In today’s era, it’s easier than ever to compare prices for services and products – this includes 3D printing services. Platforms and providers offering online 3D printing solutions enable a quick and straightforward price comparison. But what are the reasons behind the often significant price differences in 3D printing?
Similar to other products and services, a lower price may be associated with a reduced range of services or a lower level of quality. However, this correlation is not inevitable. Increased efficiency in production can also realize more affordable prices while maintaining a high standard of quality.
Crucial are the requirements set for the product. In the case of an inexpensive production process, which might have lower quality, there is fundamentally nothing to criticize as long as this is transparent to the customer and the application allows it. A typical example is simple prototypes used only for a one-time test.
However, when it comes to series components, a high and reproducible quality level is essential. Variations in the mechanical load capacity of the material – a quite possible scenario in additive manufacturing processes – can affect the stability of the components and thus lead to costly complaints. Also, inconsistencies in dimensional accuracy can cause significant problems in assembly or even make it impossible.
But what are the factors that lead to these cost differences? There are two main categories of reasons: process-independent and process-specific. The former includes general aspects, such as the type of machines used – for example, for home use or industrial quality – or the country where production takes place. The process-specific reasons are often only recognizable to experts and are related to the details of the respective manufacturing process, which can lead to different outcomes even with identical equipment and materials. This is a complex topic that we will explain to you using the example of the Multi Jet Fusion process.
Content
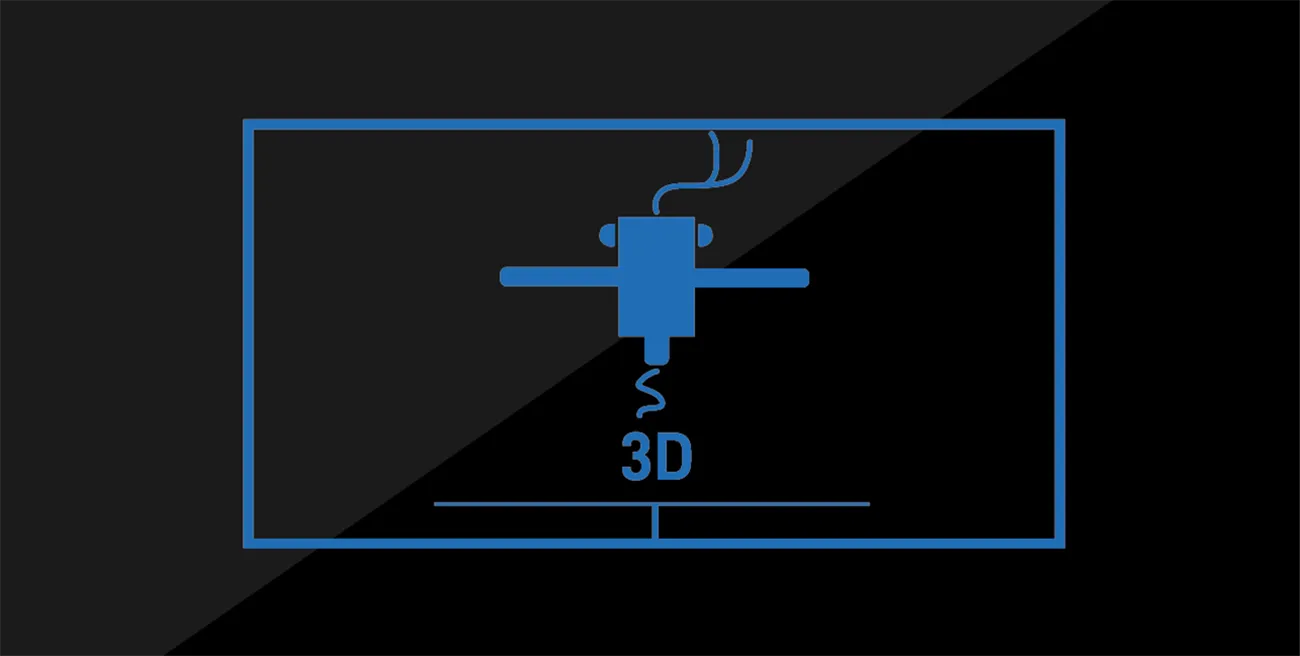
1. Process-Independent Factors: The Variety of 3D Printing Technologies and Providers
The landscape of 3D printing service providers and production capabilities is extremely diverse, so only a few selected examples will be highlighted here.
1.1 Diversity of Processes
3D printing technologies are as varied as the parts they produce (more information: Overview of 3D Printing Processes). Each technology has its specific strengths and weaknesses. For instance, a Jetting printer from Mimaki or an Objet from Stratasys is capable of creating full-color and multi-material parts with transparencies and varying strengths in a single printing process, something not possible for powder printers like the Multi Jet Fusion systems. However, the Multi Jet Fusion technology excels in efficiency, mechanical durability, and longevity – attributes essential for industrial serial components.
1.2 Range of Machines and Equipment
The available machines vary enormously in price and performance, from affordable 3D printers for hobbyists to high-priced industrial systems. Many 3D printing service providers use “semi-professional” machines that fall in the mid to low five-figure price range. These devices can directly compete with industrial FDM printers from companies like Stratasys, with the most visible difference often being the price. But what justifies these price differences?
- Build Volume and Resolution: Contrary to popular belief, the differences here are often marginal. More expensive printers do not necessarily offer higher resolution or a larger build volume.
