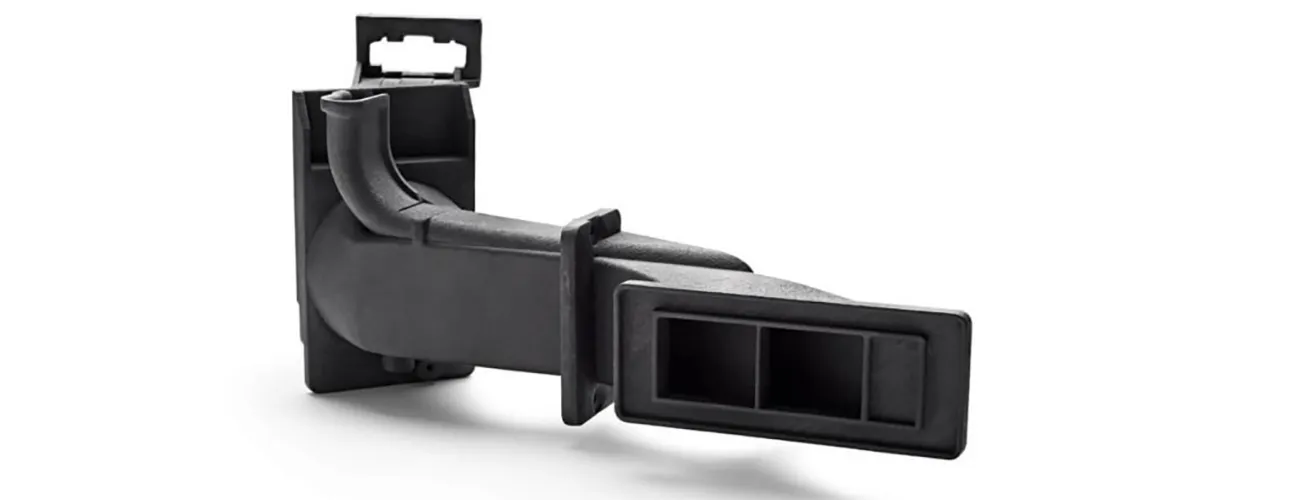
Image: HP Inc.
In the past, 3D printing objects were mostly used for rapid prototyping. The progress of additive technologies has led to an expansion in the use of prototypes. In the meantime, fully functional components can be produced which can no longer only be used as visual or test objects, but which can also be used in the final product. Hydraulic components have so far played an exception in this development, as watertight (fluid-tight) components could not be achieved with most additive manufacturing technologies. The HP Multi Jet Fusion process has closed this gap, as the manufactured objects are now largely watertight.
The differences in fluid tightness of HP Jet Fusion and Laser Sintering
We are comparing these two additive technologies for a simple reason: both use PA 12 as 3D printing material. The biggest difference is in the production method. The objects used in laser sintering are quite porous and therefore not suitable for use with liquids.
To achieve a certain degree of water tightness in laser sintered objects, resin can be used to infiltrate the part. The resin (e.g. epoxy) polymerises within the pores and close up the gaps.
It is not necessary to undergo this process step with HP Jet Fusion, as the material grains are fused together. Although Jet Fusion does not achieve a 100% material density, the gaps are negligible compared to laser sintering. The following figure shows the difference in density between PA 12 components created using the Multi Jet Fusion process and the PA 12 components which were laser sintered.
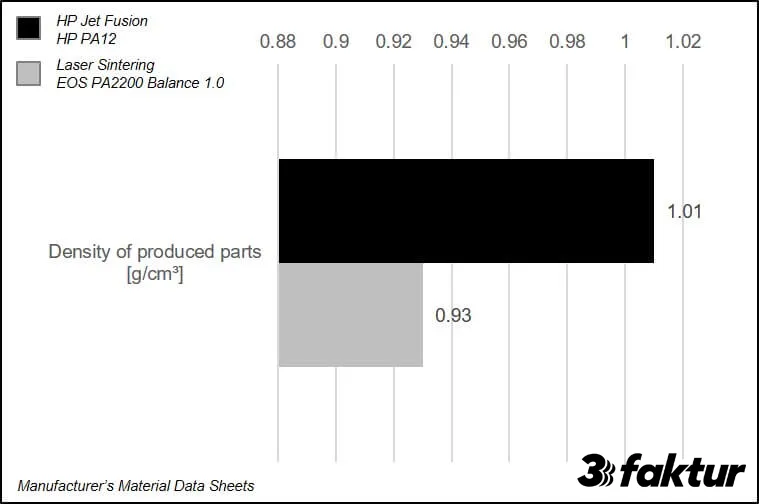
Image 1: Density [g/cm³] of HP Multi Jet Fusion and laser sintering parts, material PA 12. Source: Material data sheet HP HR PA 12; EOS PA2200
Influence of wall thickness and geometry
The liquid permeability of 3D-printed objects is significantly dependent on 3 factors:
- Wall thickness of the object
- Geometry of the object
- Pressure exerted on the object
Wall thickness: Not surprisingly, the wall thickness plays a decisive role in determining the pressure up to which the material is watertight. However, the wall thickness is not the only relevant factor, but the shape of the component is also important.
