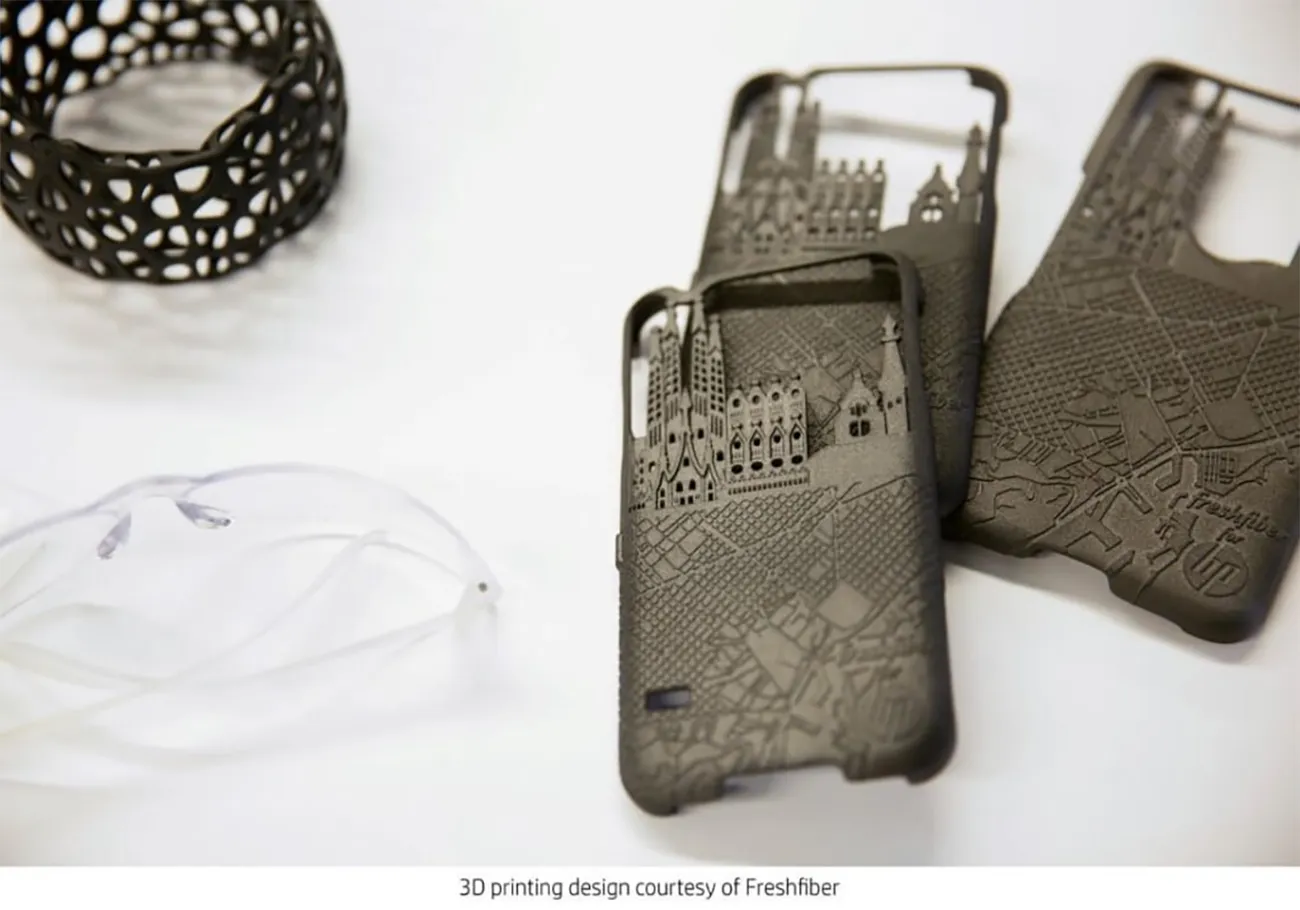
For over 150 years, people have been using plastics to obtain specific technical properties. Several methods have been developed to process plastics. Turning, milling, and injection molding are the most well-known and widely used. Additive manufacturing processes like 3D printing are the most recent methods for processing plastics. Until recently, additive manufacturing processes were considered suitable only for prototyping/sample production. However, 3D printing technologies have now advanced to the point where serial production (including small or pre-series) can seriously compete with established methods.
