The previous chapters focused on DfMJF from the perspective of optimizing the functionality of the components and the basic requirements for 3D models to fully leverage the advantages of additive manufacturing. This chapter addresses how targeted DfMJF can reduce costs for 3D printing.
<- Go to Chapter 6 (Optimization of Accuracy)
Chapter 7: Cost Optimization
7.1 Volume Reduction of a Component
The key price factors in MJF are material usage and the space occupied in the machine (“machine volume” – see next section). Thanks to targeted design optimization for additive manufacturing, the volume (material consumption) can be reduced, thus reducing production time and costs.
The following strategies can be applied to reduce material volume:
- Removal of unnecessary elements: Structures that are not essential can be removed. Often, plastic parts are designed for casting or machining processes and include surfaces that are no longer necessary for 3D printing. The resulting geometries with high complexity, such as undercuts or free-form surfaces, can be easily implemented with 3D printing. See also: Topology Optimization.
- Hollowing out solid structures: We recommend hollowing out the model starting from a wall thickness of 10 mm. You have the following options:
- Hollowing with opening: Excess material is removed from the cavity.
- Hollowing without opening: Excess material remains inside. We can do this upon request.
- Hollowing with lattice structure: Material remains inside, and support structures are added to provide additional stability to the interior. The lattice structure can be added by us upon your request.
- The lattice structure is our standard process when you select the “allow hollowing” option. If you prefer pure hollowing, please let us know in the order messages.
- Hollowing out by us has no impact on costs! It improves quality!
7.2 Reduction of Required Build Volume
In the Multi Jet Fusion process, the build volume can be almost fully utilized with parts, typically between 50 and 250 pieces. Bulky components take up more space and therefore increase the price per part, as unused space is costly. A cost-optimized design for additive manufacturing (DfAM) therefore avoids voluminous structures.
Protruding or projecting elements significantly increase the “bounding box” of an object, resulting in inefficient use of the build volume and a significant increase in printing costs. Often, such elements can be sensibly removed or printed separately and then assembled. Depending on their function, foldable elements could also be considered, which are printed in a folded position and then unfolded (see Chapter 4). These approaches can significantly contribute to reducing the cost of 3D printing.
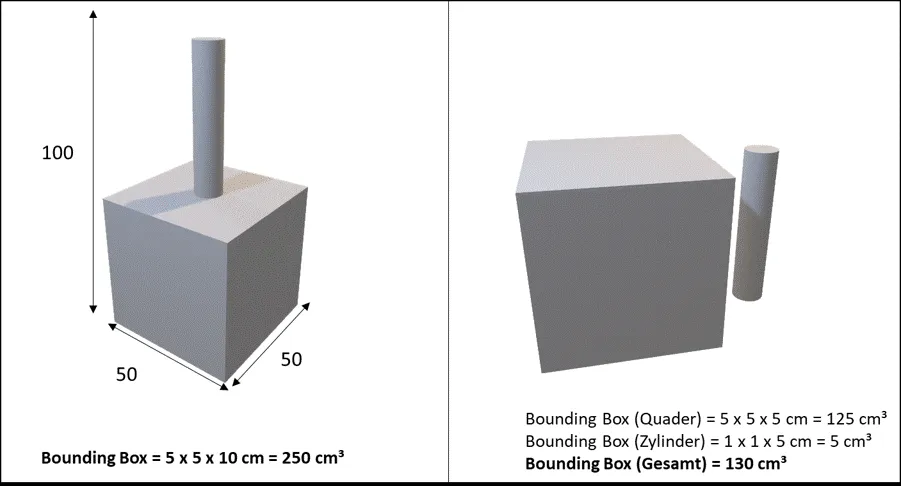
7.3 Use of Assemblies
The nearly limitless design freedom of the MJF process allows you to significantly reduce the number of components needed. This can be achieved by combining various components into few (even one) without reducing functionality. This reduces complexity and often saves weight and costs. Furthermore, fewer components need to be processed, resulting in additional cost reductions.