3Faktur specializes in additive serial production. We exclusively use the “Multi Jet Fusion” process. Our specialization allows us to achieve a very high degree of optimization and efficiency. We meet the highest quality standards and are certified as an industrial additive manufacturing facility by TÜV Süd among other certifications.
For you, this means reliable quality, replicability, and competitive delivery times.
Preparation
Preparation forms the basis for successful production. Your workpieces go through an elaborate process before production begins. Our preparation relies on the experience gained from hundreds of thousands of components to optimize your project to its fullest potential.
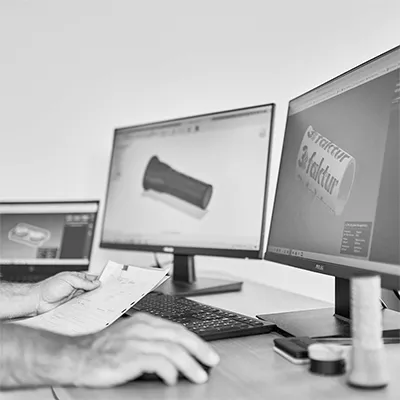
Component Orientation
The component orientation significantly affects dimensional accuracy and surface quality. Each component is individually analyzed by our experienced preparers to ensure the optimal balance between surface quality and dimensional accuracy in all dimensions.
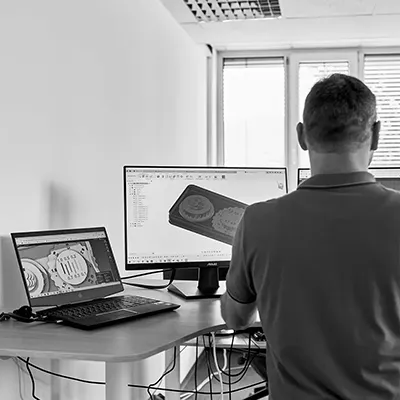
Manufacturing Analysis
All components undergo a fundamental analysis to determine their manufacturability and identify potential issues. For example, the component is examined for wall thicknesses or potentially problematic geometries such as internal narrow channels, geometries prone to warping, or similar factors.
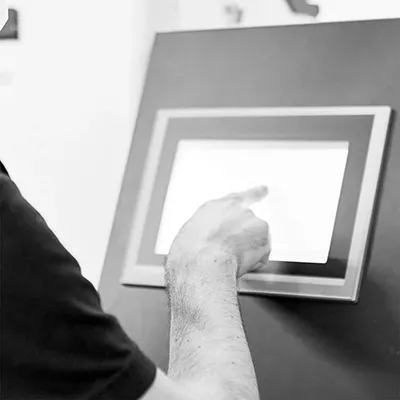
Individual Production Parameters
For each model, individual production parameters are defined to achieve the best possible result. For example, the distance to other components and the position in the build space are individually defined.
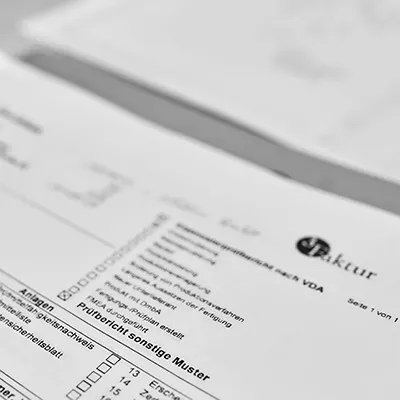
Customized Process Flow
Each component is different, and every project has its specific requirements. For each order, an individual process flow (‘Pathway’) is defined, which includes fundamental processing steps as well as geometry-specific instructions for the operator.
