In der heutigen Zeit ist es einfacher denn je, Preise für Dienstleistungen und Produkte zu vergleichen – so auch für die 3D-Druck Dienstleistung. Plattformen und Anbieter mit Online 3D-Druck-Lösungen ermöglichen einen schnellen und unkomplizierten Preisvergleich. Doch worin begründen sich die oft erheblichen Preisunterschiede beim 3D-Druck?
Ähnlich wie bei anderen Produkten und Dienstleistungen, kann ein niedrigerer Preis mit einem reduzierten Serviceangebot oder einem geringeren Qualitätsniveau einhergehen. Doch dieser Zusammenhang ist nicht zwangsläufig. Durch gesteigerte Effizienz in der Produktion lassen sich auch bei hohem Qualitätsstandard günstigere Preise realisieren.
Entscheidend sind die Anforderungen, die an das Produkt gestellt werden. Bei einem günstigen Produktionsprozess, der möglicherweise eine geringere Qualität aufweist, gibt es grundsätzlich nichts zu beanstanden, solange dies für den Kunden transparent ist und die Anwendung dies zulässt. Ein typisches Beispiel hierfür sind einfache Prototypen, die lediglich für einen einmaligen Test genutzt werden.
Wenn es jedoch um Serienbauteile geht, ist ein hohes und reproduzierbares Qualitätsniveau essenziell. Schwankungen in der mechanischen Belastbarkeit des Materials – ein durchaus mögliches Szenario bei additiven Fertigungsverfahren – können die Stabilität der Bauteile beeinträchtigen und somit zu kostspieligen Reklamationen führen. Auch Inkonsistenzen in der Maßhaltigkeit können bei der Montage erhebliche Probleme verursachen oder diese gar unmöglich machen.
Aber welche Faktoren sind es nun, die zu diesen Kostenunterschieden führen? Es gibt zwei Hauptkategorien von Gründen: verfahrensübergreifende und verfahrensspezifische. Erstere umfassen allgemeine Aspekte, wie die Art der eingesetzten Maschinen – beispielsweise für den Heimgebrauch oder industrielle Qualität – oder das Land, in dem die Produktion stattfindet. Die verfahrensspezifischen Gründe sind oft nur für Fachleute erkennbar und hängen mit den Details des jeweiligen Fertigungsverfahrens zusammen, die selbst bei identischen Anlagen und Materialien zu unterschiedlichen Ergebnissen führen können. Dies ist ein komplexes Thema, das wir Ihnen am Beispiel des Multi Jet Fusion Verfahrens näher erläutern werden.
Inhalt
1. Verfahrensübergreifende Faktoren: Die Vielfalt der 3D-Drucktechnologien und -anbieter
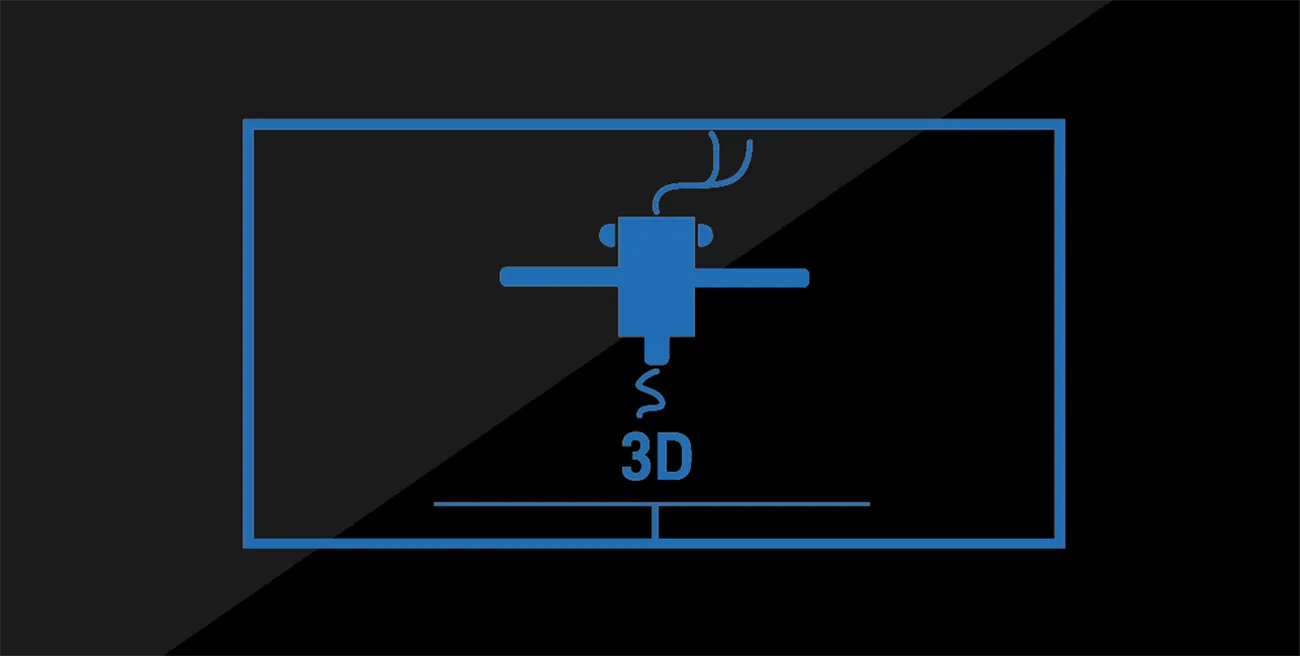
Die Landschaft der 3D-Druckdienstleister und Produktionsmöglichkeiten ist äußerst vielfältig, weshalb im Folgenden nur einige ausgewählte Beispiele beleuchtet werden.
1.1 Diversität der Verfahren
3D-Drucktechnologien sind so unterschiedlich wie die Bauteile, die sie erzeugen (mehr Informationen: Überblick über 3D-Druckverfahren). Jede Technologie hat ihre spezifischen Stärken und Schwächen. Während beispielsweise ein Jetting Drucker von Mimaki oder ein Objet von Stratasys in der Lage ist, vollfarbige und multimateriale Bauteile mit Transparenzen und unterschiedlichen Festigkeiten in einem einzigen Druckvorgang zu erstellen, ist dies für Pulverdrucker, wie die Multi Jet Fusion Anlagen, nicht möglich. Doch gerade die Multi Jet Fusion Technologie punktet mit Effizienz, mechanischer Belastbarkeit und Langlebigkeit – Eigenschaften, die für industrielle Serienbauteile essenziell sind.
1.2 Bandbreite der Maschinen und Anlagen
Die verfügbaren Anlagen variieren enorm in Preis und Leistung, von preiswerten 3D-Druckern für den Hobbybereich bis hin zu hochpreisigen industriellen Systemen. Viele 3D-Druck Dienstleister nutzen „semi-professionelle“ Maschinen, die in der mittleren bis niedrigen fünfstelligen Preisklasse liegen. Diese Geräte können in direkter Konkurrenz zu den industriellen FDM-Druckern von Unternehmen wie Stratasys stehen, wobei der sichtbarste Unterschied oft im Preis liegt. Aber was rechtfertigt diese Preisunterschiede?
