Kurzübersicht Toleranzen unserer 3D-Druck Verfahren
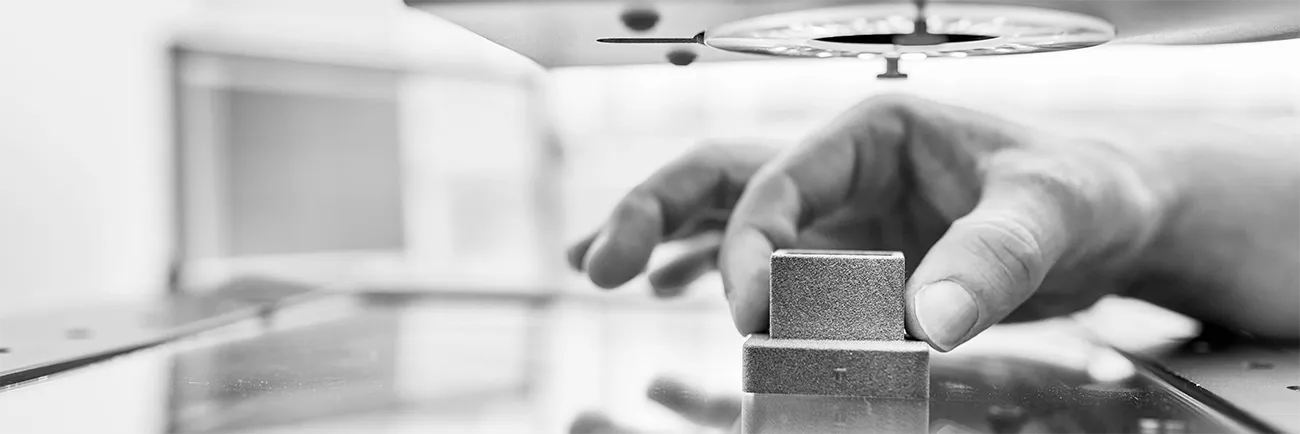
Multi Jet Fusion
Polyamid 12
± 0,3 % (min. ± 0,3mm)
Polyamid 12 W (weiß)
± 0,3 % (min. ± 0,3mm)
Polyamid 11
± 0,5 % (min. ± 0,5 mm)
TPU
±1,8 % (min. 1,5 mm) für grau
Mikro-3D-Druck
HTL
± 50 µm
Metall-3D-Druck
AlSi10Mg
ISO 2678-1-m
Stahl 1.4404
ISO 2678-1-m
Multi Jet Fusion
Wie funktioniert das 3D-Druck Verfahren?
Das Multi Jet Fusion (MJF) Verfahren ist ein 3D-Druckprozess, bei dem eine wärmeleitende Flüssigkeit (Fusing Agent) auf einen pulverförmigen Kunststoff, z.B Polyamid, an den Stellen aufgetragen wird, die verschmolzen werden sollen. Ein Infrarotstrahler erhitzt das Pulver, wobei die Flüssigkeit die Wärmeaufnahme an den markierten Stellen verstärkt und das Material dort verschmilzt. Der Prozess wiederholt sich Schicht für Schicht, bis das Bauteil vollständig aufgebaut ist.
Woraus ergeben sich Ungenauigkeiten?
Obwohl die Positioniergenauigkeit der Druckköpfe sehr hoch ist und maschinenbedingte Ungenauigkeiten daher kaum ins Gewicht fallen, gibt es einige verfahrensbedingte Faktoren, die zu Ungenauigkeiten führen können:
Schrumpfung
- Materialbedingt: Beim Schmelzen oder der Polymerisation des Kunststoffes kommt es zu einer Volumenverringerung des Materials, was zu Schrumpfungseffekten führt.
- Pulverbedingt: Das Ausgangsmaterial ist pulverförmig und weist eine geringere Dichte auf. Beim Schmelzen verringert sich das Volumen der Schicht, da das Pulver eine Dichte unter 100 % hat.
