We are convinced that innovation is the key factor to stay competitive and offer our customers the best possible service as well as products of the highest quality and reproducibility. In numerous development projects, we have already developed a variety of innovative systems, software solutions, and artificial intelligence applications. We successfully use these in our daily business operations to make our processes more efficient and error-free.
In addition to our internal developments, we actively participate in publicly funded projects. In doing so, we work closely with leading companies and renowned universities at home and abroad to jointly drive innovation in additive manufacturing.
Below, we would like to introduce you to some of our exciting innovation projects:
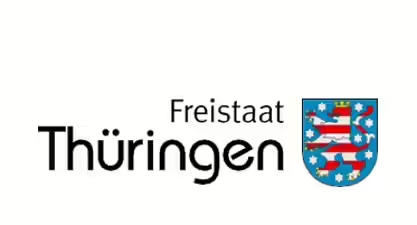
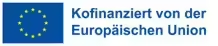
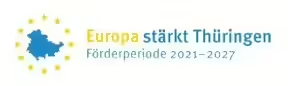
SLC – Development of a process for forgery-proof marking of additively manufactured components using laser beam embossed optical micro-elements
The aim of the project is to deliberately integrate structural elements into the near-surface area of additively manufactured components made of plastic and metal. Using a fast-moving laser beam, these elements will be deformed and their surface roughness selectively reduced compared to the surrounding surface. The location and sequence of the form elements contain binary-coded information, such as serial numbers or manufacturing parameters to increase traceability. Enhanced forgery protection is achieved through the three-dimensional shaping in combination with an innovative reading unit. The innovative marking process combines a special shaping process with a laser beam polishing process. Parts of the additively manufactured surface are ablated and polished simultaneously. The process creates form elements (e.g., concave reflection elements) that are distinctly different from the surrounding component surface. The low roughness of the form elements enables evaluation using optical measurement methods in reflection. These elements are referred to as laser beam embossed optical micro-elements.