- Bauraum und Auflösung: Entgegen der landläufigen Meinung sind die Unterschiede hier oft marginal. Teurere Drucker bieten nicht unbedingt eine höhere Auflösung oder einen größeren Bauraum.
- Materialien: Hier zeigen sich signifikante Unterschiede. Während günstigere Anlagen oft auf Materialien wie PLA oder ABS beschränkt sind, können industrielle Drucker mit anspruchsvolleren Materialien wie PC/ABS, ULTEM oder PEEK umgehen, die eine hohe thermische und mechanische Belastbarkeit aufweisen.
- Mechanische Eigenschaften und Replizierbarkeit: Industrieanlagen bieten durch ihre Materialkonsistenz und ausgefeilte Technik eine hohe Reproduzierbarkeit und enge Toleranz, was zu geringeren Abweichungen über viele Druckzyklen hinweg führt.
Für Konsumprodukte mit niedrigeren Anforderungen kann der Einsatz kostengünstiger Anlagen (z.B. in so genannten „3D Printer Farmen„) sinnvoll sein, während für industrielle Bauteile in Serie oder für funktionale Tests die Investition in die Fertigung mit teuren Systemen gerechtfertigt ist.
1.3 Länderabhängige Kostenunterschiede
Auch international variieren die Kosten für 3D-Druck signifikant. Dies liegt unter anderem an zwei Faktoren:
- Lohnkosten: Diese variieren je nach Automatisierungsgrad der Fertigung und spielen bei hochautomatisierten Prozessen (z.B. in der additiven Serienfertigung) eine geringere Rolle als in manuellen Prozessen, z.B. im Prototypenbau.
- Subventionen: Selbst innerhalb der EU gibt es große Unterschiede in der staatlichen Förderung, was zu differenzierten Kosten und Preissetzungen führt. Außerhalb der EU kann dies noch extremer ausfallen, einige Länder halten sehr hohe Subventionen für die Anschaffung von Anlagen vor.
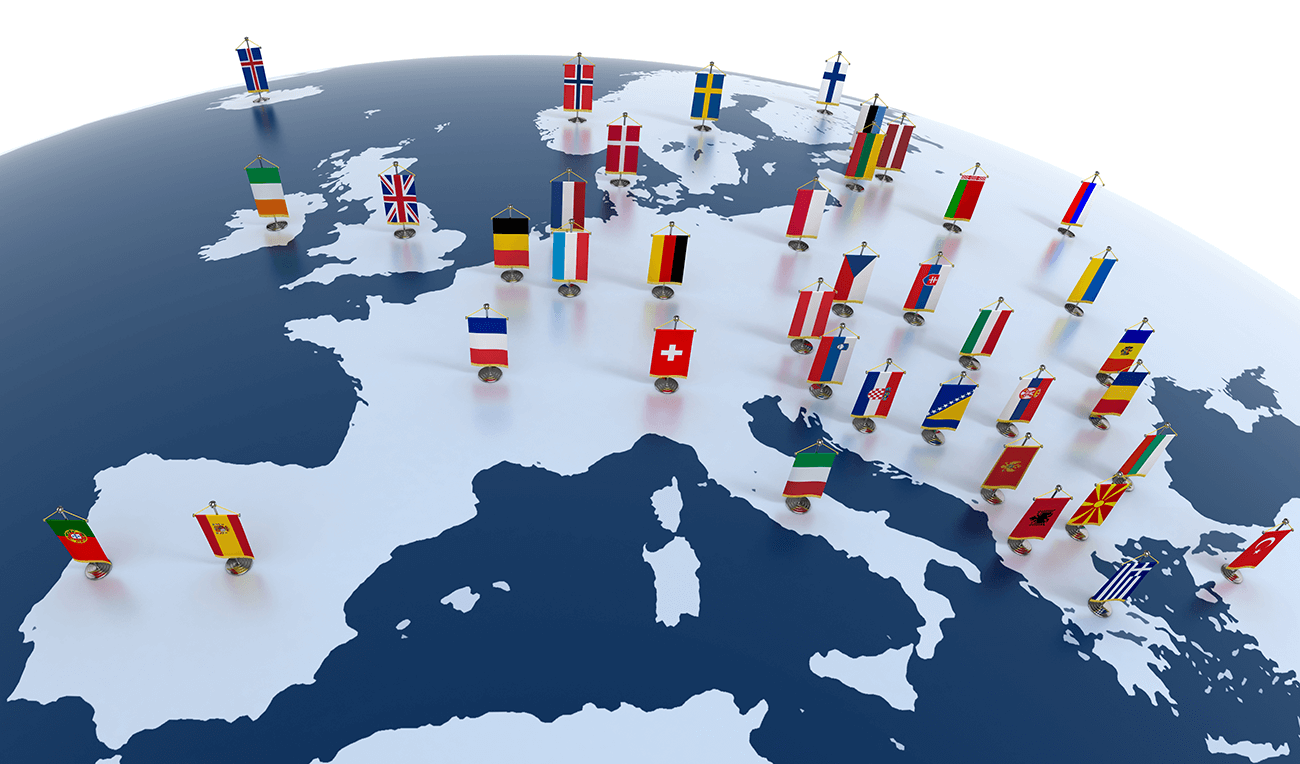
1.4. Geschäftsmodelle und deren Einfluss
Die Geschäftsmodelle und Intentionen hinter dem Einsatz der 3D-Drucktechnologie sind ebenso vielfältig. Als Beispiel seien genannt:
- Auf Prototypen spezialisierte Fertigungen: Hier liegt der Fokus darauf, Teile zu produzieren, die den später in Serie produzierten Bauteilen zum Verwechseln ähnlich sind. Dies erfordert eine breite Palette von Technologien und oft individuelle Bearbeitungsprozesse, was die Kosten erhöht.
- Auf Serien oder Kleinserien spezialisierte Anbieter: Bei diesen stehen Effizienz und hohe Auslastung der Anlagen im Vordergrund, was generell zu günstigeren Kosten führt, allerdings mit weniger Flexibilität im Vergleich zu Dienstleistern, die sich auf Prototypen spezialisieren.
In jedem Fall ist es die spezifische Anwendung, die bestimmt, welches Modell und welche Technologie am wirtschaftlichsten ist.
2. Verfahrensspezifische Gründe am Beispiel Multi Jet Fusion
Der 3D-Druck, weit entfernt von einer einheitlichen Technologie, zeigt eine facettenreiche Palette an Verfahren – jedes mit seinen individuellen Vorteilen und Herausforderungen. Das Verständnis dieser Unterschiede erfordert oft tiefgreifendes Expertenwissen und ist aufgrund der technischen Komplexität für Kunden nicht immer leicht zu durchdringen. Exemplarisch lässt sich dies am Multi Jet Fusion (MJF) Verfahren darstellen, bei dem 3Faktur als einer der ersten Anwender in Europa eine führende Rolle einnimmt und dementsprechend eine ausgeprägte Expertise besitzt.
