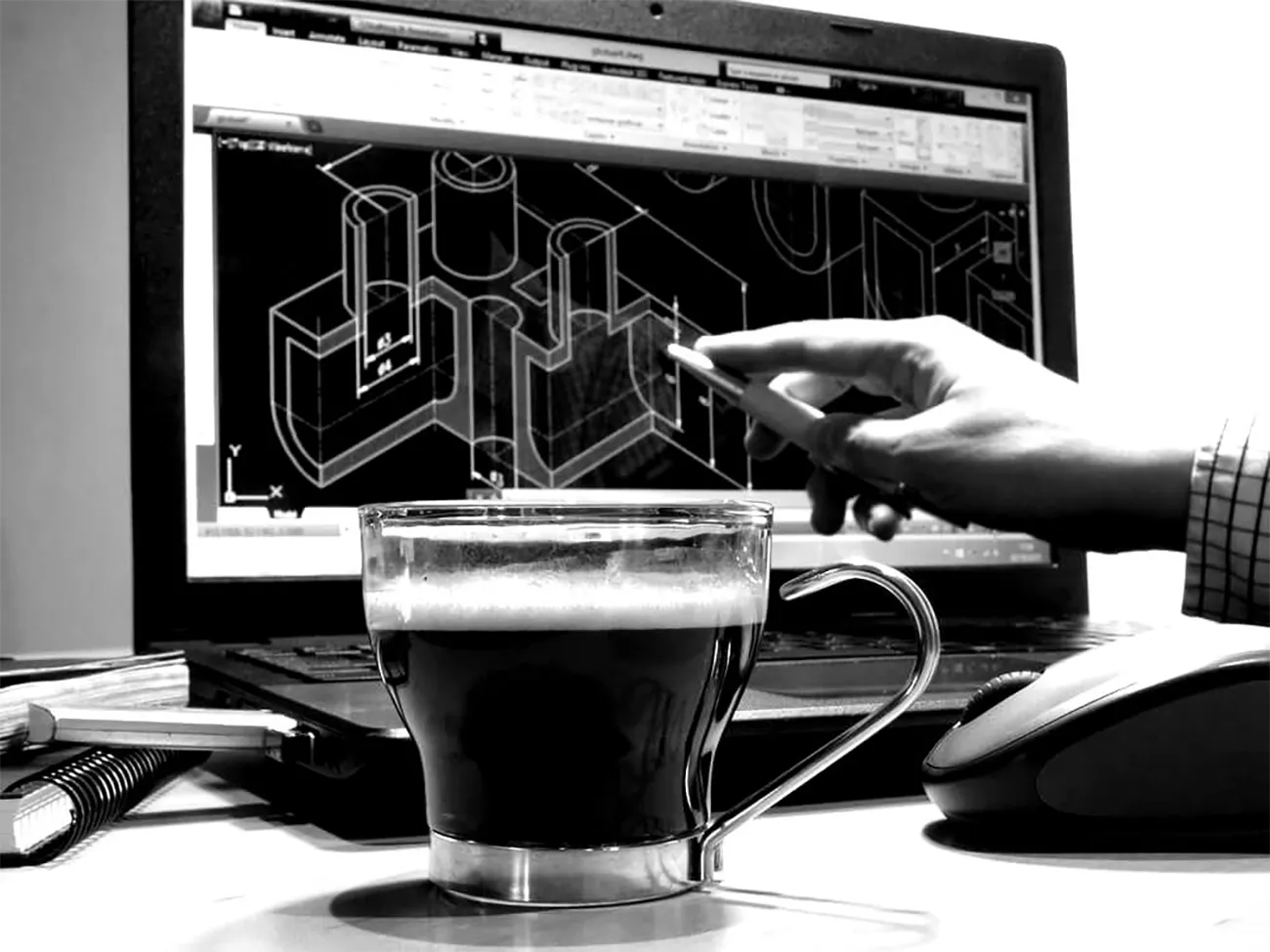
In 3D printing processes, the orientation of components in the build space during the printing process plays a significant role in the quality of the result. In the HP Multi Jet Fusion process, no support structures are necessary as it is a powder bed process. Capillary effects may occur during the printing process. Additionally, the heat profiles of individual components are crucial, making component orientation important for the quality of printed objects.
Component Orientation in HP Multi Jet Fusion
Topside/Bottomside
The unique aspect of the Jet Fusion process is the spraying of a heat-conductive liquid onto the material powder, causing the powder to sink slightly. However, at the edges, capillary effects cause the opposite effect, where the liquid-powder mixture is pulled slightly upwards. As a result, the surfaces are slightly concave with upward-standing edges (on the order of ≈ 0.1 mm). The heat source acts from above on the build space, making the upward-facing surfaces hotter and somewhat rougher. On the “bottomside,” the surfaces are smooth, but the edges towards the object are slightly rounded.
Stepped Effects
The so-called stepped effects are the visible layers typical of 3D printing production, primarily occurring in the Z-dimension. They are usually barely or not visible on straight surfaces. Particularly on curves and shallow angles, the layers become apparent. We offer post-processing treatments that can reduce these stepped effects (tumbling, painting).
Accuracy / Resolution
The accuracy (resolution) of the HP Jet Fusion process actually depends on the droplet size (20 µm) of the fusing agent and the layer thickness used for printing. However, since the material powder has a grain size of 60 µm, there is a limitation to the accuracy here.
- On the X-Y plane, a resolution of 1,200 dpi is used.
- The Z-plane has a resolution of 80 µm and is usually the limiting factor for accuracy.
- Deviation from the original size occurs in HP Jet Fusion due to manufacturing reasons. The material powder is melted and then slowly cooled. The resulting shrinkage and material tensions are the reasons for any deviations from the original.
- This effect is more pronounced due to the lower resolution in the Z-plane.
Possible Orientations in the Build Space
There are actually only two sensible possibilities for component orientation in the build space (flat or angled).
- The usual case is the flat orientation, which increases accuracy.
- An angled orientation increases surface uniformity but comes at the expense of accuracy.
Special Cases
- To avoid warping, printing should always be done flat, as the probability of warping increases with an angled orientation.
- Curves should always be oriented flat to avoid the object from becoming perfectly round due to visible layers.
- Depending on the geometry, a specific orientation may also be sensible for certain objects. Especially for components where the heat profile plays a role, such as delicate components, housing parts, or large cavities, this may become necessary. Please inform us of such special cases.
The experience gained from printing over 100,000 objects per year enables our engineers to optimally orient your components in the build space. If you have specific requests regarding the orientation of your component, please notify us, and we will assess the feasibility.
About 3Faktur: 3Faktur specializes in 3D printing, rapid prototyping, and rapid manufacturing. We utilize HP’s Multi Jet Fusion technology and offer various materials for prototyping and series production. If you have any questions about your project, feel free to contact us.