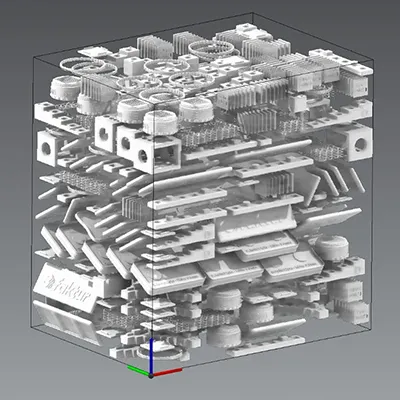
Nesting
Once all parameters are defined, nesting takes place. This process involves nesting all components of a production cycle (typically 50-300 components) together to create an optimal job. The goal is to achieve a balanced heat profile. The more even the heat distribution in the printer, the better the dimensional accuracy, surface quality, and mechanical properties. The art lies in preparing the components optimally for a job and selecting the number and type of components. This requires a great deal of tact and, above all, experience.
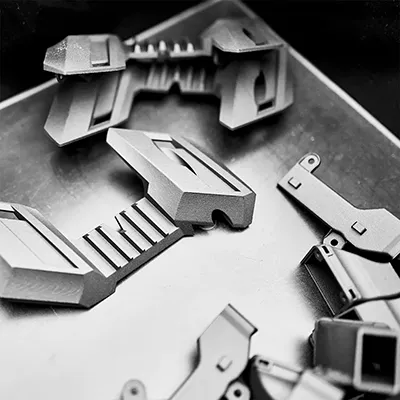
Defined Production Cycles for Serial Components
When components are produced in hundreds or thousands and regularly retrieved, individual production profiles are created. The achieved quality is intensively evaluated after the first run, and the parameters are further optimized if necessary. The goal here is to ensure the best possible replicability and quality. This includes not only general production parameters but also the requirement that serial components are always produced with an identical hardware combination.
3D Printing
Industrial production is demanding, and the difference between success and failure often lies in the details. Additive manufacturing is no different from conventional production processes in this regard.
Our high degree of specialization allows us to optimize down to the smallest detail, ensuring that even your highest expectations are exceeded.
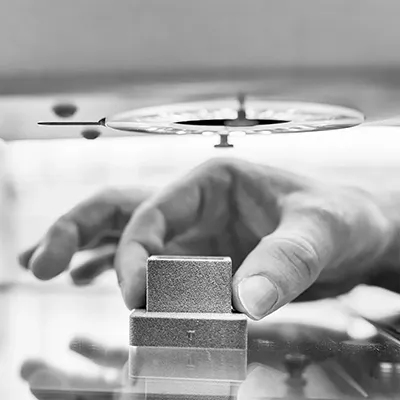
Quality-Oriented Printing Parameters
Printing is done in “Balanced Mode” (layer thickness for Polyamide 12: 80 µm). This mode offers an optimal balance of mechanical strength, surface quality, and dimensional accuracy. An individual parameter set is defined for each production cycle, based on thousands of cycles of experience.
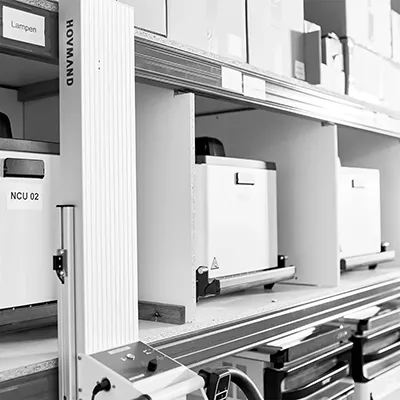
Slow Cooling Process
During printing, the build chamber in the printer heats up significantly. We employ a very slow cooling phase (at least 2 days) and explicitly avoid accelerating the cooling phase (“Fast Cooling”). This approach significantly improves dimensional accuracy, mechanical properties, and surface quality.
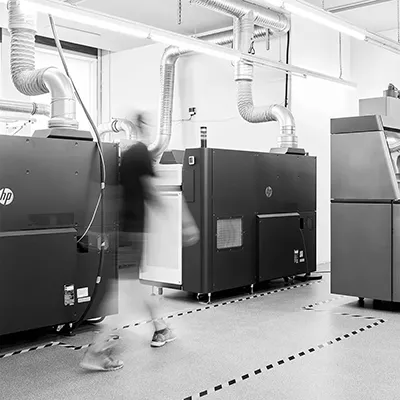
Controlled Production Environment
The thermal processing of polymers requires high standards for the production environment. Our production rooms are fully air-conditioned, ensuring constant temperature and humidity to guarantee maximum replicability in serial production.
