Im vorangegangenen Kapitel 4 haben wir uns auf die Konstruktionsleitlinien zur Optimierung von Funktionen konzentriert. Im nun folgenden Kapitel 5 liegt der Schwerpunkt auf Strategien zur Verbesserung der Oberflächenqualität von Multi Jet Fusion-Komponenten. Zudem werden wir Konstruktionshinweise für typische Nachbearbeitungsverfahren bereitstellen.
Kapitel 5: Optimierung der Oberfläche
5.1 Oberseite/Unterseite von Flächen
Eine besondere Eigenschaft des Multi Jet Fusion-Verfahrens besteht darin, dass eine wärmeleitende Flüssigkeit auf das Materialpulver aufgesprüht wird. Dies führt zu einer leichten Absenkung des Pulvers.
Die Hitzequelle agiert von oben auf den Bauraum, wodurch die nach oben gerichteten Flächen stärker erhitzt und folglich etwas rauer werden. Auf diesen Flächen führt das zu einem leichten Absinken des Pulvers („Einsacken“).
An den Rändern jedoch geschieht durch Kapillareffekte das Gegenteil: Das Gemisch aus Flüssigkeit und Pulver wird leicht nach oben gezogen. Dies resultiert in leicht konkaven Flächen, das heißt, die Ränder stehen bis zu etwa 0,1 mm nach oben. Im Gegensatz dazu sind die Flächen auf der „Unterseite“ ansprechend glatt, allerdings mit leicht abgerundeten Kanten zum Objekt hin. Folglich sollten Sichtseiten möglichst nach unten bzw. schräg orientiert sein. Sie können in Ihrer technischen Zeichnung die Sichtseite markieren oder die Druckorientierung definieren.
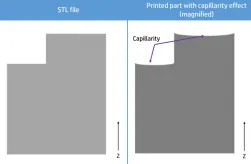
Quelle: HP
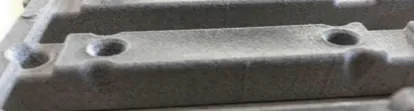
Quelle: HP
5.2 Treppenstufeneffekt
Die sogenannten Treppenstufen beziehen sich auf die sichtbaren Schichten des 3D-Druckprozesses(für MJF 80 µm bzw. 110 µm im „Economy“ Modus (nur PA12)), die in der Z-Dimension auftreten. Auf geraden Flächen sind sie in der Regel kaum oder nicht erkennbar. Jedoch können sie insbesondere bei Rundungen und flachen Winkeln sichtbar werden. Um den Treppenstufeneffekt zu minimieren, sollten Objekte, die aus einer großen flachen Oberfläche herausragen, dies mit einem Winkel von mindestens 20° tun. Auf der Unterseite ist dieser Effekt weniger ausgeprägt, hier ist ein Winkel von mindestens 10° ausreichend.
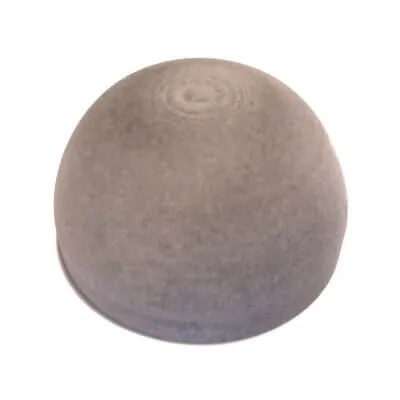
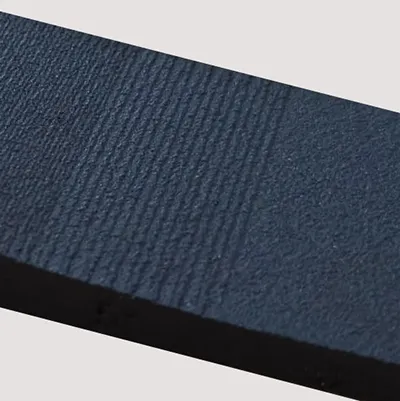
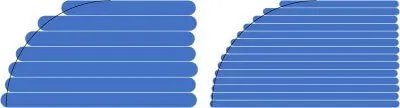
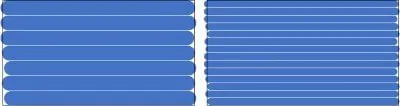
5.3 Einsacken/Verzug
Große / massive Körper neigen dazu, im Zentrum einzusacken. Bei dünnen geraden, relativ großen Flächen, kann es hingegen zum Verzug des Werkstückes kommen.
