AlSi10Mg is an innovative aluminum alloy that stands out for its unique combination of strength and lightness. It consists mainly of aluminum, silicon, and magnesium, giving it outstanding mechanical properties. With high strength, low weight, and good corrosion resistance, AlSi10Mg is ideal for applications in aerospace, automotive, medical technology, and tool manufacturing. The alloy enables the production of complex geometries, fast prototyping processes, and efficient material usage, making it a preferred choice in additive manufacturing.
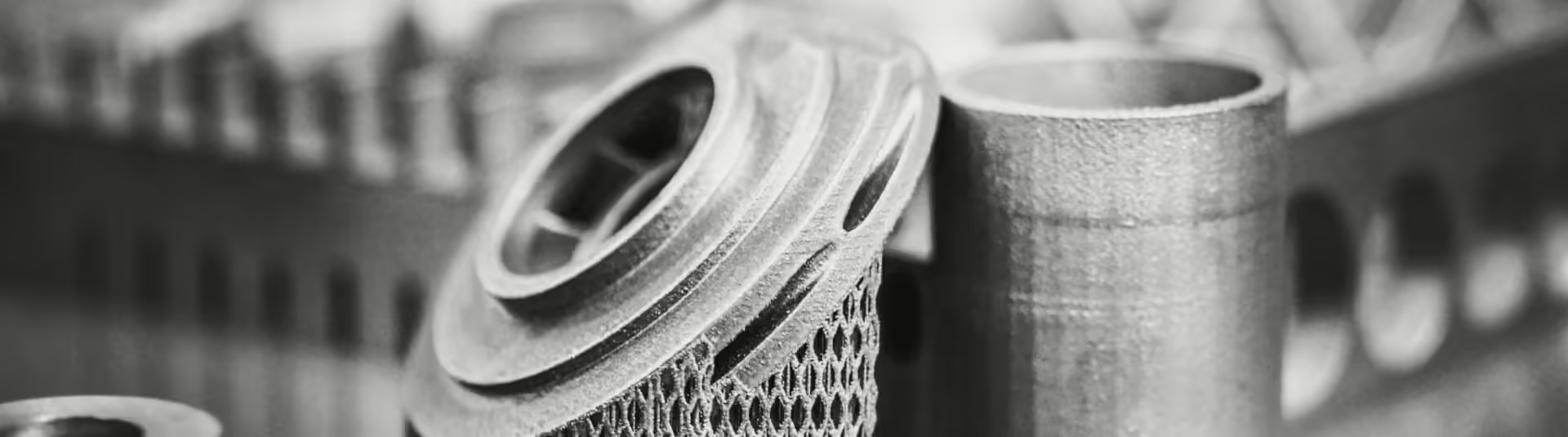
Key Info
Technology
Metal 3D Printing
Colors
–
Build Volume
150 x 150 x 150 mm
Production Time
approx. 10 working days
Accuracy
ISO 2678-1-m
Material Properties of Aluminum AlSi10Mg
Mechanical Properties
AlSi10Mg, an aluminum-silicon-magnesium alloy, is characterized by high strength and hardness combined with good ductility and toughness. These properties make it particularly suitable for applications requiring lightweight construction without compromising structural integrity.
- Tensile Strength: 418 ± 65 MPa
- 0.2% Yield Strength: 241 ± 31
- Elongation at Break: 4 ± 1 %
- Modulus of Elasticity: 73 ± 5 MPa
- Density: ~2.65 g/cm³
Downloads
- Material Data Sheet: AlSi10Mg Data Sheet
Manufacturing Tolerance
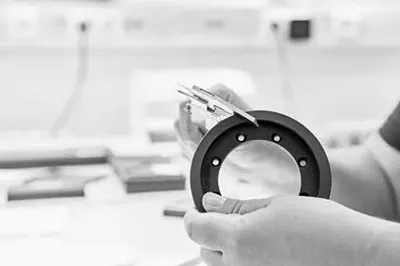
The general tolerance is according to ISO 2678-1-m.
Post-Processing
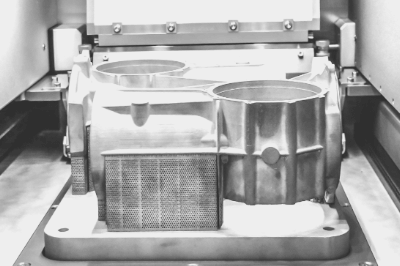
Standard: Support Removal & Blasting
For all manufactured parts, the support structures are removed. These are initially roughly removed and then manually ground. The contact points on the part are therefore visually noticeable.
Afterwards, the parts are blasted with glass beads, which improves the homogeneity of the surface and the haptic quality.
