Wann lohnt sich welches Verfahren?
Die additiven Fertigungsverfahren haben sich in den vergangenen Jahren rasant weiterentwickelt. Die Preise sind aufgrund größerer Verbreitung und technischer Reifung rapide gesunken und die Technologien sind insgesamt ausgereifter geworden. Was ist besser geworden? Die Toleranzen wurden signifikant reduziert und die Oberflächen wurden glatter und beständiger. Natürlich sind mit steigender Reife der Technologie und der wachsenden Erfahrung der jungen Unternehmer auch die Kosten gesunken, die Herstellungszeiten reduziert worden und die werden Prozesse insgesamt effizienter gestaltet. Darüber hinaus konnten die Materialpreise und die Preise für die Anlagen reduziert werden. Auch bei der Steuerungssoftware wurden Fortschritte gemacht. 3D-Druck oder Spritzguss? Ob die Fortschritte der 3D-Drucktechnologie reichen, um sich gegen das etablierte Spritzgussverfahren durchzusetzen, wollen wir in diesem Artikel besprechen.
Wenn Sie hohe Stückzahlen von Kunststoffobjekten produzieren möchten (>2.000 Stück), dann führt in aller Regel kein Weg am Spritzgussverfahren vorbei. Der große Vorteil von Spritzguss bei diesen hohen Stückzahlen sind die niedrigeren Kosten, die besseren Oberflächen und die grundsätzlich höhere Auswahl an Materialien. Abhängig von den gewünschten Eigenschaften der Objekte kann das Spritzgussverfahren schon im Bereich von 300-500 Stück seinen Kostenvorteil ausspielen.
Fallbeispiele: Ab welcher Stückzahl ist Spritzguss günstiger?
Die hier abgebildeten Teile (aus dem Automobilbereich) sollen in größerer Stückzahl produziert werden. Dazu wurden von uns die Option Lasersintern mit Spritzguss (Material ABS) verglichen. Um eine gute Vergleichbarkeit herzustellen, wurde für das Spritzgussverfahren eine niedrige Oberflächenqualität angefordert. Die Mittelwerte zweier Fremdanbieter verglichen mit den Lasersinter-Preisen finden Sie jeweils links aufgeführt.
Im nächsten Abschnitt erläutern wir, welche Faktoren Sie bei der Auswahl des für Ihr Projekt geeigneten Verfahrens beachten sollten.
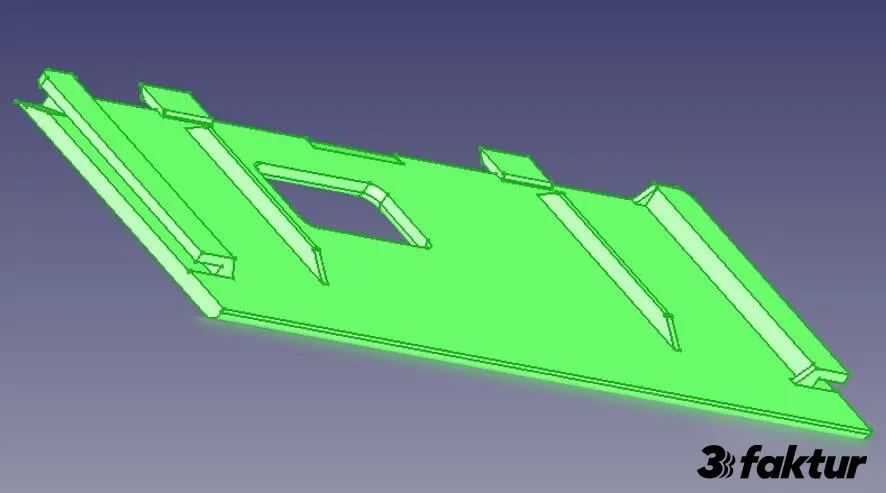
Abdeckung; 129,5 x 52,6 x 5,6 mm. Ein Extrembeispiel, die Geometrie und Größe macht das Teil perfekt für das Lasersintern. In den meisten anderen Fällen lohnt sich spätestens ab 1.000 Stück ökonomisch das Spritzgussverfahren.