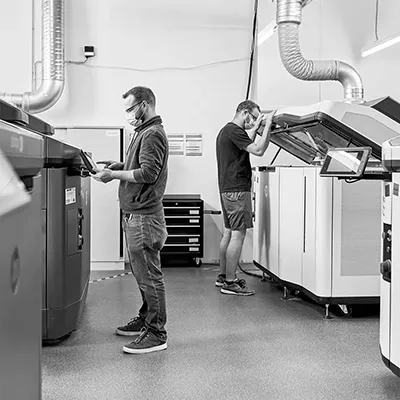
Industrial Production Technology
Our machine park includes state-of-the-art production equipment, which is maintained and calibrated before each production cycle. High replicability is of paramount importance to us, which is why wear parts are often replaced before the end of their service life to avoid potential quality impacts.
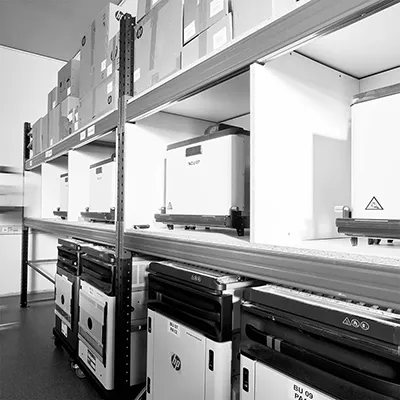
High Capacity
Due to our high specialization, we have sufficient capacity in both production technology and post-processing to handle large quantities. We operate in multiple shifts and on weekends to manage peak workloads and have achieved a “99.9% On-time Delivery” rate in 2020.
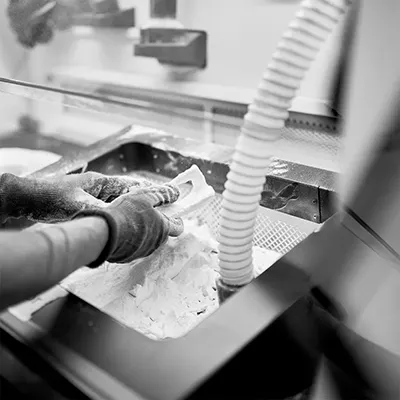
High-Quality Raw Materials
We only use certified, high-quality raw materials for production and post-processing. Each new batch of material is tested, and the starting material is checked before each production cycle to meet our high-quality standards.
Post-Processing
The actual printing is only part of the production chain; additional processing steps are required for the finished product. We rely on documented, highly optimized processes to deliver consistently high-quality and replicable parts.
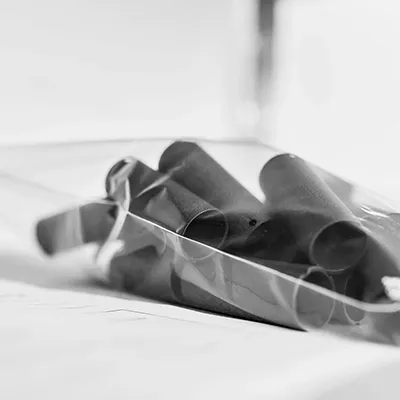
Replicable Processes
As a specialized provider, we can focus all resources on a manufacturing process. Thousands of parts go through this process every week under constant and optimized conditions. Each cycle is documented, controlled, and continuously improved.