Es gibt zahlreiche Möglichkeiten, Kosten im 3D-Druckprozess zu optimieren, wobei einige Einsparungen auf Kosten der Qualität gehen können, während andere direkt den Kunden zugutekommen.
Beispiel einer qualitätsorientierten Fertigung:
- Die Produktionsumgebung ist speziell für das MJF-Verfahren optimiert, mit konstanten Umweltbedingungen wie Temperatur, Luftfeuchtigkeit und geringen Vibrationen, gepaart mit hochspezialisierten Anlagen in bestem technischen Zustand.
- Eine konsistente, wiederholbare Bearbeitung wird durch die Definition und konsequente Anwendung eines optimalen Parametersatzes für jedes Bauteil sichergestellt.
- Packdichten werden im optimalen Bereich gefahren und die Pulverqualität wird rigoros überprüft.
- Jeder Produktionsschritt und die fertigen Bauteile unterliegen strengen Qualitätskontrollen; die Prozesse sind standardisiert, dokumentiert und streng kontrolliert.
Beispiel einer kostenoptimierten Fertigung:
- Hier ist die Produktionsumgebung hauptsächlich auf Kostenoptimierung ausgerichtet, wobei Umweltbedingungen oft wenig kontrolliert werden.
- Der Parametersatz ist auf Kosteneffizienz getrimmt, manchmal zu Lasten der Konsistenz.
- Es werden hohe Packdichten gefahren, was nicht selten zu erhöhter Pulverdegradation, reduzierter mechanischer Belastbarkeit, größeren Maßabweichungen und schlechteren Oberflächenqualitäten führt.
- Prozesse und Qualitätskontrollen können lückenhaft sein und sind häufig nach ökonomischen statt nach qualitätsorientierten Kriterien optimiert.
Bei einer kostenoptimierten Fertigung sind erhebliche Kostenvorteile möglich, jedoch geht dies zu Lasten des Qualitätsniveaus – wie bei Maßabweichungen, Homogenität der Oberflächen, mechanischer Belastbarkeit und Wiederholbarkeit. Im Gegensatz dazu erzielt eine qualitätsorientierte Fertigung in diesen Punkten deutlich bessere Ergebnisse, allerdings verbunden mit entsprechenden Kosten.
In den folgenden Abschnitten werden wir detailliert erklären, welchen Einfluss diese Faktoren haben und wie sie sich in der Praxis des 3D-Drucks manifestieren.
2.1 Arbeitsvorbereitung und Orientierung
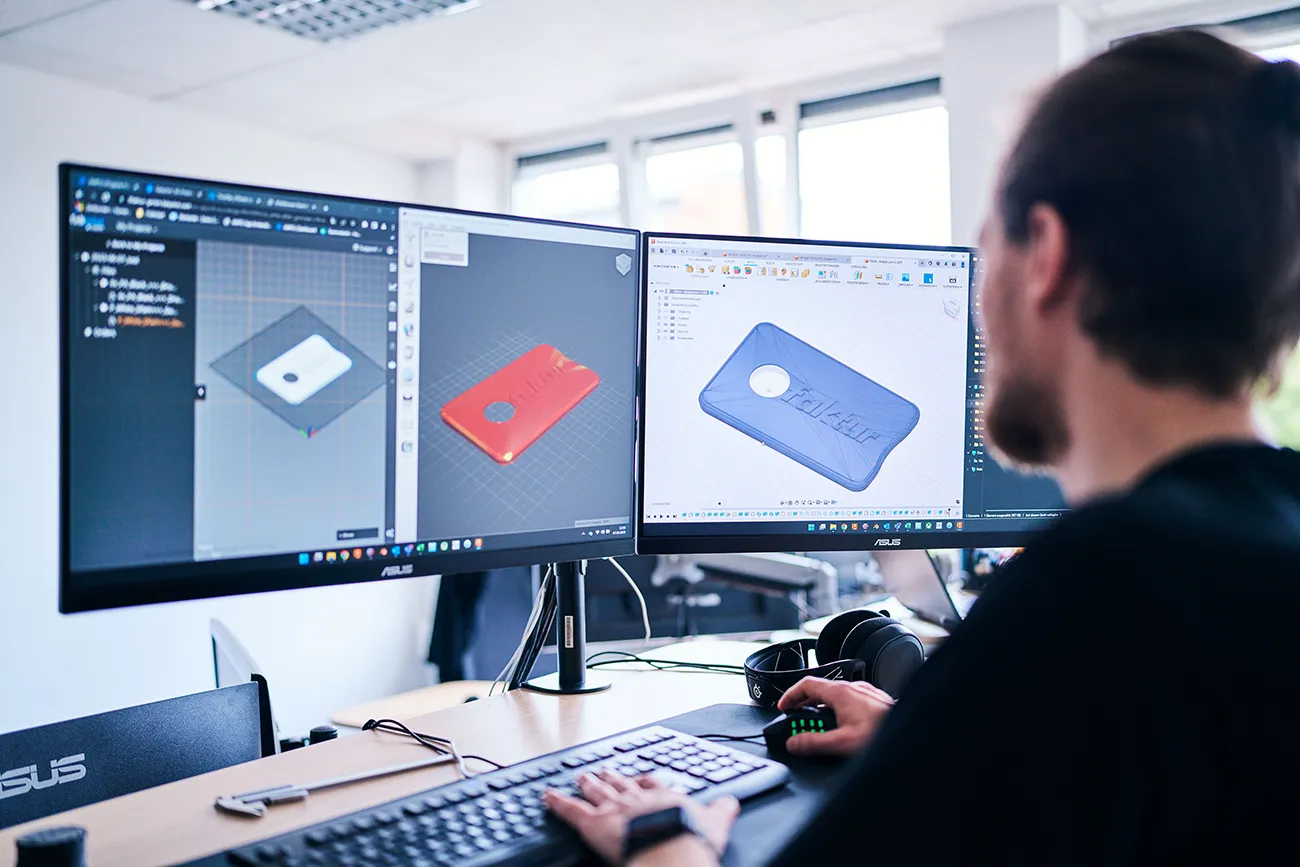
Die Vorbereitung eines jeden Bauteils im 3D-Druckprozess ist eine Kunst für sich, die mit der Ermittlung des optimalen Parametersatzes beginnt. Ein wesentlicher Aspekt hierbei ist die Orientierung des Bauteils während des Drucks. Dieser Schritt wird bei 3Faktur mit größter Sorgfalt behandelt, um sicherzustellen, dass auch bei Wiederholbestellungen die Orientierung konstant bleibt, was die Konsistenz und die Qualität der Endprodukte maßgeblich beeinflusst. Dies wenden wir auch auf andere wichtige Parameter im Druckprozess an.
Einfluss auf die Qualität:
Die Ausrichtung des Bauteils im Druckraum hat einen erheblichen Einfluss auf die Oberflächengüte und Homogenität. Da jede Seite eines 3D-gedruckten Objekts leicht variierte Oberflächencharakteristika aufweisen kann, ist eine gleichbleibende und optimierte Ausrichtung von großer Bedeutung.
