Projection Micro Stereolithography (PµSL) or Micro 3D Printing is an advanced manufacturing technology that enables the creation of highly precise microstructures in millimeter to a few centimeters scale in three-dimensional objects. Using a projection-based UV exposure process, thin layers of resin are cured, resulting in detailed and complex geometries. This micro 3D printing offers an excellent resolution of up to 10 µm and is used in fields such as microelectronics, medical technology, and microfluidics. Thanks to the high precision and flexibility of PµSL, innovative products and prototypes can be manufactured with exceptional accuracy and quality.
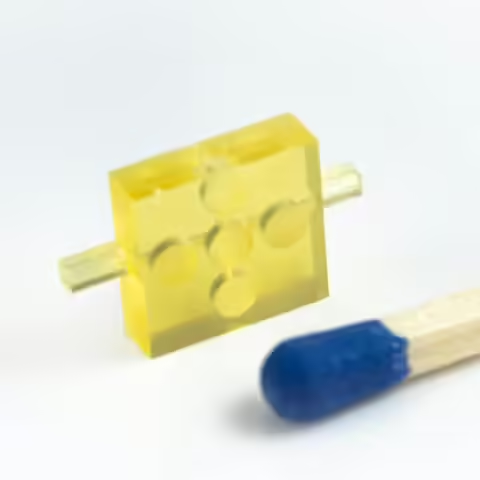
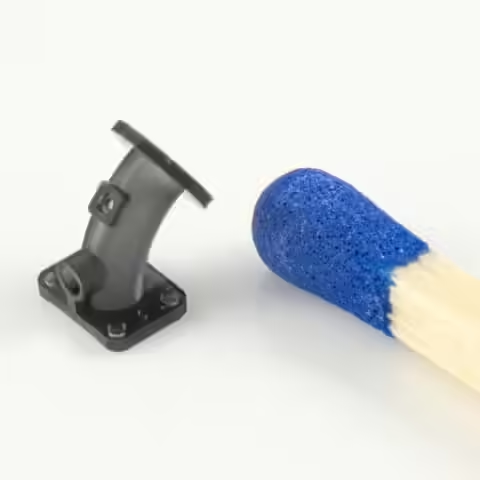
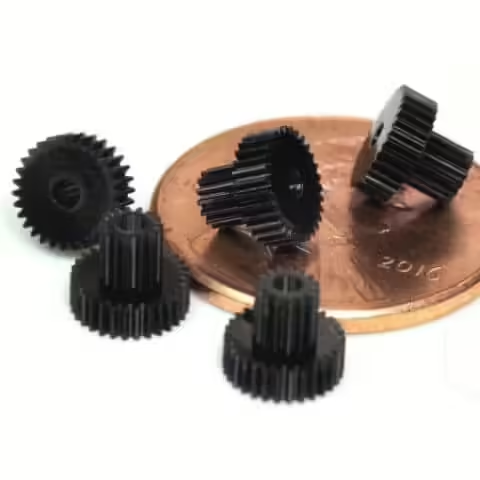
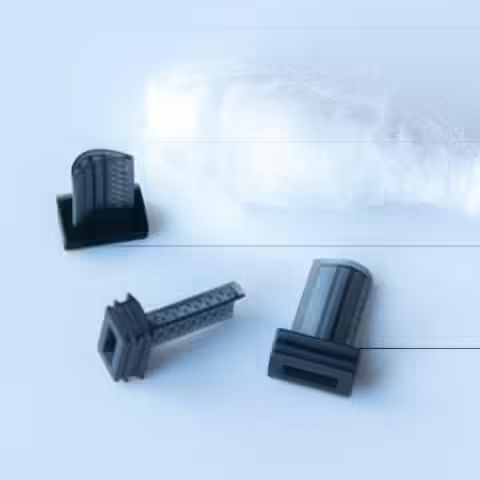
Key Information
Materials
HTL
Others on request
Colors
yellow translucent
black on request
Build Volume
100 x 100 x 50 mm
Production Time
Approx. 5 – 7 working days
Accuracy
+/- 25µm ~ +/- 50µm
The Micro 3D Printing Process PµSL
The printing process in Projection Micro Stereolithography (PµSL) begins with the creation of a digital 3D model that is divided into thin layers. A UV light projector gradually exposes these layers onto a liquid resin surface, curing the resin at the exposed areas. The unique feature of micro 3D printing PµSL is that the projector only illuminates a very small area. For larger parts (in the centimeter scale) or a large number of parts, the resin vat shifts so that the projector gradually illuminates the entire surface. Technologically, this is a masterpiece as the resin vat is moved with positioning accuracies in the nanometer range. The downside is that this extends the printing times, often taking several days.
