Selective Laser Melting (SLM) is similar to the Selective Laser Sintering process. In metal laser melting, unlike SLS, the melting point of the material is exceeded. Selective Laser Melting has become the established additive manufacturing process for making metals in powder form usable for 3D printing. Metal 3D direct printing is therefore suitable for the rapid and precise production of metal prototypes and small series. Similar to laser sintering, 3D printing using the SLM process also allows the production of complex geometries that are often not achievable using conventional methods due to geometric constraints. Common terms for this manufacturing process include DMLS (Direct Metal Laser Sintering), LMF (Laser Metal Fusion), or according to the standard PBF-LB/M (Laser-based powder bed fusion of metals).
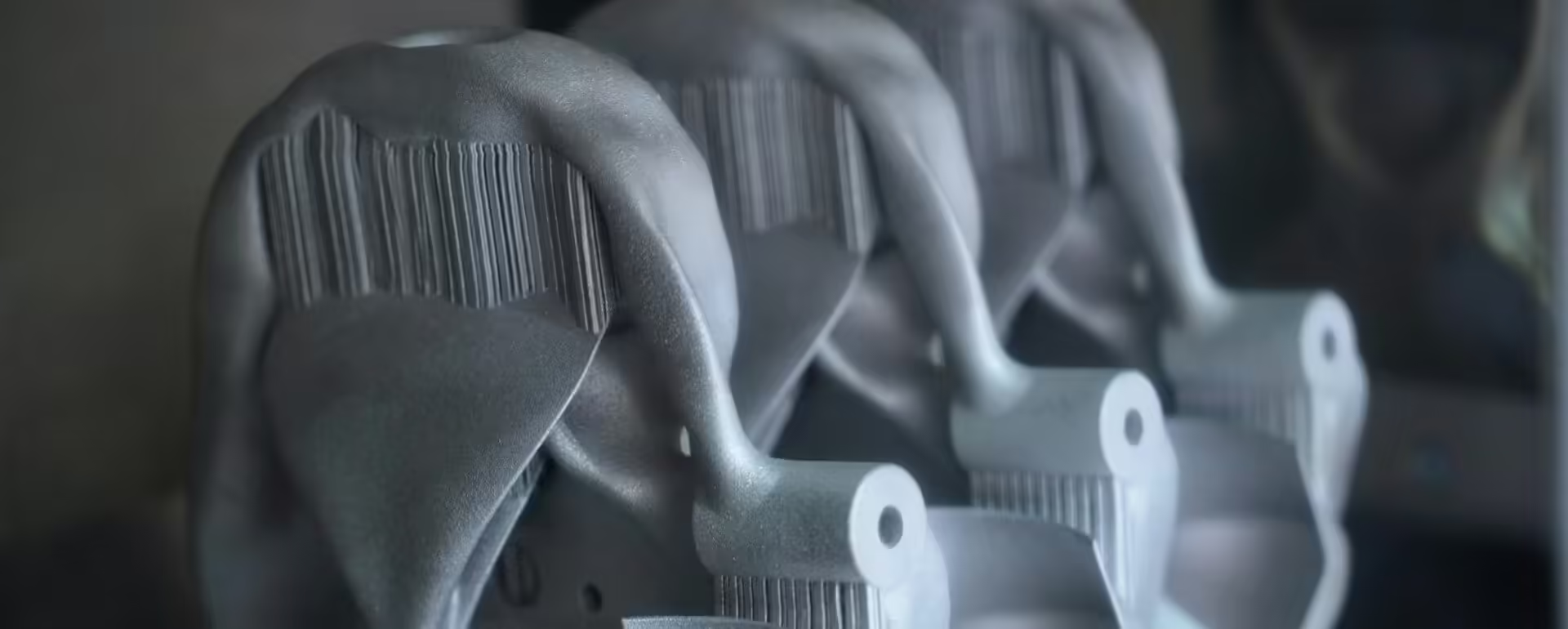
Key Info
Materials
Aluminum AlSi10Mg, Stainless Steel 1.4404 (316L)
Colors
–
Build Volume
150 x 150 x 150 mm
Accuracy
Tolerance according to ISO 2678-1-m
Production Time
10 – 14 working days
Metal 3D Printing Technology: Selective Laser Melting
As with all 3D printing processes, laser melting requires a pre-existing and printable 3D model in addition to the 3D printer. This model is computer-controlled and divided into a large number of layers (slicing). These layers are individually transferred to a material in powder form (average particle size ≈ 30 µm). At this point, the powder is completely melted with a laser (usually a fiber laser) and solidifies, forming a solid layer of the material used. The build platform then moves down by a defined layer thickness – usually between 20 and 60 µm. After lowering, a new layer of material is applied, and the laser melts the next layer of the 3D model into the powder. This continues until the 3D model is fully printed. As with other powder bed-based additive manufacturing processes, the object must be cleaned of excess powder afterward.
To prevent excessively high process temperatures and manufacturing-related distortions due to thermal input, support structures and a firm connection to a metal build platform are necessary in this process. A heated build platform may also be used to prevent thermal distortion.