- Materials: Significant differences are evident here. While cheaper machines are often limited to materials like PLA or ABS, industrial printers can handle more demanding materials like PC/ABS, ULTEM, or PEEK, which exhibit high thermal and mechanical resilience.
- Mechanical Properties and Reproducibility: Industrial machines provide high reproducibility and tight tolerances due to their material consistency and sophisticated technology, leading to fewer deviations over many print cycles.
For consumer products with lower requirements, the use of cost-effective equipment (e.g., in so-called “3D Printer Farms“) can be sensible, while for industrial serial components or functional testing, the investment in manufacturing with expensive systems is justified.
1.3 Country-Dependent Cost Differences
Internationally, the costs for 3D printing vary significantly. This is due to two factors, among others:
- Labor Costs: These vary depending on the degree of automation in manufacturing and play a lesser role in highly automated processes (e.g., in additive serial production) than in manual processes, for example, in prototype construction.
- Subsidies: Even within the EU, there are significant differences in government funding, leading to differentiated costs and pricing. Outside the EU, this can be even more extreme, with some countries offering very high subsidies for the acquisition of equipment.
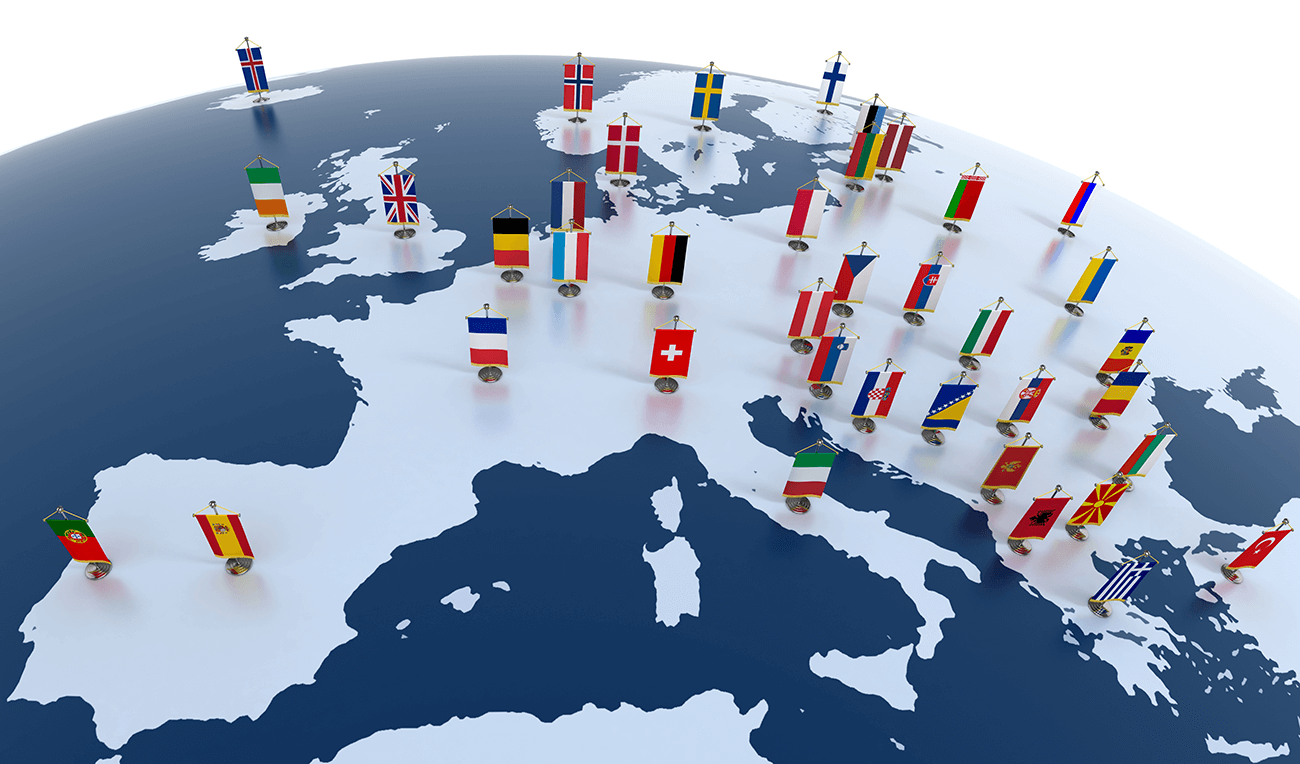
1.4. Business Models and their Influence
The business models and intentions behind the use of 3D printing technology are equally diverse. As examples:
- Manufacturing specialized in prototypes: The focus here is on producing parts that are almost indistinguishable from the later mass-produced components. This requires a wide range of technologies and often individual processing methods, which increases costs.
- Providers specialized in series or small series: Here, the focus is on efficiency and high utilization of the equipment, generally leading to lower costs but with less flexibility compared to providers specializing in prototypes.
In every case, it is the specific application that determines which model and technology are most economical.
2. Process-Specific Reasons Using the Example of Multi Jet Fusion
3D printing, far from a uniform technology, shows a multifaceted array of processes – each with its individual advantages and challenges. Understanding these differences often requires in-depth expert knowledge and can be challenging for customers due to the technical complexity. This can be exemplified using the Multi Jet Fusion (MJF) process, where 3Faktur is one of the first users in Europe to take a leading role and accordingly possesses profound expertise.
