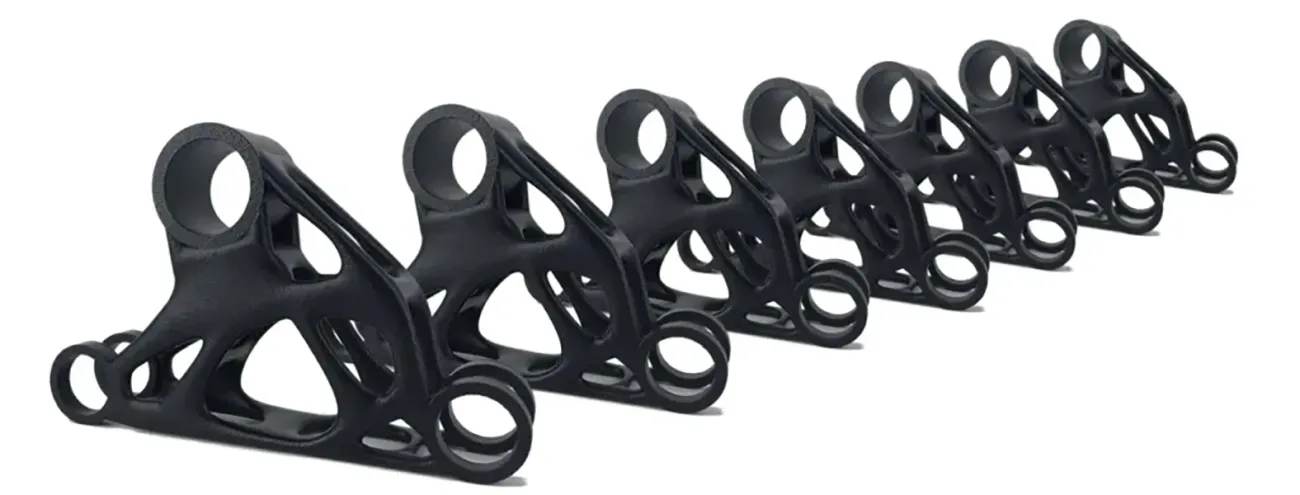
Das selektive Lasersintern (SLS) und Multi Jet Fusion (MJF) sind beides Polymer-Pulverbett-Schmelzverfahren. Dabei wird ein pulverförmiges Polymer schichtweise aufgetragen und an den gewünschten Stellen selektiv gesintert bzw. geschmolzen. So entstehen Schicht für Schicht hochwertige, industrielle Kunststoffbauteile.
Beide Verfahren haben vieles gemeinsam, z.B.
• Stützstrukturen sind nicht notwendig, es können daher hochkomplexe Geometrien produziert werden
• In einem Produktionszyklus können duzende, hunderte oder sogar Tausende Bauteile produziert werden, da diese während der Produktion miteinander verschachtelt werden können
• Beide Verfahren können nur teilkristalline Polymere verwenden. In der Praxis sind dies meist Polyamide, jedoch kommen zunehmend auch weitere Polymere wie TPU, TPA oder Polypropylen hinzu
Jedoch gibt es auch Unterschiede in den Verfahren, auf welche im Folgenden im Detail eingegangen wird.
