PA11, also known as Polyamide 11, originates from renewable sources and represents the next generation of technical thermoplastics. It differs from PA12 due to its increased flexibility and impact resistance, while also offering high mechanical resilience. The material (commercially named HP High Reusability PA11) is distinguished by its excellent toughness and chemical resistance. The material is well-suited for flexible components such as film hinges and snap connections, as well as highly durable orthoses.
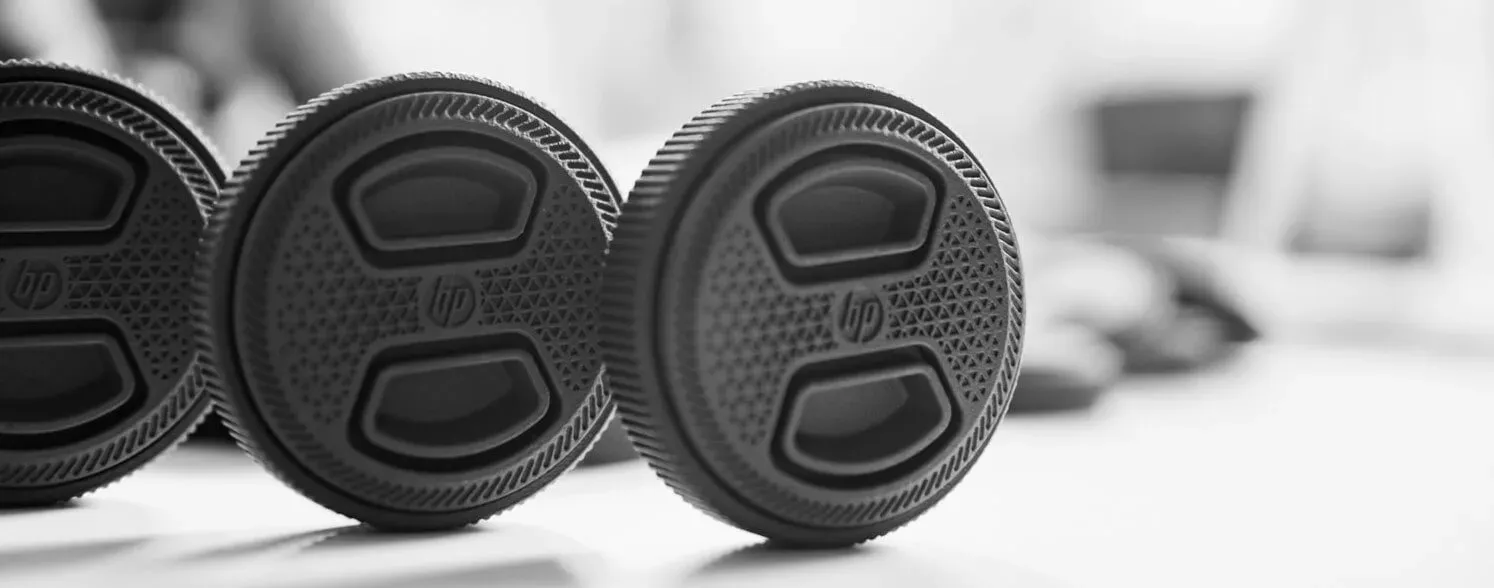
Key Information
Technology
Multi Jet Fusion
Colors
Gray
Black (dyed)
Build Volume
min. 10 mm
max. 380 mm
Production Time
9 business days
Accuracy
± 0.5 %
(min. ± 0.5 mm)
Material Properties
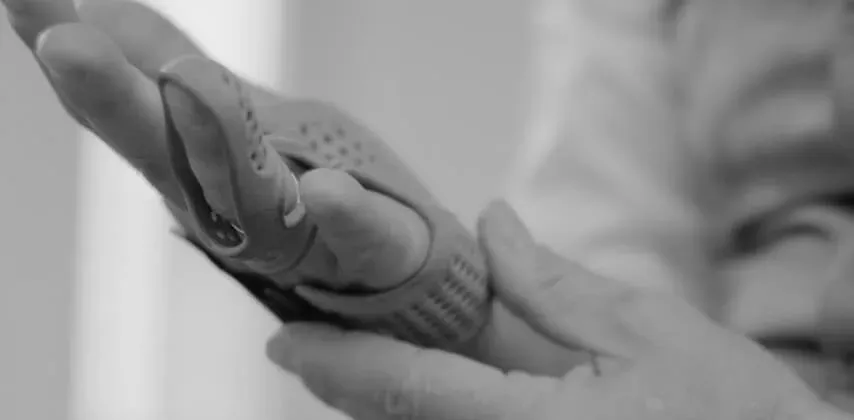
Mechanical Properties
- Tensile Strength: 52 MPa
- Elongation at Break: 35 – 50% (X/Y); 25% (Z)
- Modulus of Elasticity: 1,800 MPa
- Density: ~0.9 – 1.05 g/cm³ (geometry-dependent)
Polyamide 11 is a flexible, resilient, and durable plastic. It sets itself apart from PA12 with its increased flexibility and impact resistance, while also offering high mechanical durability. PA 11 is known for its outstanding toughness and chemical resistance.