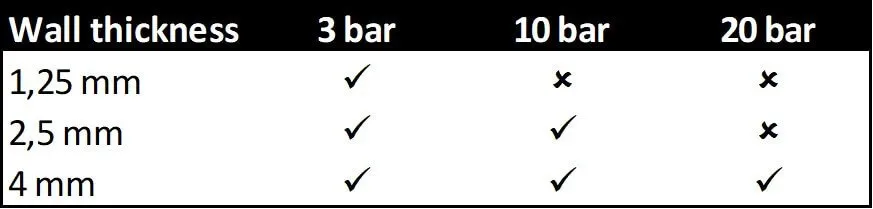
Table 1: recommended wall thicknesses for fluid vessels depending on pressure. Source: HP Inc.
Geometry: The shape of the object has a strong influence on the liquid tightness of 3D-printed components. While spherical objects can withstand pressures of up to 10 bar with a wall thickness of approx. 2.5 mm, a cubic object with the same wall thickness can hardly withstand pressures of even 3 bar. It is recommended to make the components as spherical as possible, as this means that the pressure on the walls is more evenly distributed.
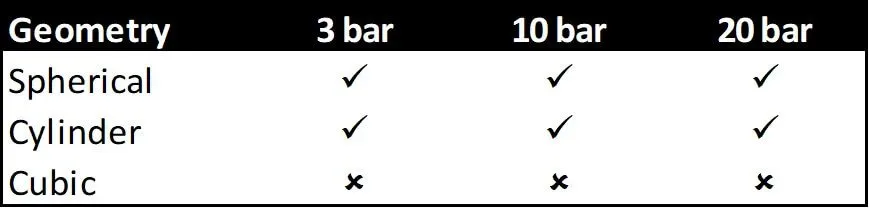
Table 2: recommended geometry for fluid vessels depending on pressure. Source: HP Inc.
Types of liquids which can be used
Liquid systems often use not only water but also a range of other chemicals. PA 12 is chemically resistant to commonly used chemicals, with the exception of aggressive acids such as chromic acid, nitric acid or hydrochloric acid.
The table below gives you a brief overview of the chemicals which can be used.
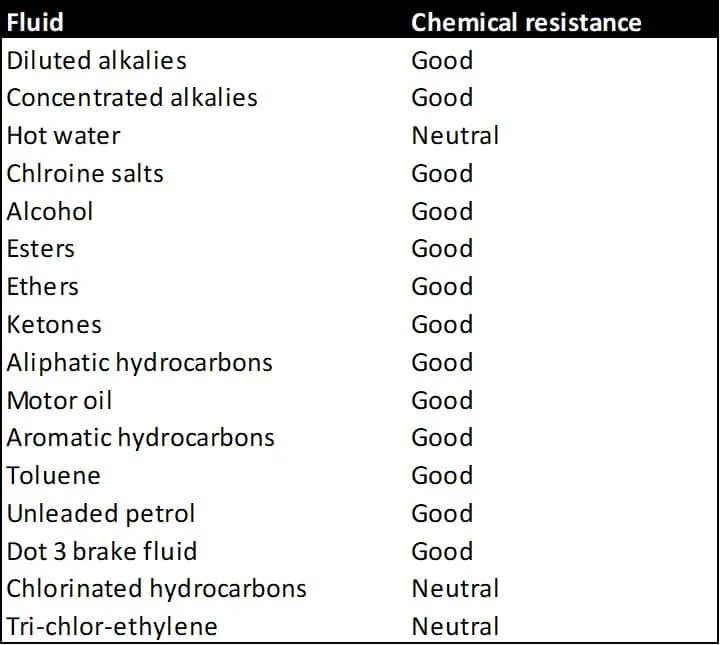
Table 3: Chemical resistance of PA 12 (HP Mutli Jet Fusion). Source: HP Inc.
Additional information
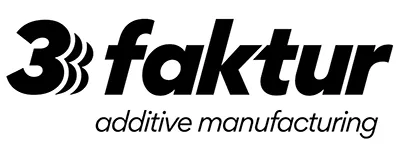
About 3Faktur: 3Faktur specializes in 3D printing, rapid prototyping, and rapid manufacturing. We utilize HP’s Multi Jet Fusion technology and offer various materials for prototyping and series production. If you have any questions about your project, feel free to contact us.