Übersicht Lasersintern vs. Multi Jet Fusion
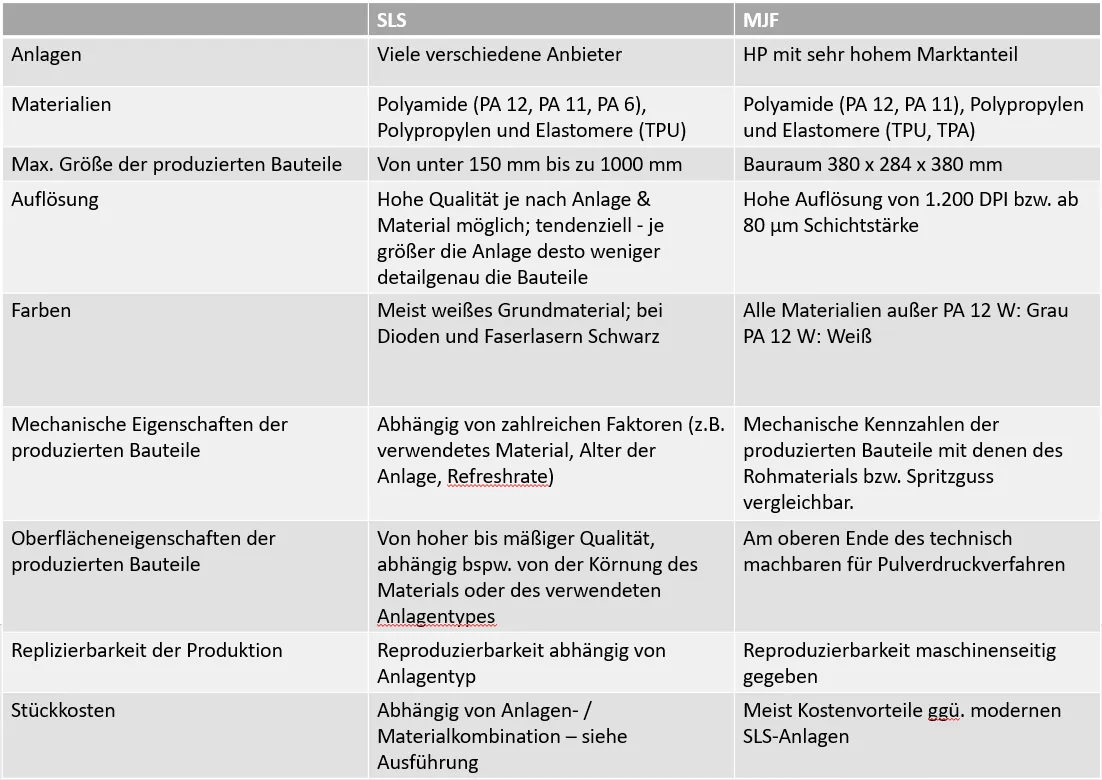
Verfahren | Anlagen | Materialien | Max. Größe | Auflösung | Farben | Mech. Eigenschaften | Oberflächeneigenschaften | Replizierbarkeit | Stückkosten
Verfahren
Selektives Lasersintern (SLS)
Das Lasersinterverfahren folgt einem relativ einfachen Prinzip: Auf eine Bauplattform wird eine dünne Schicht Materialpulver aufgetragen. Ein Laser erhitzt selektiv die spezifizierten Bereiche im Pulverbett, wodurch das Pulver so stark erhitzt wird, dass die Partikel miteinander „versintern“. Beim Abkühlen härtet das Material aus, die Bauplattform wird um etwa 100 – 120 µm abgesenkt und der Prozess wiederholt sich, bis das Objekt fertiggestellt ist.
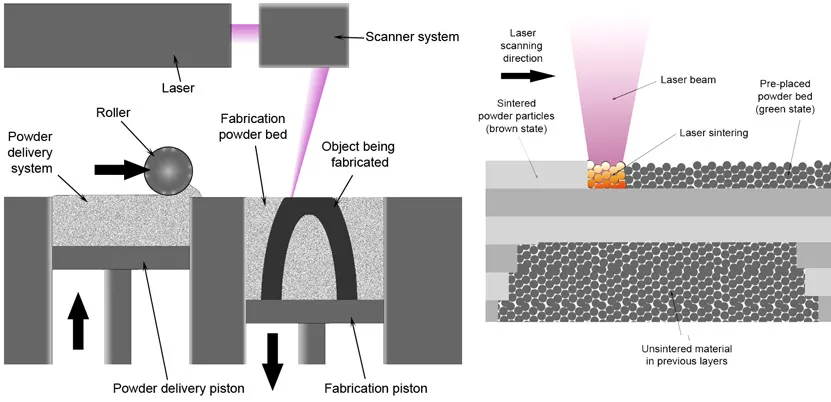
Multi Jet Fusion
Eine Gemeinsamkeit mit dem Lasersinterverfahren ist das Auftragen einer dünnen Pulverschicht auf die Bauplattform. Im Gegensatz zum Lasersintern arbeitet man jedoch nicht mit einem Laser, sondern mit Druckköpfen. Die Düsen des Jet Fusion 3D-Druckers sprühen eine wärmeleitende Flüssigkeit, genannt „Fusing Agent“, an die vom 3D-Modell vorgegebenen Stellen in das Pulver. Am Druckkopf befinden sich Heizstrahler, welche die mit Fusing Agent benetzten Bereiche stärker erhitzen als die nicht benetzten Pulverbereiche. In der Folge schmilzt das Pulver an den „bedruckten“ Stellen.