There are numerous ways to optimize costs in the 3D printing process, some of which can come at the expense of quality, while others directly benefit the customer.
Example of quality-oriented manufacturing:
- The production environment is specifically optimized for the MJF process, with constant environmental conditions such as temperature, humidity, and minimal vibrations, coupled with highly specialized equipment in top technical condition.
- Consistent, repeatable processing is ensured by defining and consistently applying an optimal parameter set for each component.
- Packing densities are operated in the optimal range and powder quality is rigorously checked.
- Each production step and the finished components are subject to strict quality controls; the processes are standardized, documented, and strictly monitored.
Example of cost-optimized manufacturing:
- Here, the production environment is mainly focused on cost optimization, with environmental conditions often being less controlled.
- The parameter set is trimmed for cost efficiency, sometimes at the expense of consistency.
- High packing densities are used, which often leads to increased powder degradation, reduced mechanical load capacity, greater dimensional deviations, and poorer surface qualities.
- Processes and quality controls can be sporadic and are often optimized for economic rather than quality-oriented criteria.
In cost-optimized manufacturing, significant cost advantages are possible, but this comes at the expense of the quality level – such as in dimensional deviations, surface homogeneity, mechanical load capacity, and repeatability. In contrast, quality-oriented manufacturing achieves significantly better results in these areas, albeit at corresponding costs.
In the following sections, we will explain in detail the influence of these factors and how they manifest in the practice of 3D printing.
2.1 Work Preparation and Orientation
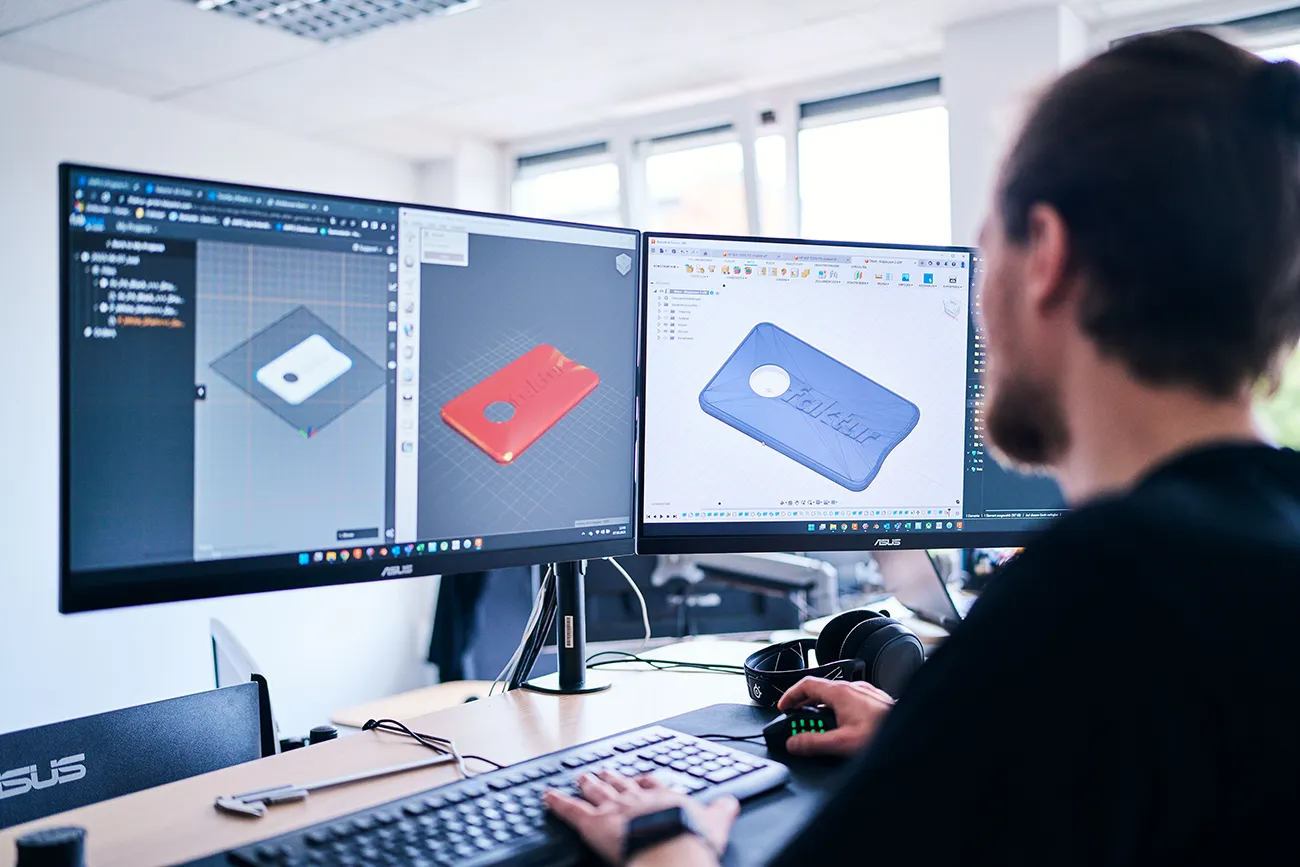
Preparing each component in the 3D printing process is an art in itself, starting with the determination of the optimal parameter set. A crucial aspect here is the orientation of the component during printing. This step is treated with the utmost care at 3Faktur to ensure that the orientation remains constant for repeat orders, significantly affecting the consistency and quality of the end products. This is also applied to other important parameters in the printing process.
