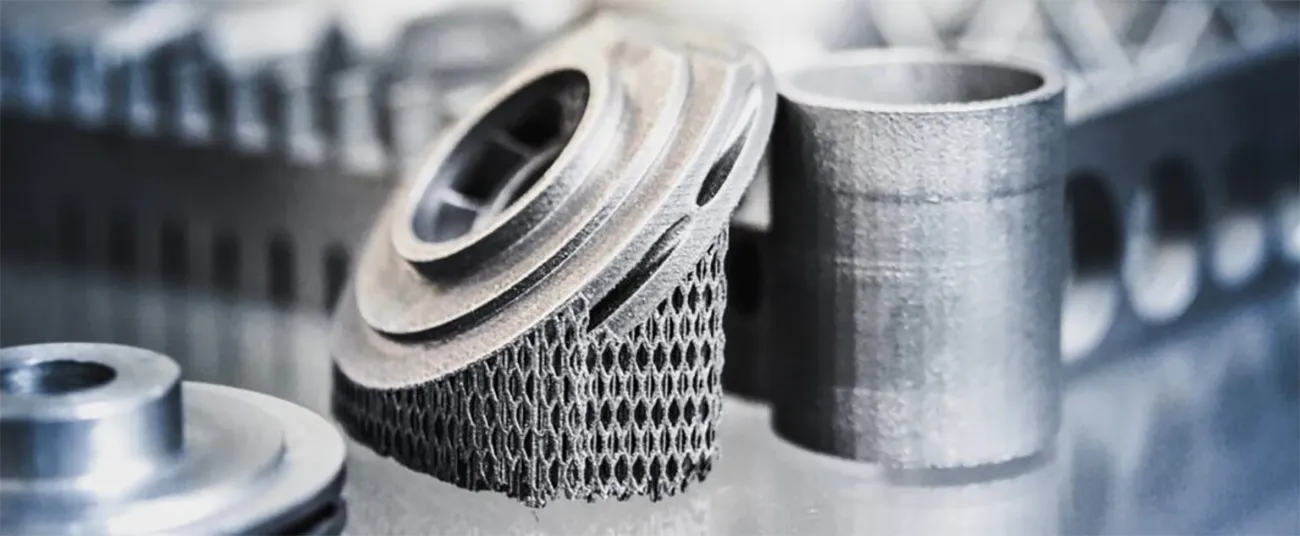
Additive manufacturing is constantly evolving. A significant part of this evolution involves technical improvements to existing processes. However, there are also innovations with the potential to revolutionize additive manufacturing. In the following article, we have summarized the current trends and analyzed their impact on the 3D printing market.
Plastics
In the additive manufacturing of plastics, developments focus on three main areas: improving component quality, reducing unit costs, and expanding the material portfolio. There are various technical approaches to achieve these goals. We introduce the latest innovations in photopolymer technologies (SLA/DLP), powder bed processes, and the entirely new STEP technology.
Photopolymer Technologies (SLA, DLP, and others)
Current Situation: Commonly found in the market are DLP (light source: projector) and SLA (stereolithography, light source: laser) systems. Currently, their throughput and cost-effectiveness are lower compared to powder bed processes (e.g., selective laser sintering, multi-jet fusion). Due to the support structures, only a single row of parts can be printed at a time. Printing parts on top of or inside each other, as is common with powder bed processes, is not possible with this technology.
Innovations: To catch up in terms of throughput, numerous manufacturers are working on significantly reducing production times while further improving the quality of parts. This effort particularly focuses on three areas:
- Light Source: Very fast systems use projectors or LED screens as light sources, enabling the entire layer to be exposed at once.
- Printing Process Speed: The current process works as follows:
- The print bed moves up by one layer thickness (usually 50 – 100 µm).
- New material accumulates between the print bed and the exposure window.
- The light source exposes the surface.
- The process repeats.
⇒ In the future, the process will run simultaneously. In simplified terms, the print bed will move up at a constant speed while the surface is continuously exposed. A particular challenge is to ensure a constant layer of material during this process (i.e., preventing air pockets).
- Printing Process Monitoring: Monitoring and dynamically adjusting printing parameters to optimize part quality.
Current Approaches by 3D Printer Manufacturers:
Nexa3D
Sie sehen gerade einen Platzhalterinhalt von Standard. Um auf den eigentlichen Inhalt zuzugreifen, klicken Sie auf den Button unten. Bitte beachten Sie, dass dabei Daten an Drittanbieter weitergegeben werden.
Weitere InformationenSource: YouTube/NEXA3D
The company has developed a 3D printer capable of achieving up to one cm/hour in the Z-direction, even with a full build volume. This currently represents the absolute speed record.