Darüber hinaus verwendet HP einen „Detailing Agent“, der um die Ränder des Objekts herum ausgebracht wird. Dieser Agent wirkt wärmeisolierend und verhindert, dass das übrige Materialpulver mit verschmilzt. Dadurch wird eine erhöhte Detailtreue gewährleistet.
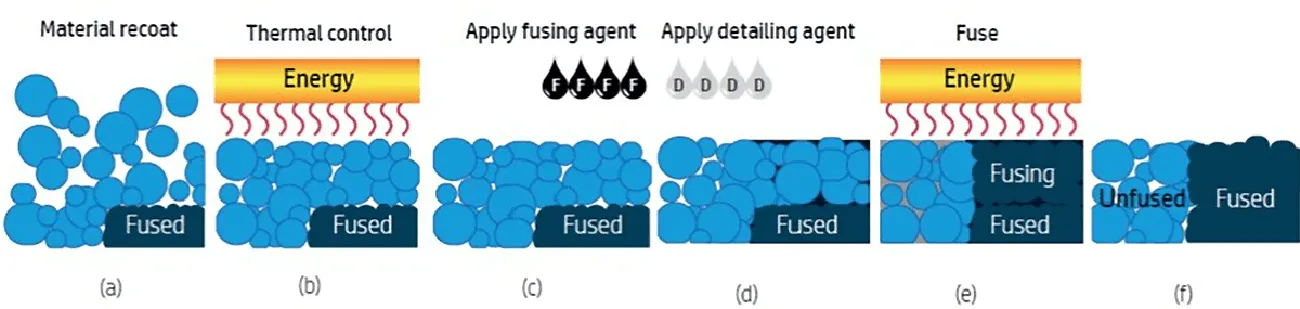
Anlagen
Selektives Lasersintern (SLS)
Einer der zentralen Unterschiede zwischen MJF und SLS ist die Vielfalt der verfügbaren Geräte. Im Bereich des Lasersinterns gibt es bereits Dutzende Anbieter sowohl für industrielle als auch semi-professionelle Systeme. Der Marktführer im Bereich der industriellen Geräte ist EOS, bekannt für weit verbreitete Modelle wie die kompakte Formiga, die trotz ihres kleineren Bauraums (~250 mm) hohe Auflösungen erlaubt. Daneben stehen die 39x-Systeme, die mit größeren Bauraumen punkten. Weitere industrielle Anbieter sind beispielsweise 3D Systems, Prodways und Farsoon. Im semi-professionellen Sektor existieren kleinere Geräte, wie sie beispielsweise von Formlabs oder Sintratec angeboten werden.
Durch die 30-jährige Marktpräsenz dieser Technologie existiert eine große Vielfalt an Gerätetechnik, einschließlich älterer Systeme. Deshalb sind nicht alle „Lasersinterteile“ gleich. Die Qualität kann von Anbieter zu Anbieter erheblich variieren.
Multi Jet Fusion (MJF)
Mit der Einführung des MJF-Verfahrens betrat HP zuerst den Markt und beherrscht seitdem dieses Technologie-Segment. Es gibt noch zwei weitere Anbieter von ähnlichen Technologien: Voxeljet mit dem HSS-Verfahren und Stratasys mit dem SAF-Verfahren, obwohl beide im industriellen Umfeld noch eher selten vertreten sind.
MJF-Geräte gibt es mittlerweile in der zweiten Generation. HP startete mit dem 42er-System und brachte nach weniger als vier Jahren eine Weiterentwicklung, die 52er, auf den Markt. Hinsichtlich Maßgenauigkeit und mechanischer Eigenschaften sind beide Geräte vergleichbar, allerdings ist die 52er Technologie deutlich leistungsfähiger aufgrund kürzerer Produktionszyklen.