Thermal Properties
- Heat Deflection Temperature (HDT) at 0.45 MPa: 185 °C
- Heat Deflection Temperature (HDT) at 1.82 MPa: 54 °C
For continuous use, temperatures should not exceed 95 °C. For short-term loads, temperatures up to a maximum of 120 °C are possible depending on geometry. Particularly for thin wall thicknesses (< 2 mm) and/or simultaneous mechanical stress, load-bearing capacity may be reduced.
Surface Properties
- Surface Roughness Ra Bottom: 4 ± 2 µm
- Surface Roughness Ra Top: 9 ± 2 µm
- Surface Roughness Ra Slope (45°): 7 ± 2 µm
The base material used in Multi Jet Fusion is in a powder state in its raw form. This results in a slightly rough surface, similar to fine sandpaper. The typical 3D printing layering effects (print lines) are visible on shallow angles (up to about 15°) and quite fine, as the layer thickness is only 80 µm. PA11 has a smaller grain size compared to PA 12, leading to slightly improved surface properties and detail resolution.
Color
In the 3D printing process, white PA 11 powder is mixed with a black dye. This results in a complete black coloration of the interior of the components. However, on the outer surface, white particles remain, primarily from fused white powder, leading to a characteristic gray appearance. The production process creates varying light-dark shades on this surface. An optional black dyeing process is available, which colors all white areas, making the component uniformly black in appearance – both on the outside and the interior.
DOWNLOADS
- Material Data Sheet: Material Data Sheet
- RoHS/Reach: Certificate
- UV Stability: Accelerated Weathering Test
- Summary of Regulatory Requirements: Summary of Regulatory Compliance and Environmental Attributes
MANUFACTURING TOLERANCE
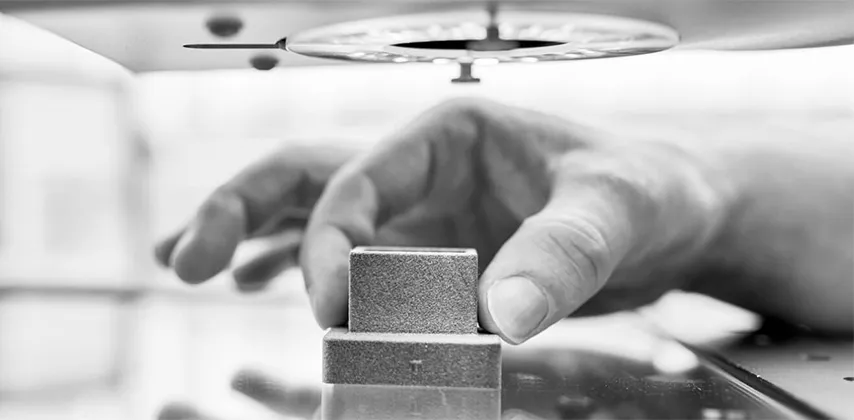
The general tolerance is 1.2 mm up to 100 mm outer dimension, above this 0.5 %.
PA 11 is susceptible to warpage and is not suitable for large-area, flat components (e.g. large, flat housing parts).
Properties Manufacturing Tolerance Post-Processing Design Guidelines Applications Prices
Post-Processing
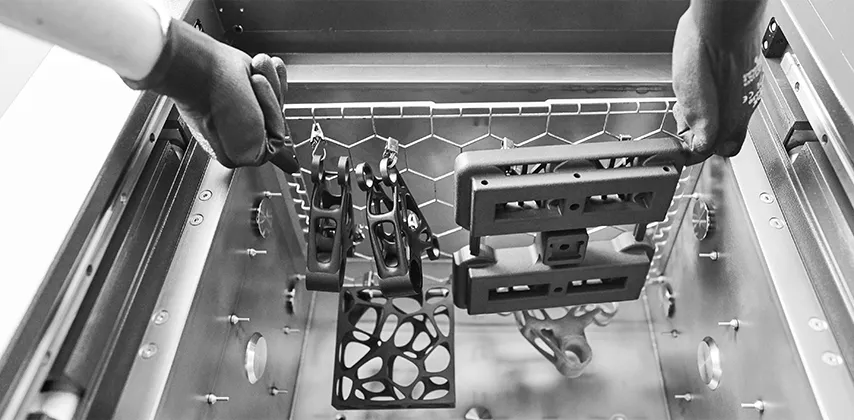
Black Coloring & Shot Peening
Recommended for visible parts: immersion dyeing followed by surface compaction (shot peening) for a visually and tactilely high-quality finish.