Influence on quality:
The orientation of the component in the print chamber has a significant impact on surface quality and homogeneity. Since each side of a 3D printed object can have slightly varied surface characteristics, consistent and optimized orientation is of great importance.
Orientation also significantly influences dimensional accuracy, particularly in the Z-direction, where deviations can be much more significant than in the X/Y plane. With changing orientation, different sides of the component protrude in the Z-direction, leading to greater deviations in dimensional accuracy.
Potential for cost reduction:
Applying cost-optimized orientations makes it possible to achieve higher packing densities, offering the potential for significant cost savings, but is very concerning from a quality perspective (see below).
Furthermore, the process of work preparation, otherwise a cost-intensive phase, is significantly simplified. This allows for cost savings by reducing staff and relying on less qualified personnel.
Indicators of quality defects:
Differences in surface texture and dimensional accuracy are often visible to the naked eye when comparing two components.
These phenomena are particularly noticeable when batches with different orientations are compared. In a production strongly focused on cost efficiency, varying orientations can even be found within a single batch – a practice geared purely towards cost optimization.
The approach of 3Faktur:
At 3Faktur, no compromise is made when it comes to work preparation. Each component is carefully checked, and the most optimal orientation and production parameters are chosen.
Moreover, it is verified whether a component has been produced in the past, ensuring that parameters from previous batches are adopted for consistent consistency.
2.2 Packing Density: A Key Element in Powder Printing
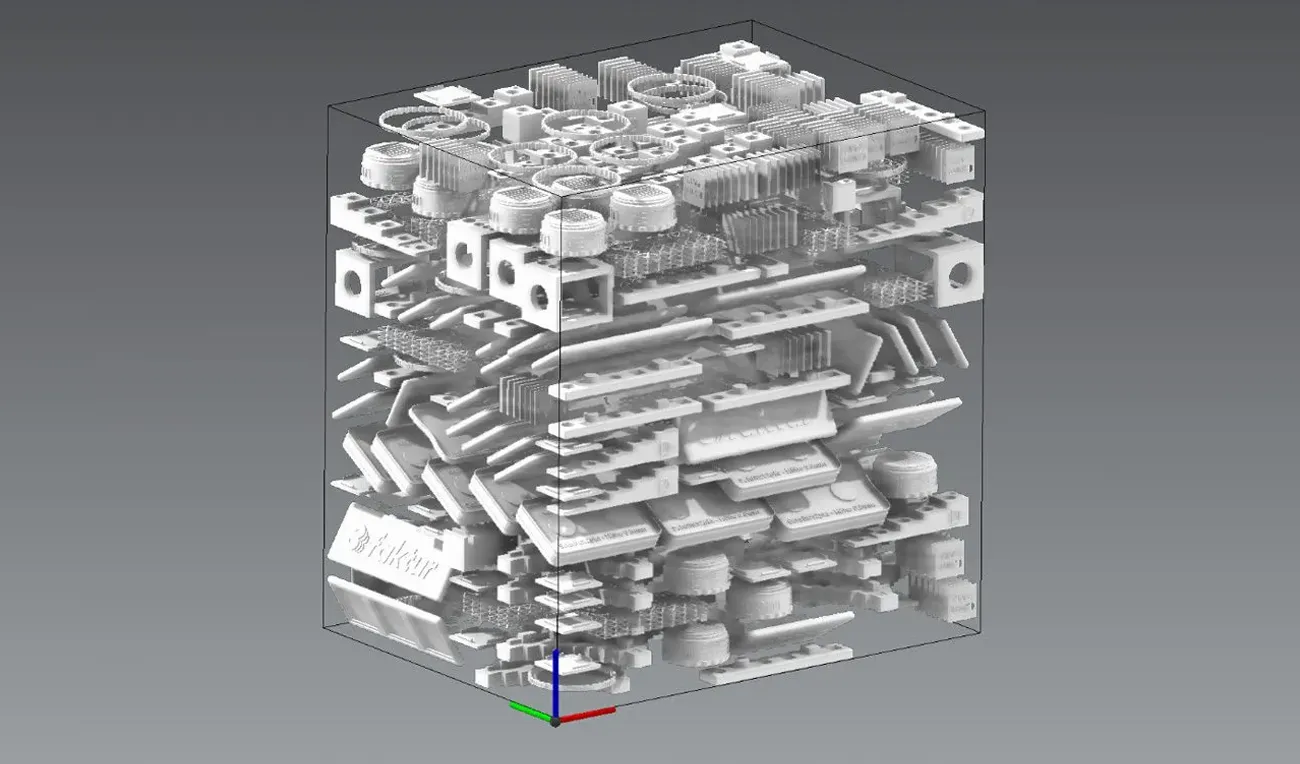
In powder printing, both in Multi Jet Fusion and in laser sintering, the entire build volume is filled 100% with powder during printing. However, not all the powder is fused into components; a certain percentage remains as loose residual powder. Packing density is the measure of how much of the powder is actually converted into components.
Example of Packing Density:
Consider a hypothetical build volume of 10 x 10 x 10 cm, equating to a volume of 1,000 cm³. With a packing density of 10%, 100 cm³ of this volume would be converted into components, while 900 cm³ would remain as residual powder.
Influence on Quality:
As packing density increases, the thermal load on the non-component residual powder significantly increases. During the build process, which occurs at high temperatures, this increased load can lead to powder degradation.