- Einsacken: Bei der Multi Jet Fusion-Technologie können massive Strukturen Probleme wie Einsackungen oder die Bildung einer „Elefantenhaut“ (Orangenhaut) aufweisen. Dies resultiert aus übermäßiger Wärmeaufnahme und ungleichmäßiger Abkühlung. Eine Lösungsstrategie besteht darin, massive Körper auszuhöhlen, insbesondere bei Strukturen mit einer Stärke von 10 mm oder mehr. Um die Stabilität zu erhöhen, können in diese Hohlräume Stützstrukturen wie Gitternetze (Waben oder Knochenstrukturen) integriert werden. Die Auswahl der Struktur hängt von der Geometrie und der Belastungsrichtung ab. Escape Holes können eingefügt werden, um überschüssiges Pulver zu entfernen. Bei verschlossenen Hohlräumen bleibt das Pulver innen. In unserem Online-Tool steht die Option zur Auswahl. Standardmäßig werden wir bei dieser Auswahl eine Gitternetzstruktur einbringen.
- Verzug: Großflächige, dünne Konstruktionen können beim Multi Jet Fusion-Verfahren zum Verzug neigen. Das liegt an der Temperaturdifferenz, die entsteht, wenn die äußeren Bereiche im Bauraum schneller abkühlen als die inneren. Dies kann zu Materialspannungen führen, die ein Verziehen oder „Warping“ des Objekts zur Folge haben. Daher ist es ratsam, solche Flächen zu vermeiden – sofern dies funktional möglich ist. Eine Möglichkeit, den Verzug zu minimieren, ist die Erhöhung der Wandstärke. Zusätzliche „Rippen“ auf der Fläche sollten jedoch vermieden werden, da sie Wärme speichern und damit eine ungleichmäßige Abkühlung fördern, was den Verzug begünstigen kann.
5.4 Konstruktionshinweise für Nachbearbeitungsverfahren im 3D-Druck
Nachbearbeitung spielt eine Schlüsselrolle, um das optimale Endergebnis in der additiven Fertigung zu erzielen. Abhängig vom 3D-Druckverfahren können verschiedene Verfahren angewendet werden. Es ist wichtig zu beachten, dass Nachbearbeitungen zusätzliche Designanforderungen stellen können. Unsere Experten beraten Sie gerne zu den passenden Verfahren für Ihr Projekt.
5.4.1 Färbung
Beim Färben werden Bauteile Temperaturen um 95°C (Standard-Schwarzfärbung) oder über 100°C (Deep Dye Coloring) ausgesetzt und in eine Färbelösung getaucht. Durch diese kontrollierte Reaktion nehmen die Bauteile Pigmente auf, wodurch sie gefärbt werden.
Konstruktionshinweise
- Verzug: Bauteile mit einem Längen-Höhen-Verhältnis von 10:1 oder mehr sind für das Färbeverfahren ungeeignet, da hohe Temperaturen und Lösemittel den Verzug verstärken können.
- Wandstärken: Die Wandstärke kann bei der Färbung von weißen Bauteilen das Endergebnis beeinflussen. Dünne Wände (< 1 mm) können etwas transluzent sein, wodurch Farben heller erscheinen. Für eine gleichmäßige Färbung sollten alle Wandstärken gleich sein, sonst sollte auf der Sichtseite eine Mindestwandstärke von 1 mm eingehalten werden.
Mehr Informationen:
5.4.2 Lackierung
Die Lackierung umfasst das Auftragen einer oder mehrerer Schichten, gewöhnlich Acryl-basierte Kunststoffe, die Pigmente und eventuell weitere Substanzen enthalten. Diese Zusätze können die Struktur beeinflussen und spezielle Effekte, wie etwa Metallic-Lackierungen, erzeugen.
Hinweise zur Konstruktion für die Lackierung:
- Details: Vermeiden Sie feine Details, da diese während des Lackierens verstopfen können und anschließend nicht mehr sichtbar sind.
- Zugänglichkeit: Schwierig zu erreichende Bereiche können ungleichmäßig lackiert werden, was zu inhomogenen Oberflächen und variierenden Schichtdicken führt.
- Formgebung: Verwenden Sie Rundungen statt scharfer Kanten, da Lack an Kanten ablaufen und dünnere Schichten erzeugen kann. Dies kann die Homogenität und Stabilität der Lackierung beeinträchtigen.
- Flächenbeschaffenheit: Eine gleichmäßige, weitläufige Fläche führt zu einem besseren Lackierungsergebnis. Je mehr Elemente, Erhebungen oder Absenkungen vorhanden sind, desto ungleichmäßiger kann das Ergebnis sein.
- Oberflächenqualität: Da die Lackschicht meist zu dünn ist, um unebene Oberflächen zu kaschieren, sollten Sie eine optimale Oberflächenqualität anstreben. Eine chemische Glättung als Vorbehandlung kann empfehlenswert sein.
- Verzug: Bei Bauteilen, die eine hohe Verzugsgefahr aufweisen, kann die Lackierung problematisch sein. Dies ist unter anderem auf die Polymerisation der Lackschichten zurückzuführen, die selbst Schrumpfungen aufweisen können und somit dünne Wandstärken verformen können.
