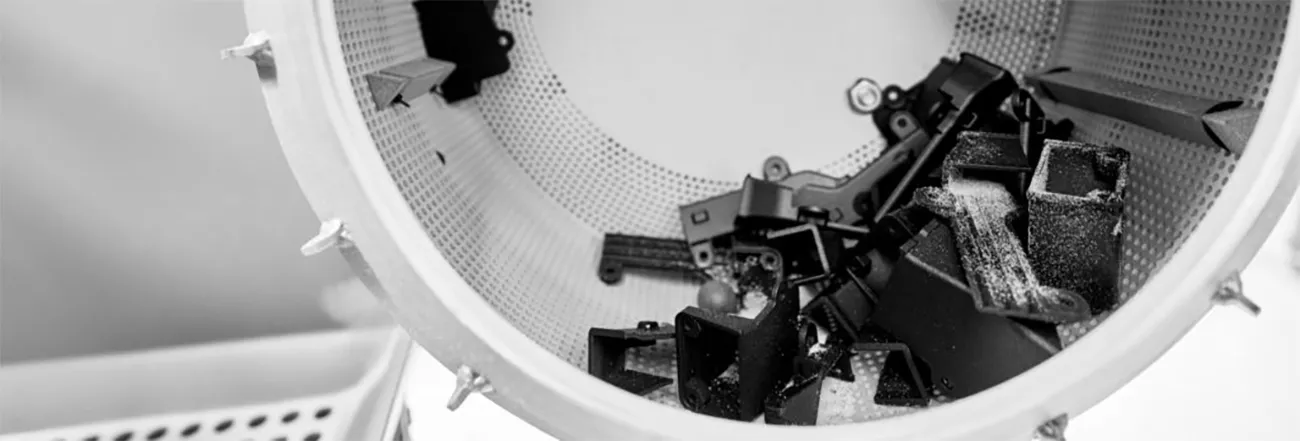
Initial Situation
The base material for additive manufacturing using the Multi Jet Fusion process is white plastic powder. During printing, the areas to be melted are mixed with black pigment and exposed to an energy source (infrared light). The black areas absorb more energy and melt, causing the powder particles to “fuse.” The white areas, on the other hand, remain in their original state.
On the surface of the components, the temperature is lower, so the grains melt together, but porosity (i.e., small pores) remains in the surface. The roughness of the surface is in the order of Ra 7 +/- 3 µm (depending on the printing orientation).
In addition, the Multi Jet Fusion process results in different colors of the interior and surface – the components are black on the inside and grayish on the surface.
Depending on the application and specific requirements for the components, various post-processing methods can be used to achieve desired modifications to the surface.
Shot Peening
The surface treatment results in modified mechanical properties, particularly compaction and increased scratch resistance of the surface, as well as improvement in aesthetics and tactile properties of the components.
The Process
After cleaning with glass beads, a second blasting pass follows. Plastic balls are usually used in the compaction blasting pass. These balls are larger than the glass beads and more resistant. That is, they do not break or break much when they hit the surface. The relatively large balls have high kinetic energy, resulting in a locally high temperature upon impact. As a result, the surface of the components is compacted (“pressed firmly”).
Achieved Modification
- The porosity of the surface is reduced.
- The surface becomes slightly glossy (the components are matte when untreated).
- The homogeneity of the surface is the best compared to all other methods.
- The roughness (Ra value) is only minimally reduced.
Figure 2: Two sample plates, left without and right with shot peening. Source: 3Faktur
Application
Application in visible parts: Due to the high homogeneity, the appearance and feel of the components are very good.
Shot Peening at 3Faktur
3Faktur applies this process as standard to all black-colored components. Separate ordering is not necessary.
Vapor Smoothing (“Chemical Smoothing”)
The treatment results in compacted and smoothed surfaces. Vapor Smoothing gives products a tactile and visual appearance similar to injection molding.
The Process
In chemical smoothing, the parts to be processed are exposed to evaporated solvent in a closed chamber. This melts the surface to a few µm. Irregularities are smoothed out and pores are closed. The result is a very smooth, practically pore-free surface.
Achieved Modification
- Very smooth and glossy surface
- Very strong reduction of porosity
- Slight improvement in roughness (Ra value)
Figure 4: Examples of chemically smoothed components. Source: AMT.
Application
- Fluid and gas-carrying systems: high tightness of the components due to processing
- Medical applications (cleaning / disinfecting) or in cleanrooms: easy cleaning possible due to pore-free surface
- Visible parts: particularly in irregular geometries and small to medium-sized components, hardly distinguishable from injection molded parts
Vapor Smoothing at 3Faktur
This service can be added separately for black-colored PA 12 components. The processing costs approximately EUR 5 plus VAT for smaller to medium-sized components, with the price increasing accordingly for larger components.
Tumbling
Mechanical process for surface treatment to remove visible traces generated during manufacturing.
The Process
The components are placed in a vibrating container with abrasive bodies. During processing, there is relative movement between the workpieces to be processed and the abrasive bodies, resulting in the surface being “ground”. In contrast to shot peening and vapor smoothing, the tumbling process removes material from the surface.
It should be noted that the selection of equipment and especially abrasive bodies is very large. For optimal results, machine parameters, in the simplest case the processing time and intensity, as well as the abrasive bodies, are optimized for a geometry.
Achieved Modification
- Irregularities are minimized and surface roughness is greatly reduced
- The reduction in the Ra value depends on the selected abrasive bodies and processing time, typically resulting in a reduction in the Ra value of 30% to 50%
- Stronger smoothing is associated with significantly greater edge rounding
- The surface is more coloristically heterogeneous in the MJF process, and the intensity of black coloring varies at different points on the component depending on the processing strength.
Figure 6: Microscopic images (from left to right: 100x, 500x, 1000x) of untreated components (top row) and deburred components (bottom row). Source: 3Faktur, Ernst Abbe University of Applied Sciences Jena
Application
- Especially suitable for components benefiting from lower roughness
- Not the preferred choice for visible components due to color inconsistency
Gleitschliff at 3Faktur
This service can be booked separately for PA 12 components.
About 3Faktur: 3Faktur specializes in 3D printing, rapid prototyping, and rapid manufacturing. We utilize HP’s Multi Jet Fusion technology and offer various materials for prototyping and series production. If you have any questions about your project, feel free to contact us.