This is achieved through the use of the company’s proprietary “Lubricant Sublayer Photo-curing” (LSPc) technology. The company claims to be able to print six times faster and with a two-and-a-half times larger volume.
3D Systems
Sie sehen gerade einen Platzhalterinhalt von Standard. Um auf den eigentlichen Inhalt zuzugreifen, klicken Sie auf den Button unten. Bitte beachten Sie, dass dabei Daten an Drittanbieter weitergegeben werden.
Weitere InformationenSource: YouTube/3D Systems
With the Figure 4 3D printing system from 3D Systems, the innovation lies in the automation of the printing process. Multiple print platforms can be loaded and parts can be removed via robotic systems. This significantly increases the system’s throughput.
Origin
Sie sehen gerade einen Platzhalterinhalt von Standard. Um auf den eigentlichen Inhalt zuzugreifen, klicken Sie auf den Button unten. Bitte beachten Sie, dass dabei Daten an Drittanbieter weitergegeben werden.
Weitere InformationenSource: YouTube/Origin
Origin is taking a different approach; instead of focusing on speed, the company emphasizes accuracy and repeatability. The company’s proprietary “Programmable Photopolymerization” (P3) technology relies on numerous sensors that continuously adjust printing parameters during printing to ensure optimal quality.
Potential Impact on the Market:
- Lead Times: Higher speeds significantly reduce production times. Lead times can be reduced from days to hours. Especially in the medical and orthopedic sectors, where custom products are needed, this can lead to a significant acceleration of manufacturing processes.
- Mass Production: Output increases due to higher production speeds and automation, but limitations regarding material selection and part geometry must be considered.
- Quality: Increasing process replicability makes the processes ‘production-ready.’ However, there are limitations on the material side (thermoplastics cannot be processed) and in geometry (undercuts may be challenging to implement due to support structures).
Powder Bed Technologies
Current Situation: Plastic processing methods using a powder bed are currently the most productive 3D printing processes. However, compared to conventional manufacturing methods such as injection molding, the throughput is relatively low. Economically viable quantities are usually several hundred to a few thousand parts before injection molding demonstrates its strengths.
Innovations: The focus here is also on increasing productivity. Since powder bed processes can process thermoplastics unlike photopolymer systems, the industrial relevance of the processes is very high. Consequently, there are currently numerous ‘big players’ in the industry introducing innovations to the market.
Current Approaches by 3D Printer Manufacturers:
HP
This is achieved through higher working temperatures, which also expand the material range of the process to industrially relevant polymers such as TPU and polypropylene.
EOS
Farsoon
Sie sehen gerade einen Platzhalterinhalt von Standard. Um auf den eigentlichen Inhalt zuzugreifen, klicken Sie auf den Button unten. Bitte beachten Sie, dass dabei Daten an Drittanbieter weitergegeben werden.
Weitere InformationenSource: YouTube/Farsoon Technologies
The Flight technology achieves higher printing speeds by using a 500 W (!) fiber laser instead of a typical 30-70 W CO² laser. Such lasers are normally only used in metal 3D printers. Farsoon states that their Flight technology is up to four times faster than conventional SLS processes. The scanning speed of Flight technology is up to 20 m/s. For comparison, an EOS Formiga has a scanning speed of approximately 5 m/s (both manufacturer’s specifications).
The printer is expected to be officially presented at Formnext 2019.
Potential Impact on the Market:
Compared to injection molding, 3D printing of plastics becomes increasingly competitive even at higher quantities, leading to more and more mass production with additive processes. The availability of more materials beyond the popular PA 12 further increases the attractiveness of 3D printing for mass production.
Selective Toner Electrophotographic Process (STEP)
Current Situation: The pure manufacturing time (excluding setup times) in 3D printing is not yet competitive with injection molding for very large quantities.
Innovation: STEP is a completely new technological approach to 3D printing inspired by offset printing in the 2D field.
Current Approaches by 3D Printer Manufacturers:
Evolve Additive Solutions, a spin-off of the 3D printing giant Stratasys, is working on a completely new technology called STEP. The basis for their approach is the use of an electrostatically charged roller, similar to those used in current photocopiers. However, instead of printing on paper, objects are built up layer by layer in three dimensions.
According to the manufacturer, much is to be expected from this technology: isotropic material properties, a wide variety of usable materials, enormous production speeds (50 times faster than the currently fastest methods), and minimal piece costs. The market launch is currently planned for the end of 2020.
Potential Impact on the Market:
If the manufacturer’s claims prove to be true in practice, this system would indeed represent a revolution in additive manufacturing and would open the door to mass production very wide.
