Chemical smoothing, also known as vapor smoothing, is a physico-chemical process that can compress and smooth thermoplastic polymers. We use this technology to smooth the surface of additively manufactured polyamide components. The technology is highly controllable and enables reproducible results without compromising the mechanical properties of a product.
Vapor Smoothing at 3Faktur
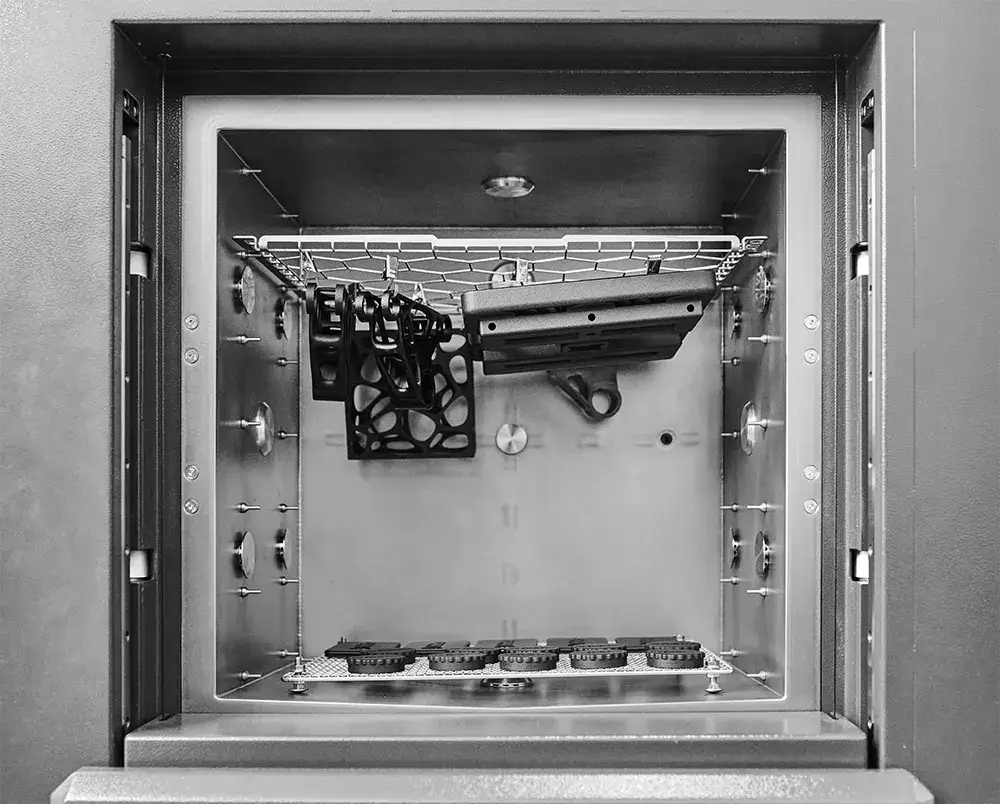
3Faktur works with the Vapor Fusion system PostPro SF 50 from the British manufacturer AMT. You can book this service with 3Faktur for all ordered components made of Polyamide 12, Polyamide 12 W (white), TPU and Polyamide 11.
Operation of Chemical Smoothing
In chemical smoothing, the parts to be processed are exposed to vaporized solvent in a closed chamber. The solvent leads to partial dissolution (“melting”) of the often rough surface of 3D-printed parts. By liquefying the surface, unevenness is leveled out, and pores are closed. The result is a very smooth, practically pore-free surface.
Applications
We currently offer vapor smoothing only for the material polyamide 12 (PA 12). There are three essential application areas for this post-processing process: visual parts, components for gas or liquid transport, and simplified cleaning.
Components for Gas or Liquid Transport
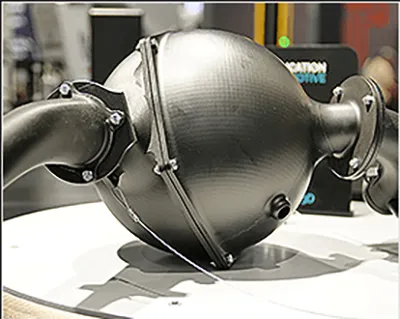
With the Multi Jet Fusion process, parts with high density can be produced, which are often “tight” when the wall thickness is sufficient. However, the relatively high porosity of the surface can be problematic.
