Im Kapitel 3 ging es um die grundlegenden Konstruktionsanforderungen für den 3D-Druck. Diese sind notwendig, damit der 3D-Druck gelingt und das Produkt funktionsfähig ist. Darüber hinaus können Sie aber auch Funktionalitäten in das 3D-Modell einbauen, wie Verschlüsse, Gewinde, Scharniere und bewegliche Elemente. Hierbei müssen ebenfalls einige Konstruktionsvorgaben beachtet werden. Damit befasst sich dieses Kapitel.
Kapitel 4: Designoptimierungen & Funktionale Elemente
4.1 Bewegliche Elemente
Bewegliche Elemente: Bewegliche Elemente stellen besondere Anforderungen an die Konstruktion. Hier ist insbesondere der Mindestabstand zwischen den Elementen zu beachten, der in Abhängigkeit von den Wandstärken variieren kann (Empfehlung: min. 0,7 mm). Bei Wandstärken über 30 mm sollten unbedingt größere Abstände zwischen den Elementen geplant werden. Bei Wandstärken von 3 mm hingegen reicht bereits ein Abstand von 0,3 mm aus. Die benötigten Abstände sind stark vom Design der jeweiligen Bauteile abhängig. Es ist daher empfehlenswert, Ihre speziellen Anforderungen mit unseren Technikern zu besprechen.
4.2 Scharniere
Die additiven Fertigungsmethoden bieten für das Design von Scharnieren interessante Möglichkeiten. Insbesondere Biege- und Filmscharniere haben sich bewährt. Schon geringfügige Änderungen der Wandstärken erhöhen die Flexibilität von PA 12-Bauteilen. Typische Wandstärken für Scharniere liegen zwischen 0,3 und 0,8 mm.
Allerdings sind auch hier die Mindestwandstärken zu beachten, da die Elemente sonst brechen oder schon beim Reinigen zerstört werden können. Die Wandstärke hängt insbesondere von der Länge des Scharniers ab. Polyamid 12 ist weitgehend isotrop, folglich sind die Scharniere stabil und weisen eine lange Lebensdauer auf. Die richtige Ausrichtung beim Druck sorgt dennoch für bessere Haltbarkeit. Die Haltbarkeit eines breiten Scharniers kann durch die Aufteilung in mehrere schmalere Scharniere noch weiter verbessert werden. Die schmale Wandung sollte in Z-Richtung gedruckt werden, da diese in X-Y Richtung gegebenenfalls noch dünner ausfällt.
4.3 Verschlüsse
4.3.1 Allgemein
Thermoplastische Kunststoffe eignen sich gut für die Herstellung von Schnappverschlüssen, da sie biegsam und dehnbar sind. Je nach Design des Verschlusses sind diese Verbindungen auch wieder lösbar. Bei der Konstruktion sind die Materialeigenschaften und die Gesetzmäßigkeiten der Physik zu beachten. Für die Gestaltung von Schnappverschlüssen gibt es verschiedene Möglichkeiten:
- Schnapparm: Der Schnapparm ist mit einer Verdickung am Ende versehen, die in eine dafür vorgesehene Öffnung gedrückt wird. Die Haltbarkeit der Verbindung ist von den gewählten Wandstärken abhängig. Varianten des Schnapparmverschlusses sind der L-förmige- und der U-förmige Schnapparm.
- Kugelförmiger Schnappverschluss: Dies ist eine Sammelbezeichnung für eine Vielzahl von rotationssymmetrischen Verbindungselementen, bei denen die Verformung beim Zusammenfügen über das gesamte Verbindungselement wirkt. Dabei wird das Passteil in eine entsprechende Aussparung eingeführt und damit wird die Verbindung der beiden Bauteile hergestellt.
- Dreh-Schnappverschluss: Der Schnappverschluss wird mithilfe einer Drehstange geöffnet.
4.3.2 Designhinweise
Die Stärke der Verbindung eines Schnappverschlusses wird über die Wandstärke des Schnapparms hergestellt. Je größer die benötigte Kraft ist, um den Schnapparm auszulenken, desto robuster/stärker ist die Verbindung. Die entscheidenden physikalischen Größen sind hierbei die Balkenspannung und das Flächenträgheitsmoment der Verschlussbauteile sowie das Elastizitätsmodul des Werkstoffes. Beachten sie bitte die empfohlene Verschlusskraft von 50 N bis 100 N, damit der Verschluss per Hand wieder gelöst werden kann.
Konstruktionsrichtlinien für das Verfahren Multi Jet Fusion:
- Dicke des Schnapparms: min. 1 mm
- Überhangstiefe: min 1 mm
- Eckenrundungsradius an der der Basis des Schnapparms: 1/2 Basisdicke des Arms
- Abrunden der Ecken des Überhangs
- Abschrägungswinkel des Überhangs: 35° bis 40°
- Lösewinkel: bei 90° bleibt die Verbindung dauerhaft, zum Öffnen eines Schnappverschlusses ist ein Lösewinkel deutlich unter 90° notwendig.