- Datenvorbereitung: Der Schrumpfungseffekt liegt in der Größenordnung von 3 %, variiert aber je nach Geometrie des Bauteils. Software zur Druckvorbereitung skaliert die Bauteile vor dem Druck etwas größer, um diesen Effekt auszugleichen. Da dies nicht immer perfekt funktioniert, kann es dennoch zu Ungenauigkeiten kommen.
Pulverauftrag
In einem vollständigen Bauraum werden fast 5.000 Schichten übereinander gedruckt. Da der Materialauftrag in der Höhe minimal schwankt, summieren sich diese kleinen Abweichungen über viele Schichten. Dies führt dazu, dass die Genauigkeit in der Z-Richtung geringer ist als in der X/Y-Ebene.
Thermisches Management
- Während des Drucks: Die Stellen, die verschmolzen werden, werden stärker erhitzt als das umliegende Pulver. Massive Bauteile geben mehr Wärme an die Umgebung ab, was den Schrumpfungsprozess umliegender Bauteile beeinflussen kann. Filigranere Strukturen hingegen heizen sich weniger stark auf, was zu variierenden Schrumpfungsprozessen führt.
- Abkühlung: Ein Druckvorgang umfasst in der Regel etwa 200 Bauteile, die vollständig von ungeschmolzenem Pulver umgeben sind. Während des Abkühlens geben die Bauteile Wärme an das umliegende Pulver ab, was die Abkühlgeschwindigkeit beeinflusst. Da die Schrumpfung von der Abkühlgeschwindigkeit abhängt, können sich auch hier Unterschiede im Endergebnis ergeben.
Kann man die Genauigkeit beeinflussen?
Ja, die Genauigkeit lässt sich bis zu einem gewissen Grad verbessern, aber nicht vollständig. Neben allgemeinen Maßnahmen wie regelmäßiger Wartung, Sauberkeit und optimal kalibrierten Maschinen liegt der Fokus vor allem auf dem thermischen Management.
Um die thermischen Effekte während des Druckens zu verbessern, optimieren wir vor allem die Anordnung der Bauteile im Bauraum. Dabei achten wir darauf, welche Bauteile kombiniert und wo sie platziert werden sowie auf ihre Ausrichtung. Da wir täglich mehrere hundert bis tausend Bauteile drucken, können wir die Anordnung im Bauraum perfekt anpassen.
Nach dem Druck lassen wir die Bauteile unter kontrollierten Bedingungen langsam auf Raumtemperatur abkühlen, was etwa zwei Tage dauert. Wir verzichten bewusst auf Schnellkühlung, da dies die Qualität beeinträchtigen könnte. Sowohl der Druckprozess als auch die Abkühlung erfolgen bei uns immer unter konstanten Bedingungen hinsichtlich Temperatur und Luftfeuchtigkeit, was die Qualität weiter verbessert.
Was sind minimal mögliche Toleranzen?
Standardmäßig garantieren wir eine Toleranz von ± 0,3 mm oder ± 0,3 % bei Bauteilen über 100 mm. Mit einer optionalen 100% Kontrolle (gegen Aufpreis) können wir Toleranzen von +/- 0,2 mm bzw. ± 0,2 % ab 100 mm sicherstellen.
Welchen Einfluss haben Nachbearbeitungsoptionen auf die Toleranz?
Der Einfluss der Nachbearbeitung auf die Bauteilgenauigkeit hängt stark von der Geometrie des Bauteils ab. Bei Oberflächenbearbeitungen wie Shot Peening, Gleitschliff und chemischer Glättung kommt es in geringem Umfang zu Volumenreduzierungen – entweder durch Verdichtung oder durch Materialabtragung. Diese Änderungen sind jedoch in der Regel so gering, dass sie im Rahmen der allgemeinen Toleranz vernachlässigbar sind.
Beim Gleitschliff, und in gewissem Maße auch beim Vapor Smoothing (Chemischer Glättung), kann es jedoch zu Kantenabrundungen kommen, was bei Bauteilen mit scharfen Kanten zu beachten ist.
Der Färbeprozess hat normalerweise keinen Einfluss auf die Toleranz. Eine Ausnahme bildet jedoch TPU, da dieses Material beim Färben stark aufquillt und je nach Geometrie um mehrere Zehntel Millimeter anwachsen kann.