Die Orientierung beeinflusst auch maßgeblich die Maßhaltigkeit, insbesondere in der Z-Richtung, wo Abweichungen deutlich stärker ausfallen können als auf der X/Y-Ebene. Bei wechselnder Orientierung ragen verschiedene Seite des Bauteils in Z-Richtung und führen dadurch zu höheren Abweichungen in der Maßhaltigkeit.
Kostensenkungspotenzial:
Durch die Anwendung von kostenoptimierten Orientierungen ist es möglich, höhere Packdichten zu erzielen, was das Potenzial für erhebliche Kosteneinsparungen bietet, gleichzeitig aus Qualitätssicht sehr bedenklich ist (siehe unten).
Weiterhin wird der Prozess der Arbeitsvorbereitung, eine sonst kostenintensive Phase, erheblich vereinfacht. Dies ermöglicht es, Kosten zu sparen, indem man Personal einspart und auf weniger qualifiziertes Personal zurückgreift.
Erkennungsmerkmale für Qualitätsmängel:
Unterschiede in der Oberflächenbeschaffenheit und Maßhaltigkeit sind oft mit bloßem Auge sichtbar, wenn man zwei Bauteile miteinander vergleicht.
Diese Phänomene treten insbesondere hervor, wenn Chargen mit unterschiedlichen Ausrichtungen verglichen werden. In einer Produktion, die stark auf Kosteneffizienz ausgerichtet ist, findet man bisweilen selbst innerhalb einer Charge variierende Orientierungen – eine Praxis, die sich rein nach Kostenoptimierung richtet.
Der Ansatz von 3Faktur:
Bei 3Faktur wird kein Kompromiss eingegangen, wenn es um die Arbeitsvorbereitung geht. Jedes Bauteil wird sorgfältig geprüft, und die optimalste Orientierung und Produktionsparameter werden gewählt.
Zudem wird bei jedem Bauteil überprüft, ob es bereits in der Vergangenheit produziert wurde, und es wird sichergestellt, dass die Parameter vergangener Chargen für eine durchgängige Konsistenz übernommen werden.
2.2 Packdichte: Ein Schlüsselelement im Pulverdruck
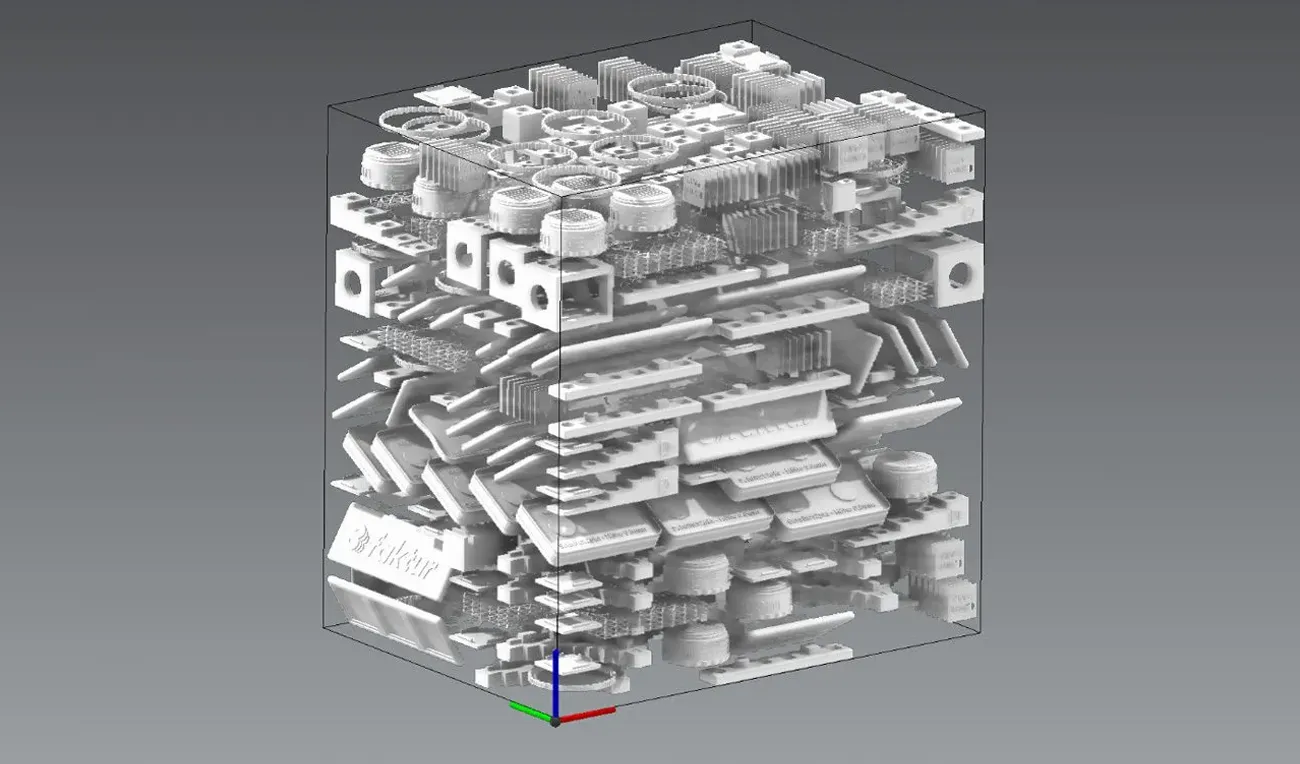
Beim Pulverdruck, sowohl bei Multi Jet Fusion als auch beim Lasersintern, wird der gesamte Bauraum beim Druck zu 100% mit Pulver gefüllt. Doch nicht das gesamte Pulver wird zu Bauteilen verschmolzen; ein bestimmter Prozentsatz bleibt als loses Restpulver übrig. Die Packdichte ist das Maß dafür, wie viel des Pulvers tatsächlich in Bauteile umgewandelt wird.
Beispiel für Packdichte:
Betrachten wir einen hypothetischen Bauraum von 10 x 10 x 10 cm, also ein Volumen von 1.000 cm³. Bei einer Packdichte von 10% würden 100 cm³ dieses Volumens in Bauteile umgewandelt, während 900 cm³ als Restpulver zurückbleiben.
Einfluss auf die Qualität:
Mit steigender Packdichte erhöht sich die thermische Belastung des nicht zu Bauteilen verarbeiteten Restpulvers beträchtlich. Während des Bauprozesses, der bei hohen Temperaturen abläuft, kann diese erhöhte Belastung zu einer Degradation des Pulvers führen.
Dies setzt sich im Abkühlprozess fort, der beim Multi Jet Fusion Verfahren typischerweise zwischen 36 und 48 Stunden dauern kann. Sind mehr Bauteile im Bauraum vorhanden, die wärmer sind als das Restpulver, fungieren diese quasi als Heizkörper und halten die Temperatur des Pulvers hoch. Dabei steigt die thermische Belastung des Pulvers (höhere Temperatur über einen längeren Zeitraum).
Als Resultat der anhaltenden Hitzeexposition kann das Pulver eine starke Degradierung erfahren, was die mechanischen Eigenschaften der daraus gefertigten Bauteile erheblich beeinträchtigt. Dabei kann die mechanische Belastbarkeit der Bauteile um bis zu 50 % reduziert werden.