Methods for Zero, Pre-, or Small Series Production of Plastic Components
For the mass production of plastic components, injection molding is almost always the most economical method. For certain objects (e.g., eyeglass frames), milling is often used as well. Vacuum forming/thermoforming is also a commonly used method for packaging/blister packaging.
In the case of small series (quantities up to a few thousand), the situation looks somewhat different. Additive manufacturing methods have gained a lot of ground on traditional methods in this area in recent years. With the Multi Jet Fusion process (HP), the limits of what is possible have been pushed even further in this area.
In this article, we want to take a closer look at the most important methods for the pre- and zero-series production of plastic objects and show the advantages and disadvantages as well as the application possibilities of the individual technologies. Due to the complexity and variety of the respective components and methods, this can naturally only be a rough overview, which does not cover all details and methods.
For the sake of clarity, we have not included laser cutting and punching in the comparison, as these methods can also be an economic option for some objects/projects.
Overview of Suitable Methods for Your Small Series
Additive Manufacturing
Methods
For the small series production of plastic objects, three 3D printing methods are suitable: Multi Jet Fusion (standard and full-color); laser sintering; and FDM/FFF.
HP Multi Jet Fusion
HP’s Multi Jet Fusion 3D printing process is a new method that has only been on the market since 2017. Similar to laser sintering, it uses PA 12 (‘Polyamide 12’ or ‘Nylon 12’) as the material. The main advantages of Jet Fusion over laser sintering are significantly higher production speed, greater accuracy, and increased stability of the 3D-printed objects. In terms of mechanical strength, Jet Fusion objects are comparable to those produced by injection molding with PA 12. Geometries similar to those achievable with laser sintering are possible with Jet Fusion, but thinner wall thicknesses can be achieved. The main disadvantage currently is that the maximum size of objects is 380 mm, and the base color is always gray, although it can later be colored with dark colors (usually black). Since 2019, it has been possible to print in full color using the Multi Jet Fusion process. The parts produced with this method are minimally less stable but otherwise equivalent to standard parts.
Nevertheless, the process is considered the new standard in additive manufacturing for small series production of plastic components with quantities in the low thousands.
Laser Sintering
Laser sintering primarily uses polyamide 12 (Nylon 12) as the material. The material is often supplemented with additives (glass beads, aluminum powder, or short fibers). The major advantages of PA 12 are its durability, biocompatibility, and high stability. These properties make PA 12 a popular material used in many industries.
With laser sintering, you can produce virtually any geometric complexity (no support structures required), allowing parts to be optimized for their intended function. The only limitations are the need to maintain certain minimum wall thicknesses (∼ 1 mm). Compared to FDM, laser sintering has a high production speed. Machine build volumes can also be used much more efficiently, enabling a large number of parts to be produced per production cycle. However, cycle times are quite long, meaning the process is less suitable for mass production. Additionally, material costs are high because only a small portion of the material powder can be recycled (approximately 50 – 60%).
The main applications of laser-sintered parts are housings/casing parts or mechanically stressed components.
FDM/FFF
In Fused Deposition Modeling (FDM), the plastic (thermoplastic) is in the form of wire (filament). The filament is melted and deposited onto the build platform. The process is relatively slow and produces surfaces of medium quality (good surfaces only achievable with elaborate post-processing methods). Due to its high stability and the popularity of the thermoplastics used (e.g., ABS, polycarbonate, polyamide 6, polyetherimide), it is in high demand. The heat resistance and high impact resistance of the materials, in particular, make the 3D printing process popular with users in the automotive and aerospace industries.
Summary
The greatest advantage of additive manufacturing is that no tools/molds or other fixtures are needed to produce the objects. Therefore, the implementation speed of your project is much higher than with machining processes or plastic injection molding. If the surface quality and available materials are acceptable for the particular product, then additive manufacturing (especially Jet Fusion) is a fast and cost-effective solution for your prototypes or small series.
Cost Calculation
The costs in additive manufacturing consist of the following 3 components:
- Machine Hours: The equipment is expensive, and depreciation is allocated to printed objects (depending on occupied machine space and running times).