Flache und großflächige Bauteile, die anfällig für Verzug sind, stellen eine allgemeine Ausnahme dar. Tatsächlich können fast alle Nachbearbeitungsschritte den Verzug solcher Bauteile verstärken.
Mikro-3D-Druck (PµSL)
Wie funktioniert das 3D-Druck Verfahren?
Das Projection Micro Stereolithography (PµSL) Verfahren ist ein 3D-Druckprozess, bei dem flüssige Photopolymere durch eine Projektion von UV-Licht in extrem feinen Schichten ausgehärtet werden. Dabei wird ein digitales Bild (Maskenprojektion) auf eine lichtempfindliche Flüssigkeit projiziert, die an den belichteten Stellen sofort aushärtet. Dieser Prozess erfolgt Schicht für Schicht mit extrem hoher Präzision und erlaubt die Herstellung sehr detaillierter Mikrostrukturen. Die Schichtdicken können dabei oft im Bereich von wenigen Mikrometern liegen, wodurch PµSL Bauteile mit extrem feinen Strukturen und hoher Oberflächenqualität ermöglicht.
Woraus ergeben sich Ungenauigkeiten?
Trotz der sehr hohen Präzision des PµSL-Verfahrens gibt es einige Faktoren, die zu Ungenauigkeiten führen können:
Schrumpfung
- Materialbedingt: Bei der Aushärtung der Photopolymere kann es zu einer gewissen Schrumpfung kommen, da das flüssige Material während des Polymerisationsprozesses an Volumen verliert. Dieser Effekt variiert je nach verwendetem Harz und kann zu Maßabweichungen führen.
- Datenvorbereitung: Der Schrumpfungseffekt liegt in der Regel unter 1 %, variiert jedoch je nach Bauteilgeometrie und Material. Eine Software zur Druckvorbereitung kann diesen Effekt durch Vergrößerung des Bauteils vor dem Druck teilweise ausgleichen, aber kleine Ungenauigkeiten bleiben möglich.
Optische Verzerrungen
- Da das PµSL-Verfahren auf der Projektion von Licht basiert, kann es bei suboptimaler Kalibrierung der Projektionssysteme zu optischen Verzerrungen kommen, was sich auf die Genauigkeit der projizierten Schichten auswirkt. Besonders bei sehr feinen Strukturen kann dies zu Maßabweichungen führen.
Schichtbildung
- Beim Aufbau der Schichten besteht die Herausforderung darin, die Schichtdicke und den Belichtungsgrad präzise zu kontrollieren. Geringfügige Abweichungen in der Schichtdicke können sich über viele Schichten hinweg summieren und zu Ungenauigkeiten in der Z-Richtung (vertikale Achse) führen.
Kann man die Genauigkeit beeinflussen?
Ja, die Genauigkeit lässt sich durch verschiedene Maßnahmen beeinflussen. Neben der Verwendung von hochwertigen Materialien und präzise kalibrierten Maschinen spielen auch die Prozessparameter eine entscheidende Rolle:
- Belichtungszeit: Die Dauer der Belichtung beeinflusst die Aushärtung des Photopolymers. Zu lange Belichtungszeiten können zu einer Überhärtung und leichten Überdimensionierung der Schichten führen, während zu kurze Belichtungszeiten eine unvollständige Aushärtung bewirken und die Maßhaltigkeit beeinträchtigen können.
- Schichtdicke: Dünnere Schichten erhöhen die Präzision, da der Treppenstufeneffekt reduziert wird. Das Einstellen sehr dünner Schichten verlängert jedoch die Druckzeit erheblich. Bei dickeren Schichten kann die Detailgenauigkeit abnehmen.
- Optische Systeme: Eine optimale Kalibrierung der optischen Systeme (Projektor und Linsen) ist entscheidend, um Verzerrungen und Unschärfen zu minimieren. Regelmäßige Kalibrierung sorgt dafür, dass die projizierten Bilder exakt sind und keine geometrischen Verformungen entstehen.
