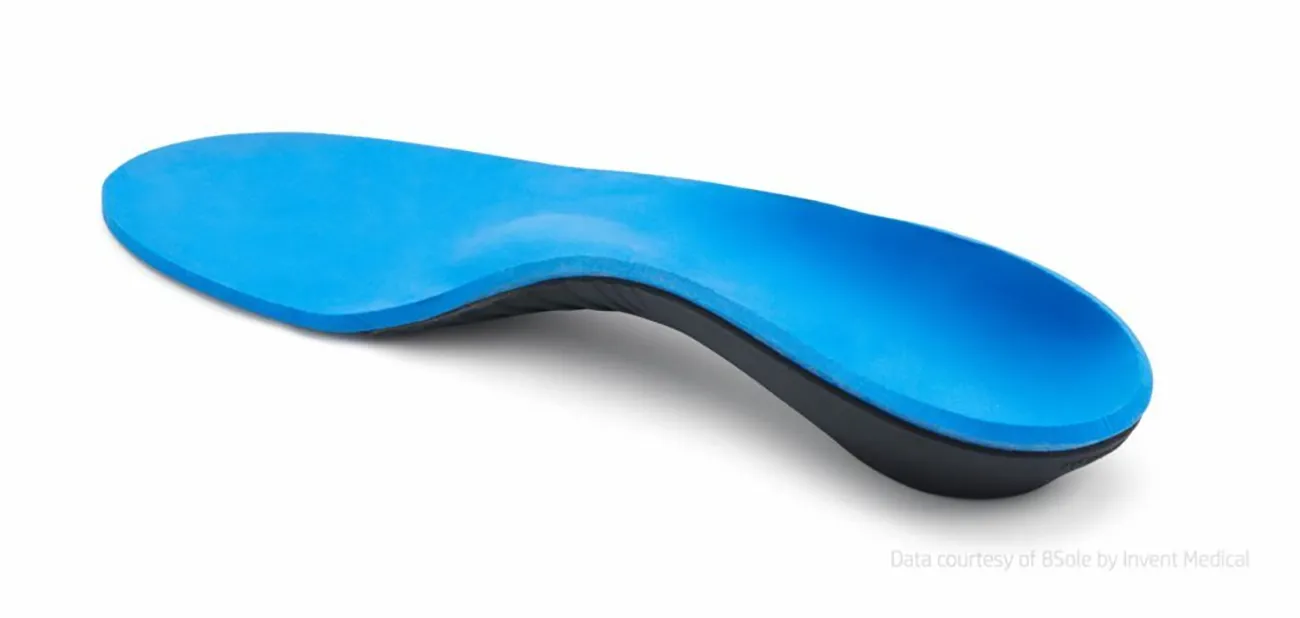
Foot injuries often have serious consequences for diabetics. Therefore, optimal footwear, including appropriate orthopedic insoles, is essential for people with diabetes. Personalized soles are not only important for diabetics but also for other medical conditions affecting stability and gait. Besides medically indicated cases, orthopedic insoles also offer opportunities to improve the situation for athletes and individuals seeking comfort for their feet in everyday life.
Both the increasing number of diabetics and the aging population are driving forces behind the growing market for orthopedic insoles. Another contributing factor is the rising number of runners. These factors are leading the insole market to grow at an annual rate of seven percent.
Traditional Production of Orthopedic Insoles
Currently, personalized insoles are mostly designed and made by orthopedists. The foot is molded with a special mass, and the “cast” then serves as a mold for producing the casted insole. For specific medical indications, the insoles are also handmade by orthopedic technicians. Another production method is CNC machining. The foot is scanned, and the sole is designed using a CAD program on a PC, and then it is manufactured using CNC milling. These production methods are relatively labor-intensive and produce a significant amount of waste.
The Future: Orthopedic Insoles through Multi Jet Fusion
First, the foot is scanned, and then a 3D model is created from it. Based on this 3D model, the personalized insole is 3D printed using the Multi Jet Fusion process.
Top left: Scanning of the foot by Invent Medical; Top right: Foot image by iOrthotics;
Bottom right: 3D model of the insole by Invent Medical; Bottom left: Finished insole by Invent Medical. Illustration: HP.
Economic Benefits
3D printing has elevated the production of individual healthcare products to a new level. The technology has the advantage of producing at a significantly higher speed and lower cost. The Multi Jet Fusion process, in particular, demonstrates its advantages. For patients, it is advantageous that usually only one visit is required to create the 3D model. Another advancement is that much less post-processing work is needed since the insoles no longer require deburring. The accuracy with repeated 3D printing is also improved compared to manual production (± 0.3 mm). The waste produced is up to 20 times lower than with subtractive methods.
Customer Benefits
Customers receive the product customized to their feet much faster. Additionally, additional functional elements can be incorporated into the insoles. For example, special, customized surface structures can increase wearing comfort and slip resistance. The rigidity of the sole can be adjusted according to the customer’s preferences by locally reinforcing the sole. 3D-printed orthopedic insoles also have a lower weight due to the omission of unnecessary structures. The insoles can also be printed in full color.
Practical Implementation
Some companies have already recognized the benefits of 3D printing for the production of orthopedic insoles.
- iOrthotics was able to triple the production of orthopedic insoles and reduce the delivery time by more than half by using the Multi Jet Fusion process. Furthermore, the waste generated during production was massively reduced.
- Invent Medical, in collaboration with 8sole, developed a lighter and more flexible everyday insole. The fast production and individual design increased customer satisfaction.
Orthopedic insole produced with Multi Jet Fusion; Image: iOrthotics.
Orthopedic insole produced with Multi Jet Fusion; Image: Invent Medical.
Summary
The use of the Multi Jet Fusion process for the production of individual orthopedic insoles brings not only significant economic benefits (cost reduction, increased production, waste reduction) but also significant advantages for customers. If you do not have your own 3D printing capabilities, it is advisable to use experienced 3D printing service providers (e.g., 3Faktur) to take over the production of orthopedic insoles.
About 3Faktur: 3Faktur specializes in 3D printing, rapid prototyping, and rapid manufacturing. We utilize HP’s Multi Jet Fusion technology and offer various materials for prototyping and series production. If you have any questions about your project, feel free to contact us.