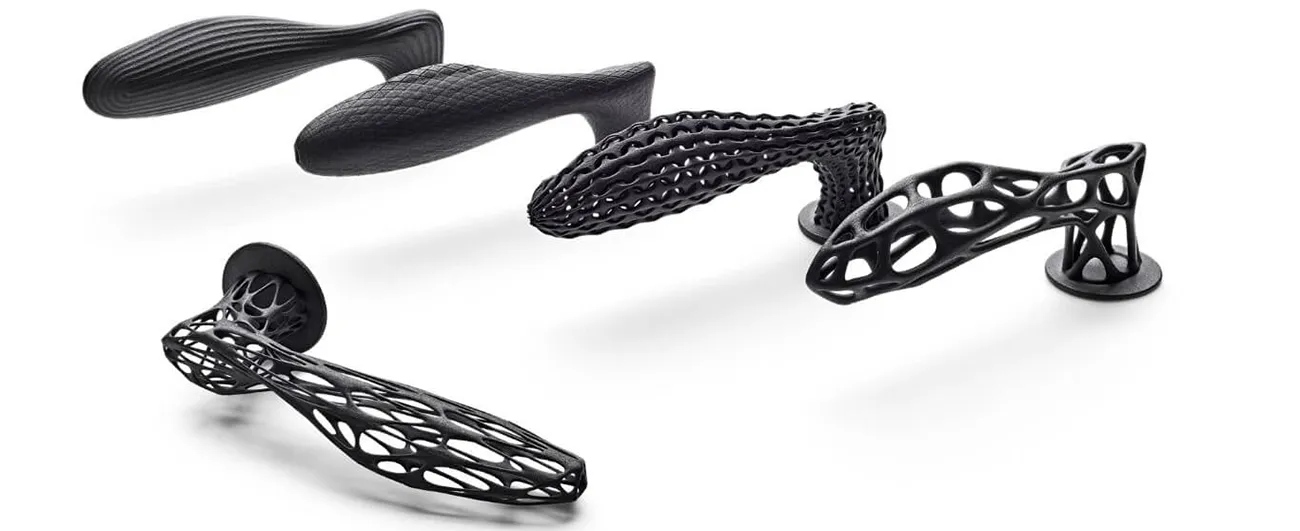
Jedes Produktionsverfahren stellt spezifische Anforderungen an das Produktdesign. Dies gilt auch für additive Fertigungsmethoden. Obwohl viele Richtlinien unter dem Begriff Design for Additive Manufacturing (DfAM) zusammengefasst werden können, bestehen wesentliche Unterschiede. Diese Übersicht konzentriert sich auf das Verfahren Multi Jet Fusion (Design for Multi Jet Fusion, DfMJF) und bietet Ihnen einen ersten Einblick. Für detaillierte Informationen zu spezifischen Aspekten des DfMJF besuchen Sie unsere weiterführenden Seiten.
1 Verfahren
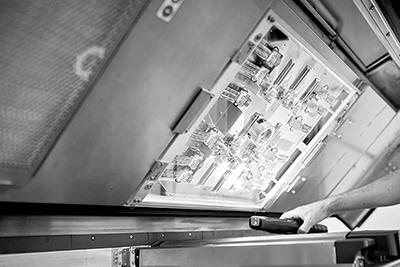
Um unsere Bauteilanforderungen und Konstruktion besser zu verstehen, ist technisches Grundwissen hilfreich. Erfahren Sie mehr über die Multi Jet Fusion-Technologie auf unserer entsprechenden Seite, inklusive:
- Unserer umfassenden und zertifizierten internen Prozesskette
- Materialauswahl spezifisch für Multi Jet Fusion
- Überblick über unsere Finishing-Prozesse
2 Anforderungen an den Datensatz
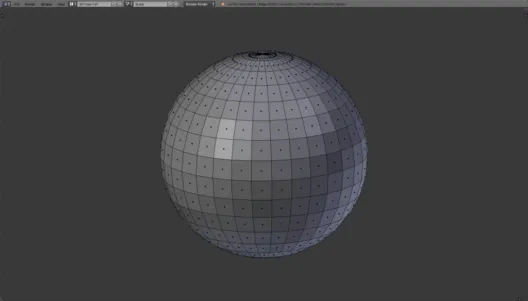
Ein 3D-Modell (CAD-Datei) ist für den 3D-Druck unerlässlich und bei Serienproduktionen ist zusätzlich eine detaillierte technische Zeichnung empfehlenswert. Im zweiten Kapitel finden Sie ausführlichere Informationen zu den spezifischen Anforderungen an die 3D-Datei (einschließlich Formate und Eigenschaften) sowie zu den erforderlichen Angaben für die technische Zeichnung.