Neben der reduzierten Belastbarkeit können auch sichtbare Oberflächenschäden, wie Orangenhaut oder Elefantenhaut sowie ein zunehmender Verzug der Bauteile auftreten. Diese Effekte sind nicht nur kosmetischer Natur, sondern können auch die Funktionalität und Passgenauigkeit der Bauteile beeinträchtigen.
Die wissenschaftliche Literatur, wie die Studie von Wegner et al. (2014), bietet eine tiefergehende Betrachtung dieser Phänomene und unterstreicht die Notwendigkeit, die Packdichte sorgfältig zu kontrollieren, um die Integrität der Materialien zu bewahren und die Lebensdauer der Bauteile zu sichern.
Ein zu hoher Grad an Materialdegradation kann das Risiko erhöhen, dass Bauteile unter normalen Betriebsbedingungen versagen, was besonders in sicherheitskritischen Anwendungen problematisch ist. In Summe verdeutlicht die Betrachtung der Packdichte die komplexe Balance zwischen Kosteneffizienz und Qualitätssicherung im 3D-Druck und unterstreicht die Notwendigkeit, jeden Aspekt des Druckprozesses zu verstehen und angemessen zu steuern.
Kostensenkungspotenzial:
Das Potenzial zur Kostensenkung durch die Erhöhung der Packdichte ist enorm, da Anbieter damit die Menge der gleichzeitig druckbaren Teile steigern können. Dies resultiert in niedrigeren Kosten pro Volumeneinheit des fertigen Materials.
Betrachten wir ein hypothetisches Beispiel: In einem Bauraum von 1.000 cm³ mit einer Packdichte von 10 % entstehen 100 cm³ gedruckte Bauteile. Bei einer Auffrischrate von 20% ist es jedoch notwendig, zusätzlich 100 cm³ Pulver zu entsorgen, da ein Fünftel des Pulvers im Druckprozess durch frisches Material ersetzt werden muss. Dies bedeutet, dass insgesamt 200 cm³ Pulver für den Druck verwendet werden, was bei einem (fiktiven) Pulverpreis von 100 EUR für 1.000 cm³ zu Kosten von 20 EUR führt. Der Preis pro Volumeneinheit für die produzierten Bauteile liegt damit bei 0,20 EUR pro cm³ (20 EUR geteilt durch 100 cm³).
Wenn die Packdichte auf 20 % angehoben wird, verdoppelt sich das Volumen der produzierten Bauteile auf 200 cm³, ohne dass zusätzliches Pulver entsorgt werden muss, da die Auffrischrate von 20 % beibehalten wird. In diesem Fall bleiben die Gesamtkosten für das Pulver unverändert bei 20 EUR, was die Kosten pro Volumeneinheit auf 0,10 EUR pro cm³ reduziert (20 EUR geteilt durch 200 cm³ produzierte Bauteile). Dies bedeutet eine Halbierung der Kosten pro Volumeneinheit.
Solche Anpassungen der Packdichte sind eine häufig genutzte Strategie von Billiganbietern, mit den o.g. Konsequenzen für die erzielte Qualität.
Erkennungsmerkmale für Qualitätsmängel:
- Oberflächenschäden: Selbst unter optimalen Prozessbedingungen können Oberflächenschäden auftreten, diese sind meist bei höheren Wandstärken häufiger anzutreffen. Wenn solche Schäden auch bei dünnen Wandstärken und regelmäßig auftreten, könnte dies auf zu hohe Packdichten hinweisen.
- Mechanische Belastbarkeit: Falls der Verdacht besteht, dass der Anbieter die Packdichte zu hoch ansetzt, kann ein Test in Form von Zugmessstäben, die in einer definierten Orientierung gedruckt (im Zweifelsfall in Z-Richtung orientieren) und dann vermessen werden, Klarheit schaffen. Signifikante Abweichungen, bspw. der Zugfestigkeit, von den Material-Herstellerangaben oder starke Schwankungen zwischen den Chargen können auf eine schlechte Pulverqualität deuten.
- Farbveränderungen: Ein deutlicher Indikator für zu hohe Packdichten ist eine Verfärbung der Bauteile. Insbesondere bei weißen Bauteilen kann eine Gelbfärbung auftreten, die bei hohen Packdichten erkennbar wird. Sollte ein Bauteil merklich gelber als erwartet ausfallen, ist dies ein klares Zeichen für eine übermäßige Pulverdegradierung.
Erwähnenswert ist noch der Zusammenhang zwischen Packdichte und Auffrischrate: Die Packdichte ist eng mit der Auffrischrate verbunden. Im Multi Jet Fusion-Verfahren wird standardmäßig mit einer Auffrischrate von 20 % Neupulver gearbeitet. Theoretisch könnten höhere Packdichten bei gleichbleibender Qualität realisiert werden, indem die Auffrischrate erhöht wird, was jedoch die Kostenersparnis negieren würde. Beim Lasersintern ist es nicht unüblich, dass Anbieter die empfohlene Auffrischrate von 50 % auf geringere Werte, z.B. 30 %, reduzieren, was zu den gleichen Problemen der Pulverdegradierung führt und gelbe Bauteile hervorbringen kann (allerdings enorm Kosten spart). Beim Multi Jet Fusion ist dies kaum möglich, da die Auffrischrate mit 20 % schon sehr niedrig ist und geringere Auffrischraten technisch nicht umsetzbar sind.
Der Ansatz von 3Faktur:
Bei 3Faktur wird die Packdichte als wesentlicher Qualitätsfaktor mit größter Sorgfalt behandelt. Der Ansatz des Unternehmens in Bezug auf die Packdichte folgt klaren Grundsätzen, um höchste Qualität zu gewährleisten:
- 3Faktur hat sich für eine mittlere Packdichte von etwa 9,5 % entschieden, was am unteren Ende des von HP empfohlenen optimalen Bereichs liegt. Diese Entscheidung ermöglicht eine ausgewogene Balance zwischen effizienter Ressourcennutzung und einem hohen Qualitätsniveau, das sich unter anderem in einer stabilen mechanischen Belastbarkeit der Bauteile und konsistenter Maßhaltigkeit über viele Produktionszyklen hinweg manifestiert.
- Weiterhin wird nach jedem Druckvorgang das Restpulver mit standardisierten Messverfahren geprüft (bspw. auf Farbveränderungen). So wird sichergestellt, dass nur Pulver von ausreichender Qualität für weitere Druckvorgänge verwendet wird. Durch dieses Vorgehen werden mögliche negative Auswirkungen von Abweichungen im Pulver durch angepasste Auffrischraten ausgeglichen und die Konsistenz des Endprodukts gesichert.
Die konsequente Umsetzung dieser Praktiken zeigt, dass 3Faktur das Kosteneinsparpotenzial durch Anpassungen der Packdichte erkennt, aber nicht zulasten der Produktqualität nutzen wird. Dieses Engagement für Qualität stellt sicher, dass die Endprodukte nicht nur wirtschaftlich, sondern auch von hoher Güte sind, was den Mehrwert für den Kunden maximiert.