After each layer, the platform is slightly lowered, and a new layer of liquid resin is applied. This process repeats until the entire object is built. Through precise control of UV light and layer thickness, complex and detailed microstructures can be produced with high accuracy and resolution.
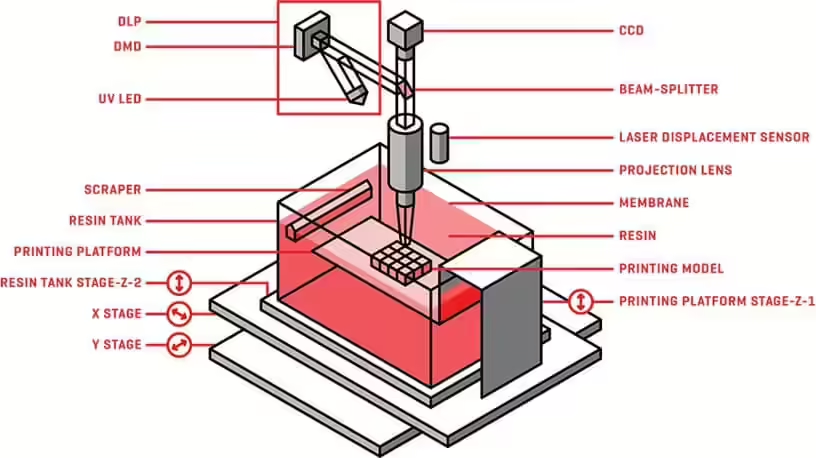
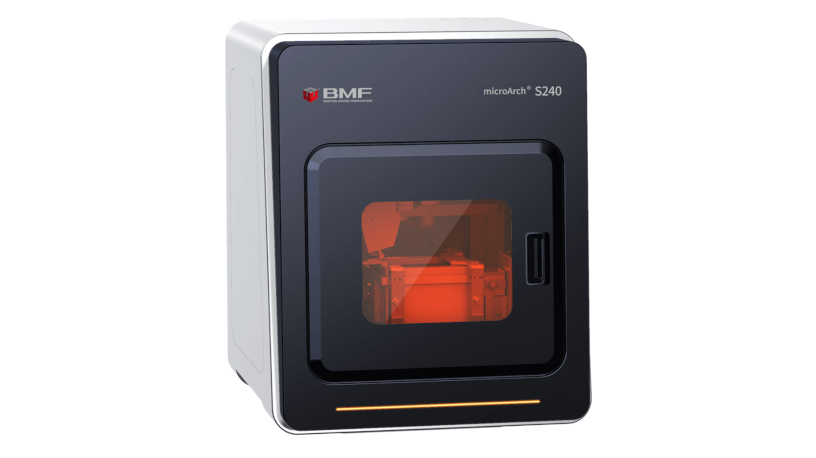
Process Chain
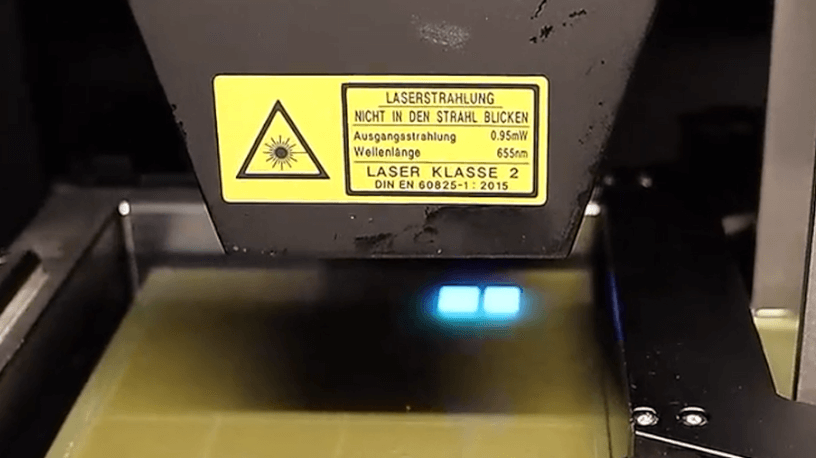
1 / Micro 3D Printing
3D printing typically takes half a day to a day, but for large or multiple parts, it can take several days. In this technology, parts larger than 10 mm already qualify as “large.”