Funding ID: 2024 VFE 0033
Project duration: 01.06.2024 – 31.05.2027
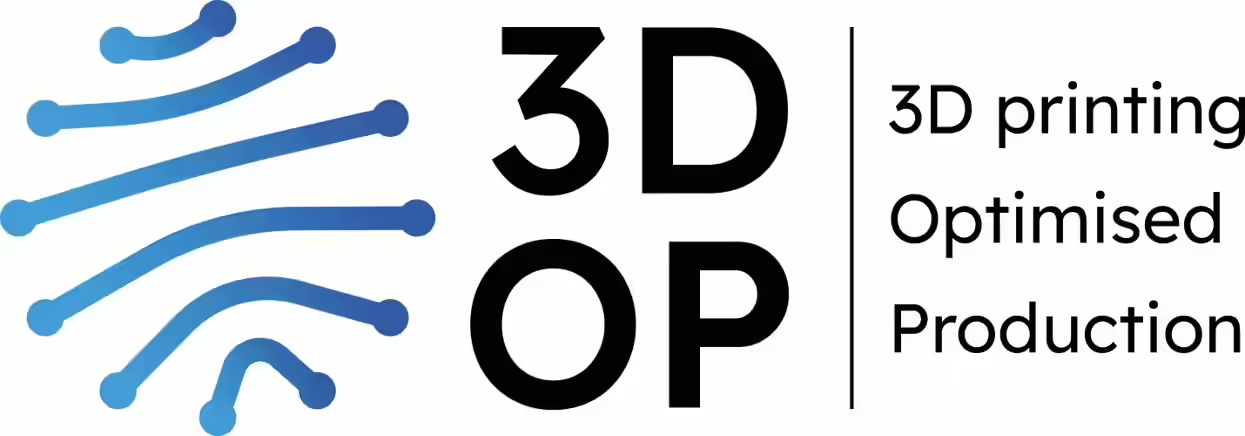
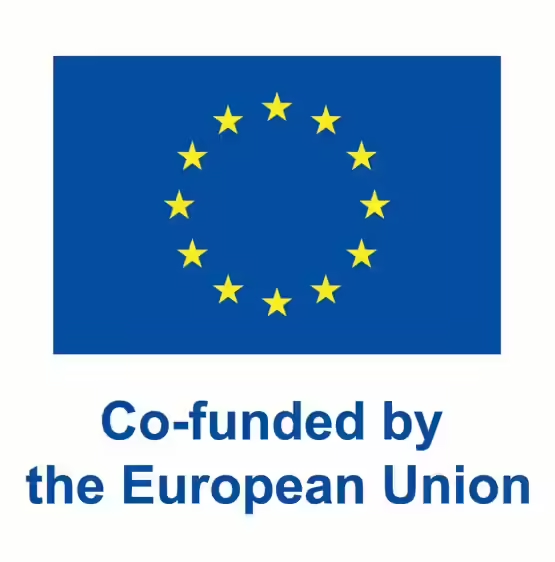
3DoP – 3D Printing Optimized Production
The 3DoP project aims to promote the spread of additive manufacturing as an innovative technology in SMEs. The intention is to address deficiencies identified as critical to the adoption of additive technologies in industry by facilitating investments at the interregional level, while also promoting partnerships and the international positioning of the participating companies. The project results will focus on four areas of technological innovation: printing of metal components, printing of components with integrated electronics, 3D printing of objects for use in the dental sector, as well as the automation of the 3D printing process and integration into industrial production lines.
Funding ID: 101083997
Project duration: 01.01.2023 – 31.12.2026
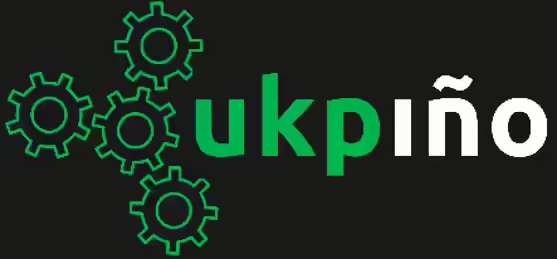
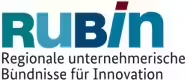
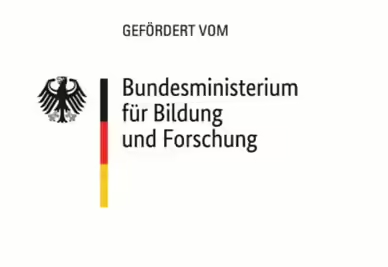
UKPino – Ultra-Short Pulse Innovation Platform for
Customized Applications
TP 3.2: USP Laser Sintered Plastic Components with Activated Electrically Conductive Structures
3Faktur is working on two key topics in this project:
1. The development of a prototype laser sintering test system that uses USP technology to additively manufacture high-resolution components from thermoplastics. The goal of the project is to produce miniaturized, complex components made of high-performance polymers or transparent thermoplastic materials for use in medical technology, robotics, sensors, and related fields.
2. The application of USP technology to integrate conductor paths into additively manufactured components. The goal is to produce fully functional components with complex conductor paths to simplify production processes, promote more sustainable production, and create entirely new product classes.