2.3 Abkühlzeit
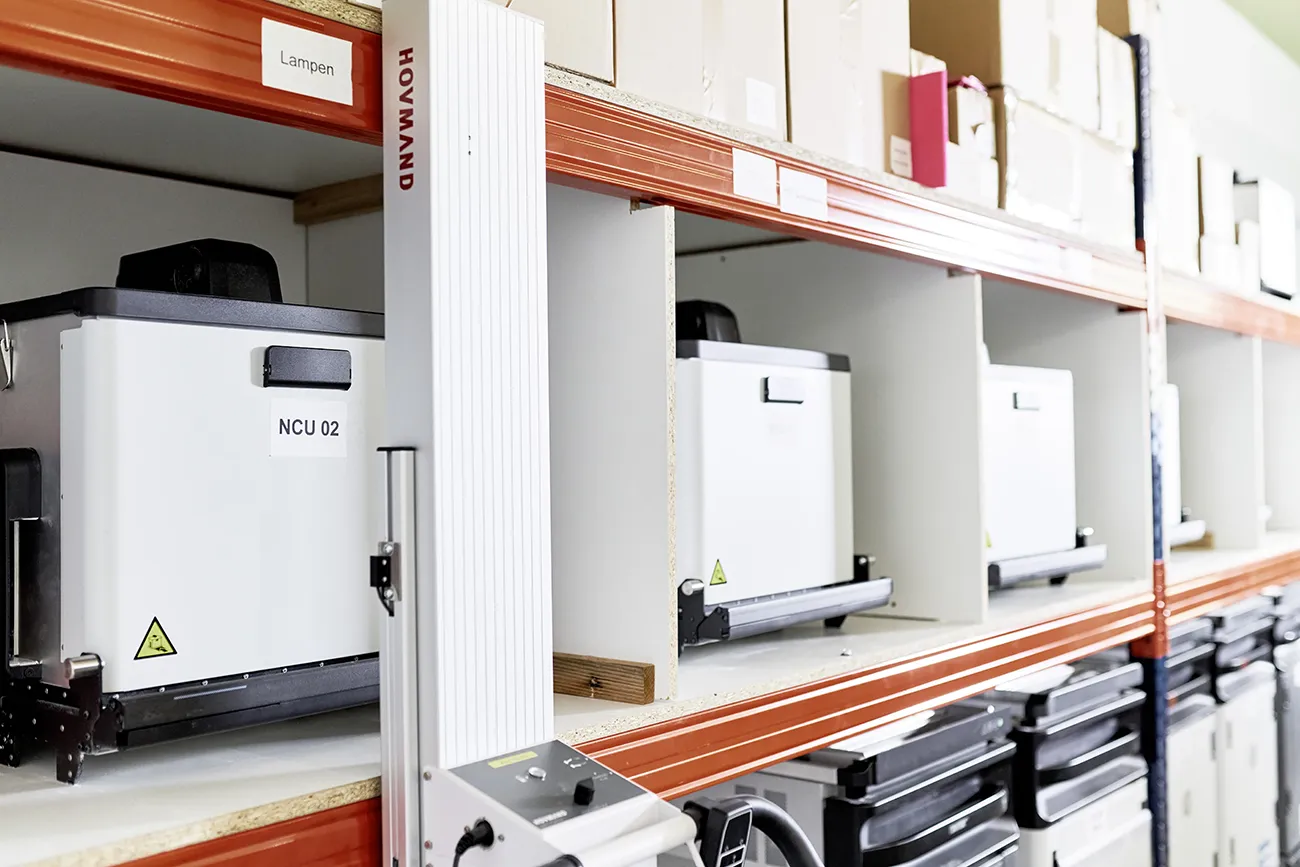
Der Abkühlprozess nach dem 3D-Druck ist ein kritischer Schritt, der entscheidend für die Endqualität der produzierten Bauteile ist.
Einfluss auf die Qualität:
Der Bauraum erfordert eine Abkühlzeit von typischerweise 36 bis 48 Stunden. Diese Zeitspanne ist notwendig, um eine gleichmäßige und verzugsfreie Abkühlung der Bauteile zu gewährleisten. Die Abkühlzeit hat dabei einen geomtrieabhängigen Einfluss auf die Qualität der Bauteile. Während einige Materialien, wie TPU, flexibler auf die Abkühlbedingungen reagieren können, ist bei anderen, insbesondere bei Polyamid 12, eine langsame und kontrollierte Abkühlung essentiell, um Maßungenauigkeiten und Verzug zu minimieren.
Zu schnelle Abkühlzeiten können insbesondere bei verzugsanfälligen Bauteilen zu Ungenauigkeiten und Qualitätsmängeln führen.
Kostensenkungspotenzial:
Die Kostenersparnis durch verkürzte Abkühlzeiten ist im Gesamtkontext der Produktion eher gering. Allerdings wird eine erhöhte Durchlaufgeschwindigkeit erzielt und verkürzt die Vorlaufzeiten entsprechend.
Erkennungsmerkmale für Qualitätsmängel:
Ungenauigkeiten, Oberflächenschäden und starker Verzug, besonders bei größeren und flächigen Bauteilen, sind typische Anzeichen für eine unzureichende Abkühlzeit.
Anbieter, die ungewöhnlich kurze Produktionszeiten anbieten, könnten dies möglicherweise durch eine Verringerung der Abkühlzeit erreichen. Normalerweise dauert ein Zyklus rd. vier Tage – Druck am ersten Tag, am zweiten und dritten Tag erfolgt die Abkühlung, am vierten Tag werden die Bauteile nachbearbeitet. Drei Tage sind möglich, wenn am ersten Tag der Druck schon früh am Tag gestartet wird. Kürzere Vorlaufzeiten können nur realisiert werden, wenn keine vollen Bauräume produziert werden, was sehr teuer ist, oder eben die Abkühlzeit reduziert wird.
Der Ansatz von 3Faktur:
3Faktur hält eine langsame und gleichmäßige Abkühlzeit von mindestens 36 Stunden, im Durchschnitt sogar über 45 Stunden für alle Chargen ein. Dieses Verfahren stellt sicher, dass jedes Bauteil die nötige Zeit erhält, um sich durch Wärme induzierte Probleme zu stabilisieren.