This continues during the cooling process, which can typically last between 36 and 48 hours in the Multi Jet Fusion process. If more components are present in the build volume, which are warmer than the residual powder, they act as radiators, maintaining the temperature of the powder high. This increases the thermal load on the powder (higher temperature over a longer period).
As a result of prolonged heat exposure, the powder can undergo severe degradation, significantly impairing the mechanical properties of the components made from it. The mechanical load capacity of the components can be reduced by up to 50 %.
Besides reduced load capacity, visible surface damages such as orange peel or elephant skin, as well as increasing warping of the components, can occur. These effects are not only cosmetic in nature but can also affect the functionality and fit of the components.
Scientific literature, such as the study by Wegner et al. (2014), provides a deeper examination of these phenomena and underscores the necessity of carefully controlling packing density to maintain material integrity and ensure the longevity of the components.
Excessive material degradation can increase the risk of component failure under normal operating conditions, which is particularly problematic in safety-critical applications. Overall, the consideration of packing density highlights the complex balance between cost efficiency and quality assurance in 3D printing and underscores the need to understand and appropriately manage every aspect of the printing process.
Potential for Cost Reduction:
The potential for cost reduction by increasing packing density is enormous, as it allows providers to increase the quantity of parts printable at the same time. This results in lower costs per unit volume of the finished material.
Let’s consider a hypothetical example: In a build volume of 1,000 cm³ with a packing density of 10 %, 100 cm³ of printed components are produced. With a refresh rate of 20 %, it is necessary to dispose of an additional 100 cm³ of powder, as one-fifth of the powder in the printing process must be replaced with fresh material. This means that a total of 200 cm³ of powder is used for printing, leading to costs of 20 EUR at a (fictitious) powder price of 100 EUR per 1,000 cm³. The price per unit volume for the produced components is then 0.20 EUR per cm³ (20 EUR divided by 100 cm³).
If the packing density is increased to 20 %, the volume of produced components doubles to 200 cm³, without the need to dispose of additional powder, as the 20% refresh rate is maintained. In this case, the total cost for the powder remains unchanged at 20 EUR, reducing the cost per unit volume to 0.10 EUR per cm³ (20 EUR divided by 200 cm³ of produced components), which means a halving of the costs per unit volume.
Such adjustments of packing density are a common strategy of low-cost providers, with the aforementioned consequences for the achieved quality.
Indicators of Quality Defects:
- Surface Damage: Even under optimal process conditions, surface damage can occur, often more frequently with thicker wall strengths. If such damages also occur with thin wall strengths and regularly, this could indicate excessively high packing densities.
- Mechanical Load Capacity: If there is suspicion that the provider sets the packing density too high, a test in the form of tensile test bars, printed in a defined orientation (in case of doubt, orient in the Z-direction) and then measured, can provide clarity. Significant deviations, e.g., in tensile strength, from the material manufacturer’s specifications or strong fluctuations between batches can indicate poor powder quality.
- Color Changes: A clear indicator of excessively high packing densities is discoloration of the components. Especially with white components, a yellowing can occur, which becomes apparent at high packing densities. If a component turns out noticeably yellower than expected, this is a clear sign of excessive powder degradation.
It is also worth mentioning the relationship between packing density and refresh rate: Packing density is closely linked to the refresh rate. In the Multi Jet Fusion process, a standard refresh rate of 20% new powder is used. Theoretically, higher packing densities could be achieved at the same quality level by increasing the refresh rate, but this would negate the cost savings. In laser sintering, it is not uncommon for providers to reduce the recommended refresh rate of 50% to lower values, e.g., 30%, which leads to the same problems of powder degradation and can produce yellow components (although it saves enormous costs). In Multi Jet Fusion, this is hardly possible, as the refresh rate of 20% is already very low, and lower refresh rates are technically not feasible.
The Approach of 3Faktur:
At 3Faktur, packing density is treated as a crucial quality factor with utmost care. The company’s approach regarding packing density follows clear principles to ensure the highest quality:
- 3Faktur has opted for a medium packing density of about 9.5%, which is at the lower end of HP’s recommended optimal range. This decision allows for a balanced mix of efficient resource use and a high level of quality, manifested in stable mechanical load capacity of the components and consistent dimensional accuracy over many production cycles.
- Furthermore, after each printing process, the residual powder is tested with standardized measurement methods (e.g., for color changes) to ensure that only powder of sufficient quality is used for further printing processes. This approach compensates for potential negative effects of deviations in the powder through adjusted refresh rates and secures the consistency of the final product.
The consistent implementation of these practices shows that 3Faktur recognizes the cost-saving potential through adjustments of packing density but will not exploit it at the expense of product quality. This commitment to quality ensures that the end products are not only economical but also of high quality, maximizing the value for the customer.