In der Vergangenheit gab es auch kleinere Systeme von HP (540 & 580), welche teils in der Lage waren vollfarbige Bauteile zu produzieren. Diese Technologie wurde jedoch seitens HP eingestellt.
Materialien
Selektives Lasersintern (SLS)
Beide Verfahren, SLS und MJF, nutzen teilkristalline Polymere, weitere Details dazu finden Sie auf der Seite Polymere für den 3D-Druck. In der Praxis wird der Markt hauptsächlich von Polyamiden dominiert, insbesondere von Polyamid 12, obwohl auch Polyamid 11 Verwendung findet. Bei der Lasersinter-Technik ist ebenfalls die Produktion mit PA6 möglich, welche erhöhte Prozess-Temperaturen erfordert. Im Bereich der Elastomere wird bei SLS meist auf TPU zurückgegriffen. Darüber hinaus gibt es auch einige hochspezialisierte Materialien im Markt, wie beispielsweise flammhemmende, ESD-konforme oder faserverstärkte Materialien.
Ein wesentlicher Vorteil von SLS ist, dass die Materialien leichter ausgetauscht werden können und es „offene Anlagen“ auf dem Markt gibt, auf denen eigene Materialien getestet und implementiert werden können. Nachteilig kann sich auswirken, dass bei Verwendung von „Nicht-Standard“ Materialien ggf. Abstriche bei der Replizierbarkeit gemacht werden müssen.
Multi Jet Fusion (MJF)
Obwohl die Materialpalette bei Multi Jet Fusion kleiner ist, besteht der Vorteil darin, dass alle Materialien entweder direkt von HP geliefert oder durch ein aufwändiges Verfahren von HP zertifiziert werden. Dies gewährleistet eine herausragend konstante Materialqualität. Die Materialpalette umfasst u.a. Polyamid 12 und 11, TPUs von Lubrizol und BASF, Polypropylen von BASF sowie ein elastisches TPA von Evonik.
Maximale Größe der produzierten Bauteile
Selektives Lasersintern (SLS)
Aufgrund der Bandbreite an Anlagen lässt sich hier keine allgemeingültige Aussage treffen. Semi-professionelle Anlagen haben meist kleinere Bauräume, teils unter 150 mm. Die größten Anlagen am Markt können hingegen auf Bauräume von bis zu 1.000 mm kommen, als Beispiel wäre hier die Farsoon 1001P zu nennen.
Multi Jet Fusion (MJF)
Die Anlagen der 42er und 52 Serie verfügen über einen Bauraum von 380 x 284 x 380 mm.
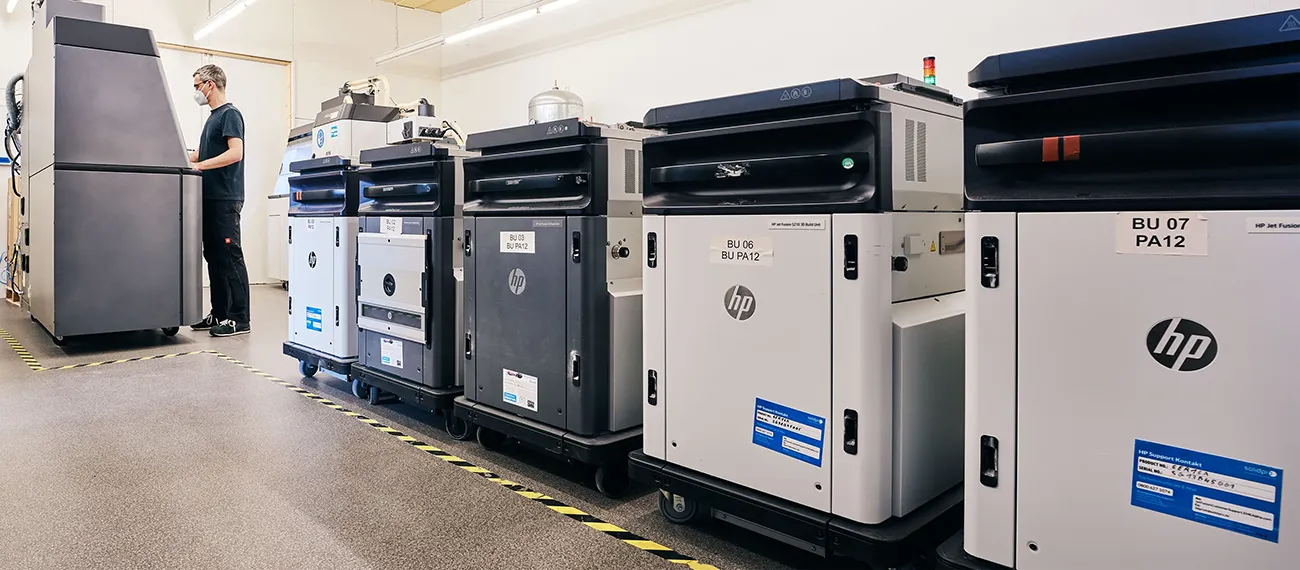
Auflösung
Selektives Lasersintern (SLS)