Optional: Additional Options
Post-processing options are varied and can be discussed with us on an optional basis. Examples include mechanical processing to achieve defined tolerances or surface roughness, heat treatment (e.g., stress-relieving), or surface finishing, such as tumbling.
Design Guidelines
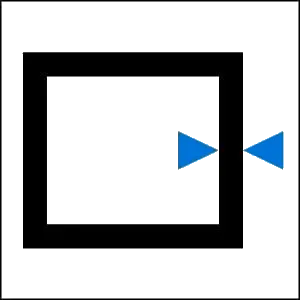
Minimum Wall Thickness
The minimum wall thickness should not be less than 0.7 mm. For longer objects/surfaces or objects exposed to mechanical stress, you should increase the wall thickness. Theoretically, wall thicknesses down to 0.4 mm are possible, but these may be damaged during post-processing (e.g., cleaning blasting). Therefore, in such cases, production is at your own risk.
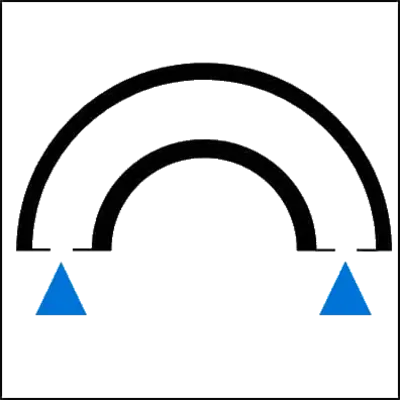
Hollow Structures
Hollow objects can be printed, but openings (min. 3 mm diameter) must be included to remove excess material. For larger cavities, you should plan multiple openings. The base material is compacted during the printing process, so excess material is very difficult to remove.
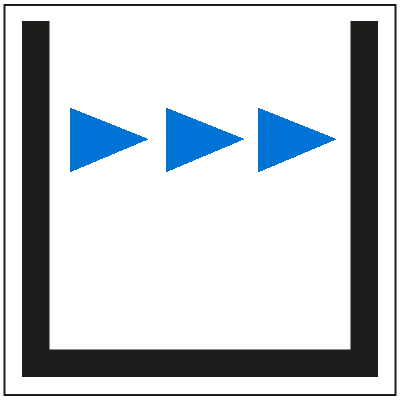
Gaps
Maintain a gap of at least 0.4 mm for grooves or closely spaced walls. Individual objects (“shells”) must always be uploaded as separate files unless they are firmly connected.
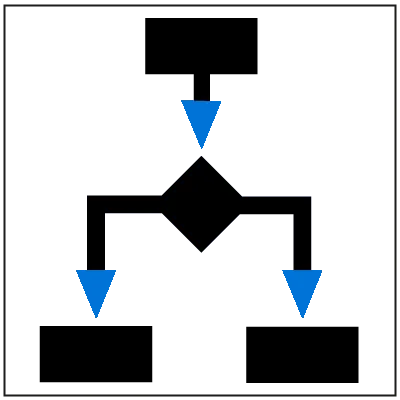
Resolution
Details up to a size of approx. 0.4 mm can be displayed.
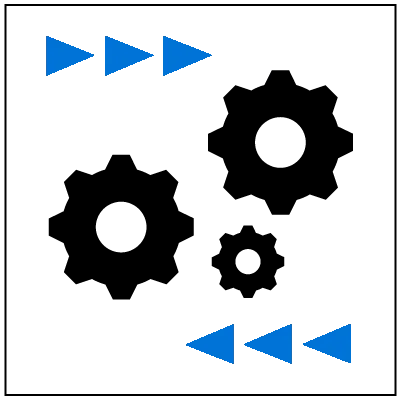
Geared Objects
Geared objects cannot be manufactured in powder bed-based 3D printing.
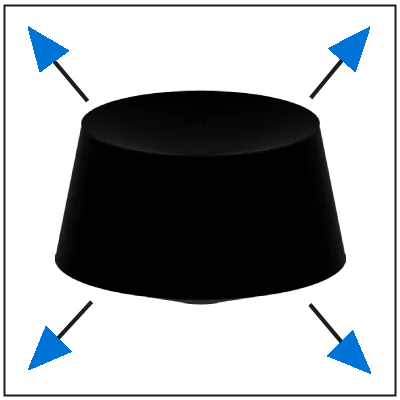
Size
The object should not be larger than 150 x 150 x 150 mm. Larger parts will be checked upon request.