3 Grundlegende Konstruktionsanforderungen
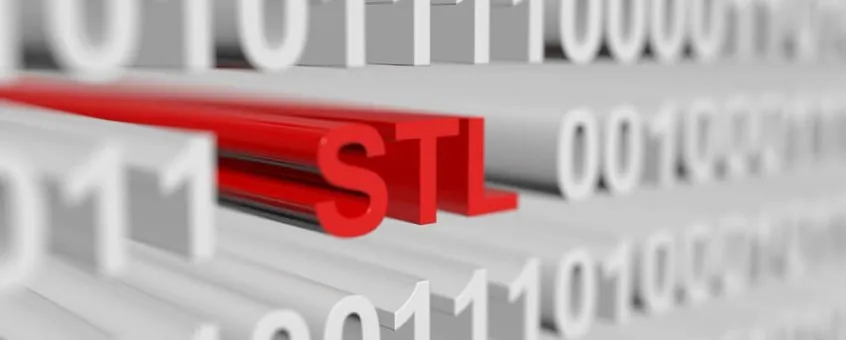
Um eine reibungslose Produktion zu gewährleisten, liefert Kapitel 3 wichtige Informationen zu Schlüsselelementen, wie Wandstärken, Schriftgrößen bzw. Detailauflösung, minimalen Abständen sowie minimalen Durchmessern für Öffnungen, Bohrungen und Kanäle.
4 Designoptimierung & Funktionale Elemente
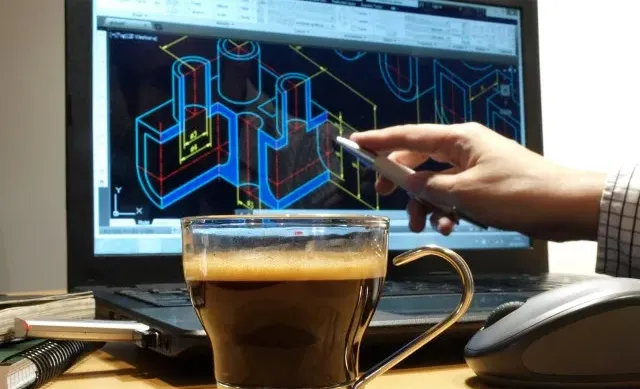
Kapitel 4 fokussiert auf Designoptimierungen und die Einbindung funktionaler Elemente in den 3D-Druck, aufbauend auf den grundlegenden Konstruktionsanforderungen, die in Kapitel 3 erörtert wurden. Hierbei wird besonders auf die Integration von beweglichen Teilen, Scharnieren, Verschlüssen und Gewinden in 3D-Modelle eingegangen sowie auf Techniken für den Leichtbau.