- Bauraumaufteilung: Die Platzierung der Bauteile im Bauraum kann sich ebenfalls auf die Genauigkeit auswirken. Eine gleichmäßige Verteilung sorgt für bessere Kontrolle der Aushärtung und verhindert thermische oder mechanische Verzerrungen.
Was sind minimal mögliche Toleranzen?
Standardmäßig garantieren wir eine Toleranz von ± 50 µm für kleine Bauteile. Engere Toleranzen, bis zu ± 25 µm, können erreicht werden, wenn optimierte Prozessparameter verwendet werden. Besonders feine Strukturen und Mikrobauteile profitieren von diesen extrem engen Toleranzen, die im Bereich von Mikrometern liegen und eine sehr hohe Maßgenauigkeit ermöglichen.
Welchen Einfluss haben Nachbearbeitungsoptionen auf die Toleranz?
Für das PµSL-Verfahren beschränken sich die Nachbearbeitungsoptionen im Wesentlichen auf Reinigung und Nachhärtung. Nach dem Druck werden die Bauteile gereinigt, um überschüssiges, nicht ausgehärtetes Harz zu entfernen. Anschließend erfolgt eine Nachhärtung unter UV-Licht, um die mechanischen Eigenschaften des Bauteils zu verbessern und die vollständige Aushärtung des Materials sicherzustellen. Diese Schritte haben in der Regel keinen signifikanten Einfluss auf die Toleranz, solange sie unter kontrollierten Bedingungen durchgeführt werden. Die Maßgenauigkeit bleibt nach der Reinigung und Nachhärtung erhalten, und das Bauteil behält die ursprünglich beim Druck erreichte Präzision.
Metall 3D-Druck (Selektives Laserschmelzen)
Wie funktioniert das 3D-Druck Verfahren?
Das Laserschmelzen (Selective Laser Melting, SLM, oder Direct Metal Laser Sintering, DMLS) ist ein 3D-Druckverfahren, bei dem ein hochenergetischer Laser pulverförmiges Metall Schicht für Schicht verschmilzt, um Bauteile herzustellen. Der Laser fährt die Konturen des Bauteils präzise ab und schmilzt das Metallpulver lokal auf, wodurch es zu einem festen Teil erstarrt. Dieser Prozess wiederholt sich, bis das Bauteil vollständig aufgebaut ist.
Woraus ergeben sich Ungenauigkeiten?
Obwohl der Laserschmelzprozess sehr präzise ist, gibt es mehrere verfahrensbedingte Faktoren, die zu Ungenauigkeiten führen können:
Schrumpfung
- Materialbedingt: Beim Laserschmelzen von Metallen treten starke thermische Effekte auf. Das geschmolzene Metall schrumpft beim Erstarren, da es beim Übergang vom flüssigen in den festen Zustand Volumen verliert. Diese Schrumpfung ist schwer vorherzusagen und kann zu Maßabweichungen führen.
- Verzug: Da hohe Temperaturen im Spiel sind und Metall ungleichmäßig abkühlt, können sich innere Spannungen im Bauteil aufbauen. Diese Spannungen führen oft zu Verzug, insbesondere bei größeren Bauteilen oder komplexen Geometrien.
- Thermische Ausdehnung: Während des Drucks dehnen sich die erhitzten Bereiche aus und ziehen sich beim Abkühlen wieder zusammen. Dies kann lokale Verformungen verursachen.
- Pulverauftrag: Da in einem vollständigen Bauraum Hunderte von Schichten aufgetragen werden, kann es zu minimalen Schwankungen in der Pulververteilung kommen. Diese kleinen Abweichungen können sich über viele Schichten summieren und zu Toleranzabweichungen führen, insbesondere in der Z-Richtung (vertikale Achse).
Thermisches Management
- Wärmeleitung und Spannungen: Beim Laserschmelzen wird das Metallpulver sehr hohen Temperaturen ausgesetzt, wodurch erhebliche Wärmeleitungs- und Spannungsprobleme auftreten. Wenn der Wärmeabfluss nicht gleichmäßig erfolgt, können sich Spannungen im Bauteil aufbauen, was zu Rissen oder Verzerrungen führen kann.