Applications
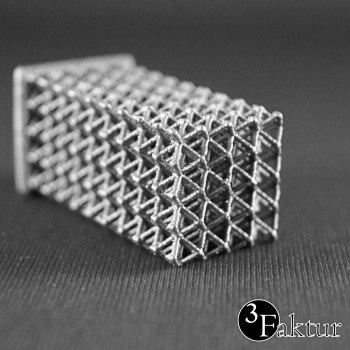
Lightweight Construction
Due to the optimal ratio of load capacity to weight, Aluminum AlSi10Mg is optimally suited for lightweight construction applications.
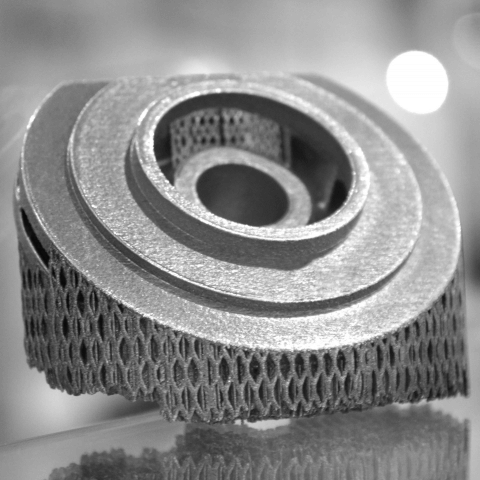
Prototypes
Aluminum AlSi10Mg, along with stainless steel 1.4404, offers an excellent price-performance ratio. Additionally, the 3D printing process with this material is simpler compared to other materials, as stress-relieving is generally not required. This enables cost-effective production of prototypes with short lead times.
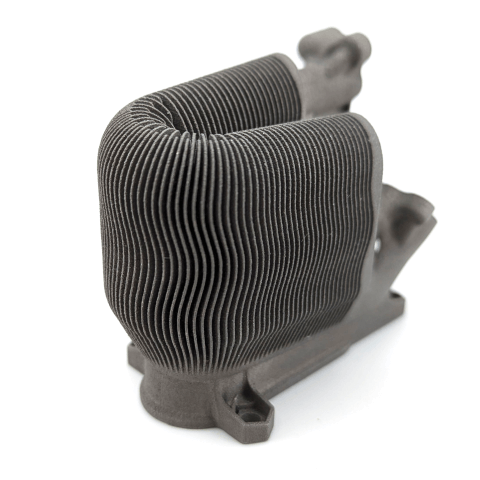
Cooling Applications
AlSi10Mg is characterized by high thermal conductivity, which is crucial for efficient heat dissipation in cooling applications. In addition, the alloy has good corrosion resistance and strength, which increases the durability and reliability of the components. Laser melting allows the production of lightweight yet stable structures that are specifically tailored to the requirements of cooling applications, further increasing efficiency.
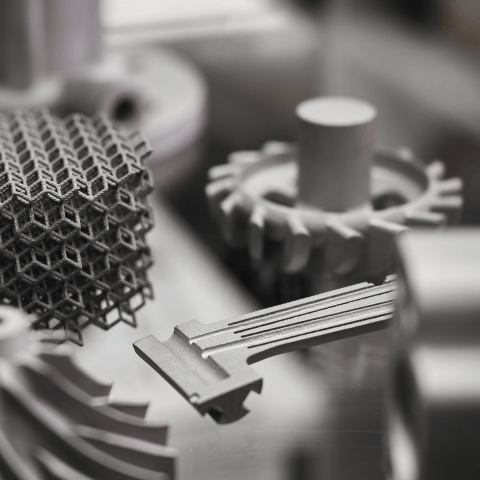
Other Applications
Due to its excellent property spectrum, AlSi10Mg is suitable for other applications:
- Automotive industry, e.g., engine, transmission housings
- Leisure and sports equipment, e.g., bicycle components
- Optics / Photonics, e.g., devices, instruments
- Robotics / Automation, e.g., distributors, housings
Pricing
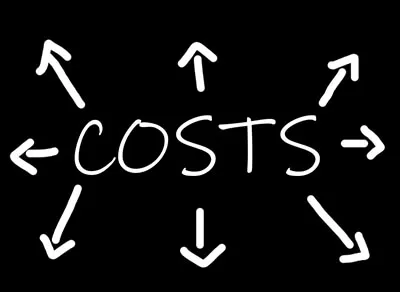
Quote
An instant price quote for metal 3D printing is not possible due to the complexity of the technology. Please use our manual inquiry function for your request. Your inquiries will be answered within one working day.
Calculation
Prices are primarily calculated based on machine running times and post-processing effort.
Minimum Order Value
EUR 50,- plus VAT (EUR 59.50 incl. VAT) per order
Discounts
For larger quantities, a reduction compared to the standard price is possible, depending on the quantity, part size, and geometry.