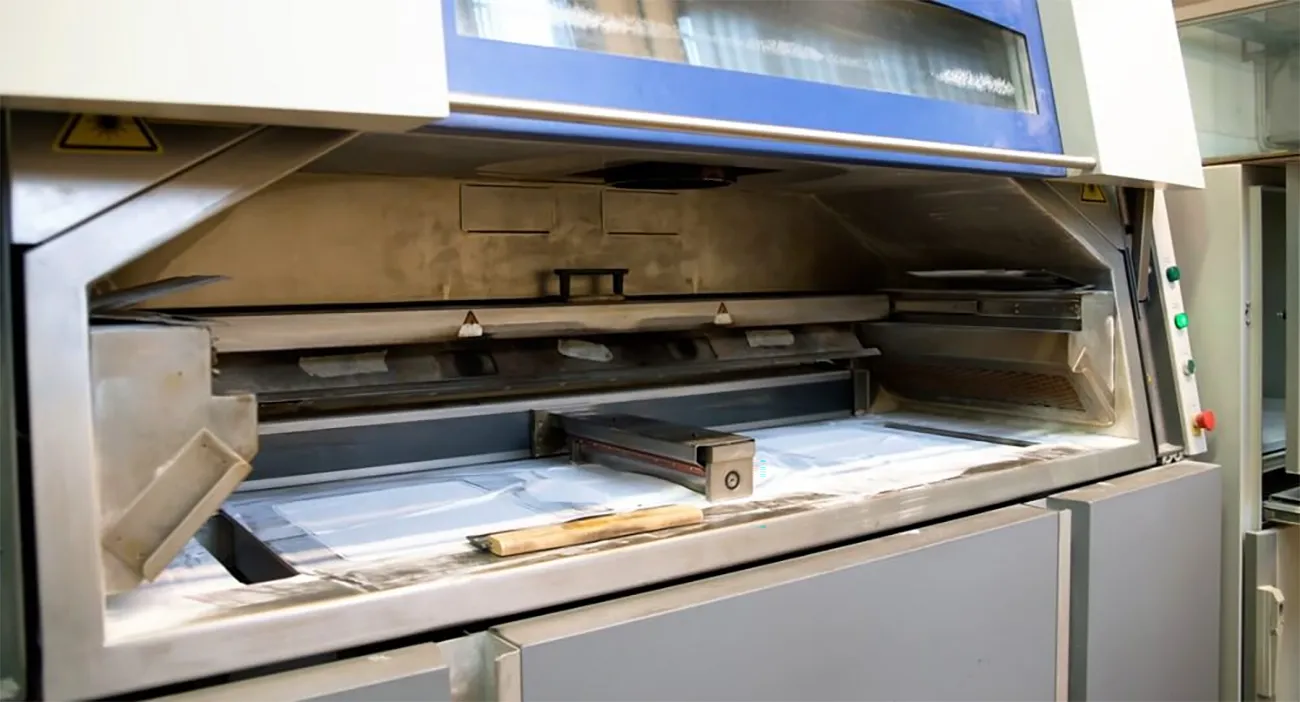
In our article Tolerances and Accuracy in 3D Printing, we provided general advice on what to consider regarding tolerance in 3D printing. As there are often questions specifically regarding tolerances and accuracy in laser sintering, we would like to focus entirely on this topic in this post.
In this post, you will learn about:
- When shrinkage occurs and its effects
- What to expect with curvatures in laser sintering
- Rounding, especially in holes and openings
- Considerations for the surface
- How sharp angles behave in laser sintering (SLS)
If you have any comments or questions, feel free to contact us via our contact form or call us at +49 (0) 3641 22591 000.
Shrinkage
Prior to laser sintering, the potential shrinkage of the workpiece is calculated. For larger models, this can be quite complex, as not all areas of the model are heated equally. Generally, the top side cools down less than the bottom side. Therefore, thick solid objects with a diameter larger than 10 cm are affected by shrinkage.
This can lead to two main issues:
Shrinkage in massive objects (large solid components, > 10 cm diameter)
If the surface area of the model per layer is too large (more than 8-10 cm in diameter), there will be more sintered powder present accordingly. These objects tend to shrink more than thinner objects. To counteract this, the workpieces are hollowed out, and the unsintered powder is left inside. The result has the same properties as a filled solid part but with the advantage of less shrinkage.
Curvatures in large, flat, and rectangular components (larger than 10 cm)
After the laser sintering process, outer surfaces cool faster than the core of the component, resulting in earlier contraction. As a result, the corners shrink more on the lower areas than in the middle, leading to slight curves at the bottom end. This is hardly noticeable in smaller pieces. To avoid this in larger objects, placeholders can be placed at the corners of the parts. These placeholders are solid and thus hot, causing less shrinkage of the material. This can lead to more accurate results.
Curvatures
As with any heat process, flat workpieces in 3D printing can experience curvatures. For example, a 1 mm DIN-A4 sheet might be curved at the ends after the process. To prevent this, the objects can be reheated and clamped cold. However, it should be noted that this process cannot be applied to all workpieces, as not all objects can be clamped.
Holes and Rounding
Roundness
Holes facing the Z-axis are generally round since the laser can draw a fairly precise circle. For holes smaller than 2 mm, powder can be trapped inside. Even if the powder does not sinter, it may get heated to a point where it solidifies, making it difficult to remove. In this case, it is recommended to work with a fine drill.
Holes that intersect the Z-axis are elliptical, especially when they are small (less than 5 mm). The hole is built up from straight lines (the layers), and therefore, a perfect circle cannot be created (similar to trying to build a circle using straight rectangular blocks). The holes are more elliptical at the top than at the bottom, as the laser cuts deeper through new powder than through sintered powder. By applying a so-called Z compensation, the downward-facing surfaces can be increased by a few tenths of a millimeter. However, since this still doesn’t make it perfect, it is advisable to do some post-processing with a drill.
Deep Holes
Small-diameter holes that extend deep into a solid part are often blocked with powder. The solid areas emit heat, causing the powder to solidify and making it difficult to remove. This can be a bigger problem, especially for holes with a diameter < 5 mm. Unfortunately, there is not much to do except for post-processing with a drill.
Surface
Surface Powder
The workpieces come out of the machine with a powder coating. This powder can be removed using a brush and an air compressor. If there is any powder left in holes at some small spots, it can be rinsed with warm soapy water or scraped out of the indentations.
Surface Details
It is possible that very delicate surface details cannot be realized during the printing process. Therefore, for details, a minimum thickness between 0.4 mm and 0.5 mm should be maintained.
Angles
With a model featuring sharp edges, inaccuracies in representation may occur. The reason for this is that the object to be printed must be divided into 0.1 mm thick sections. As a result, very sharp angles may not be fully represented. This can be avoided by transforming the edge into a flat end, which should be at least 0.4 mm thick.
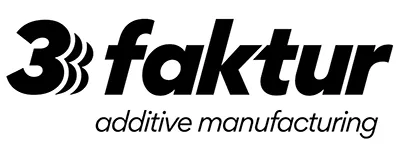
About 3Faktur: 3Faktur specializes in 3D printing, rapid prototyping, and rapid manufacturing. We utilize HP’s Multi Jet Fusion technology and offer various materials for prototyping and series production. If you have any questions about your project, feel free to contact us.