Mitnehmer; 43,9 x 18,0 x 20,2 mm
Zahnrad; 15,5 x 15,5 x 6,1 mm
Für unsere Vergleichsstudie wurde der Mittelwert aus zwei Angeboten von Fremddienstleistern gebildet (Spritzguss ABS mit geringer Oberflächenqualität). Bei den SLS-Preisen (PA2200) handelt es um unsere eigenen Preise. Die Y-Achse der Diagramme entspricht den Stückpreisen in EUR, die X-Achse stellt die Stückzahl dar.
Welche Faktoren spielen bei der Entscheidung eine Rolle?
Dieser Kostenvorteil kann sich unter bestimmten Bedingungen zugunsten des Lasersinterverfahrens verschieben. Wenn Sie planen kleinere Stückzahlen zu produzieren also eine Testserie oder Kleinserie, dann sollten Sie folgende Überlegungen beachten.
- Welche Materialeigenschaften wollen Sie erreichen?
- Wie sollen die Oberflächen beschaffen sein?
- Welche Toleranzen sind vertretbar?
- In welchen Stückzahlen soll produziert werden?
- Welche Ausmaße hat das Werkstück?
- Sollen an dem Werkstück noch Veränderungen möglich sein?
- Welchen Zeitrahmen haben Sie für die Herstellung der Objekte?
Von den Antworten auf die o.g. Fragen hängt ab, ob das Lasersinterverfahren oder das Spritzgussverfahren für Ihr Projekt optimal ist.
Materialoptionen
Für die meisten Kleinserien im 3D-Druck wird das Lasersintern (SLS) oder neuerdings auch das HP Jet Fusion Verfahren eingesetzt. Bei beiden Verfahren hat sich das Material PA12 als Standardmaterial durchgesetzt. PA12 wird aber auch bei Spritzgussverfahren verwendet. Gesintertes PA12 (PA2200) ist etwas poröser und leichter (Dichte 0,9 – 0,95 g/cm³) als das Spritzguss-PA12 nach der Produktion. PA 12 vom Jet Fusion Verfahren hat ähnliche Dichten wie im Spritzguss.
Es gibt auch noch weitere Materialien für das Lasersintern, sogenannte PA12 Compunds. Das sind Mischungen von PA12 mit anderen Materialien, um bestimmte Eigenschaften zu erhalten (Glasfasern für erhöhte thermische Belastbarkeit; Aluminde für Metalloptik und Steifigkeit). Das Material TPU 92 wiederum ist ein thermoplastisches Elastomer auf Urethanbasis. Aber für diese Materialien sind die Kosten häufig höher als für das Standardmaterial PA12.
Durch die Art der Fertigung beim Lasersintern sind die Produkte leicht anisotrop. Das bedeutet, dass die Werkstücke auf der X/Y-Achse widerstandsfähiger sind, als entlang der Z-Achse. Da dies die Dimension ist, an der das Objekt aufgebaut wird und sich die Schichten in dieser Dimension leichter wieder voneinander lösen können. Beim Spritzgussverfahren ist dieser Effekt nicht vorhanden. Dort sind die Objekte in allen Dimensionen gleich stabil.
Eine Alternative zu SLS (in der Kleinserienfertigung) stellt die Stereolithografie (SLA) dar, allerdings gilt dies nur für relativ kleine Objekte, aufgrund der hohen Kosten des Verfahrens. SLA Teile weisen eine glattere Oberfläche auf, sind jedoch relativ wärmeempfindlich.
Beim Spritzgussverfahren steht Ihnen eine große Vielfalt an Materialien mit verschiedenen Eigenschaften zur Verfügung. Dabei können unterschiedliche physikalische Eigenschaften erreicht werden, die dann Spezialanforderungen erfüllen können (Brandschutz, chemische Resistenzen, Lebensmittelechtheit). Durch die Zugabe von Pigmenten oder Masterbatches können Sie die Farbe Ihres Objektes frei definieren.
Zusammenfassung: Wenn die Eigenschaften von gesintertem PA12 (PA2200) Ihre Projektanforderungen erfüllen, dann ist SLS für Ihre Kleinserie eine Option, andernfalls sollte schon bei geringen Stückzahlen Spritzguss in Betracht gezogen werden.