Die Auflösung bei SLS wird von verschiedenen Faktoren beeinflusst, darunter die Schichtstärke, der Spot-Durchmesser des verwendeten Lasers, die Scanstrategie des Lasers und die Korngröße des Materials. Hierbei gibt es erhebliche Unterschiede zwischen den einzelnen Anlagen. Kleinere industrielle Anlagen bieten typischerweise eine hohe Auflösung, vorausgesetzt das Material erlaubt dies. Ein Beispiel hierfür ist die Formiga von EOS, die grundsätzlich eine hohe Auflösung bietet, aber in der FDR („Fine Detail Resolution“) Version sogar sehr feine Details auflösen kann. Anlagen mit größerem Bauraum nutzen dagegen häufig größere Spot-Durchmesser und Schichtstärken, um eine effiziente Produktionsgeschwindigkeit zu ermöglichen, was dazu führen kann, dass feine Details oder kleinere Bauteile nicht optimal zur Geltung kommen.
Multi Jet Fusion (MJF)
Ein wesentlicher Vorteil der MJF-Technologie liegt in der deutlich erhöhten Produktionsgeschwindigkeit. Diese ermöglicht es, die Schichtstärke auf ein Minimum zu reduzieren (typischerweise 80 µm), ohne dabei die Produktionseffizienz zu beeinträchtigen. Diese Eigenschaft, kombiniert mit der enorm hohen Auflösung von 1.200 DPI der Druckköpfe, ermöglicht es MJF-Geräten, Detailgrade zu erreichen, die sonst nur von den besten SLS-Anlagen erreicht werden können. Die mittleren Korngrößen der Pulver sind vergleichbar mit Standard-SLS-Materialien (z.B. PA2200) und liegen typischerweise bei 50-60 µm.
Farben
Selektives Lasersintern (SLS)
Die meisten SLS-Anlagen drucken auf Basis von weißem Grundmaterial, das nach dem Druckvorgang eingefärbt werden kann. Grundsätzlich lässt sich bei SLS das Rohmaterial einfärben, wobei Schwarz eine häufige Wahl ist. Diese Farbe hat oft einen technologischen Hintergrund. So arbeiten kostengünstige Lasersinteranlagen, beispielsweise von Formlabs, meist mit Diodenlasern, für die eine schwarze Grundfarbe des Pulvers notwendig ist. Ähnlich verhält es sich mit der FLIGHT Technologie, die vor allem Farsoon einsetzt – hier kommt ein Faserlaser zum Einsatz, der deutlich höhere Produktionsgeschwindigkeiten ermöglicht. Auch bei einem Faserlaser ist schwarzes Rohmaterial technisch vorteilhaft.
Multi Jet Fusion (MJF)
In der ursprünglichen Version des MJF-Verfahrens ist das Ausgangsmaterial weiß, während der Fusing Agent schwarz ist. Dies führt dazu, dass die inneren Teile der Bauteile vollständig schwarz sind, an der Oberfläche jedoch ein geringer Weißanteil verbleibt (angesintertes Restmaterial). Daher erscheinen die Bauteile grau und eher inhomogen. Typischerweise wird nach dem Druck eine Tauchfärbung durchgeführt, die den Bauteilen eine homogene Färbung und vollständige Schwärzung verleiht.