5 Optimierung der Oberfläche und der Nachbearbeitung
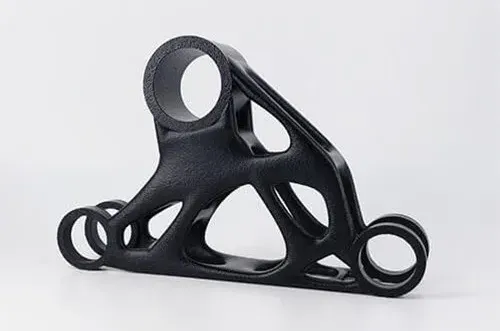
Im fünften Kapitel finden Sie umfassende Anleitungen zur Behandlung von Oberflächen, zur Minimierung des Treppenstufeneffekts und zur Vermeidung von Verzug. Darüber hinaus behandelt es Richtlinien für Nachbearbeitungsverfahren wie Färbung oder Vapor Smoothing. Diese Hinweise sind darauf ausgelegt, die Ästhetik und Qualität der additiv gefertigten Produkte zu optimieren.
6 Optimierung der Genauigkeit
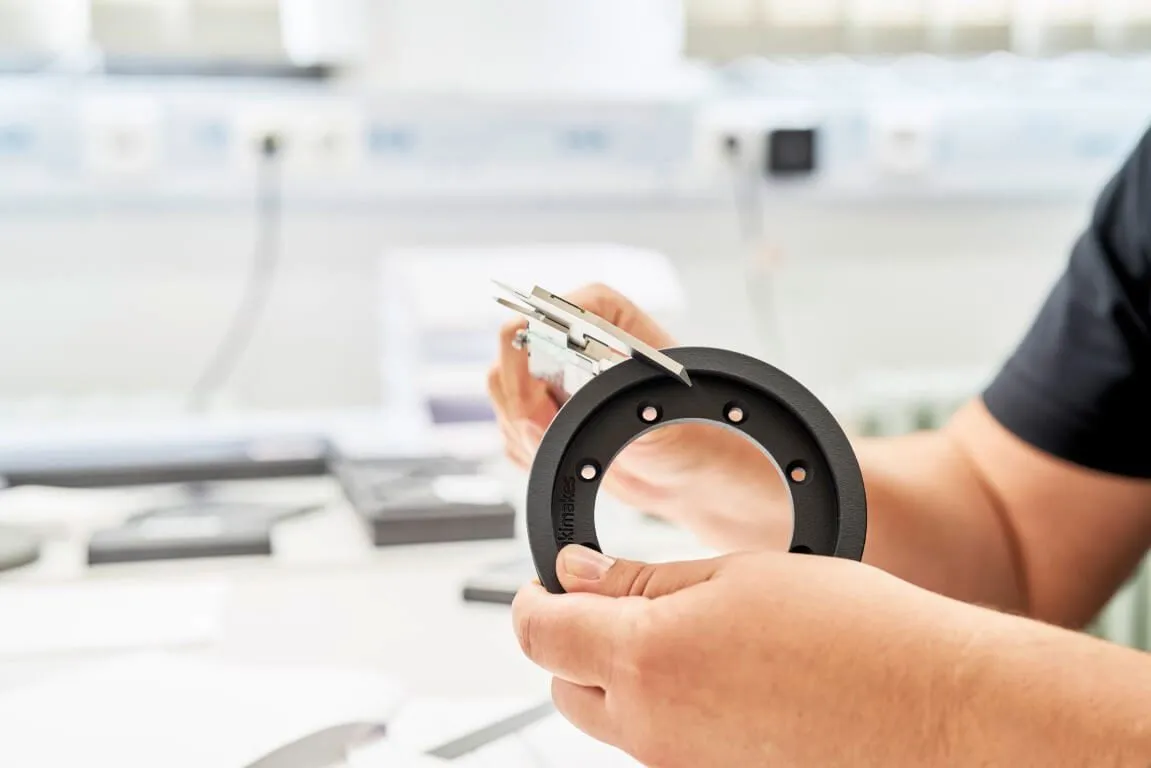
Kapitel 6 vertieft das Thema Genauigkeitsoptimierung im Kontext des Designs for Additive Manufacturing (DfAM), nachdem in den vorangegangenen Kapiteln bereits grundlegende Konstruktionsanforderungen sowie Strategien zur Optimierung von Funktionalität und Oberflächenqualität behandelt wurden. Es befasst sich eingehend mit Aspekten wie Toleranzen und Mindestmaßen für Bauteilelemente und liefert allgemeine Empfehlungen zur Verbesserung der Präzision bei additiv gefertigten Bauteilen. Das Ziel dieses Kapitels ist es, Ihnen dabei zu helfen, präzise und hochqualitative 3D-Druckobjekte zu erzeugen.