2.4 Qualitätskontrollen
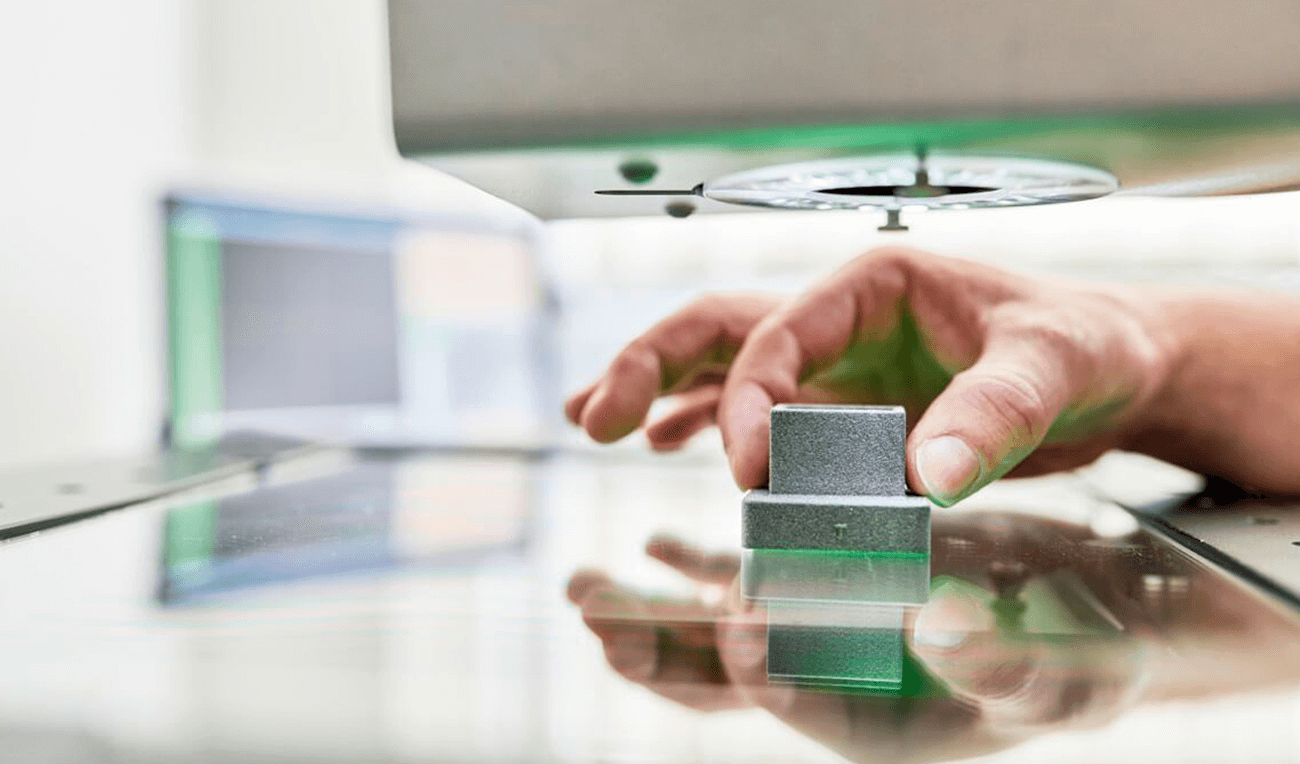
Im 3D-Druck ist die Qualitätskontrolle ein entscheidendes Element, das die Integrität und Zuverlässigkeit der Endprodukte sicherstellt. Bei 3Faktur wird ein umfassendes Qualitätsmanagement umgesetzt, das (vereinfacht) in zwei Hauptbereichen untergliedert ist: die Prozesskontrollen während der Fertigung und die Endkontrolle der fertigen Bauteile.
Einfluss auf die Qualität:
Unzureichende Qualitätskontrollen in jedem dieser Schritte können zu nicht reproduzierbaren und stark abweichenden Ergebnissen führen. Solche Variabilitäten in der Produktion sind nicht nur für den Anbieter in Bezug auf Material- und Zeitaufwand kostspielig, sondern auch für den Kunden, der mit erhöhtem Ausschuss konfrontiert werden kann.
Kostensenkungspotenzial:
Die Optimierung von Qualitätskontrollen hat großes Potenzial zur Kostensenkung, da intensive manuelle Prüfungen personal- und zeitaufwendig sind.
Erkennungsmerkmale für Qualitätsmängel:
Eine hohe Rate an Ausschuss und signifikante Schwankungen in der Qualität der produzierten Bauteile können auf unzureichende Qualitätskontrollen bzw. Qualitätsmanagement hinweisen. Diese Probleme offenbaren sich oft durch inkonsistente Maße, funktionale Defizite oder sichtbare Mängel an den Bauteilen.
Der Ansatz von 3Faktur:
3Faktur verpflichtet sich zu lückenloser Dokumentation und Kontrolle jedes Schrittes im Fertigungsprozess. Die Endkontrolle der Bauteile erfolgt mithilfe automatisierter Systeme, die eine hohe Anzahl von Messpunkten und Bauteileigenschaften erfassen können, weit über das, was manuell möglich wäre. Diese automatisierten Messungen werden durch Sichtkontrollen und selektive manuelle Prüfungen ergänzt, insbesondere dort, wo automatisierte Methoden an ihre Grenzen stoßen könnten.
2.5 Nachbearbeitung & Ausstattung der Prozesskette
Für eine effiziente, qualitativ hochwertige und konsistente Bearbeitung der Bauteile nach erfolgtem 3D Druck ist die Verwendung hochspezialisierter und für das Multi Jet Fusion (MJF) Verfahren adäquater Anlagen und Prozesse notwendig.
Einfluss auf die Qualität:
Der Einsatz spezialisierter Anlagen, z.B. für die Reinigung oder Oberflächenbearbeitung der Bauteile, trägt wesentlich zur Erzielung hochwertiger und konsistenter Ergebnisse bei.
Kostensenkungspotenzial:
Obwohl die Anschaffungskosten für spezialisierte Anlagen hoch sein können, ist das Kostensenkungspotenzial moderat, da diese Systeme häufig mit einem hohen Automatisierungsgrad einhergehen. Der dadurch geringere manuelle Aufwand und die erhöhte Effizienz können die höheren Initialkosten teilweise oder sogar vollständig ausgleichen.
Dies gilt allerdings in der Regel nur bei hoher Auslastung der Anlagen. Kleinere Dienstleister bzw. Fertigungen mit einer begrenzten Anzahl von Anlagen können die Kosten für solche spezialisierten Geräte oft nicht vollständig amortisieren und greifen daher u.U. auf weniger professionelle Lösungen zurück.
Erkennungsmerkmale für Qualitätsmängel:
Merkmale umfassen unsaubere Bauteile mit Restpulver, inhomogene Oberflächenbeschaffenheit und ungleichmäßige Farbverteilungen auf den Bauteilen.
Der Ansatz von 3Faktur:
3Faktur stellt eine der modernsten und umfangreichsten Prozessketten für das MJF-Verfahren bereit. Dies beinhaltet eine durchdachte Auswahl an Geräten und Prozessen, die auf maximale Qualität und Effizienz ausgelegt sind, um den Anforderungen des MJF-Verfahrens gerecht zu werden und die bestmöglichen Endprodukte zu liefern.
