HTL (High-Temperature Liquid) from Boston Micro Fabrication is an advanced material for micro 3D printing, known for its exceptional temperature resistance and excellent mechanical properties. Ideal for applications in electronics, automotive, and other industries, HTL enables the production of highly precise and durable micro-components.
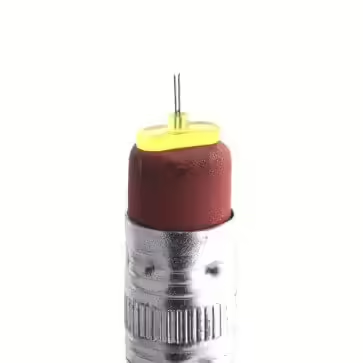
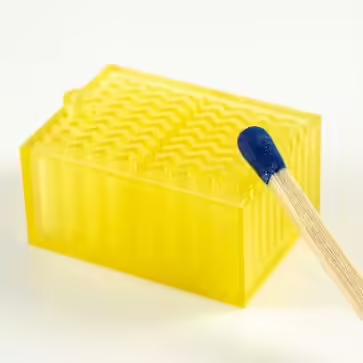
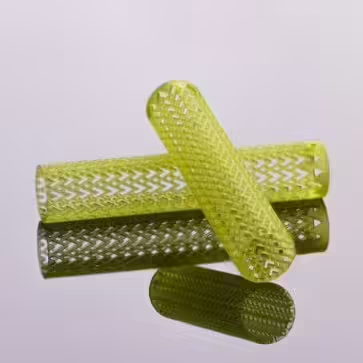
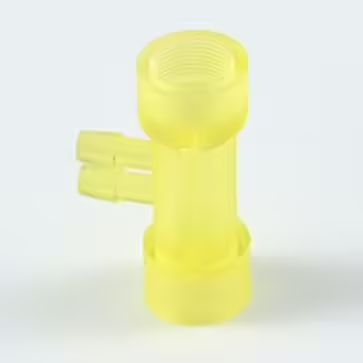
Key Information
Technology
Micro 3D Printing PµSL
Colors
Yellow-Translucent
Build Volume
100 x 100 x 50 mm
Production Time
Approx. 5 – 7 working days
Accuracy
+/- 25µm ~ +/- 50µm
Material Properties of HTL
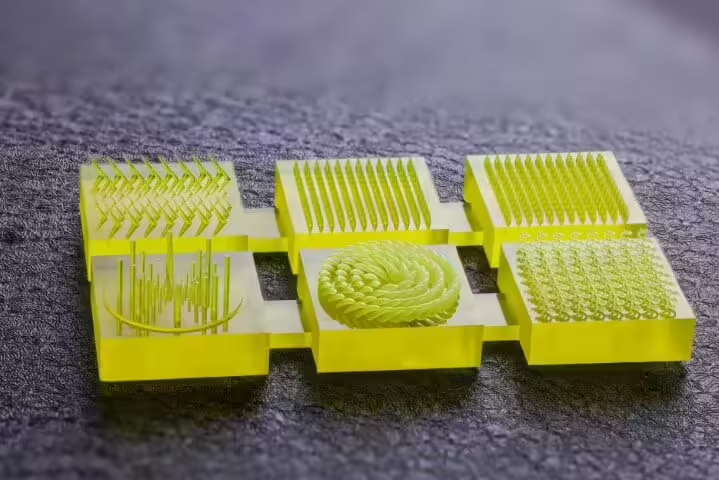
Mechanical Properties
HTL (High-Temperature Liquid) is characterized by high strength, stiffness, and heat resistance. The material is excellent for applications requiring high precision and detail, as well as technical and medical applications requiring autoclave sterilization.
- Tensile Strength: 71.5 MPa
- Elastic Modulus: 2,397 MPa
- Elongation at Break: 7.8%
- Flexural Strength: 112.9 MPa
- Flexural Modulus: 2.8 GPa
- Hardness: 81 (Hardness D)
- Water Absorption: 1.05% after 24 hours
Thermal Properties
With relatively high heat deflection temperature, the material can also be used at higher temperatures. This heat resistance makes HTL particularly suitable for applications in electronics and medical technology, where components need to withstand autoclaving (sterilization) or demanding operating conditions.