7 Optimierung der Kosten
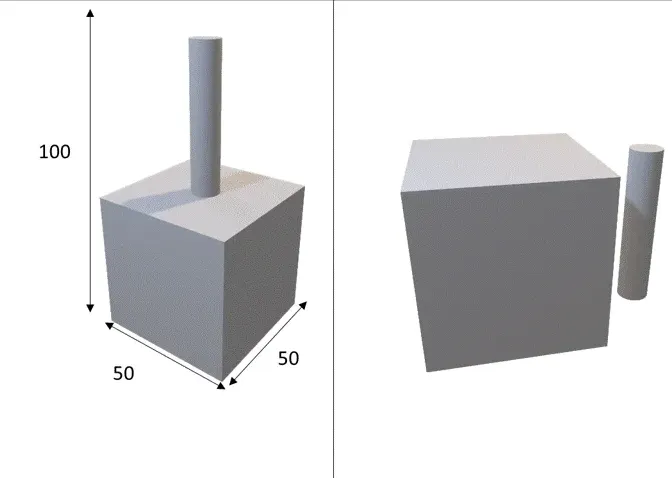
Kapitel 7 fokussiert auf die Kostenoptimierung. Es zeigt auf, wie ein gezieltes DfAM die Kosten für den 3D-Druck reduzieren kann, indem es Aspekte wie Volumenreduktion, Bauraumreduktion und die Konstruktion von Baugruppen behandelt. Ziel des Kapitels ist es, den Nutzern zu helfen, die Vorteile der additiven Fertigung optimal auszuschöpfen und gleichzeitig die Kosten zu minimieren.
Übersicht über alle Inhalte
Kapitel 1 – Das Multi Jet Fusion Verfahren
- 1 Verfahren, Materialien, Nachbearbeitung und mehr
Kapitel 2 – Anforderungen an den Datensatz
- 2.1 CAD Daten
- 2.1.1 Formate
- 2.1.2 Notwendige Eigenschaften der 3D-Modelle
- 2.1.3 Umwandlung & Auflösung von STL Dateien
- 2.2 Technische Zeichnung für die additive Fertigung
Kapitel 3: Grundlegende Konstruktionsanforderungen
- 3.1 Wandstärken
- 3.2 Minimale & maximale Objektgröße
- 3.3 Schriftgrößen
- 3.4 Bohrungen & Kanäle
- 3.5 Hohlräume
- 3.6 Fügen von Objekten
Kapitel 4: Designoptimierungen & Funktionale Elemente
- 4.1 Bewegliche Elemente
- 4.2 Schaniere
- 4.3 Verschlüsse
- 4.4 Gewinde
- 4.5 Leichtbau / Topologieoptimierung
Kapitel 5: Optimierung der Oberfläche
- 5.1 Oberseite/Unterseite von Flächen
- 5.2 Treppenstufeneffekt
- 5.3 Einsacken/Verzug
- 5.4 Konstruktionshinweise für Nachbearbeitungsverfahren im 3D-Druck
- 5.5 Allgemeine Hinweise
Kapitel 6: Optimierung der Genauigkeit
- 6.1 Toleranzen
- 6.2 Mindestmaße für Elemente von Bauteilen
- 6.3 Bauteilorientierung
- 6.4 Allgemeine Hinweise
Kapitel 7: Optimierung der Kosten
- 7.1 Volumenreduktion
- 7.2 Bauraumreduktion
- 7.3 Baugruppen