Chemical smoothing completely seals the surfaces. The processed parts are particularly suitable for applications where tightness is functionally necessary.
Simplified Cleaning
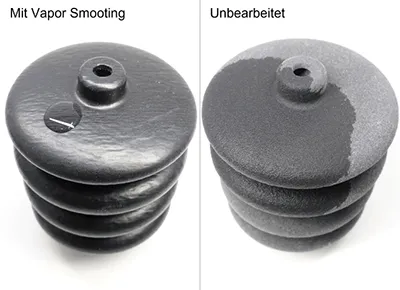
The typical rough surfaces that occur in powder-based 3D printing are difficult to clean. However, in cleanroom environments or in medical and laboratory diagnostics, cleaning is essential.
Chemical smoothing significantly reduces surface roughness (down to Ra 1 – 3 µm). At the same time, all pores are closed, allowing the parts to be easily cleaned and used in sensitive areas.
Visual Parts
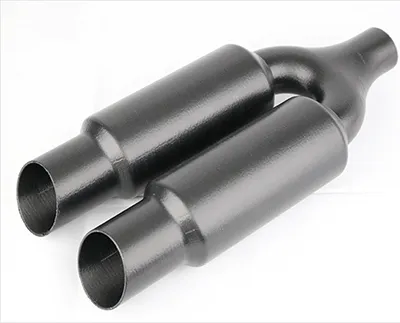
Chemical smoothing significantly improves the surface quality of 3D-printed parts, resulting in a visually appealing appearance. It removes layer lines and roughness, giving the parts a smooth and polished finish. This makes it suitable for applications where aesthetics are important, such as consumer products, architectural models, or visual prototypes.
Special Features of Chemical Smoothing
The components are suspended from a fixture and pushed into the processing chamber. There they are exposed to the vaporized solvent for only a few seconds, which condenses on the component surface and acts there for a few minutes. This is followed by a drying process of approx. 30 – 45 minutes, during which the solvent evaporates completely from the surface. The chamber is completely hermetically sealed during processing and drying. Following drying, the fixture is removed from the chamber and the machined components are removed from the fixture.
Most components can be easily hung from existing structures. However, some geometries require an additional structure to allow or facilitate hanging.
FAQ Chemical Smoothing
What are the processing costs per part?
The costs per part are primarily determined by the size and surface area of the component. In general, the costs range from low to mid-single-digit EUR per part, with a minimum order value of EUR 25,- plus VAT for a component geometry. You can calculate the costs based on your CAD data using our online calculator.
Do I need to add structures to the component for it to be suspended in the processing chamber?
If the geometry of your component is not suitable for optimal suspension in the chamber, we will contact you. If attaching a structure is necessary, you can do it yourself or we can handle it. In the latter case, of course, in consultation with you.
Do the dimensions or accuracy of the component change?
The changes are minimal and typically below 0.4%. For large, flat objects that are already prone to warping during printing, warping effects may be enhanced or reduced.
Does edge rounding occur?
Yes, but only minimally. Problems associated with edge rounding are extremely rare in practice.
Do the mechanical properties of the material change?
In the Multi Jet Fusion process, the 3D-printed material is dense internally (approx. 98-100% density), but the surface is porous. The surface properties have a greater influence on the overall behavior and reduce the mechanical strength, especially for thin wall thicknesses.
Chemical smoothing reduces the porosity of thin wall thicknesses, thereby increasing their mechanical strength. Therefore, the process has a positive effect on the load-bearing capacity.
However, this effect is less pronounced for thicker wall thicknesses.
Does the material retain any solvents?
The manufacturer of the process guarantees that no significant amounts of solvents remain on the material. Our own analyses so far have confirmed this statement.
Does the production time of the ordered components increase due to chemical smoothing?
When combined with black dyeing, the production time can be extended by approximately 1 working day. This is due to the required drying phases for both processes, which usually cannot be performed on the same day.