- Heat Deflection Temperature (HDT @ 0.45 MPA): 114.2 °C
- Glass Transition Temperature (Tg): 172 °C
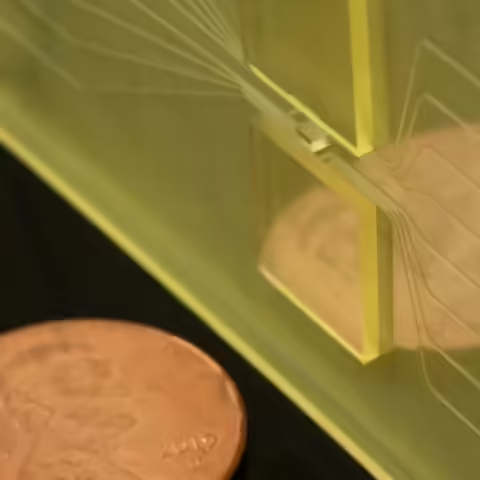
Surface Properties
The surfaces produced by the technical process are already very smooth, eliminating the need for additional surface treatments.
- Surface Roughness (Top): 0.4-0.8 µm Ra
- Surface Roughness (Side): 1.5-2.5 µm Ra
Color
HTL is available in various colors, including yellow-translucent, black, and carbon black. Our standard color is yellow-translucent. The properties of the material may vary depending on printing conditions and post-processing procedures.
Downloads
- Material Data Sheet: HTL Material Data Sheet
Manufacturing Tolerance
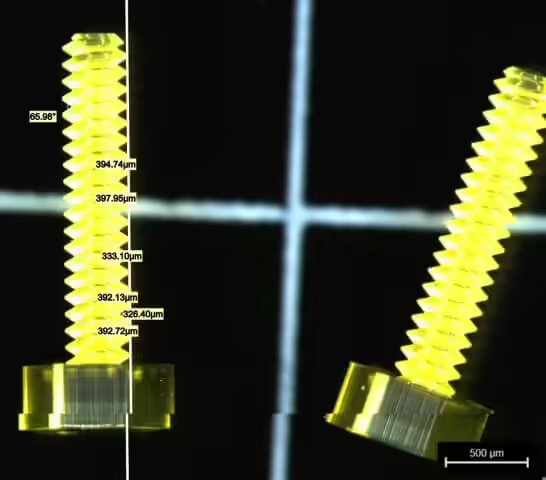
The general tolerance is +/- 25µm to +/- 50µm, depending on geometry and the resolution used (10 µm or 25 µm).
Post-Processing of HTL
Post-processing is currently not offered for this material.
Design Guidelines
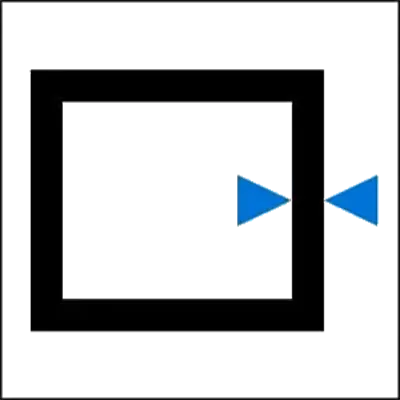
Minimum Wall Thickness The minimum wall thickness should not be less than 50 µm.
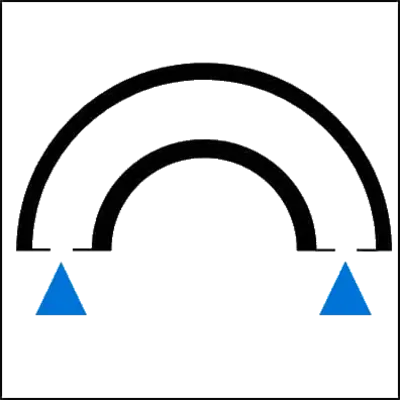
Cavities
Hollow objects should provide openings in two places to allow excess material to be removed.
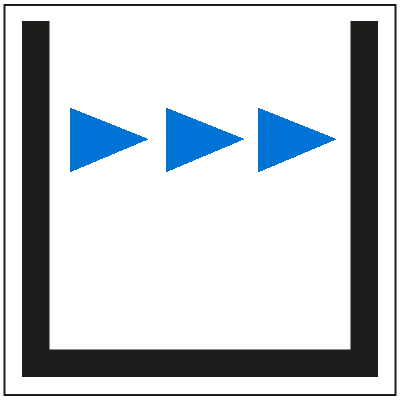
Spacing
Maintain a distance of at least 50 µm for grooves or closely spaced walls. Individual objects (“shells”) must always be uploaded as separate files unless they are firmly connected.