Mehr Informationen:
Shot Peening
Shot Peening ist ein Prozess zur Oberflächenveredelung, bei dem kleine Partikel oder „Shots“ mit hoher Geschwindigkeit auf die Oberfläche des Bauteils abgefeuert werden. Dieses Verfahren dient zur Verfestigung der anfänglich porösen Oberfläche, um homogenere und widerstandsfähigere Oberflächen zu erzielen. Sofern keine chemische Glättung angefordert wird, bearbeiten wir alle gefärbten Bauteile bei 3Faktur mit dieser Technologie – eine separate Bestellung ist nicht erforderlich.
Konstruktionshinweise:
- Wandstärken: Eine Mindestwandstärke von 1,0 mm wird empfohlen, da der Prozess eine hohe mechanische Belastung für die Bauteile darstellt. Zu dünne Wandstärken können durch die Bearbeitung beschädigt („durchschossen“) werden und spitz zulaufende Kanten können ausbrechen.
- Zugänglichkeit: Je zugänglicher die Elemente sind, desto gleichmäßiger und effektiver ist die Bearbeitung, was zu einem besseren Endergebnis in Form einer homogenen Oberfläche führt.
- Schmale Öffnungen: In engen Schlitzen kann das Bearbeitungsmedium stecken bleiben und kann nicht mehr entfernt werden. Wir empfehlen daher, Öffnungen mit einer Mindestbreite von 1 mm zu konstruieren.
Mehr Informationen
5.4.4 Vapor Smoothing (Chemische Glättung)
Im Prozess des chemischen Glättens werden die zu behandelnden Bauteile in einer abgeschlossenen Kammer mit verdampftem Lösungsmittel in Kontakt gebracht. Dieses kondensiert auf der Oberfläche und verflüssigt diese kurzzeitig, was einem „Schmelzen“ der häufig rauen Oberflächen bei 3D-gedruckten Bauteilen gleichkommt. Durch das Aufweichen der Oberfläche werden Poren versiegelt und kleine Unregelmäßigkeiten beseitigt. Das Endergebnis ist eine nahezu porenfreie, glatte Oberfläche.
Konstruktionshinweise für die chemische Glättung:
- Wandstärken:
- Dünne Wände: Bei Wänden mit weniger als 1 mm Stärke ist es schwierig, einen Temperaturgradienten zu erzeugen. Infolgedessen kondensiert kaum oder gar kein Lösungsmittel, was zu einem weniger ausgeprägten Effekt führt. Wir empfehlen daher eine Mindestwandstärke von 1 mm.
- Unterschiedliche Wandstärken: Bei Teilen mit erheblichen Unterschieden in der Wandstärke kann es zu inhomogenen Oberflächen kommen, da bei massiven Elementen mehr Lösungsmittel kondensiert als bei dünneren. Vermeiden Sie starke Schwankungen in der Wandstärke im Sichtbereich.
- Zugänglichkeit: Dieses Verfahren wirkt am besten auf leicht zugänglichen Bereichen. Lösungsmittel dringt schwer in Hinterschneidungen oder Kavitäten ein, was zu minimaler oder keiner Bearbeitung in diesen Bereichen führt.
- Kanten: Scharfe Innenkanten sollten vermieden werden, da sich hier das Lösungsmittel ansammeln und Oberflächenschäden ähnlich Schweißnähten verursachen kann.
- Positionierung im Bauraum: Es gibt zwei Optionen, die Bauteile im Bauraum zu platzieren.
- Auflegen: Die Teile werden auf einem Nagelbrett platziert. Diese Methode ist kostengünstiger, beeinträchtigt jedoch die Unterseite des Teils. Bei Bedarf können temporäre Auflageelemente hinzugefügt und nach der Bearbeitung entfernt werden. Sofern nicht anders gewählt, wird diese Positionierung von uns angewendet.
- Aufhängen: Das Teil wird im Bauraum aufgehängt. Dies führt zu einer gleichmäßigeren Behandlung, wobei an der Aufhängungsstelle eine Markierung sichtbar ist. Auch hier können Sie Strukturen vorsehen, an denen das Teil aufgehängt und nach der Bearbeitung entfernt wird.
Mehr Informationen
5.5 Allgemeine Hinweise
- Verwenden Sie sanfte Übergänge zwischen unterschiedlichen Querschnitten.
- Aushöhlen kann nur durch uns durchgeführt werden, es sei denn, der Hohlraum hat eine Öffnung.
- Vermeiden Sie Strukturen mit Seitenverhältnissen von über 10:1.
- Verzichten Sie auf die Verwendung von Erhöhungen und Rippen auf großen, flachen Flächen.
- Bringen Sie Details an der Unterseite von großen Flächen an.
- Beachten Sie die Nachbearbeitungsverfahren, die für Ihr Produkt notwendig sind. Diese können u.U. die Konstruktionsanforderungen verändern.