Seit Anfang 2023 ermöglicht eine neue Gerätevariante, die 5240 von HP, auch das Drucken von vollständig weißen Bauteilen. Diese zeichnen sich im Vergleich zu den meisten Lasersinter-Bauteilen durch ein homogeneres Weiß auch bei dünnen Wandstärken aus (letztere sind beim SLS häufig transluzent). Zudem bieten sie eine deutlich erhöhte Stabilität gegenüber UV-Einstrahlung – sowohl in Bezug auf die Farbstabilität (kein Vergilben, wie es beim SLS üblich ist) als auch hinsichtlich der mechanischen Eigenschaften. Hier zeigt sich eine signifikant verringerte Abnahme der mechanischen Eigenschaften unter UV-Einwirkung im Vergleich zu gängigen SLS-Materialien.
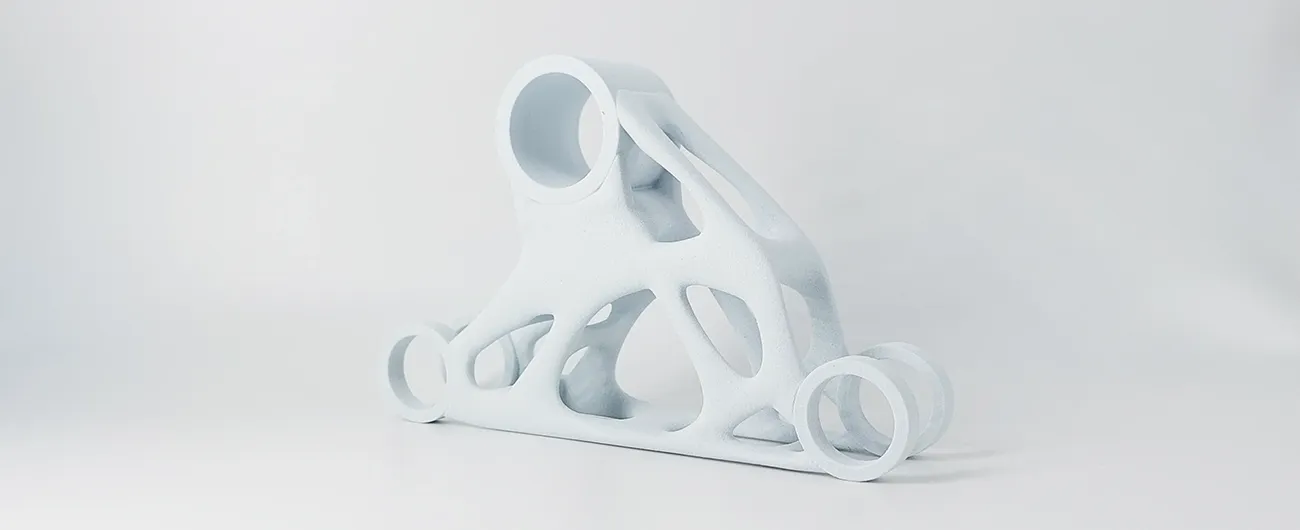
Mechanische Eigenschaften der produzierten Bauteile
Selektives Lasersintern (SLS)
Die mechanische Leistungsfähigkeit der Bauteile wird stark durch das verwendete Material und die Anlage beeinflusst. Bei semi-professionellen Anlagen, bei denen ein Diodenlaser zum Einsatz kommt, ist die mechanische Belastbarkeit der Bauteile oft eingeschränkt. Auch bei älteren Anlagen, deren Laser viele Betriebsstunden hinter sich haben, ist häufig eine Abnahme der mechanischen Stabilität der produzierten Bauteile zu beobachten.
Eine weitere SLS-spezifische Eigenschaft ist die hohe „Refresh-Rate“. Dabei handelt es sich um das Verhältnis von neuem zu wiederverwendetem Rohmaterial pro Druckvorgang. Beim Lasersintern liegt dieser Wert typischerweise bei 50% (d.h., 1:1 Neu- und Altpulver). Wenn der Anteil des Neupulvers in der Produktion reduziert wird, nimmt die mechanische Belastbarkeit des Druckteils signifikant ab.