- Material Costs: Used thermoplastics (e.g., PA 12) are around 5 – 10 times more expensive than identical materials used in injection molding. The reason for this is the more precise and finer powder structure required for laser sintering and multi-jet fusion. The same applies to filaments in FDM 3D printing.
- Labor Costs: Machine setup and post-processing of objects are done manually, which is relatively labor-intensive and is factored into the cost calculation.
Advantages
- Fast: No tools, programs, or fixtures required – production is done directly from the CAD file.
- Flexible: Objects can be adjusted at any time without problems. Low piece costs even with small batch sizes. Just-in-time production at optimal piece costs possible.
- Cost-Effective: For low batch sizes, especially for small to medium-sized objects, often the most cost-effective method for manufacturing plastic parts.
- Object Complexity: Jet fusion and laser sintering have few limitations in the complexity of geometric shapes – this simplifies the design process and offers advantages such as weight savings or reduction of complexity in manufacturing (no need to manufacture individual parts and assemble them).
Disadvantages
- Restricted Material Selection: Only a small number of polymers available. In particular, specialty materials (e.g., with certain certifications) are often (still) not available.
- Surface Finish: Ra values are often 10 or higher, higher surface finishes require sometimes elaborate (cost-increasing) post-processing.
- Tolerances: The accuracies in additive manufacturing generally range from 1 to 3 tenths per 100 mm, which is significantly less precise than what can be achieved with machining or injection molding.
Vacuum Casting
The Process
Prior to vacuum casting, a master model is created (usually using 3D printing techniques such as stereolithography or polyjet, or using machining processes). Subsequently, vacuum molding is performed using silicone. Casting is usually done with polyurethanes, epoxies, or acrylics. The cost of mold production is low compared to injection molding (often in the lower to mid-three-digit range). However, with the limitation that a mold made in this way is only sufficient for approximately 15 – 50 casts (usually around 25). Very good surface qualities can be achieved. Injection molding-specific methods such as overmolding can also be simulated.
Cost Calculation
In vacuum casting, there are mainly two cost factors:
- Labor Costs: For mold making and casting per part, meaning the more complex the object, the more complex and time-consuming the work process (sanding, preparing the master model).
- Material Consumption: Materials (casting silicone, resins) are generally very expensive, so material costs account for a high proportion of manufacturing costs.
Advantages
- Fast: With mold making and casting, low quantities can be produced within a few days.
- Cost-Effective: For low quantities (double-digit or low triple-digit ranges), very cost-effective compared to injection molding.
- Variability: Many materials available for casting – numerous effects from injection molding possible (overmolding, soft materials, transparencies).
Disadvantages
- Mold Stability: Molds are not durable, batches are therefore very small. Objects may vary from mold to mold (tolerances).
- Quantities: Large quantities are hardly economically feasible with this technology.
- Material Classes: Commonly used thermoplastics in everyday practice cannot be processed with this method.
Applications
Vacuum casting is particularly suitable for the production of pre-series parts that are later to be produced by injection molding (vacuum casting enables surface qualities similar to injection molding). Other methods are better suited for the production of functional components (additive manufacturing, injection molding, machining processes).
Machining
The Processes
Machining technologies (e.g., turning, milling) are highly complex but also offer users many production possibilities. The rotary tools used to extract the desired objects from the material block/plate are among the best the industry has to offer. However, when working with plastics, these tools can also cause problems as the resulting temperatures can damage the workpieces.
Source: YouTube / FWU Das Medieninstitut der Länder
Source: YouTube / FWU Das Medieninstitut der Länder
Cost Calculation
For machining processes, the following factors have been identified as cost drivers:
- Labor Hours: Programming the machines and post-processing (e.g., deburring) are time-consuming, and high setup costs are incurred.
- Machine Hours: Machines are very expensive, and their depreciation is allocated to the manufactured objects.
- Materials and Consumables: Tools wear out, and workpieces are cut out from material blocks, resulting in a lot of material waste.
Advantages
- Materials: High-performance plastics like PEEK or similar can be processed in high quality.
- Accuracy: Machining processes can achieve very high accuracies (depending on requirements).
- Surfaces: Very good quality surfaces can be achieved depending on requirements.
- Flexibility: The variety of machines also allows for the processing of extremely large parts (sometimes several meters).