Oberflächen
Beim Lasersintern werden feine Pulverkörner des Ausgangsmaterials thermisch miteinander verbunden (gesintert). Verfahrensbedingt sind die produzierten Werkstücke leicht porös und die Oberflächen sind ohne Nachbearbeitung etwas rau. Mithilfe von teilautomatisierten Nachbearbeitungsverfahren können die Oberflächen etwas geglättet werden. Dabei werden aber nicht die Ra-Werte (Mittelrauwert), des Spritzgusses erreicht. Wie oben beschrieben, bietet sich für glattere Oberflächen auch das SLA-Verfahren an, allerdings mit den genannten Nachteilen (geringe Belastbarkeit, höhere Kosten).
Abhängig von den Anforderungen können mit dem Spritzgussverfahren sehr gute Oberflächeneigenschaften erreicht werden.
Zusammenfassung: Bei sehr hohen Oberflächenansprüchen für Kleinserien ist das Lasersintern nicht die erste Wahl. Stereolithografie ist für kleine, nicht stark beanspruchte Werkstücke oder kleinere Stückzahlen (~100) eine Alternative.
Toleranzen
Das Lasersintern weißt eine verfahrensbedingte Toleranz von ca. +/- 300 µm bzw. +/- 0,3 % auf. Aber diese Toleranzen hängen stark von den zu druckenden Objekten ab und können z.B. durch eine geschickte Ausrichtung des Objekts im Drucker beeinflusst werden.
Auch beim Spritzgussverfahren gibt es Toleranzen, diese können aber von erfahrenen Formenbauern in einem Bereich von 100 µm gehalten werden.
Zusammenfassung: Bei sehr hohen Toleranzanforderungen sollte auch bei kleineren Stückzahlen das Spritzgussverfahren bzw. andere 3D-Druckverfahren (bspw. Stereolithografie oder Polyjet) gewählt werden.
Stückzahlen
Erfahrungsbedingt hat sich eine Art Faustregel etabliert: Ab einer Anzahl von 200 – 500 Stück ist das Spritzgussverfahren unter Kostengesichtspunkten das beste Verfahren. Auch bei großen oder geometrisch einfachen Werkstücken ist der Spritzguss lohnenswert. Bei kleinen oder komplexen Werkstücken lohnt sich das Lasersintern auch für relativ große Stückzahlen, da beim 3D-Druck die Auslastung des Bauraums eine entscheidende Rolle spielt. Verdoppelt man beispielsweise die Größe des Werkstücks, verachtfacht sich das, benötige Material bzw. das Bauvolumen. Daher sind die Preise für 3D-gedruckte Objekte stark volumenabhängig. Diese Regel spielt beim Spritzgussverfahren bei Objektgrößen bis ca. 25 cm weniger extreme Rolle.
Anders verhält es bei der geometrischen Komplexität, hier hat das Lasersintern große Stärken. Die Komplexität ist bei diesem Verfahren quasi „kostenlos“. Hinterschneidungen, Hohlräume oder Löcher sind ohne Probleme darstellbar und erzeugen keine zusätzlichen Kosten.
Beim Spritzguss führen diese Besonderheiten zu meist erheblichen Kostensteigerungen, da sogar zusätzliche Produktionsschritte notwendig werden können. Deshalb lohnt sich der Spritzguss erst bei höheren Stückzahlen als üblich.
Zusammenfassung: Bei kleinen oder komplexen Objekten ist das Lasersintern die beste Wahl. Erst bei relativ hohen Stückzahlen (>500) gewinnt das Spritzgussverfahren einen Kostenvorteil. Bei großen Teilen kann sich der Spritzguss schon bei relativ geringen Stückzahlen (>50) lohnen. Typische Anwendungsfälle sind Vorserien mit <100 Stück oder Kleinserien mit geringen Stückzahlen pro Jahr.