Multi Jet Fusion (MJF)
Aufgrund der begrenzten Anzahl von Anlagen und der niedrigen Refresh-Rate von nur 20% bleibt die mechanische Belastbarkeit der Bauteile konstant. Probleme können auftreten, wenn Nutzer zu viele Bauteile gleichzeitig drucken (eine „zu hohe Packing-Rate“ verwenden). Die daraus resultierende höhere Prozesstemperatur kann das Pulver schneller altern lassen, was ebenfalls zu einer Herabsetzung der mechanischen Belastbarkeit führen kann. 3Faktur führt in diesem Zusammenhang strenge Kontrollen durch, um dieses Problem zu vermeiden und eine gleichbleibend hohe Materialqualität sicherzustellen.
Insgesamt haben mit MJF produzierte Bauteile im Schnitt eine höhere Materialdichte und sind damit, bei gleichem Polymer, am oberen Ende des technisch machbaren.
Oberflächeneigenschaften der produzierten Bauteile
Selektives Lasersintern (SLS)
Die Qualität der Oberfläche bei SLS hängt ähnlich wie die Detailauflösung von verschiedenen Faktoren ab, darunter die Körnung des Materials und die Schichtstärken. Eine gröbere Körnung und größere Schichtstärken können zu einer minderwertigen Oberflächenqualität führen. Dies ist stark von der verwendeten Anlage und des Materials abhängig. Eine gute Oberflächenbeschaffenheit entsteht auch bei niedrigen Prozesstemperaturen, die jedoch zu verringerten mechanischen Eigenschaften führen können. Das ist zum Teil bei sehr kostengünstigen Anlagen der Fall: Die Bauteile „sehen gut aus“, weisen jedoch eine reduzierte Belastbarkeit auf.
Multi Jet Fusion (MJF)
Die Qualität der Oberflächen bei MJF ist durchgehend hoch und befindet sich am oberen Ende dessen, was beim Pulverdruck machbar ist. Dies liegt ähnlich wie bei der Detailauflösung an der feinen Körnung des verwendeten Pulvers, der hohen Auflösung der Druckköpfe und der geringen Schichtstärke.
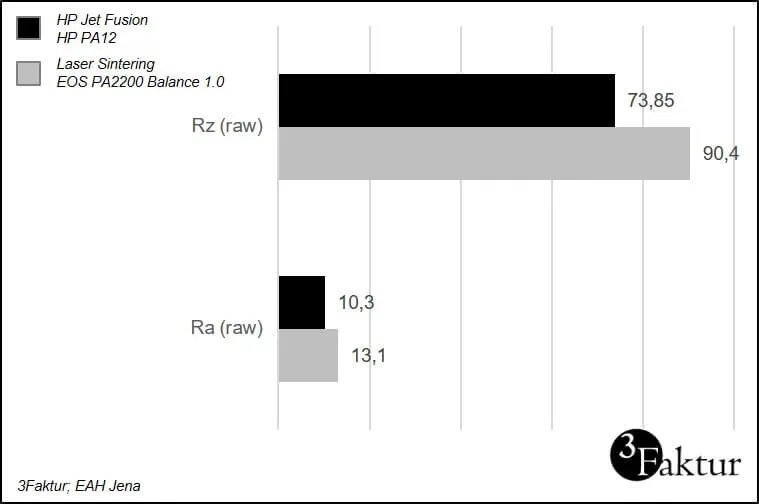
Quelle: 3Faktur & Ernst-Abbe Hochschule Jena
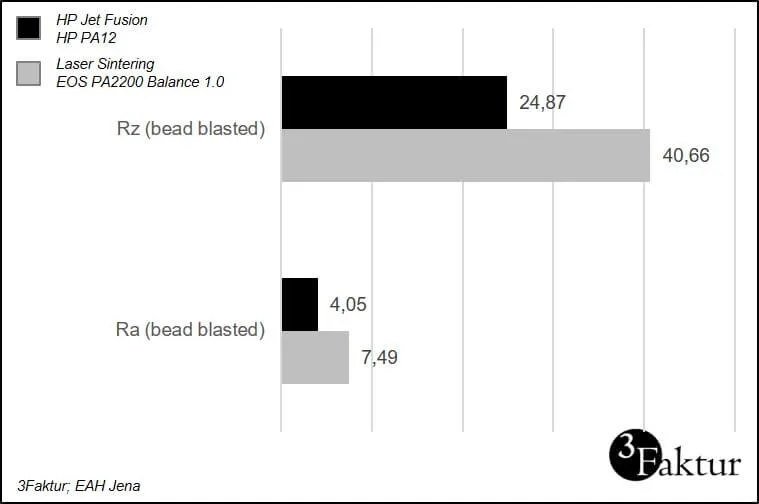
Quelle: 3Faktur & Ernst-Abbe Hochschule Jena
Replizierbarkeit der Produktion
Selektives Lasersintern (SLS)
Bei hochpreisigen, industriellen und gut gewarteten Anlagen von namhaften Herstellern wie z.B. EOS, ist eine Reproduzierbarkeit gegeben. Bei kostengünstigeren bzw. älteren Anlagen kann die Qualität jedoch stark schwanken.
