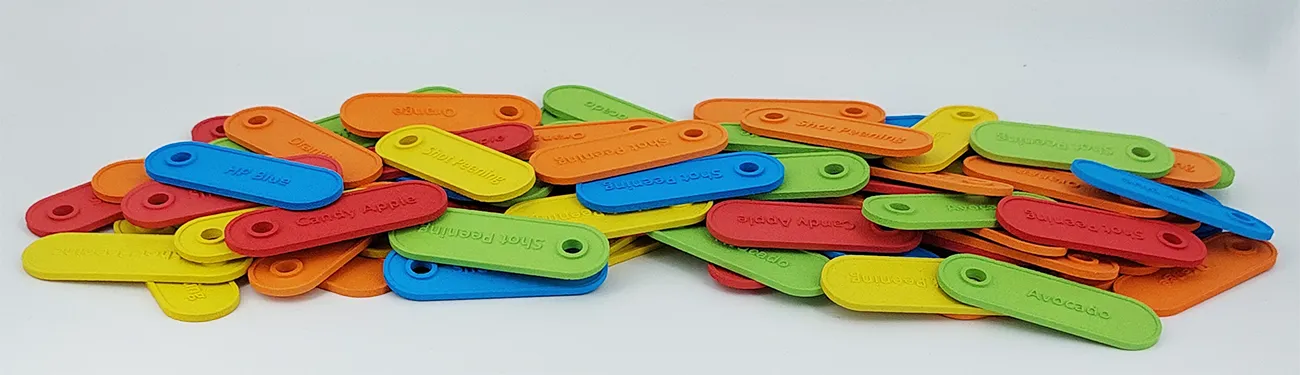
Until the end of 2022, the Multi Jet Fusion (MJF) process could only produce parts that were entirely black on the inside and, due to a technical white component, appeared gray on the outside. This lack of color variety is reminiscent of Henry Ford’s famous quote: “You can have a 3D print in any color as long as it’s black.”
The color selection in 3D printing was limited for a long time, especially in the MJF process. Fortunately, this has changed now – thanks to the material PA 12 W and the Deep Dye Coloring process, which allows for the production of parts in various colors. This article provides an overview of monochrome and full-color 3D printed parts as well as the technologies behind them.
1. Monochrome additively manufactured parts
There are two essential approaches to producing monochrome parts:
A. Colors in the raw material
In most 3D printing technologies, raw materials are already available in various colors. This is particularly useful for processes where a simple change of raw material is possible, such as Fused Deposition Modeling (FDM) or Fused Filament Fabrication (FFF). In these processes, changing the filament roll is sufficient to change the color. However, the available colors are limited to the manufacturer’s palette and may not be suitable for demanding industrial applications.
Advantages:
• Parts are fully colored.
Disadvantages:
• Limited color selection, depending on manufacturers.
• May not be suitable for demanding industrial applications.
B. Coloring of white base material
An interesting approach is dip dyeing, where white base material is dipped into a pigment solution to achieve the desired color. This method is often used in powder-based processes such as Selective Laser Sintering (SLS) and MJF.
There are two main methods:
• Simple dip dyeing: Also known as “pot dyeing.” In this method, the parts are dipped into a heated dye solution. This is economical, but color control is limited, and the penetration depth is small.
• Pressure dip dyeing (Deep Dye Coloring): This process is done under high pressure and high temperature, resulting in better color consistency and deeper penetration depth. This is especially useful for colored parts.
In the MJF-Verfahren sind schwarze Bauteile aus PA 12 im Inneren standardmäßig schwarz, während an der Oberfläche nur ein minimaler Weißanteil von wenigen Hundertsteln verbleibt. Aufgrund dieses geringen Weißanteils ist keine tiefe Eindringtiefe der Farbe erforderlich. 3Faktur verwendet das einfache und kostengünstige Tauchverfahren, um hochwertige Bauteile in bester Schwarzfärbung anzubieten, ohne Kompromisse bei der Qualität einzugehen.
Um die Qualität über verschiedene Chargen hinweg sicherzustellen, werden strenge Kontrollen implementiert. Alle Schritte sind robotergesteuert, um Abweichungen in der Reaktionszeit auszuschließen. Temperatur und Färbelösung werden sorgfältig überwacht und gemäß den festgelegten Zeitzyklen gewechselt, um eine gleichmäßige Schwarzfärbung zu garantieren.
Advantages:
• Fast production of large quantities.
• Customizable dye solutions, ideal for corporate colors.
Disadvantages:
• Inner layers remain white and can be visible in deep scratches.
2. “Full-color” parts
Manufacturing multicolored plastic parts is more complex and offers various advantages and disadvantages.
A. Full-color Multi Jet Fusion (MJF)
Unfortunately, this promising full-color technology by HP has been discontinued in favor of monochrome technology. Nevertheless, it was capable of producing stable thermoplastic colored parts, which was more cost-effective than other methods.
For more information on the current form of the Multi Jet Fusion technology, visit our page: Multi Jet Fusion: The Process.
Advantages:
• Stable, colored parts.
• Cost-effective production.
Disadvantages:
• The technology has been discontinued.
B. Polyjet/UV-Curable Inkjet
This technology allows the combination of different materials and the production of transparent objects. It is based on print heads that apply millions of tiny droplets of photosensitive materials and cure them immediately with UV light. This allows products with different material properties, color variations, and even transparent and opaque areas to be printed in a single part. The only drawback is that the material is not suitable for permanent use, limiting its application to prototyping.
Advantages:
• Material combinations possible.
• High resolution.
Disadvantages:
• Not durable enough for end products.
• High production costs.
C. Colorjet
The Colorjet technology has been on the market for over two decades and was long considered the only method for full-color 3D printing. In this method, material powder is held together using a colored adhesive, resulting in a kind of artificial sandstone. This material is relatively heavy, brittle, and has low mechanical stability. Although the manufacturer still offers the technology, it has not become widespread and is rarely encountered today.
Advantages:
• Solid material, suitable for architectural models.
Disadvantages:
• Very brittle, low resistance to environmental factors.
D. FDM / FFF with multiple print heads
Most FDM/FFF printers typically work with only one material per print job. However, there are now machines capable of printing with multiple materials to create multicolored objects. In these printers, different colors are applied by different print heads, but this can significantly extend the printing time.
A special case is the indirect full-color FDM printing developed by the Taiwanese company XYZ-Printing (New Kingpo Group). This is an indirect process because the originally monochrome object (usually white or transparent) is colored after the actual printing process.
Advantages:
• Cost-effective option.
Disadvantages:
• Low resolution.
• Usually not suitable for mass production.
3. Creating full-color models for 3D printing
For completeness, we’d like to provide you with a brief overview of how to create full-color 3D models that can be produced using one of the technologies mentioned above.
- 3D Scanning: Modern 3D scanners can create colored scans but often require post-processing to make them suitable for 3D printing.
- CAD Program Design: Most CAD programs allow the use of colors or textures in model creation, which is advantageous for technical objects.
- 3D Modeling Software Design: This method is well-suited for organic shapes but less suitable for technical objects.
About 3Faktur: 3Faktur is your 3D printing service provider for high-quality industrial plastic parts. With our 3D printing service, we support leading companies in various industries, including mechanical engineering, high-tech devices, medical technology, orthopedics, automotive industry, drone manufacturing, bicycles, commercial vehicles, toys, and more. If you have any questions about your project, feel free to contact us.