Ordering Information
- Delivery Time: + 1 working day
- Price: Dependent on quantity and size, typical unit costs of approximately EUR 1 – EUR 10; excluding VAT
- Maximum Size: 350 x 250 x 150 mm
Vapor Smoothing (Chemical Smoothing)
Chemical surface treatment that results in a pore-free surface with reduced roughness. Significant applications include components carrying liquids or gases, parts requiring easy cleaning (medical, cleanroom), or as a foundation for subsequent coating processes (reduction of ‘outgassing,’ porosity reduction, smoothing).
Ordering Information
- Delivery Time: + 5 working days
- Price: Dependent on quantity and size, typical unit costs of approximately EUR 7 – EUR 10; excluding VAT
For more information, please visit Chemical Smoothing.
Painting
For wet painting, a paint specifically formulated for polyamide is applied.
Ordering Information
- Delivery Time: + approximately 2 weeks
- Price: Highly dependent on size and quantity. Note: The minimum order value for this service is EUR 100,- excluding VAT.
For more information, please visit Painting.
Properties Manufacturing Tolerance Post-Processing Design Guidelines Applications Prices
Design Guidelines
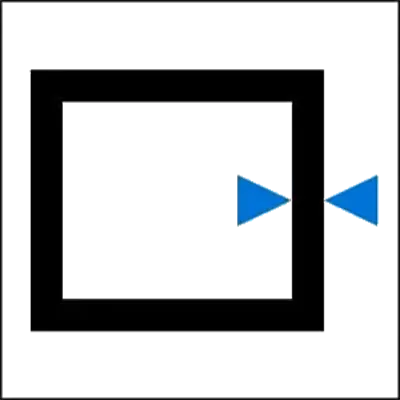
Minimum Wall Thicknesses
A minimum wall thickness of 1.2 mm is recommended. For flexible elements, especially film hinges, smaller wall thicknesses can be used.
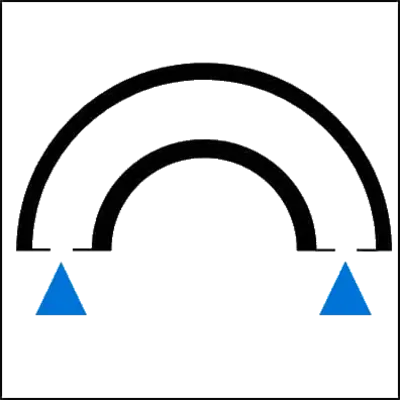
Cavities
Hollowed objects can be printed, but openings (min. 10 mm diameter) must be inserted so that excess material can be removed. For larger cavities, you should plan for several openings. The source material is compacted during the printing process, so excess material is very difficult to remove.
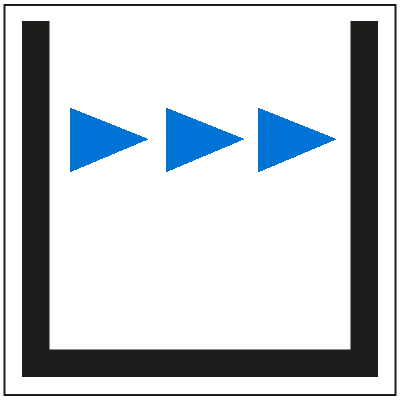
Distance
Keep a distance of min. 0.5 mm for grooves or walls that are close to each other. Individual objects (“shells”) must always be uploaded as a separate file unless they are firmly connected to each other.
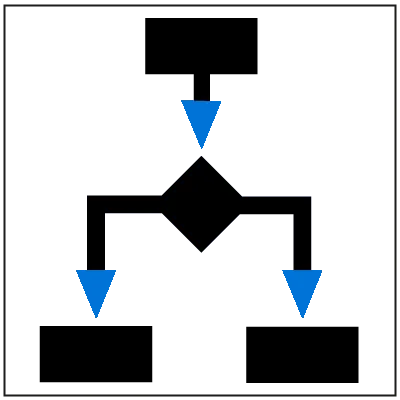
Resolution
Details down to a size of approx. 0.5 mm can be displayed.