Funding ID: 03RU2U033B
Project duration: 01.06.2023 – 30.05.2026
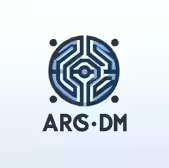
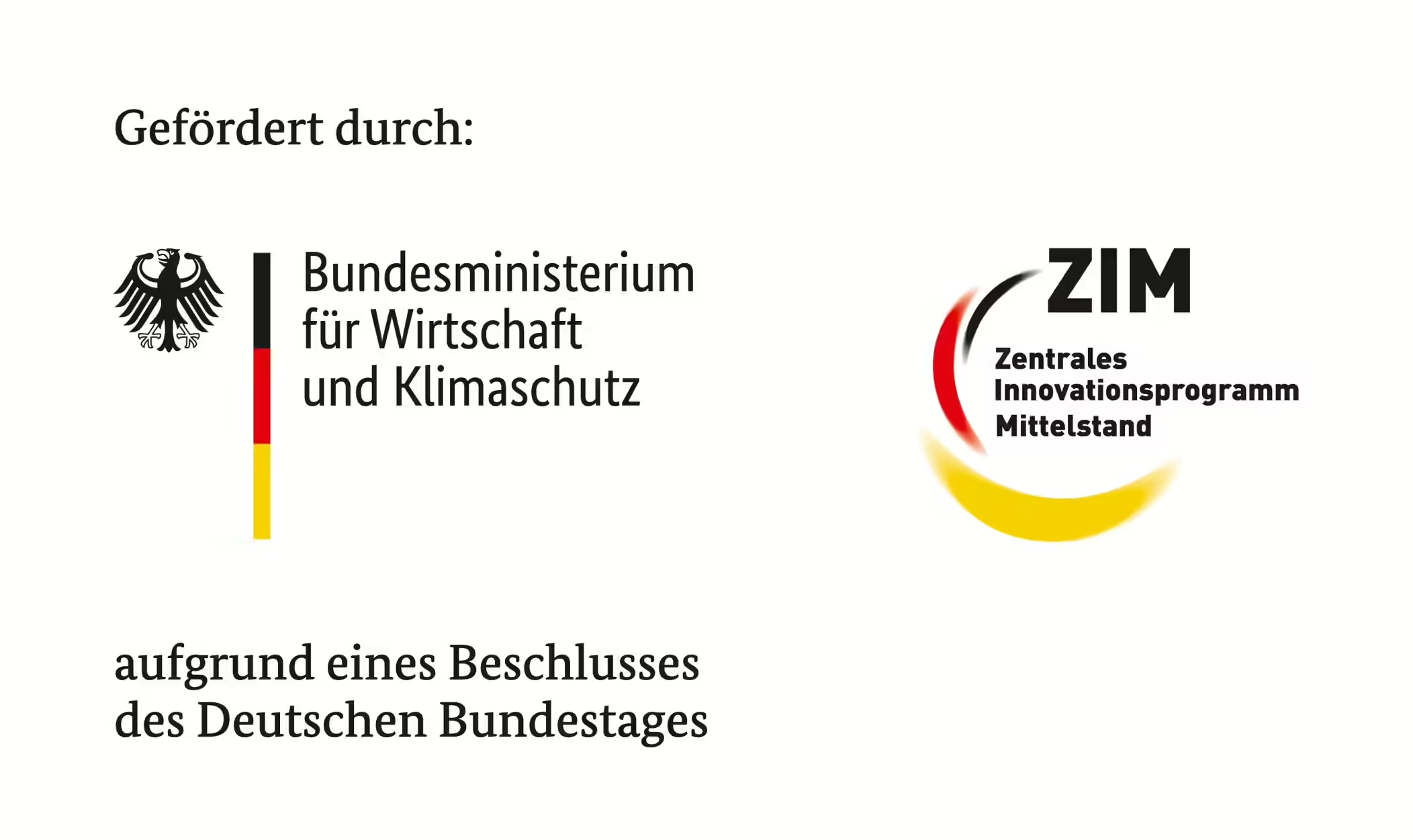
AROS-DM – AI-driven Resource Optimization for Sustainable Digital Manufacturing
Subproject: Coding, Automated Data Collection, and Development of Dynamic Nesting
The overall project goal is to increase resource efficiency in additive manufacturing. This will be achieved primarily by reducing waste and increasing packing density in build volume. The project aims to develop an AI algorithm that enables intelligent production control, dynamically controlled nesting, and optimization of resource use for a wide range of components. Machine learning methodology will be used as the basis for AI, with real data from produced parts and production runs, especially from batches, build volumes, and build jobs, serving as the foundation for training prediction models. Another innovation is the development of intelligent production control, based on the criteria of producibility, provision of optimized process parameters, and networked production planning. For the first time, invisible coding of parts will also be carried out during the 3D printing process, which will be decoded using a specially developed laser-guided thermography evaluation.
Funding ID: KK5350003KL3
Project duration: 01.07.2024 – 30.06.2026