Multi Jet Fusion (MJF)
Das MJF-Verfahren wurde von HP für die industrielle Produktion und nicht für den Prototypenbau konzipiert. Daher ist eine hohe Reproduzierbarkeit bei guter Instandhaltung der Anlage definitiv gegeben.
Stückkosten
Selektives Lasersintern (SLS)
Wie bei allen anderen Faktoren, ist auch hier eine Betrachtung der Anlagen- / Materialkombination notwendig. Bei niedrigen Preisen kann u.U. eine der folgenden Situationen vorliegen:
• Anlagenalter: Ältere, abgeschriebene Anlagen können oft zu einem sehr günstigen Preis produzieren. Je nach Instandhaltung und Lebensdauer des Lasers kann die Qualität und/oder Reproduzierbarkeit der Ergebnisse jedoch eingeschränkt sein.
• Anlagenqualität: Werden sub-industrielle Systeme bzw. Systeme von nicht namhaften bzw. Nischenanbietern verwendet, können auch hier günstige Preise angeboten werden. Ebenso ist hier die Qualität sorgfältig zu evaluieren, da sie ggf. nicht industriellen Ansprüchen gerecht wird.
• Materialqualität: Wird Material von Nischenanbietern bzw. eine zu niedrige Refresh-Rate gewählt, können auf Kosten der Bauteilqualität Einsparungen erzielt werden.
Bei modernen, gut gewarteten industriellen Anlagen und gängigen Materialien, wie PA2200 von EOS oder DuraForm von 3D Systems, und den empfohlenen Refresh-Raten kann eine hohe Qualität gewährleistet werden. Allerdings können sich hier für das SLS-Verfahren u.U. Kostennachteile ergeben:
• Abschreibung: Preislich liegen die Anlagen oft ähnlich denen von MJF-Anlagen. Allerdings ist die Druckgeschwindigkeit reduziert, was zu einer höheren Abschreibung pro Bauteil führt.
• Refresh-Rate: Während beim MJF-Verfahren nur 20% Neupulver pro Druck benötigt werden, liegt dieser Wert bei SLS bei 50%, daher sind die Materialkosten pro Druck deutlich höher. Dem SLS-Verfahren kommt zugute, dass eine höhere Packdichte („Packing Rate“) erreicht werden kann. Dies kann jedoch den Mehraufwand an Pulver i.d.R. nicht kompensieren.
Multi Jet Fusion (MJF)
Durch die hohe Leistungsfähigkeit des 3D-Druckers, eine umfangreiche und teils automatisierte Prozesskette bei dem Verfahren sowie wenig Materialverbrauch hat dieses Verfahren mit vergleichbaren SLS Anlagen meist Kostenvorteile.
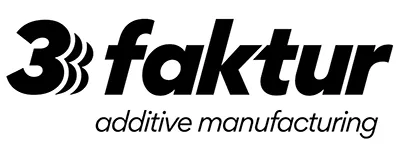
Über 3Faktur: 3Faktur ist Spezialist für 3D-Druck, Rapid Prototyping und Rapid Manufacturing. Wir arbeiten mit dem Multi Jet Fusion-Verfahren von HP und bieten unterschiedliche Materialien für den Prototypenbau und die Serienproduktion an. Sollten Sie Fragen zu Ihrem Projekt haben, können Sie uns gern kontaktieren.