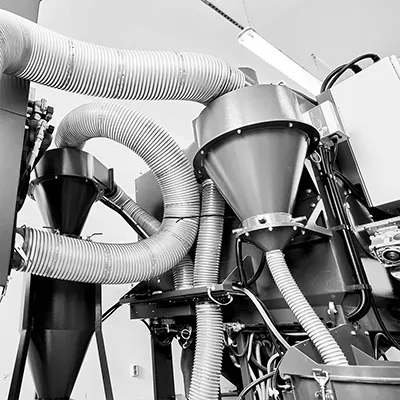
Optimized Plant Technology
To optimize the quality, replicability, and efficiency of the manufacturing processes, we also rely on specialized machines designed and manufactured to meet our requirements, helping us further enhance our production processes.
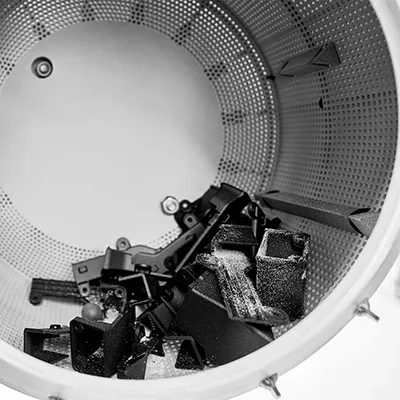
Extensive Experience
As one of the first providers of Multi Jet Fusion technology in Germany, we have a wealth of experience. Our processes are documented, controlled, and remain stable and reliable even during peak loads or unforeseen events (e.g., machine breakdown). However, that doesn’t mean we can’t improve further: we strive for continuous improvement to exceed your high expectations every day.
Quality Control
Quality assurance begins with the receipt of your order. Various checks are conducted at each step of the production chain to identify and address potential issues early on. The actual quality control represents the final step and includes numerous inspections of your parts and accompanying production samples, in addition to individual agreements.
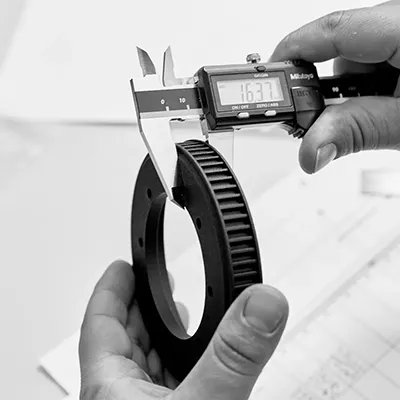
Systematic Testing Process
Quality checks are performed at all stages of production in our manufacturing facility. In the final quality control, various inspection and measurement steps are conducted. This includes individually agreed-upon measurement protocols, various sample tests, and thorough examination of production samples.
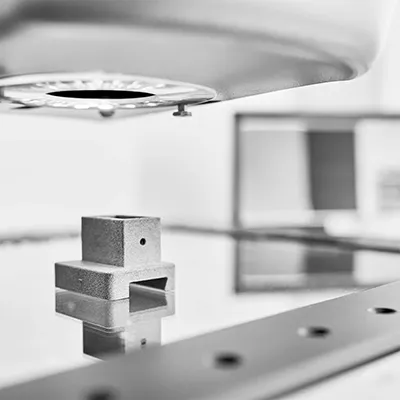
Modern Testing Technology
Additive manufacturing allows for the production of highly complex geometries. We can test the vast majority of geometries in our quality management laboratory using modern measuring techniques.
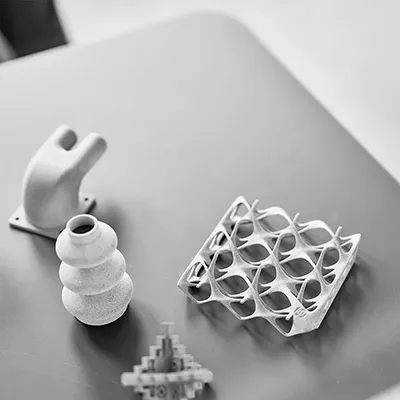
Individual Test Plans
In additive serial production, we often use individual, part-specific measurement protocols. This involves checking specific measurement points essential for the function of the parts or conducting functional tests. In addition to the types of tests, the agreed-upon sample size, up to 100% inspection, is determined.