2.3 Cooling Time
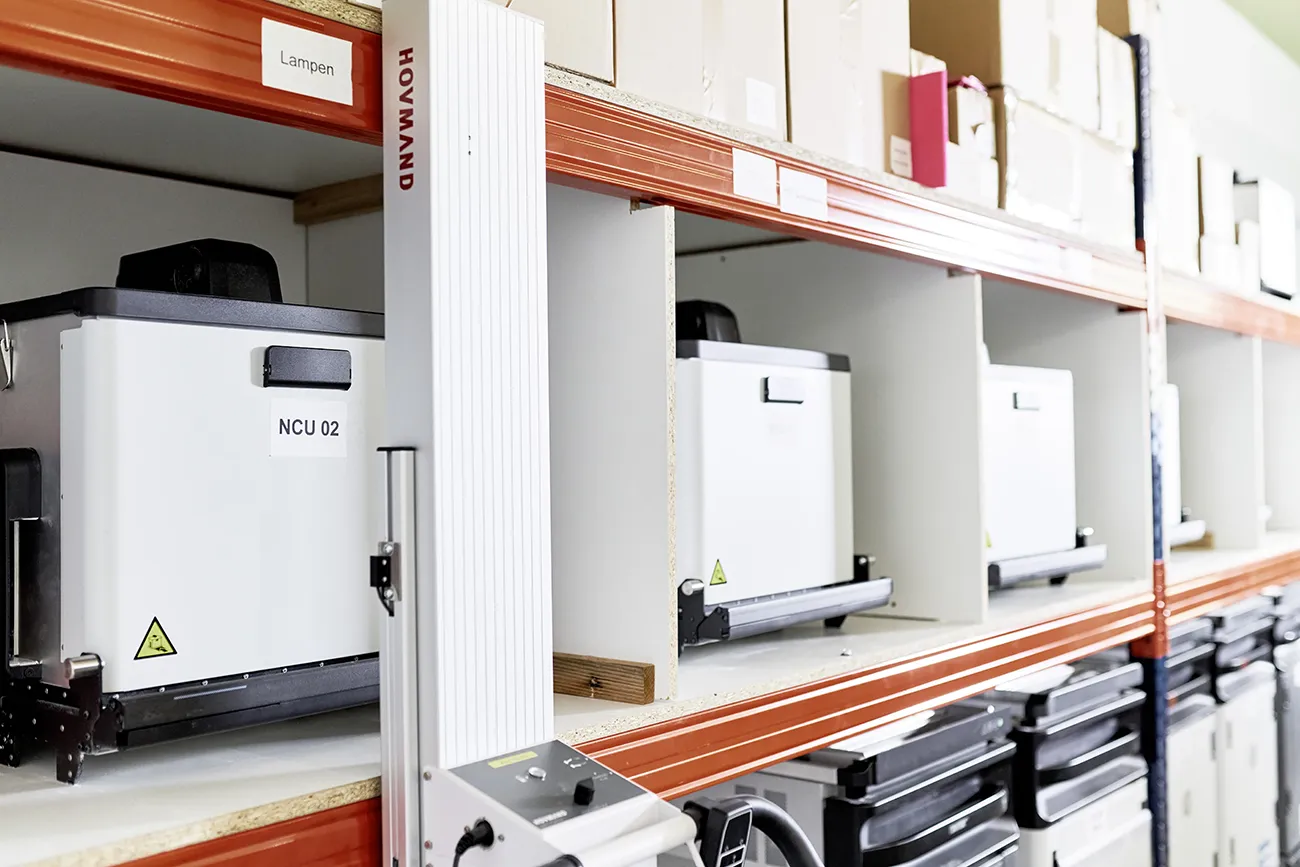
The cooling process after 3D printing is a critical step crucial for the final quality of the produced components.
Influence on Quality:
The build chamber requires a cooling time of typically 36 to 48 hours. This period is necessary to ensure even and warp-free cooling of the components. The cooling time has a geometry-dependent impact on the quality of the components. While some materials, such as TPU, can be more flexible in response to cooling conditions, with others, particularly Polyamide 12, slow and controlled cooling is essential to minimize dimensional inaccuracies and warping.
Too rapid cooling times can lead to inaccuracies and quality defects, especially in warp-prone components.
Cost Reduction Potential:
The cost savings from shortened cooling times are rather small in the overall context of production. However, an increased throughput is achieved and shortens lead times accordingly.
Indicators of Quality Defects:
Inaccuracies, surface damage, and strong warping, especially in larger and more extensive components, are typical signs of insufficient cooling time.
Providers who offer unusually short production times might possibly achieve this by reducing the cooling time. Normally, a cycle lasts about four days – printing on the first day, cooling on the second and third days, and post-processing on the fourth day. Three days are possible if printing starts early in the day. Shorter lead times can only be realized if full build chambers are not produced, which is very expensive, or indeed the cooling time is reduced.
The Approach of 3Faktur:
3Faktur maintains a slow and even cooling time of at least 36 hours, averaging over 45 hours for all batches. This method ensures that each component receives the necessary time to stabilize from heat-induced issues.