Größe/Komplexität des Werkstücks
Wie wir schon besprochen haben, ist die Größe/das Volumen es Werkstückes der wichtigste Kostentreiber in der additiven Fertigung. Darüber hinaus sind die Bauräume der Sinteranlagen in ihrer Größe limitiert. Die größten verfügbaren Sinteranlagen haben einen Bauraum von ca. 75 cm. Die gängigsten Anlagen haben allerdings nur einen Bauraum von etwa 50 cm. Bei voller Auslastung des Bauraums müssen Sie allerdings mit einer Druckzeit von 24 – 48h rechnen, d.h. solch große Objekte sind wenig praktikabel für die Kleinserienfertigung mit SLS. Bis zu einer Werkstückgröße von 25 cm sollten Sie SLS als Alternative für Ihre Kleinserie in Betracht ziehen.
Anders verhält es sich bei der Komplexität des Objektes. Durchlassungen, abstehende Teile, Hinterschneidungen, Hohlräume oder andere Bestandteile des Objektes erhöhen den Kosten in Spritzguss signifikant. Da es den Formenbau entscheidend komplexer macht und damit verteuert. Diese Komplexität gibt es beim 3D-Druck „kostenlos“, hier muss nur festgestellt werden, ob ein 3D-Modell „druckfähig“ ist und eventuell nachbearbeitet werden muss.
Zusammenfassung: Je größer ein Objekt ist (25 cm) desto eher ist Spritzguss zu empfehlen. Je komplexer Ihr Produkt ist, desto eher ist der 3D-Druck kostengünstiger.
Sollen Änderungen am Werkstück möglich sein?
Beim Verwenden von 3D-Drucktechnologien in der Fertigung können Sie jederzeit und problemlos das Design ändern, indem Sie das 3D-Modell bearbeiten.
Der Spritzguss bietet diese Möglichkeit nicht. Hier müssen Sie für jede Änderung eine neue Form herstellen.
Zusammenfassung: Wenn Sie sich die Möglichkeit der Bearbeitung Ihres Werkstückes in der Pilotphase/Testphase offen halten möchten, dann ist die additive Fertigung genau die richtige Technologie für Sie.
Zeithorizont
Hier ist die Entscheidung relativ einfach und eindeutig. Während für die Herstellung von Formen/Werkzeugen für den Spritzguss häufig mehrere Wochen oder gar Monate vergehen, können Sie bei der Verwendung des Lasersinterns schon innerhalb von 48h erste Werkstücke erhalten.
Fazit
Der 3D-Druck ist aller Regel wesentlich schneller als der Spritzguss. Da die zeitaufwendige Herstellung der Werkzeuge/Formen entfällt. Weiterhin sind kurzfristige Änderungen am Produkt (durch die Bearbeitung des 3D-Modells) ohne Probleme möglich. Sobald die Objekte größer werden oder die akzeptierte Toleranz geringer wird, ist das Spritzgussverfahren die bessere Option. Ab Stückzahlen von >1.000 ist der Spritzguss in der Regel das lohnendere Verfahren. Trotzdem, dass 3D-Druckmaterial PA12 vielseitig einstetzbar ist, beim Spritzguss haben Sie eine riesige Auswahl an zum Teil hochspezialisierten Materialien.
Der 3D-Druck lohnt sich also immer dann, wenn Sie relativ kleine Stückzahlen benötigen, an denen Sie eventuell noch etwas ändern möchten. Und das alles in sehr kurzer Zeit. Typische Anwendungsfälle wären also Testserien oder Vorserien eines Produktes. Auch für hochindividualisierte Serien ist der 3D-Druck eine gute Alternative zum Spritzgussverfahren. Weitere Anwendungsgebiete sind die Fertigung von spezialisierten medizinischen Geräten oder „versteckte“ Funktionsteile, bei denen es nicht auf die Oberflächenbeschaffenheit ankommt.
Die Frage ob Sie 3D-Druck oder Spritzguss wählen sollten, kann nicht immer eindeutig beantwortet werden. Mit dem obenstehenden Artikel haben Sie aber ein Werkzueg in der Hand, dass Ihnen die Entscheidung erleichtern kann.
Über 3Faktur: 3Faktur ist Spezialist für 3D-Druck, Rapid Prototyping und Rapid Manufacturing. Wir arbeiten mit dem Multi Jet Fusion-Verfahren von HP und bieten unterschiedliche Materialien für den Prototypenbau und die Serienproduktion an. Sollten Sie Fragen zu Ihrem Projekt haben, können Sie uns gern kontaktieren.