- Beachten Sie auch die verfahrensbedingten Toleranzen beim Konstruieren der Bauteile.
- Durch die Verwendung eines sich verjüngenden Schnapparms sinkt die Belastung an der Basis, Material wird gespart und die Verschlusskraft sinkt.
- Zum Schutz von empfindlichen Bauteilen wird die Verwendung eines Sinterkastens empfohlen.
4.4 Gewinde
Es gibt verschiedene Arten, wie Gewinde in 3D-gedruckte Objekte integriert werden können. Die verbreitetsten Methoden sind der direkte 3D-Druck des Gewindes, das Nachschneiden sowie das Einsetzen von Gewindebuchsen. Hier finden Sie eine kurze Übersicht der häufigsten Verfahren.
Gewindeeinsätze:
- Verfahren: Im CAD-Datensatz wird lediglich ein Kernloch konstruiert. Die notwendigen Abmaße variieren von Hersteller zu Hersteller (Herstellerangaben für die Gewindeeinsätze beachten – z.B. hier). Nach dem 3D-Druck wird der Gewindeeinsatz in das Kernloch eingebracht (Spreizen, Heißpressung/Ultraschall, selbstschneidend).
- Empfehlung: Wenn es die Objektgeometrie zulässt, ist dieses Verfahren die erste Wahl und bildet auch sehr kleine Gewinde zuverlässig ab.
- Haltbarkeit: Das Verfahren gewährt eine hohe bis sehr hohe Haltbarkeit.
- Dienstleistung 3Faktur: Wir bieten das Einbringen von Spreizgewinden gegen Aufpreis an.
Selbstschneidende Schrauben:
- Verfahren: Auch hier wird lediglich das Kernloch konstruiert. Nach dem 3D-Druck wird eine selbstschneidende Schraube einmalig eingedreht.
- Empfehlung: Für einmaliges Zusammenfügen eine schnelle und praktische Lösung.
- Haltbarkeit: Bei einmaliger Anwendung mittel. Wenn die Baugruppe häufiger aufgebaut und zerlegt werden muss, eher ungeeignet.
Direkter 3D-Druck eines Gewindes:
- Verfahren: Das Gewinde wird schon im CAD-Programm mit konstruiert und in das Bauteil integriert. Anschließend wird das Bauteil, wie bei 3D-Druck üblich, in das Dateiformat STEP oder STL exportiert. (Fehlerquelle: Wird das Gewinde in der Datei nicht angezeigt, ist der Export fehlgeschlagen.)
- Empfehlung: Erfahrungsbedingt ist diese Methode erst für metrische Gewinde ab einer Größe von M6 x 0.7 sinnvoll (der Hersteller empfiehlt hier M8).
- Haltbarkeit: Materialbedingt ist die Haltbarkeit dieser Gewinde eher niedrig.
Gewinde nachschneiden:
- Verfahren: Zuerst wird ein Kernloch in der CAD-Datei angelegt. Nach dem 3D-Druck wird das Gewinde in das Kernloch geschnitten. Ggf. sind bei produktionsbedingten Abweichungen noch Nachbohrungen notwendig.
- Empfehlung: Die Genauigkeit beim Nachschneiden ist nicht optimal, wir empfehlen daher das Verfahren nicht.
- Haltbarkeit: Materialbedingt ist die Haltbarkeit dieser Gewinde eher niedrig.
4.5 Leichtbau / Topologieoptimierung
Der 3D-Druck bietet im Bereich des Leichtbaus/Topologieoptimierung viele Optionen und Einsparpotenziale. Die Besonderheiten der additiven Fertigungsmethoden ermöglichen es im Zusammenspiel mit der entsprechenden Software, die Anzahl der Bauteile von Baugruppen massiv zu reduzieren. Aber auch spürbare Gewichtsreduktionen bei Bauteilen sind leicht möglich. Dies wird durch das Weglassen von nicht benötigten/nicht belasteten Elementen erreicht. Dabei wird die Funktionalität des Bauteils nicht beeinträchtigt. Dieser Prozess reduziert signifikant Gewicht und Kosten.
Objekte aushöhlen
Massive Bauteile können automatisiert mit der entsprechenden Software ausgehöhlt werden. Eine Mindestwandstärke von 2 mm wird empfohlen. Stärkere Wände erhöhen die Stabilität. Wird der Hohlraum von verbleibendem Materialpulver befreit, verringert sich das Gewicht des Bauteils. Verbleibt das nicht verwendete Material im Hohlraum, erhöht sich die Stabilität des Bauteils und die Nachbearbeitungszeit wird reduziert. Hier ist auf ausreichende Zugänglichkeit zur Entpulverung zu achten!