The Process Chain in Metal 3D Printing
1 / Data Checking & Preparation
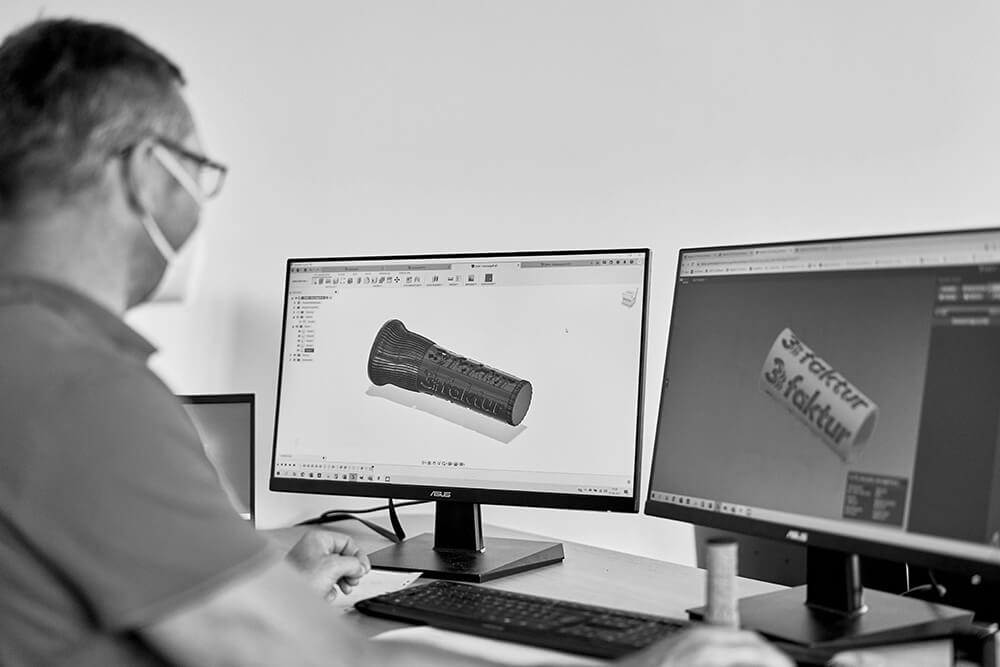
As with other processes, CAD data is checked for manufacturability. Due to the complexity of the process, certain technical limitations must be considered. At this stage, potential design optimizations are also reviewed and agreed upon if necessary. Once the data is finalized, the print is prepared (part orientation and support generation) and the printing parameters are selected.
2 / 3D Printing
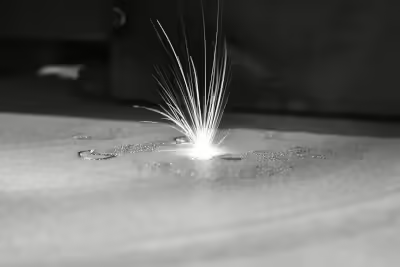
The duration of metal 3D printing depends heavily on the build height and the specific geometry of the parts being produced. Typically, the printing takes about a full day for smaller parts and several days for larger parts. Depending on the requirements, parameters can be selected for higher productivity or higher accuracy, which also affects production times. Typical build rates are around 20 cm3 per hour.
3 / Removing Excess Powder
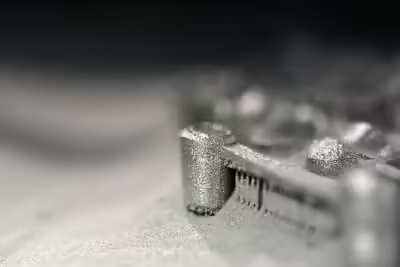
Before separating the parts from the build platform, the excess unused powder is removed. This can be done either directly in the manufacturing machine or in an external unpacking station, depending on the equipment used. The unused powder is then processed and can be largely reused in the process.
4 / Removing Support Structures
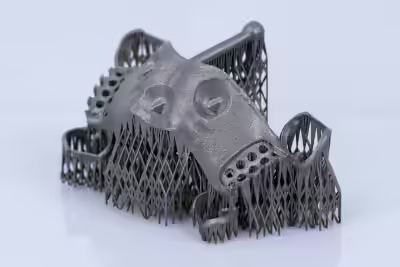
The parts are then separated from the build platform, and the support structures are usually removed with hand tools.
5 / Surface Treatment
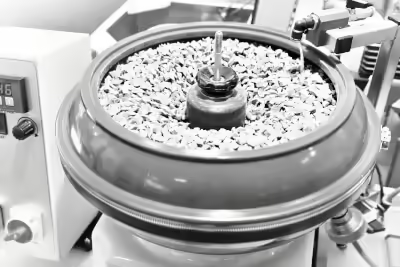
These steps are followed by further processing steps, such as machining or stress relief annealing, as required.