2.4 Quality Controls
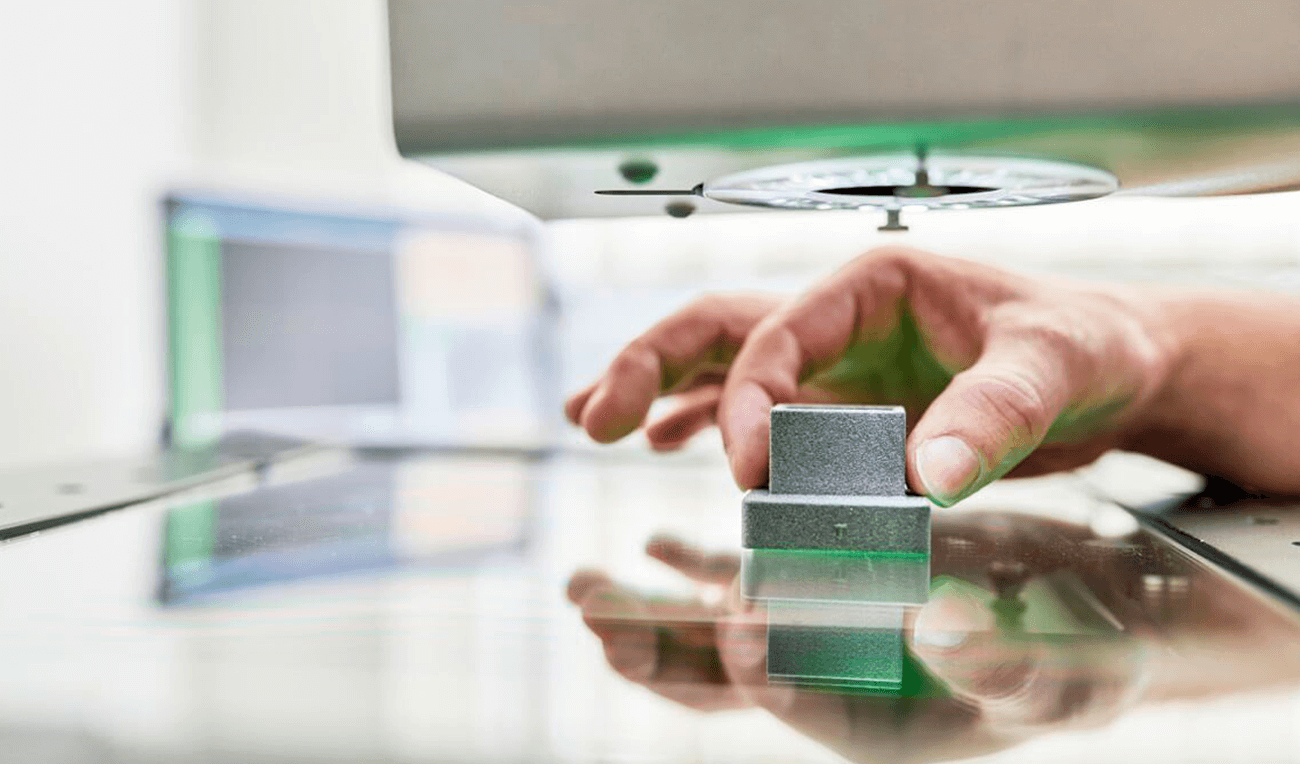
In 3D printing, quality control is a crucial element that ensures the integrity and reliability of the final products. At 3Faktur, a comprehensive quality management system is implemented, which is (simplified) divided into two main areas: process controls during manufacturing and final inspection of the finished components.
Influence on Quality:
Inadequate quality controls in any of these steps can lead to non-reproducible and widely varying results. Such variabilities in production are not only costly for the provider in terms of material and time expenditure, but also for the customer, who may face increased scrap.
Cost Reduction Potential:
Optimizing quality controls has great potential for cost reduction, as intensive manual inspections are personnel and time-intensive.
Indicators of Quality Defects:
A high rate of scrap and significant fluctuations in the quality of produced components can indicate inadequate quality controls or quality management. These problems often reveal themselves through inconsistent dimensions, functional deficits, or visible defects on the components.
The Approach of 3Faktur:
3Faktur commits to comprehensive documentation and control of every step in the manufacturing process. Final inspection of the components is carried out using automated systems that can capture a large number of measurement points and component properties, far beyond what would be possible manually. These automated measurements are supplemented by visual inspections and selective manual checks, particularly where automated methods might reach their limits.
2.5 Post-Processing & Equipment of the Process Chain
For efficient, high-quality, and consistent processing of components after 3D printing, the use of highly specialized equipment and processes suitable for the Multi Jet Fusion (MJF) process is necessary.
Influence on Quality:
The use of specialized equipment, e.g., for cleaning or surface treatment of the components, contributes significantly to achieving high-quality and consistent results.
Cost Reduction Potential:
Although the acquisition costs for specialized equipment can be high, the cost reduction potential is moderate, as these systems often come with a high degree of automation. The reduced manual effort and increased efficiency can partly or even completely offset the higher initial costs.
However, this generally only applies with high utilization of the equipment. Smaller service providers or manufacturers with a limited number of machines often cannot fully amortize the costs for such specialized devices and therefore may resort to less professional solutions.
Indicators of Quality Defects:
Characteristics include unclean components with residual powder, inhomogeneous surface texture, and uneven color distributions on the components.
The Approach of 3Faktur:
3Faktur provides one of the most modern and comprehensive process chains for the MJF process. This includes a well-considered selection of devices and processes designed for maximum quality and efficiency, to meet the requirements of the MJF process and deliver the best possible end products.