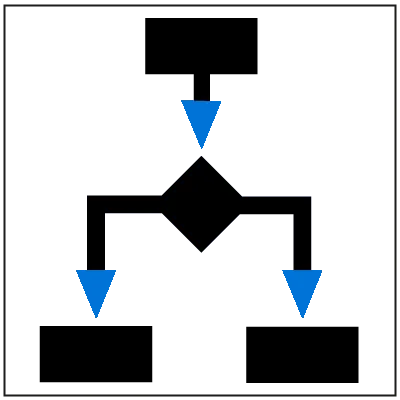
Resolution
Details up to a size of about 50 µm can be represented.
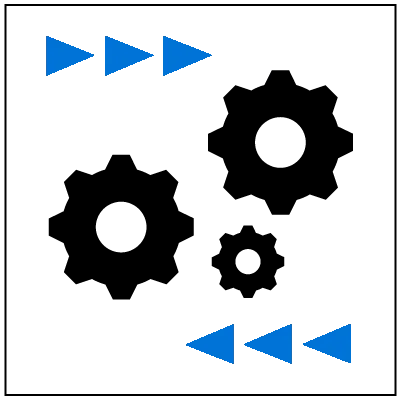
Geared Objects
Intermeshed objects cannot be manufactured.
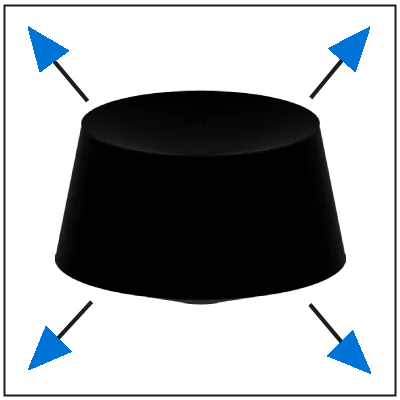
Size
The platform size allows for component sizes up to 100 mm. However, the process is more aimed at smaller components up to a few centimeters or even components in the millimeter range.
Applications
The HTL material can be used for both prototypes and end-use applications.
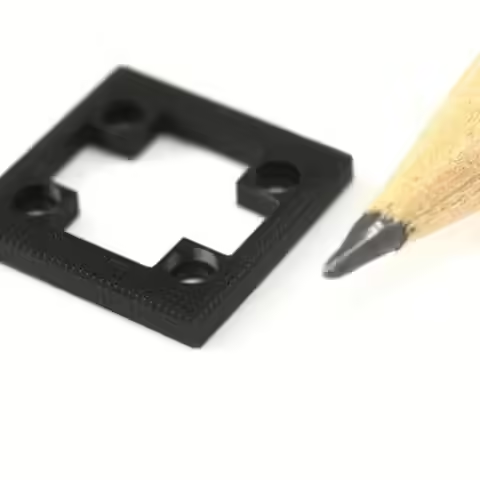
Electronics
Micro 3D printing PµSL enables the production of small electronic components such as connectors and chip sockets with the necessary thermal and mechanical stability required for demanding applications like 5G. In addition, PµSL supports the miniaturization of electronics without compromising speed, precision, and surface quality.
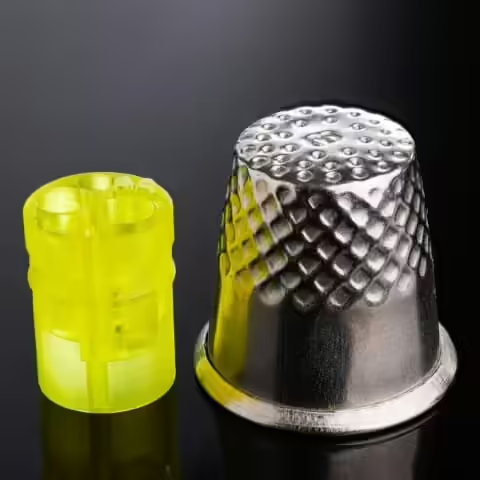
Medical Components
Projection Micro Stereolithography (PµSL) enables the production of small, high-precision parts that are crucial for modern medical devices. This technology can print biocompatible plastics with a resolution of 10 µm and accuracy of +/- 25 µm, making it ideal for applications such as endoscope tips, cardiovascular stents, and spiral needles for minimally invasive surgery. PµSL also reduces the number of required components and assembly steps, leading to shorter production times and increased design flexibility.