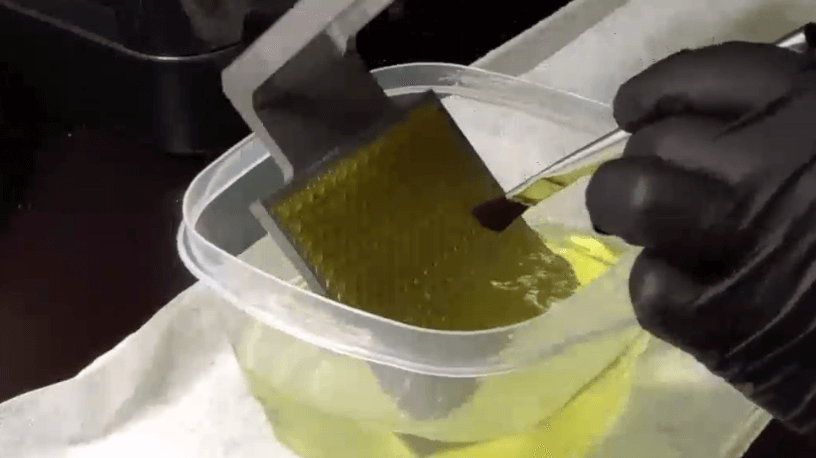
2 / Removing Excess Material
The remaining liquid, excess material is removed using a solvent.
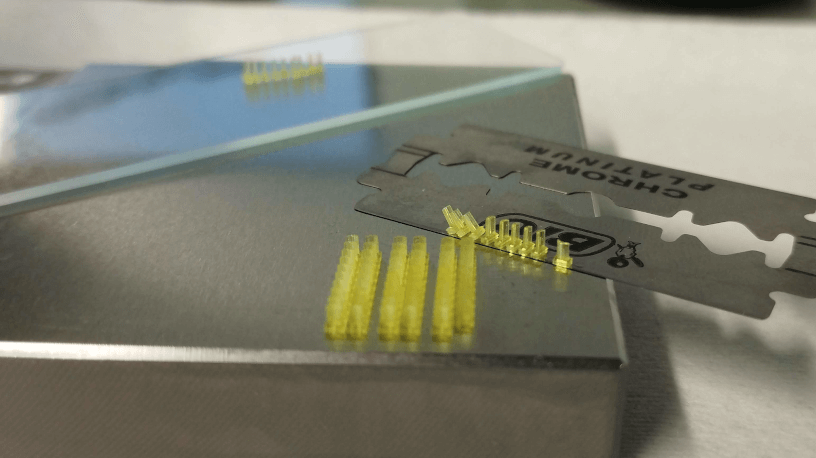
3 / Removing Parts from the Build Platform
The parts are separated and removed from the build platform using a sharp tool, such as a razor blade.
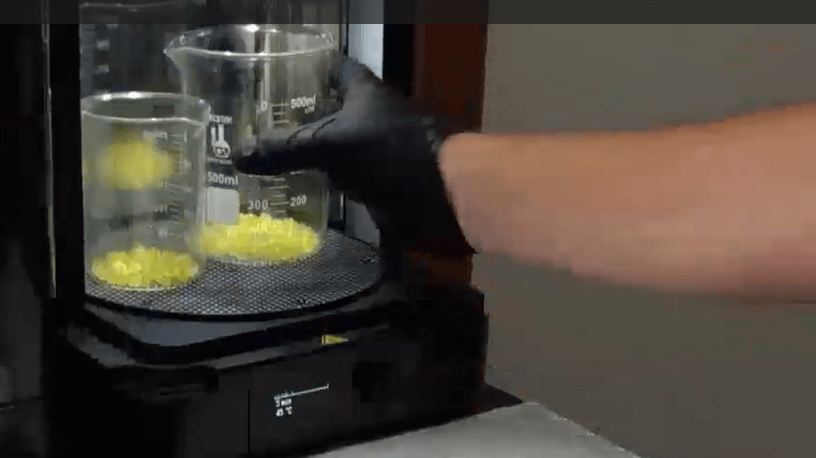
4 / Post-Curing
In the final step, the parts are cured once again in a UV chamber. This additional UV exposure ensures that the resin fully cures, improving the mechanical properties and stability of the part.