- Überhitzung und Kühlung: Massive Bauteile speichern mehr Wärme und kühlen langsamer ab, was die Schrumpfung und Spannungen beeinflusst. Filigranere Strukturen können hingegen schneller abkühlen, was ebenfalls zu Ungleichmäßigkeiten führt. Ein langsamer Abkühlprozess nach dem Druck kann Spannungen minimieren, ist aber zeitaufwändig.
Kann man die Genauigkeit beeinflussen?
Ja, die Genauigkeit lässt sich bis zu einem gewissen Grad verbessern, aber nicht vollständig eliminieren. Neben dem thermischem Management spielen auch die Prozessparameter eine wichtige Rolle.
Zu den wesentlichen Prozessparametern, die die Genauigkeit beeinflussen, gehören:
- Laserleistung: Eine höhere Laserleistung kann die Schmelztiefe vergrößern, aber auch zu Überhitzung und Verzug führen. Eine zu niedrige Laserleistung kann hingegen zu unzureichender Verschmelzung und Porosität im Bauteil führen.
- Scan-Geschwindigkeit: Die Geschwindigkeit, mit der der Laser über das Pulver fährt, beeinflusst direkt, wie viel Material aufgeschmolzen wird. Zu hohe Geschwindigkeiten können zu unvollständigem Schmelzen führen, während zu langsame Geschwindigkeiten zu übermäßigem Aufschmelzen und Verzug führen können.
- Schichtdicke: Dünnere Schichten bieten mehr Kontrolle über die Genauigkeit und reduzieren Treppenstufeneffekte. Allerdings führt dies zu längeren Druckzeiten. Dickere Schichten können den Druckprozess beschleunigen, aber die Präzision verringern.
- Spotgröße des Lasers: Die Größe des Laserpunkts beeinflusst, wie fein die Details im Druck erfasst werden können. Eine kleinere Spotgröße sorgt für höhere Präzision, kann aber auch die Prozessdauer verlängern.
- Bauraumtemperatur: Eine höhere Temperatur im Bauraum kann thermische Spannungen während des Drucks reduzieren und so die Maßhaltigkeit verbessern. Ein zu kalter Bauraum hingegen kann das Risiko von Verzug erhöhen.
- Schweißstrategie: Die Art und Weise, wie der Laser das Material schmilzt (z.B. linear, schachbrettartig oder spiralförmig), beeinflusst, wie sich die Wärme im Bauteil verteilt. Eine optimierte Schweißstrategie kann helfen, thermische Spannungen und Verzug zu minimieren.
Zusätzlich zur Feinabstimmung dieser Parameter können Nachbearbeitungsschritte wie Wärmebehandlung oder Heißisostatisches Pressen (HIP) helfen, Spannungen abzubauen und die Maßgenauigkeit zu verbessern. Auch eine optimierte Bauteilanordnung im Bauraum trägt zur Reduzierung thermischer Einflüsse bei, indem Wärmeableitung und Abkühlung gleichmäßiger erfolgen.
Was sind minimal mögliche Toleranzen?
Unsere allgemeinen Toleranzen richten sich nach dem Standard ISO 2768-1-m (mittlere Toleranzklasse), was in der Regel Toleranzen von ± 0,1 mm bis ± 0,2 mm für kleinere Bauteile und bis zu ± 0,5 % der Nennlänge bei größeren Bauteilen bedeutet. Engere Toleranzen können durch nachträgliche maschinelle Bearbeitung (CNC-Fräsen) erreicht werden, wodurch Genauigkeiten von ± 0,05 mm oder besser erzielt werden können, abhängig von der Bauteilgeometrie und dem verwendeten Material.
Welchen Einfluss haben Nachbearbeitungsoptionen auf die Toleranz?
Der Einfluss der Nachbearbeitung auf die Bauteilgenauigkeit hängt stark von der Geometrie und den Materialien ab. Mechanische Nachbearbeitungen wie CNC-Fräsen oder Schleifen können dazu beitragen, die Maßgenauigkeit zu erhöhen, indem sie überschüssiges Material abtragen und Oberflächen glätten. Diese Nachbearbeitung hat jedoch ihre Grenzen, besonders bei komplexen Geometrien.