Materials for Metal 3D Printing
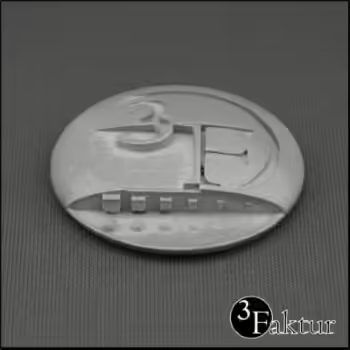
Aluminum AlSi10Mg
The aluminum alloy AlSi10Mg is particularly valued for its lightweight properties combined with high strength, making it especially suitable for lightweight construction applications, such as in aerospace.
Build Volume: max. 150 x 150 x 150 mm
Costs: Request a quote
Material Datasheet: Download
Material Information Page: Aluminum AlSi10Mg
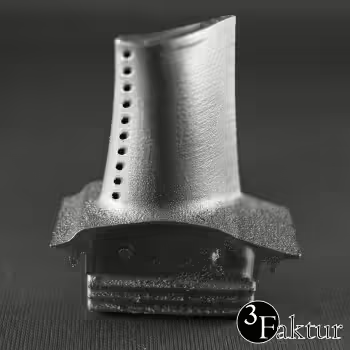
Stainless Steel 1.4404
The stainless steel 1.4404 (“316L”) is valued for its good deformation properties and corrosion resistance. It is therefore used, for example, in automotive and medical technology.
Build Volume: max. 150 x 150 x 150 mm
Costs: Request a quote
Material Datasheet: Download
Material Information Page: Stainless Steel 1.4404
Post-Processing
Standard Processing
- Support Removal: The support material is removed, and the contact points are manually ground.
- Sandblasting: The parts are treated with compressed air blasting using solid blasting media.
Additional Finishing Options
Upon request, we offer the following post-processing options:
- Mechanical Post-Processing: Additively manufactured metal parts can be post-processed using CNC machining to achieve specific target roughness and/or tolerances.
- Stress Relief Annealing: Stress relief annealing reduces stresses in the material. For the materials we offer, this is generally not required but can be advantageous in certain applications or geometries.
- Surface Treatment: Additional surface treatments, such as vibratory finishing (“trowalizing”), can be arranged individually.
Applications
Prototypes
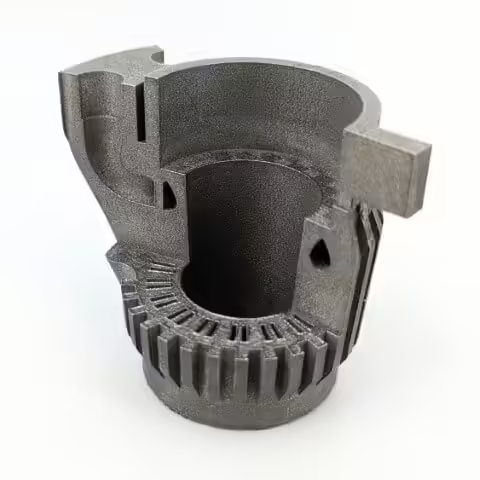
Metal 3D printing allows for the rapid production of prototypes of small and medium-sized machine components and other metal parts.
Jigs & Tools
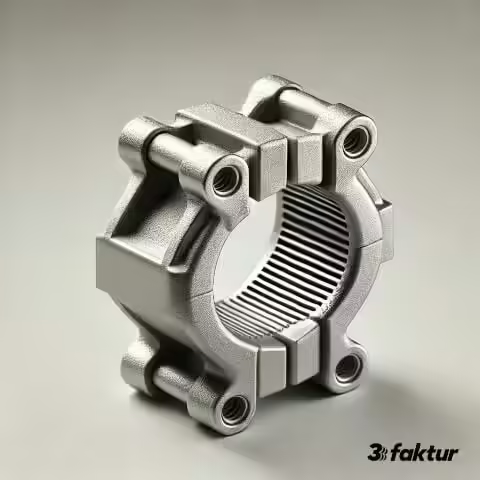
Additive metal manufacturing is ideal for producing jigs for industrial manufacturing. The ability to create complex, organic structures allows for the production of jigs with optimal contours in short lead times.
Small Series of Machine Components
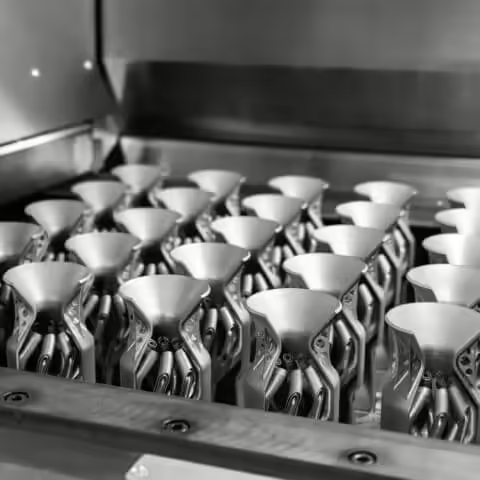
Geometrically complex metal parts can also be produced in small and medium series of up to a few dozen pieces. The densities achieved are over 99%, meaning the strengths achieved are comparable to those of conventionally manufactured technologies.