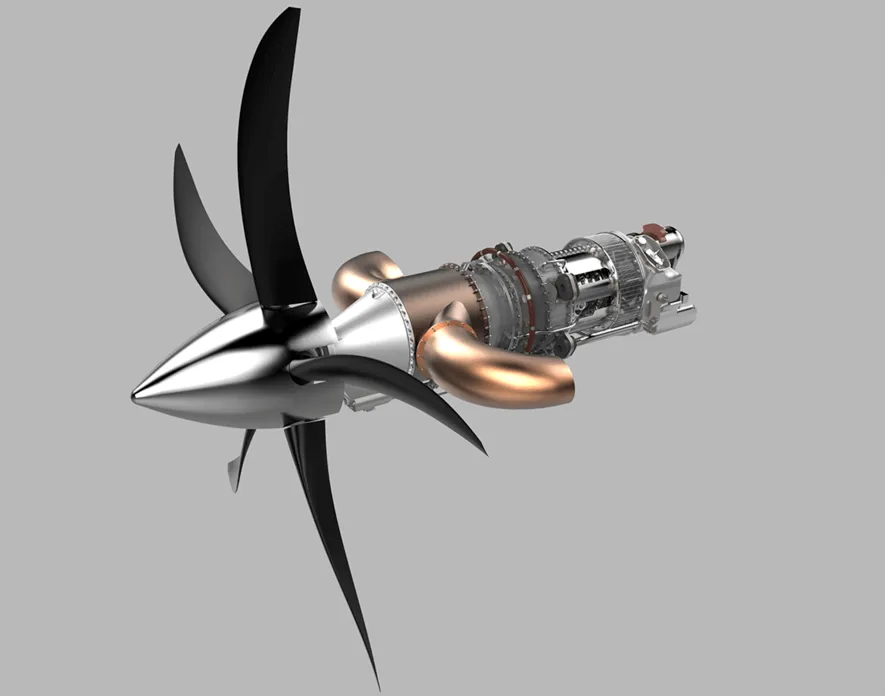
Bild: Turboprop-Motor/GE Aviation
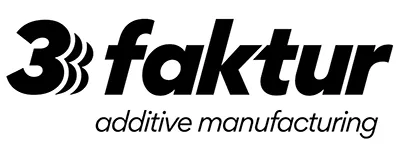
Über 3Faktur: 3Faktur ist Spezialist für 3D-Druck, Rapid Prototyping und Rapid Manufacturing. Wir arbeiten mit dem Multi Jet Fusion-Verfahren von HP und bieten unterschiedliche Materialien für den Prototypenbau und die Serienproduktion an. Sollten Sie Fragen zu Ihrem Projekt haben, können Sie uns gern kontaktieren.