To optimize a component for additive serial production, an adjustment of the construction is usually necessary. The respective 3D printing process needs to be taken into account. Thus, optimization for metal printing differs significantly from optimization for a plastic process.
3Faktur specializes in additive manufacturing using the Multi Jet Fusion process (MJF). To prepare your components for (small-scale) serial production, we offer construction optimization for this process.
Our Service: Optimization of Construction for the Multi Jet Fusion Process
In general, optimization is economically viable for functional components that are installed and produced in higher quantities. The optimization includes the following focal points:
- Improvement of Surface Quality: For visible components, surface optimization is advisable. This involves minimizing stair-stepping effects and production-related effects (such as the sink effect typical for MJF). Applying textures (e.g., leather or wood-like structures) can also be part of the optimization process.
- Achievement of Defined Accuracies: If high accuracies are required at specific locations on the component, optimization can be beneficial. This often involves conducting test series with different scaling factors and making targeted changes to the geometry (e.g., to minimize shrinkage effects) to achieve tighter tolerances.
- Expansion of Functionality of Components / Assemblies: The Multi Jet Fusion process allows for the production of highly complex components. Components or assemblies that are produced in multiple components and then assembled in injection molding can often be produced with fewer individual components in additive manufacturing. By optimizing the design of the parts, the desired component functionality can be ensured.
- Cost Reduction: For high order values, cost optimization can be beneficial. The potential savings depend heavily on the geometry and functionality. Possible optimizations include removing protruding elements (cheaper printing) or combining components into a group (savings in post-processing).
- Lightweight Design: Weight reduction is a frequently desired characteristic of additively manufactured parts. The Multi Jet Fusion process allows for the creation of highly complex structures (lattices, topologically optimized, bionic structures), as there are hardly any design limitations. The applied construction optimization primarily depends on the component’s function.
Further Information about Our Service:
- Costs: Billing based on effort; typical budgets range from low to mid-three-digit EUR amounts.
- Procedure: Submit the data to us (STEP + drawing). We will review the data and contact you if necessary. For more information, please visit our quote and ordering process page.
- Timelines: Deadlines depend heavily on the project. They can range from a few (1-3) days for less complex projects to several weeks if multiple iterations, tests, and customer inspections are required.
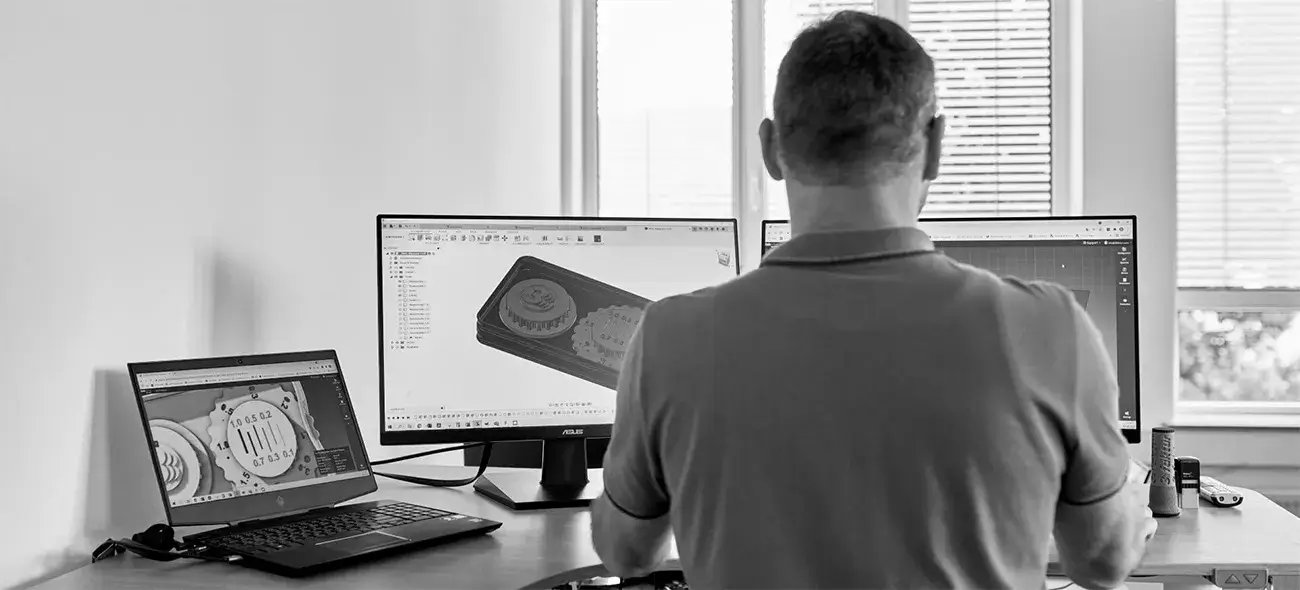
Resources: Tutorials and Guidelines for Additive Manufacturing Construction
Of course, you can also perform the optimization yourself. You can find online guidelines and tutorials on construction for additive manufacturing here.
When performing optimizations, we recommend creating multiple component variants and having them 3D printed and tested first. This way, you can ensure that the desired results are achieved in production.
If you have any questions, you can contact our technical customer service at +49 3641 225 910 020.