Disadvantages
- Cost: Preparations (writing programs, etc.) are very labor-intensive, making it an expensive process for complex workpieces and long machine run times.
- Complexity of Process: Manufacturing requires highly experienced companies to ensure the desired product quality.
- Speed: Production speed is often rather slow depending on the part and machines used.
Applications
Machining processes are suitable for prototypes or for quantities below those for which injection molding would be economical. This is particularly true when only small tolerances are desired or very good surface finishes are needed. Especially for compact shapes or objects with low geometric complexity, machining is an economical option.
Injection Molding
The Process
Injection molding is a relatively old (since about 1850) and well-developed process for mass production. In this process, heated, liquid plastic is injected into a mold. There, it cools down until it solidifies again. The finished object is then ejected from the mold. This process offers a huge range of applications. The most famous objects manufactured using this process are the famous LEGO bricks. But also the garbage containers in front of your house are manufactured using this process.
The crucial aspect of injection molding is the creation of the mold. The quality of the mold determines the cycle time (time from injection to ejection of the object), accuracy, surface quality, and many other parameters. Therefore, a large part of the development work is invested in creating the mold.
Source: YouTube / oncampusFHL
Source: YouTube / oncampusFHL
Cost Calculation
In injection molding, the creation of the mold is the biggest cost driver. For very large objects with high quality requirements, six-figure amounts are possible. For small, simple objects of lower quality and for batch sizes of < 5,000 pieces, you can expect costs starting from approximately EUR 2,500. Typical tools for producing several thousand pieces typically cost (for ‘normal’ components) around EUR 15,000 – 25,000.
Advantages
- Cost: Mold creation is a cost driver; moldings are relatively simple and inexpensive. → For high volumes, the process is almost unbeatably inexpensive.
- Quality: Depending on product requirements, very high accuracies and surface values can be achieved.
- Range: A wide variety of plastics are available.
Disadvantages
- Initial Investment: Mold creation is enormously expensive. → Unit price for low volumes is very high.
- Low Flexibility: The mold cannot be easily modified. Changes to the object often require a new mold or a new insert for a mold.
- Restricted Complexity: Multi-material components (or complex objects) can be created using multi-part molds, but this greatly increases costs.
Applications
Injection molding is suitable for the production of plastic objects of any kind in high to very high quantities.
Deep Drawing
The Process
A plastic sheet is heated and sucked/pressed onto a mold using vacuum/underpressure. The plastic sheet now takes on the contour of the mold and solidifies in this position. The molds for this process are usually much cheaper to produce than for injection molding. However, there are some limitations in component geometry. Only objects that can be formed from a plastic sheet can be manufactured (usually cups/blister packaging).
Source: YouTube / Bernard Vanosmael
Source: YouTube / Bernard Vanosmael
Cost Calculation
The shape of the object also has a major impact on the costs in deep drawing. However, the mold/tool is less expensive than in the injection molding process. Material consumption is also a cost factor, especially since relatively large amounts of material are cut off depending on the shape of the object (especially at the edge). Labor costs for post-processing of the objects are not crucial for series production in deep drawing.
Advantages
- Cost-effective: For typical deep drawing forms like blister packaging, the process is cost-effective.
- Variable: Very large parts and various materials can also be realized.
Disadvantages
- Types of Components: Limited number of types of components producible.
- Complexity: Complex plastic parts with different wall thicknesses, openings, etc. are not or only with great effort possible.
Applications
Deep drawing is most commonly used in the production of packaging materials (blister) and simple disposable items like drinking cups. However, form components are also manufactured using this method in the automotive industry.
Comparison of Manufacturing Methods
Summary
On the way from prototype to finished mass-produced product, all sorts of uncertainties can arise. For mass-produced goods, a zero or pilot series is recommended. This allows you to test the product/production well before transitioning to mass production (usually injection molding). For lower quantities (several hundred to a few thousand) and especially for small/medium-sized objects, additive manufacturing offers a fast and flexible alternative to traditional manufacturing methods. Another advantage of 3D printing processes is the significant simplification of design work and the production process.
About 3Faktur: 3Faktur specializes in 3D printing, rapid prototyping, and rapid manufacturing. We utilize HP’s Multi Jet Fusion technology and offer various materials for prototyping and series production. If you have any questions about your project, feel free to contact us.