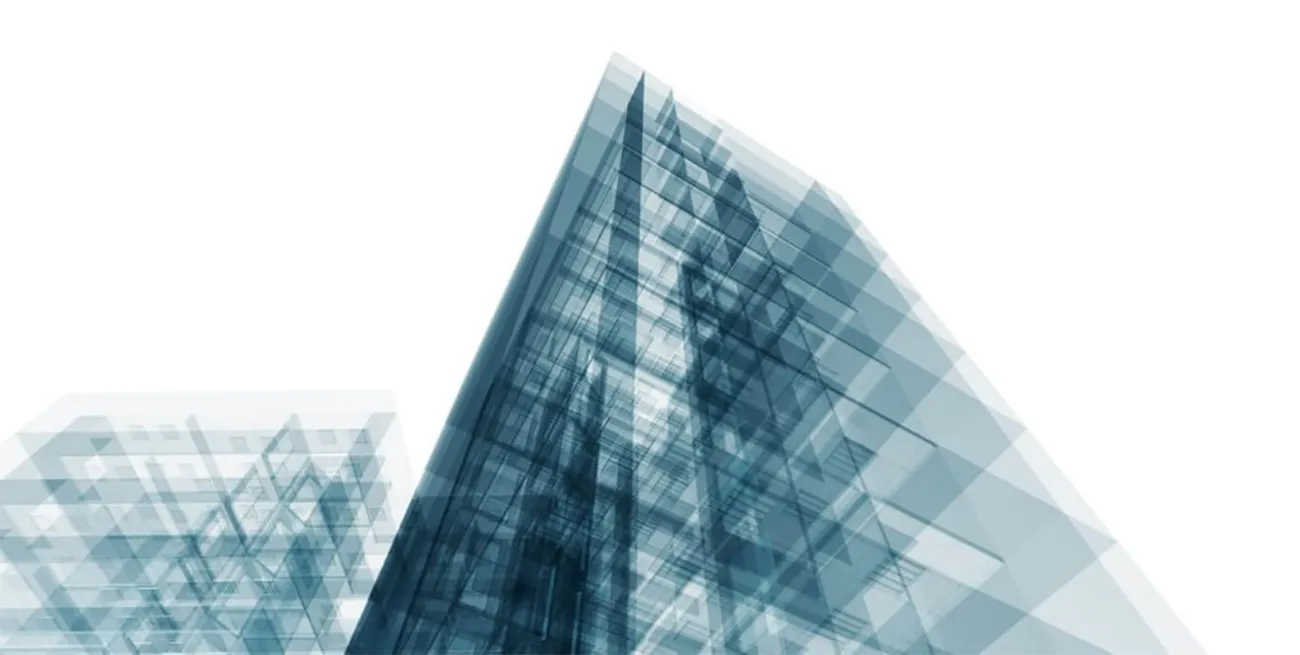
If you are moving in the world of 3D printing, you will inevitably come across a variety of different file formats (.OBJ; .3DS; .STL; .STP; .IGES; .3DM). From this variety, we have selected 2 file formats that we would like to explain in more detail: .STL and .STP. Both are widely used, and most of you will have dealt with them at one time or another.
STL
The .STL file format is the most commonly used format for 3D printing. Most rapid manufacturing machines can work with this format. The STL format represents the three-dimensional shape of a model using a large number of triangles. This is in contrast to CAD formats, such as the STP format (see below), where geometric bodies are defined by certain algorithms.
In detail, the file format includes a network of triangles and, for each of the triangles, the normal vector (which defines what is inside and outside) and the coordinates of the three vertices. A major advantage of the file format is that syntax errors are easy to recognize. However, the file format does not convey textures and is therefore only suitable for monochromatic models.
The difference between the mesh format STL and a CAD format like STP can be imagined as follows: in the STP format, for example, a perfect sphere is described by a formula. In the STL format, there is no sphere defined, only individual triangles with coordinates. So, if you want to export a sphere in an STL file (from a CAD program), a mesh of triangles representing the shape of the sphere will be calculated. This has two implications:
- Information content of the file format: The information (or formula) that it is a sphere is lost; only coordinates of triangles remain. In other words, exporting from STP to STL is not a problem, but converting from STL to STP is not straightforward. This can only be achieved through a process called ‘surface reconstruction,’ which involves partly automatic and partly manual conversion of the mesh to a CAD file. This is a very complex and often expensive process.
- Resolution: Most CAD files have default settings for resolution when exporting to an STL. The resolution of the STL corresponds to the number of triangles. The default settings are usually sufficient for straight structures. However, for curves or free surfaces, a finer resolution is often required to avoid the curves appearing blocky (see images below). The trade-off between resolution and file size needs to be considered. Conventional 3D printers cannot realize resolutions below 100 µm, so some ‘blockiness’ is acceptable.
Conversion of a sphere from STP to STL format with increasing resolution from left to right. The resolution is chosen based on the size and general complexity of the component. The two middle resolutions are sufficient for most components.
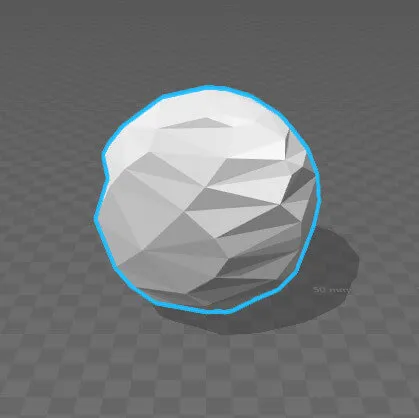
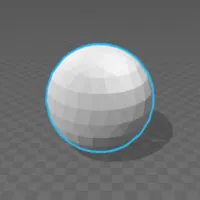
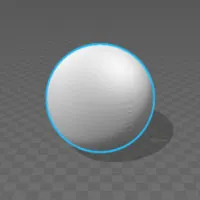
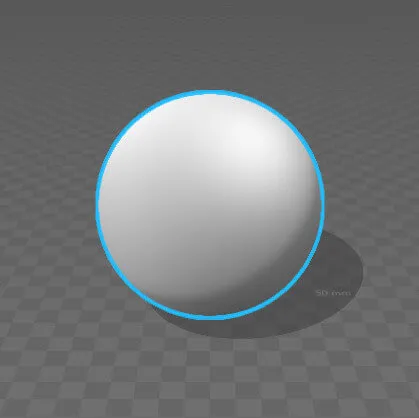
STP
The file format .STP is the file name extension of a standard for the exchange of product data (STEP) and much more complex than the STL format. The “STandard for the Exchange of Product model data” is a standard to enable the exchange of data between different CAx systems. The file format is standardized and updated by ISO 10303. The data can be modified over the different stages of product development since the dataset is very comprehensive. It includes information about tolerances, material properties, textures, material types, and topologies of the object. However, this makes the files of this format very large.
STP data is not directly 3D printed but converted into a mesh beforehand, i.e., STL. STP is the format of choice for transferring the files. This ensures that the conversion into a mesh only happens at the very last step (printing). If the conversion occurs too early, making changes to the model will be very difficult.
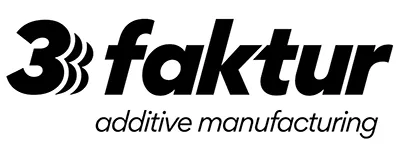
About 3Faktur: 3Faktur specializes in 3D printing, rapid prototyping, and rapid manufacturing. We utilize HP’s Multi Jet Fusion technology and offer various materials for prototyping and series production. If you have any questions about your project, feel free to contact us.