Gitternetzstrukturen
Dabei wird ein massives Bauteil ebenfalls ausgehöhlt und in den Hohlraum wird eine Gitternetzstruktur konstruiert. Dies verbessert die Stabilität des Objekts signifikant bei entscheidender Gewichtsreduktion und Kostenersparnis. Das Konstruieren der Gitternetzstruktur wird von der Konstruktionssoftware übernommen.
Topologieoptimierung
Dabei geht es darum, die bestmögliche Struktur, Form und Zusammenspiel der Elemente herauszufinden und zu implementieren. Ziel ist es, die Konstruktion so anzupassen, dass die gewünschte Funktionalität bei geringstmöglichem Materialeinsatz erzielt wird.
Dies äußert sich meist in einer signifikanten Reduzierung des Gewichts und damit auch des Preises des Objekts. Grund dafür ist das Weglassen von nicht belasteten Flächen. Dafür stehen Ihnen unterschiedliche kommerzielle Softwareprogramme zur Verfügung (z. B. Abaqus, Optistruct). Dabei kommen verschiedene Methoden zur Anwendung: solid isotropic material penalization method (SIMP), ground structure method, homogenization method, etc.
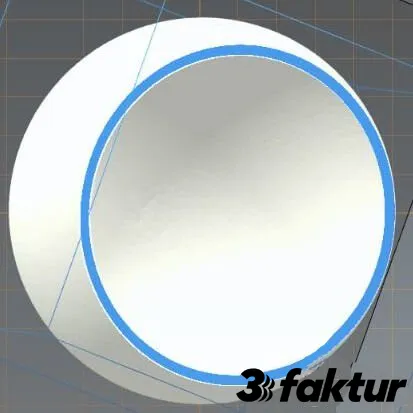
Strukturen, die größer als 10 mm sind, werden üblicherweise ausgehöhlt. Eine typische Wandstärke von 3 mm umgibt dann den entstandenen Hohlraum. Während des Druckprozesses füllt sich dieser Hohlraum mit verdichtetem Pulver. Dieses Pulver ist fest im Inneren verankert und kann daher nicht „geschüttelt“ werden.
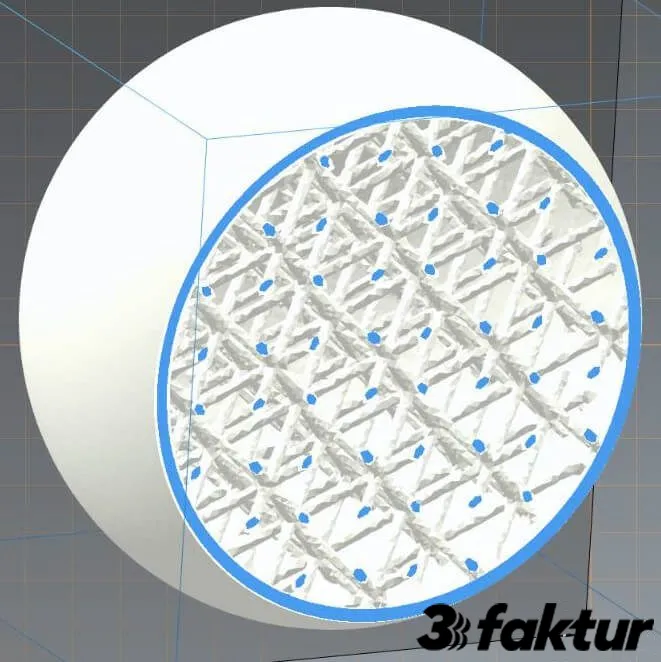
Optional können diese Strukturen zusätzlich mit einem Gitternetz ausgestattet werden. Dies gewährleistet eine erhöhte Stabilität und führt durch die gesteigerte Prozesstemperatur dazu, dass das Pulver im Innenraum leicht versintert. Dieses Vorgehen trägt zusätzlich zur Verbesserung der Stabilität des Endprodukts bei.
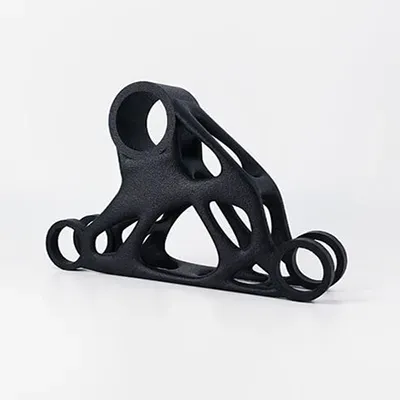
„Klassische“ Topologieoptimierungen sind überwiegend im Bereich des Metall-3D-Drucks anzutreffen. Dennoch gibt es auch im Kunststoff-3D-Druck Anwendungen, bei denen diese Vorgehensweise sinnvoll ist. Neben einer Gewichtsreduktion, die in Bereichen wie dem Automobilbau, der Robotik, der Luftfahrt oder bei Drohnen von Nutzen ist, trägt auch der effiziente Einsatz von Ressourcen zur Steigerung der Nachhaltigkeit beim 3D-Druck bei.