Materials for Micro 3D Printing
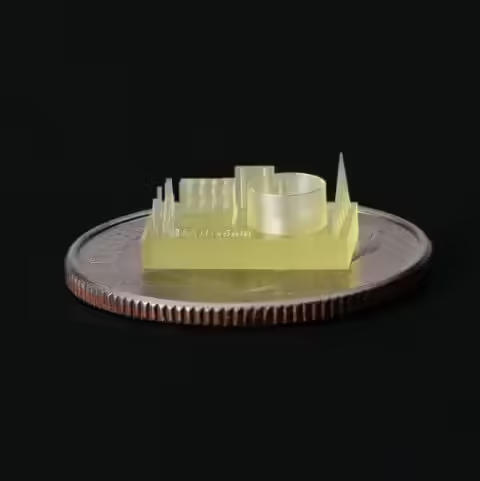
HTL
The innovative material HTL (High-Temperature Liquid) was developed by Boston Micro Fabrication specifically for use in Projection Micro Stereolithography (PµSL). It is characterized by its high-temperature resistance and excellent mechanical properties, making it ideal for applications in electronics, the automotive industry, and other fields that require robust and durable micro-components. HTL enables the production of precise and detailed structures that reliably function even under extreme conditions.
Post-Processing
Due to the tiny size of the parts and the already very low roughness values of sometimes < 1 µm (Ra) after printing, surface treatments are not carried out.
Applications
Micro 3D printing PµSL is suitable for miniaturized components as well as parts with very high accuracy requirements. The process works with a liquid raw material, allowing the production of internal channels with very small diameters (depending on the geometry, up to 50 µm).
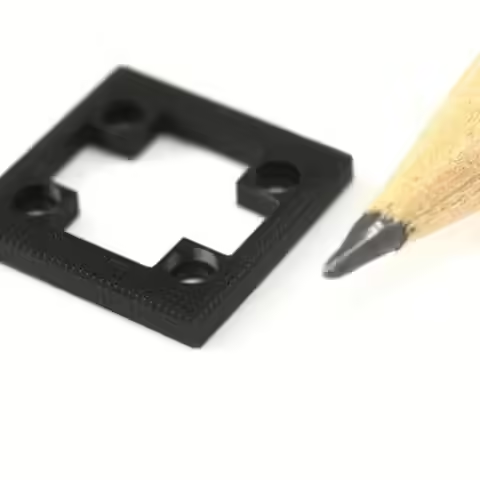
Electronics
Micro 3D printing PµSL enables the production of small electronic components such as connectors and chip sockets with the necessary thermal and mechanical stability required for demanding applications like 5G. Additionally, PµSL supports the miniaturization of electronics without compromising speed, precision, and surface quality.
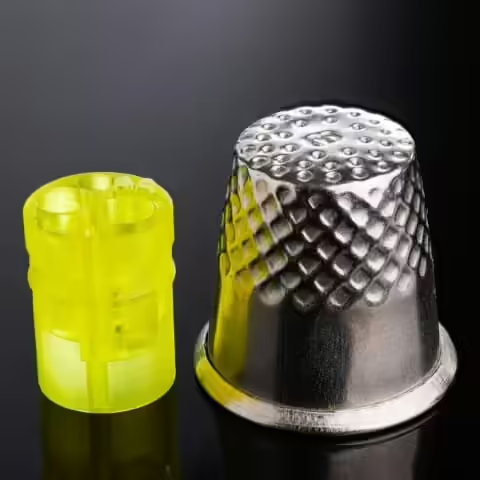
Medical Components
Projection Micro Stereolithography (PµSL) enables the production of small, high-precision parts that are critical for modern medical devices. This technology can print biocompatible plastics with a resolution of 10 µm and accuracy of up to +/- 25 µm, for example, for applications such as endoscope tips, cardiovascular stents, and spiral needles for minimally invasive surgery. PµSL also reduces the number of required components and assembly steps, resulting in shorter production times and increased design flexibility.