Metals
Metal 3D printers allow for the tool-less production of geometrically complex components in very short lead times. However, due to the high acquisition costs, low printing speeds, and expensive peripherals, the piece costs are still very high.
Furthermore, in additive metal manufacturing, somewhat exaggeratedly expressed, only a rough part is produced, often requiring post-processing with conventional (mostly CNC) production methods.
Therefore, the innovation focus in metal 3D printing is on reducing piece costs while simultaneously improving quality.
Laser-based Systems
Current Situation: In laser-based metal 3D printing, post-processing steps (turning, milling, grinding, etc.) are usually still necessary due to the process, so that the surfaces have an appealing quality. Furthermore, printing speeds are currently relatively low, making metal 3D printing relatively expensive and time-consuming.
Innovation: Reduced production times and better surfaces through the use of a multi-level printing system or through better integration of software and hardware.
Current Approaches by 3D Printer Manufacturers:
Aurora Labs
Aurora Labs’ metal 3D printer is the first printer that can merge multiple material layers “at once” (Multi-layer Concurrent Printing (MCP)). Multiple individually adjustable lasers are used for this purpose. This pushes Aurora Labs into new dimensions in terms of printing speed in metal 3D printing. Currently, these printers achieve approximately 113 kg per day (compared to a few kg per printer with current systems). The goal is one ton of processed material powder per day.
The system is currently in the beta phase and is expected to be released to the market in 2019.
Velo 3D
Velo3D focuses primarily on software to increase the quality of produced components and reduce piece costs. Various areas are being improved, including importing STEP data instead of mesh data (reducing errors in conversion), and improved print simulation (according to the manufacturer, 90% success rate on the first print). However, the significant reduction in support structures is particularly advantageous for the printer.
Compared to established laser-based metal 3D printers, the volume of support structures is reduced by three to five times. This not only increases printing speed but also reduces the complexity of post-processing.
The printer has already been introduced to the market (2019).
Potential Impact on the Market:
Both manufacturers offer solutions that could reduce component costs and potentially increase component quality. While Velo3D offers an ‘evolutionary’ improvement over established systems, Aurora Labs’ process has the potential to be revolutionary. With potential production quantities of up to one ton per machine per day, this would exceed the current performance of laser-based systems by orders of magnitude.
Metal Binder-Jetting Systems
Source: HP
Current Situation: In metal binder-jetting, the metal material powder is “glued” together with a binder, giving it a “green state”. The part is then sintered in an oven. The process is relatively new and is currently only offered by two manufacturers (Digital Metal, ExOne). Other systems are in development.
Innovations: The available models are rather small machines; new systems are expected to enable mass production with significantly larger capacities. It should be noted that several manufacturers are working on such systems; we present the solutions from HP and GE as examples.
Current Approaches by 3D Printer Manufacturers:
HP
HP uses two print heads and a new binder that should only account for 1% of the part’s mass (compared to 10% in existing processes). Furthermore, unlike existing providers, de-bonding (removing the binder as a separate production step) is not necessary. The HP Metal Jet process is expected to be up to 50 times more productive than existing binder-jetting and sintering processes on the market.
GE
Source: GE
In recent years, GE has heavily invested in additive metal manufacturing, for example, through the acquisitions of 3D printer manufacturers Concept Laser (Germany, laser-based systems) and Arcam (Sweden, electron beam-based systems). With this combined expertise, the company is now also working on binder-jet systems for additive metal manufacturing. The current model ‘H2’ (in the image above the predecessor H1) is currently being tested, among others, by the engine and turbine manufacturer Cummings and is expected to be released to the market in 2021. This system also promises a multiple increase in production speed compared to laser-based systems.
Potential Impact on the Market:
Competition stimulates business; the “new” providers HP and GE are challenging the “established” ones such as ExOne, Digital Metal, and (soon) also Desktop Metal with their systems. The development leads to an ever faster and more cost-effective production of metal components. However, these are still limited to a size of up to approximately five cm. For larger components, the error rate sometimes increases significantly due to the sintering process, which does not proceed uniformly for large components.
Summary
For the next few years, three main trends can be observed among 3D printer manufacturers:
- Production speed increases and production costs decrease.
- Additional materials are expected to expand the applications of 3D printing.
- Better integration of 3D printing software with hardware.
About 3Faktur: 3Faktur specializes in 3D printing, rapid prototyping, and rapid manufacturing. We utilize HP’s Multi Jet Fusion technology and offer various materials for prototyping and series production. If you have any questions about your project, feel free to contact us.