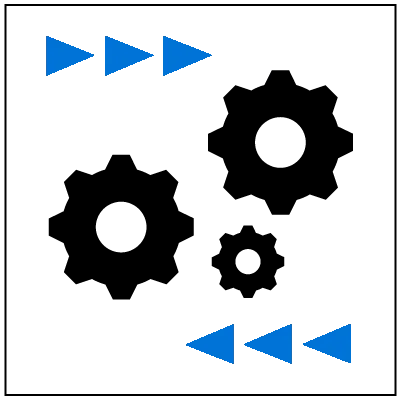
Toothed Objects
Interlocked objects can be printed. Please note the minimum distance between the objects of min. 0.5 mm. Also note that the corresponding areas are accessible in order to be able to remove excess material powder.
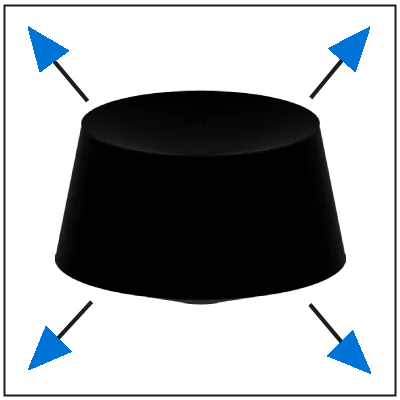
Size
The object should not be larger than 370 x 274 x 380 mm.
Properties Manufacturing Tolerance Post-Processing Design Guidelines Applications Prices
Applications
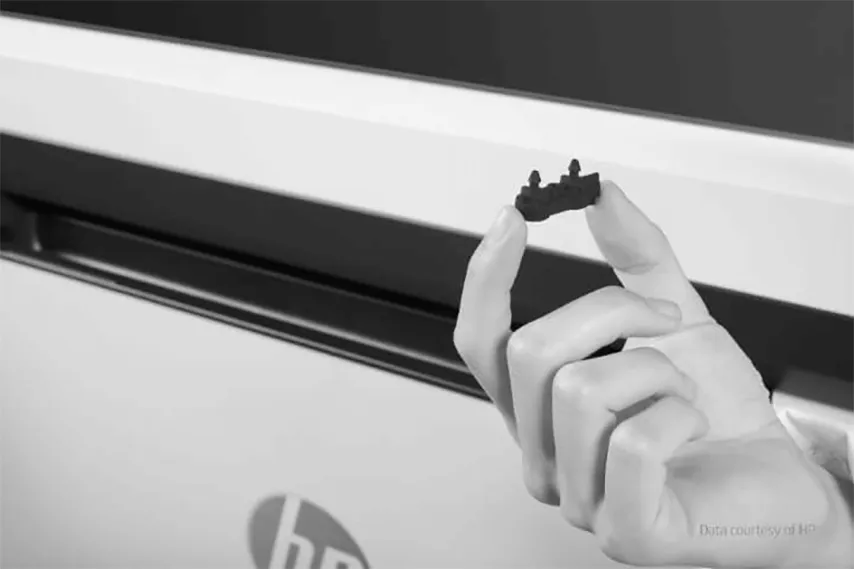
In terms of resilience, durability and replicability in processing, the material is designed for series production up to a batch size of approx. 5,000 units. Of course, this does not stand in the way of its use for prototypes. Typical applications for polyamide 12 include:
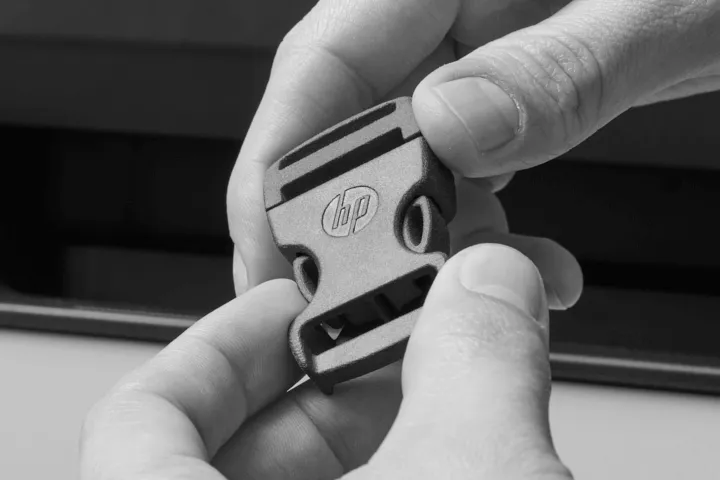
Components with functional, flexible elements
PA 11 is ideal for flexible elements such as snap-fit connections, film hinges or spring elements and often shows a higher load-bearing capacity than polypropylene processed in 3D printing.