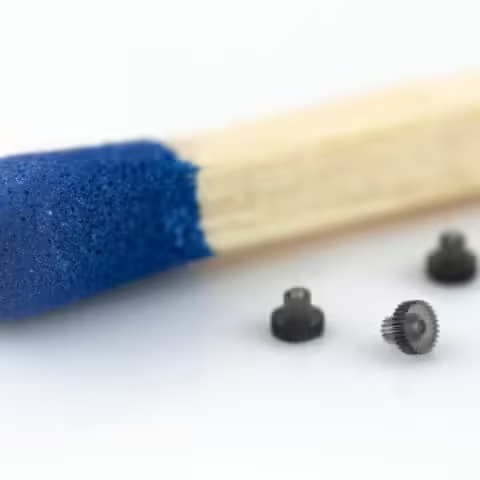
Micro-Electro-Mechanical Systems (MEMS)
Micro 3D printing supports the production of small mechanical parts such as switches, gears, sensors, motors, and valves required in MEMS applications. A key advantage of PµSL is the ability to print internal structures and fine details that are difficult to achieve with traditional micro-injection molding or CNC machining. Additionally, PµSL reduces the need for expensive tooling and speeds up the prototyping process. This shortens development cycles and reduces costs.
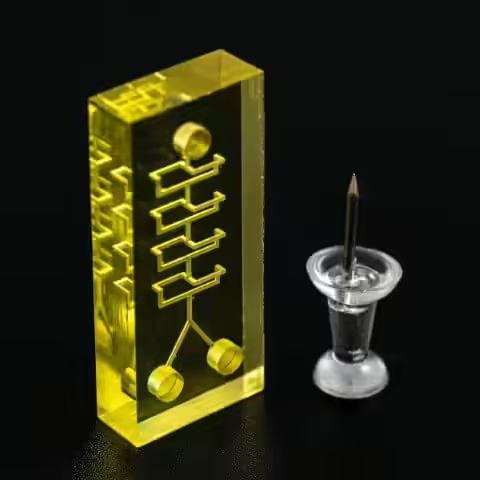
Microfluidics
This technology can print microchannels with diameters as small as 50 micrometers and high aspect ratios, making it crucial for the precise handling of extremely small liquid volumes. PµSL offers fast processing and excellent surface quality, significantly facilitating the production of lab-on-a-chip (LOC) devices and other microfluidic applications. Additionally, PµSL supports biocompatible and high-temperature resistant materials required for use in biomedicine and diagnostics.
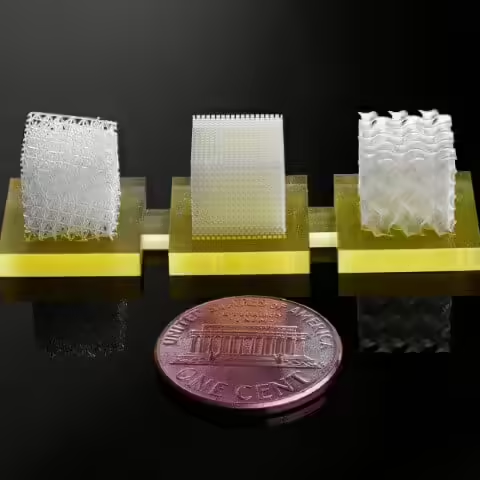
Research & Development
PµSL enables the production of microscopically small, high-precision components. PµSL technology offers a resolution of 10 µm and accuracy of +/- 25 µm, which is critical for the development and research of new materials and devices. This technology reduces the need for expensive tools and chemicals used in traditional micro-manufacturing methods such as micro-injection molding or photolithography. It also allows for faster prototype development and iterative testing, accelerating innovation cycles and making them more cost-effective.