Thermische Nachbearbeitungen wie Wärmebehandlung oder Heißisostatisches Pressen (HIP) tragen dazu bei, die inneren Spannungen im Material abzubauen und die Dichte zu erhöhen. Diese Verfahren verbessern die Qualität und Festigkeit des Bauteils, beeinflussen jedoch die endgültigen Maße nur geringfügig.
Besonders bei großen und flachen Bauteilen, die anfällig für Verzug sind, können thermische Nachbehandlungen helfen, Verzug zu reduzieren. Allerdings können auch hier Nachbearbeitungsschritte den Verzug weiter verstärken, wenn sie nicht sorgfältig kontrolliert werden.
Allgemeine Hinweise zur Verbesserung der Genauigkeit
Datenkonvertierung
Um für den 3D-Druck verwendet werden zu können, muss das Modell in einer STL-Datei vorliegen. Diese wird aus einer CAD-Datei, üblicherweise im STP-Format (STEP), exportiert oder umgewandelt. Bei der Umwandlung von STP in STL entstehen nur minimale Ungenauigkeiten im Hundertstelmillimeterbereich. Ein wichtiger Faktor bei dieser Umwandlung ist jedoch die Oberflächenqualität. Besonders bei hochpräzisen Verfahren wie dem Mikro-3D-Druck kann eine unzureichende Auflösung die feinen Details und die Oberflächengenauigkeit negativ beeinflussen.
Das Problem liegt in der Art und Weise, wie die Oberflächenkonvertierung stattfindet. Das STP-Format verwendet glatte Oberflächen, während das STL-Format diese in ein Mesh (Netz aus Dreiecken) umwandelt. Dieser Prozess erfordert eine Vereinfachung der Oberfläche, die stark von der gewählten Mesh-Auflösung abhängt:
- Geringere Auflösung führt zu größeren Abweichungen von der ursprünglichen Geometrie, da größere Dreiecke verwendet werden, was die Oberflächenqualität beeinträchtigen kann.
- Höhere Auflösung führt zu einer genaueren Darstellung, jedoch steigt dabei auch die Dateigröße erheblich an. Zu große Dateien können schwer oder gar nicht verarbeitet werden.
Wenn Sie sich unsicher sind, welche Auflösung Sie wählen sollen, können Sie uns einfach die STP-Datei zusenden. Wir wählen dann die technisch maximal mögliche Auflösung, die für den Druckprozess geeignet ist.
Datei Größe: 0,01 MB
Datei Größe: 0,03 MB
Datei Größe: 0,5 MB
Datei Größe: 3,7 MB
Beachtung von Konstruktionsrichtlinien
Um die Genauigkeit und Qualität beim 3D-Druck zu maximieren, ist es wichtig, dass die Konstruktion auf das jeweilige Verfahren abgestimmt ist. Jedes 3D-Druckverfahren hat spezifische Anforderungen und Einschränkungen, die bereits in der Konstruktionsphase berücksichtigt werden sollten. Optimierte Geometrien, die auf das Druckverfahren abgestimmt sind, reduzieren Spannungen, Verzug und Maßabweichungen.
Beispiele hierfür sind:
- Wandstärken: Gleichmäßige und ausreichend dimensionierte Wandstärken helfen, Verzerrungen zu minimieren.
- Überhänge und Stützstrukturen: Bei bestimmten Verfahren (z. B. SLM) müssen Überhänge und komplexe Geometrien durch Stützstrukturen gesichert werden, um Verzug und Verformungen zu verhindern.
- Toleranzen und Passungen: Passungen zwischen Bauteilen sollten so ausgelegt werden, dass sie den Drucktoleranzen des Verfahrens entsprechen, um eine präzise Montage zu ermöglichen.
Eine frühzeitige Optimierung der Konstruktion kann dazu beitragen, die Maßgenauigkeit zu verbessern und Nacharbeit zu minimieren.
Mehr Informationen: umfangreiche Übersicht zu Konstruktionshinweise für das Multi Jet Fusion Verfahren.