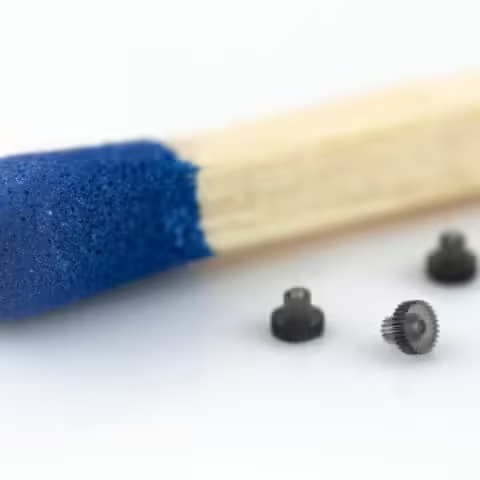
Micro-Electro-Mechanical Systems (MEMS)
Micro 3D printing supports the production of small mechanical parts such as switches, gears, sensors, motors, and valves required in MEMS applications. A key advantage of PµSL is the ability to print internal structures and fine details that are difficult to achieve with traditional micro-injection molding or CNC machining. PµSL also reduces the need for expensive tooling and speeds up the prototyping process, shortening development cycles and reducing costs.
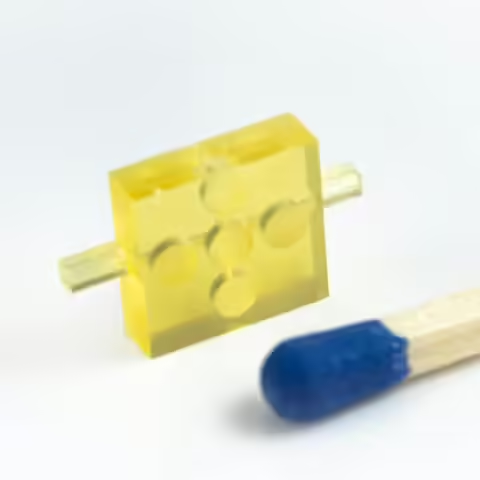
Microfluidics
This technology can print microchannels with diameters as small as 50 micrometers and high aspect ratios, making it critical for the precise handling of extremely small liquid volumes. PµSL offers fast processing and excellent surface quality, significantly facilitating the production of lab-on-a-chip (LOC) devices and other microfluidic applications. In addition, PµSL supports biocompatible and high-temperature resistant materials required for use in biomedicine and diagnostics.
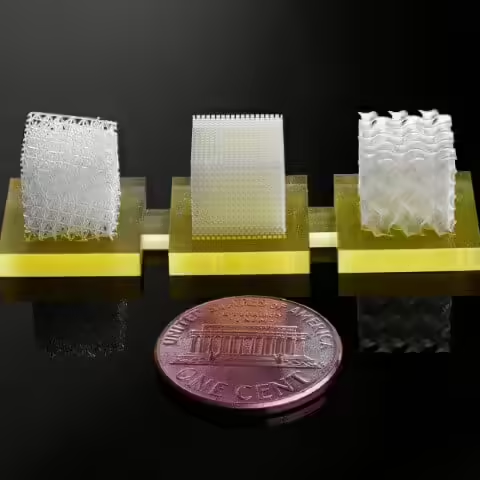
Research & Development
PµSL enables the production of microscopically small, high-precision components. PµSL technology offers a resolution of 10 µm and accuracy of +/- 25 µm, essential for the development and research of new materials and devices. This technology reduces the need for expensive tools and chemicals used in traditional micro-manufacturing methods such as micro-injection molding or photolithography. It also allows for faster prototype development and iterative testing, accelerating innovation cycles and making them more cost-effective.
Prices
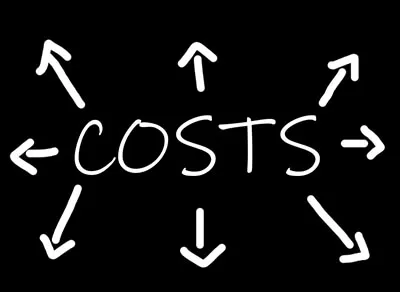
Offer
An instant price offer for micro 3D printing is currently not possible due to the complexity of the technology. Please use our manual inquiry function for your request. Your inquiries will be answered within one working day.
Calculation
Prices are primarily based on machine runtime, as well as the extent and complexity of cleaning.
Minimum Order Value
EUR 50,- plus VAT (EUR 59.50 incl. VAT) per order
Discounts
Significant reductions compared to the standard price are possible for larger quantities, depending on the quantity, part size, and geometry.