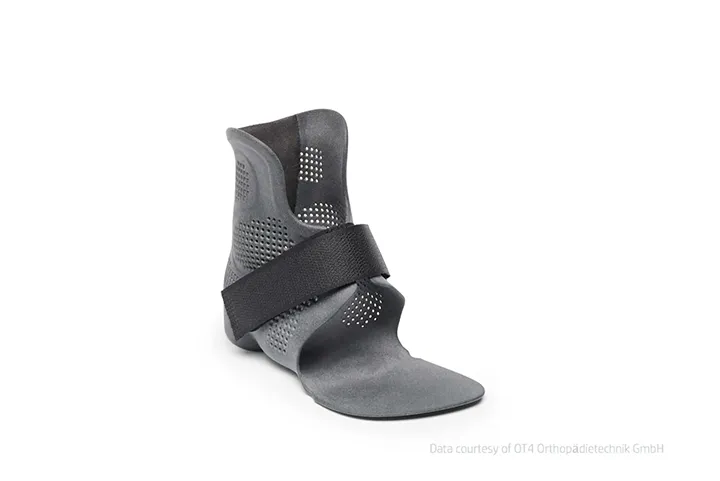
Orthoses
PA 11 has a higher elongation at break and is therefore often a better option than PA 12 for dynamic loads. In addition, PA 11 is certified for skin contact and is basically suitable for various orthopedic products.
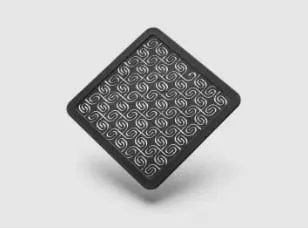
Smaller components with a high level of detail
The raw material of PA 11 has an average grain size that is about 20% smaller than that of PA 12. This enables better representation of small details, and components made of PA 11 are characterized by an overall higher surface quality.
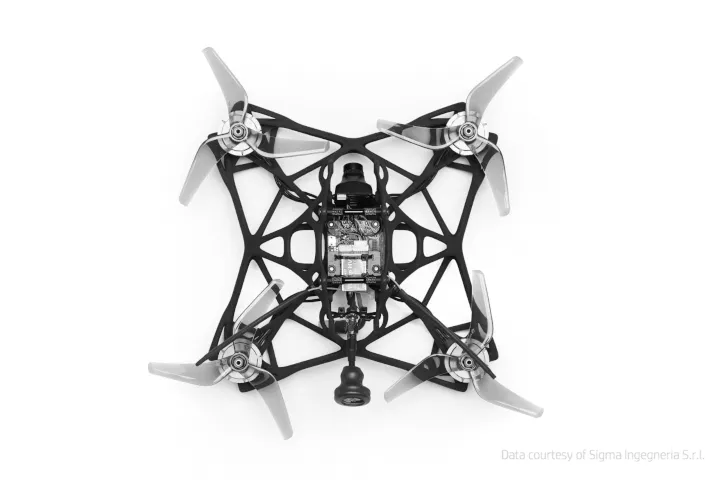
Drones
PA 11, with its high elongation at break, is ideally suited for structural elements in drone construction. Elements made from it can even withstand crashes from great heights.
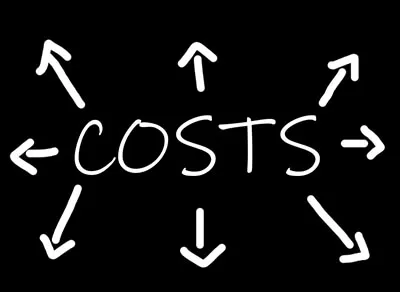
Quotation
You can receive an instant price quote for your model here.
Calculation
Prices are calculated based on factors such as machine volume, model surface, and material usage.
Minimum Order Value
EUR 50,- plus VAT (EUR 59.50 including VAT) / Order
Discounts
For higher quantities, reductions up to approximately 45% compared to the standard price are possible (dependent on quantity, part size, and geometry).