2.6 Auslastung
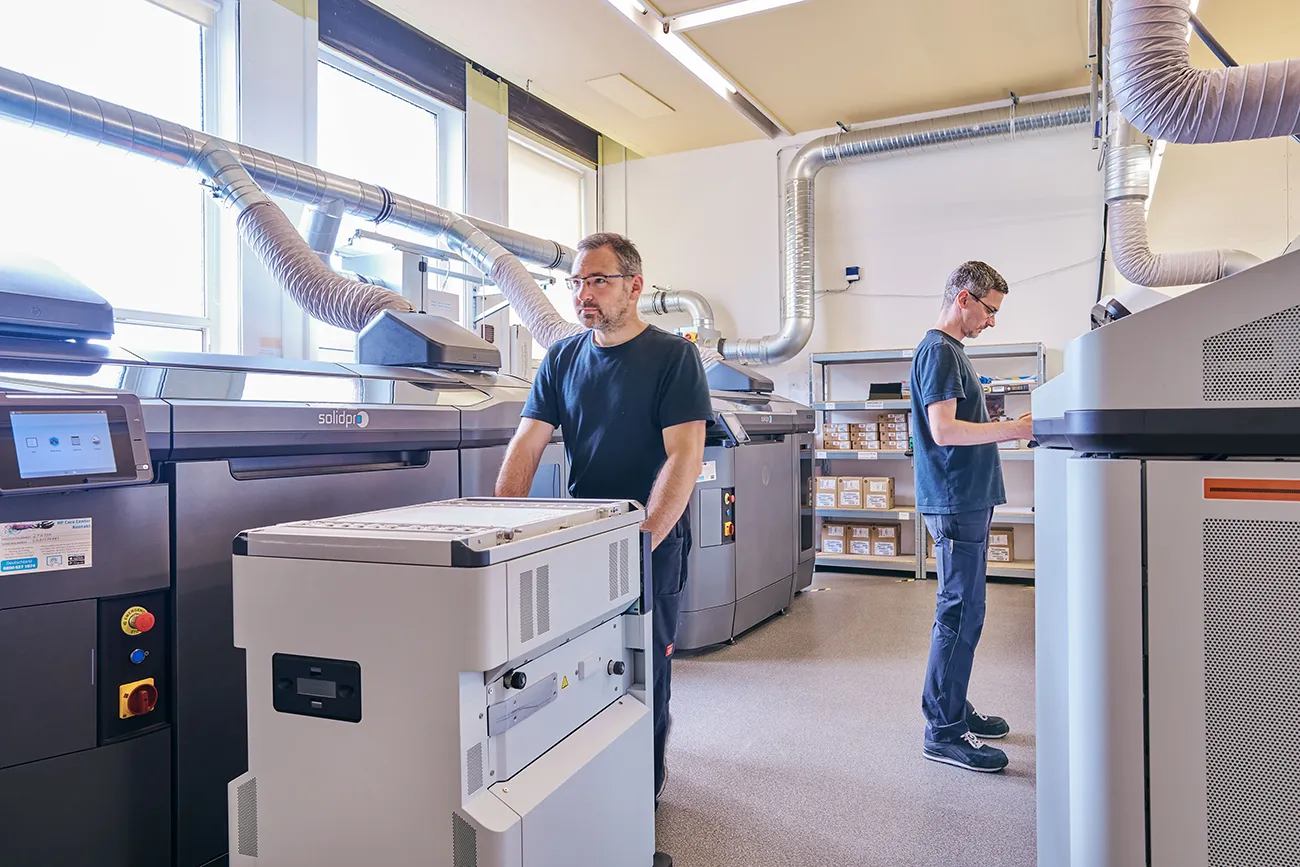
Industrielle 3D-Drucker stellen eine beträchtliche Investition dar. Eine hohe Auslastung ist notwendig, um die Kosten pro Bauteil zu senken.
Einfluss auf die Qualität:
Grundsätzlich keine, da mit optimalen Abläufen und dem Einsatz geeigneter Anlagen und Peripheriegeräte auch bei hoher Auslastung eine gleichbleibend hohe Qualität gewährleistet werden kann. Sind diese nicht gegeben, kann es zu Unordnung und einem Qualitätsverlust kommen (salopp: „Chaos“).
Kostensenkungspotenzial:
Die Maximierung der Auslastung ist eine effektive und bewährte Methode, um Kosten zu reduzieren, ohne bei der Qualität Abstriche zu machen.
Erkennungsmerkmale für Qualitätsmängel:
Negative Anzeichen einer unzureichenden Prozesskette bei hoher Auslastung können häufige Lieferverzögerungen, schwankende Qualität und die Lieferung falscher oder defekter Bauteile sein. Im positiven Szenario ermöglicht eine hohe Auslastung mit optimierten Prozessen ein niedriges Preisniveau bei gleichbleibend hoher Qualität der Bauteile.
Der Ansatz von 3Faktur:
3Faktur nutzt eine hochspezialisierte Prozesskette, die für hohe Volumen konzipiert ist und einen der höchsten Automatisierungsgrade in der additiven Kunststoff-Fertigung aufweist. Zum Einsatz kommen fortschrittliche Technologien wie KI-basierte Sortiersysteme, automatisierte Verpackungs- und Messsysteme sowie robotergesteuerte Nachbearbeitungsprozesse und Auspackanlagen. Diese hochautomatisierte und effiziente Produktionsweise ermöglicht es 3Faktur, eine sehr hohe Auslastung zu erreichen und somit beste Qualität zu fairen Preisen anzubieten.
Durch die Kombination aus hochentwickelter Technologie und straffen Prozessen stellt 3Faktur sicher, dass die hohen Investitionen in die Produktionsanlagen sich nicht nur durch geringere Stückkosten, sondern auch durch eine hohe Produktqualität auszahlen. Dieses Modell dient als Grundlage für ein nachhaltiges Geschäft, das die Bedürfnisse der Kunden nach kosteneffizienten, qualitativ hochwertigen 3D-gedruckten Bauteilen erfüllt.
2.7 Hinweise für Nutzer von 3D-Druck Plattformen
Bei der Auswahl eines 3D-Druckdienstes über Plattformen ist Vorsicht geboten: Einige Plattformen kommunizieren nicht transparent darüber, welcher Anbieter den Druck durchführt. Verschiedene Anbieter können zu Qualitätsschwankungen führen, da jede Charge möglicherweise von einem anderen Anbieter produziert wird. Dies kann für Serienbauteile, bei denen die Konsistenz entscheidend ist, problematisch sein.
3. Fazit
Zum Abschluss gilt der altbekannte Rat: Entscheidungen sollten nicht allein auf der Grundlage des Preises getroffen werden. Eine umfassende Betrachtung aller relevanten Faktoren wie Qualitätssicherungsmaßnahmen, Packdichten und die Konsistenz der Fertigungsprozesse ist entscheidend.
Es ist wichtig, bei der Auswahl eines Anbieters kritische Fragen zu stellen und zu erfahren, wie dieser mit Qualitätskontrollen, Prozessreplizierbarkeit und anderen Schlüsselfaktoren umgeht. Zertifizierungen, besonders die ISO/ASTM 52920, die spezifische Qualitätsstandards für additive Fertigungsprozesse vorgibt, können als Indikatoren für die Verpflichtung eines Unternehmens zu Qualität und Zuverlässigkeit dienen. Diese Norm gibt Aufschluss über die Verfahrensweisen eines Unternehmens und seine Qualitätsphilosophie. 3Faktur ist nach dieser Norm zertifiziert, was unser Engagement für Qualität und kontinuierliche Verbesserung unterstreicht. Für eine Übersicht zertifizierter Unternehmen im Bereich der additiven Fertigung können Sie die TÜV SÜD-Webseite besuchen.