2.6 Utilization
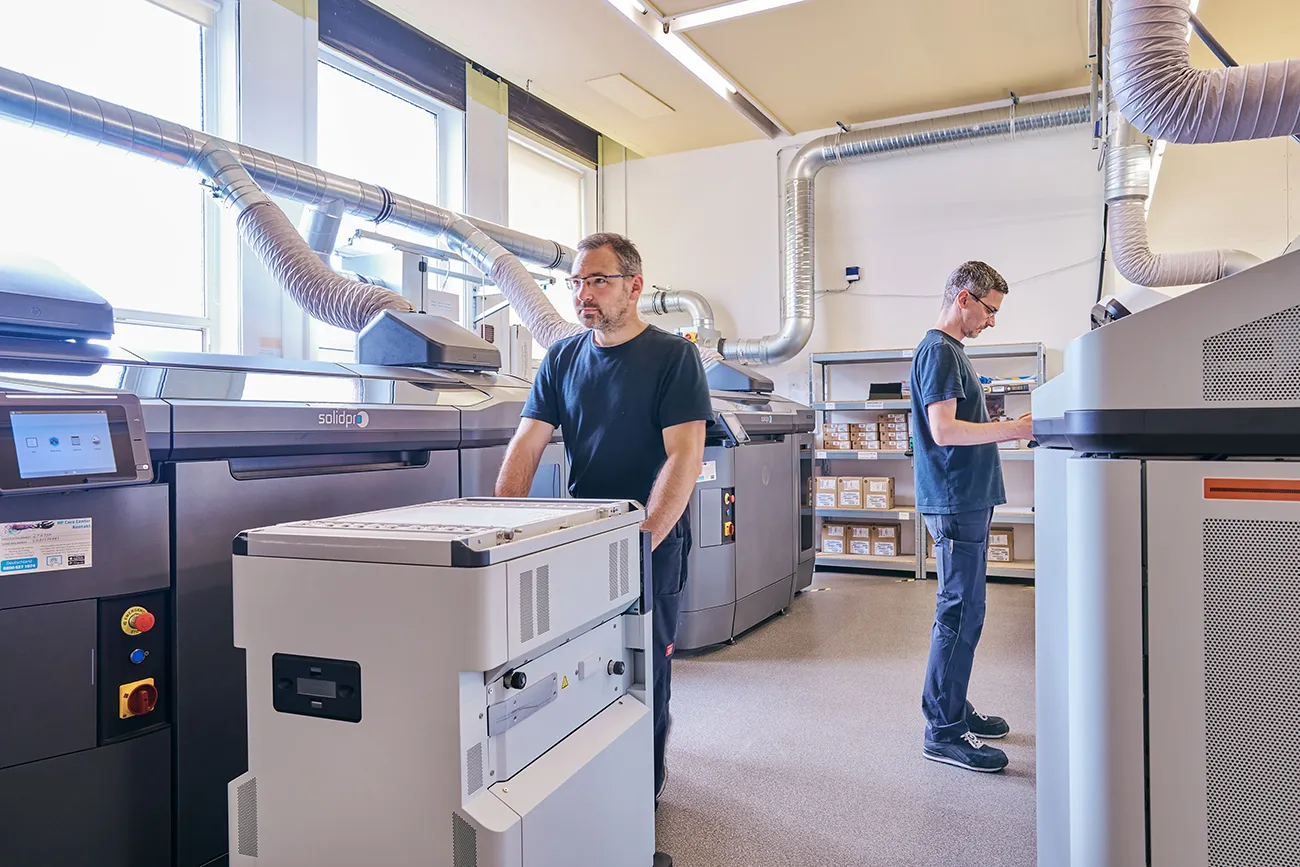
Industrial 3D printers represent a considerable investment, and high utilization is necessary to reduce the cost per component.
Influence on Quality:
Fundamentally none, as high quality can be ensured even at high utilization rates with optimal processes and the use of suitable equipment and peripherals. If these are not in place, it can lead to disorder and a loss of quality (colloquially: “chaos”).
Cost Reduction Potential:
Maximizing utilization is an effective and proven method to reduce costs without compromising on quality.
Indicators of Quality Defects:
Negative signs of insufficient process chain at high utilization rates can include frequent delivery delays, fluctuating quality, and the delivery of incorrect or defective components.
In a positive scenario, high utilization with optimized processes allows for a low price level while maintaining consistently high quality of the components.
The Approach of 3Faktur:
3Faktur utilizes a highly specialized process chain designed for high volumes and features one of the highest degrees of automation in additive plastic manufacturing.
Advanced technologies such as AI-based sorting systems, automated packaging and measuring systems, as well as robot-controlled post-processing processes and unpacking systems are used. This highly automated and efficient production method enables 3Faktur to achieve very high utilization, thus offering the best quality at fair prices.
Combining advanced technology and streamlined processes, 3Faktur ensures that the high investments in production equipment pay off not only through lower unit costs but also through high product quality. This model serves as the basis for a sustainable business that meets customers’ needs for cost-efficient, high-quality 3D-printed components.
2.7 Tips for Users of 3D Printing Platforms
When choosing a 3D printing service through platforms, caution is advised: Some platforms do not transparently communicate which provider performs the printing. Different providers can lead to fluctuations in quality, as each batch may be produced by a different provider. This can be problematic for serial components where consistency is crucial.
3. Conclusion
In conclusion, the well-known advice applies: Decisions should not be made solely based on price. A comprehensive consideration of all relevant factors such as quality assurance measures, packing densities, and the consistency of manufacturing processes is crucial.
It is important to ask critical questions when selecting a provider and to learn how they handle quality controls, process replicability, and other key factors. Certifications, especially ISO/ASTM 52920, which sets specific quality standards for additive manufacturing processes, can serve as indicators of a company’s commitment to quality and reliability. This standard provides insight into a company’s procedures and quality philosophy. 3Faktur is certified according to this standard, which underscores our commitment to quality and continuous improvement. For an overview of certified companies in the field of additive manufacturing, you can visit the TÜV SÜD website.