Rapid Prototyping refers to the tool-less production of prototypes. It is often used synonymously with 3D printing and additive manufacturing. The chosen method for prototype manufacturing depends on the desired goal. We can differentiate between two main approaches:
- Rapid Prototyping for Conventional Manufacturing: The prototype serves a product that will not be additively manufactured in the later product lifecycle but will be produced using conventional methods such as injection molding, thermoforming, or machining.
- Rapid Prototyping for Additive Manufacturing: Additive manufacturing is applied during the product lifecycle, either in series production or at the end of life for spare part manufacturing.
Rapid Prototyping for Conventional Manufacturing Rapid Prototyping for Additive Manufacturing 3Faktur Quality Features
1. Rapid Prototyping for Conventional Manufacturing
The primary goal is to produce a prototype that closely resembles the serial product. To ensure this, we offer a versatile selection of materials, colors, and surface finishes.
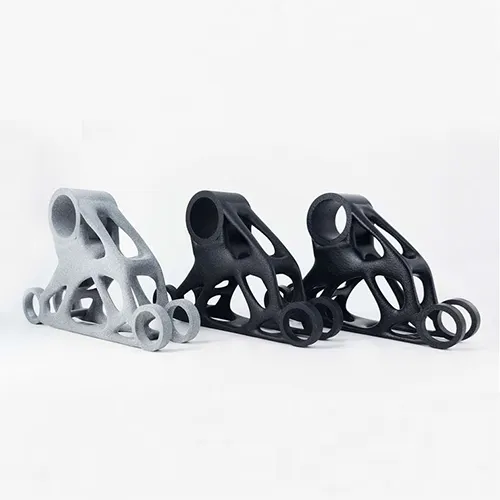
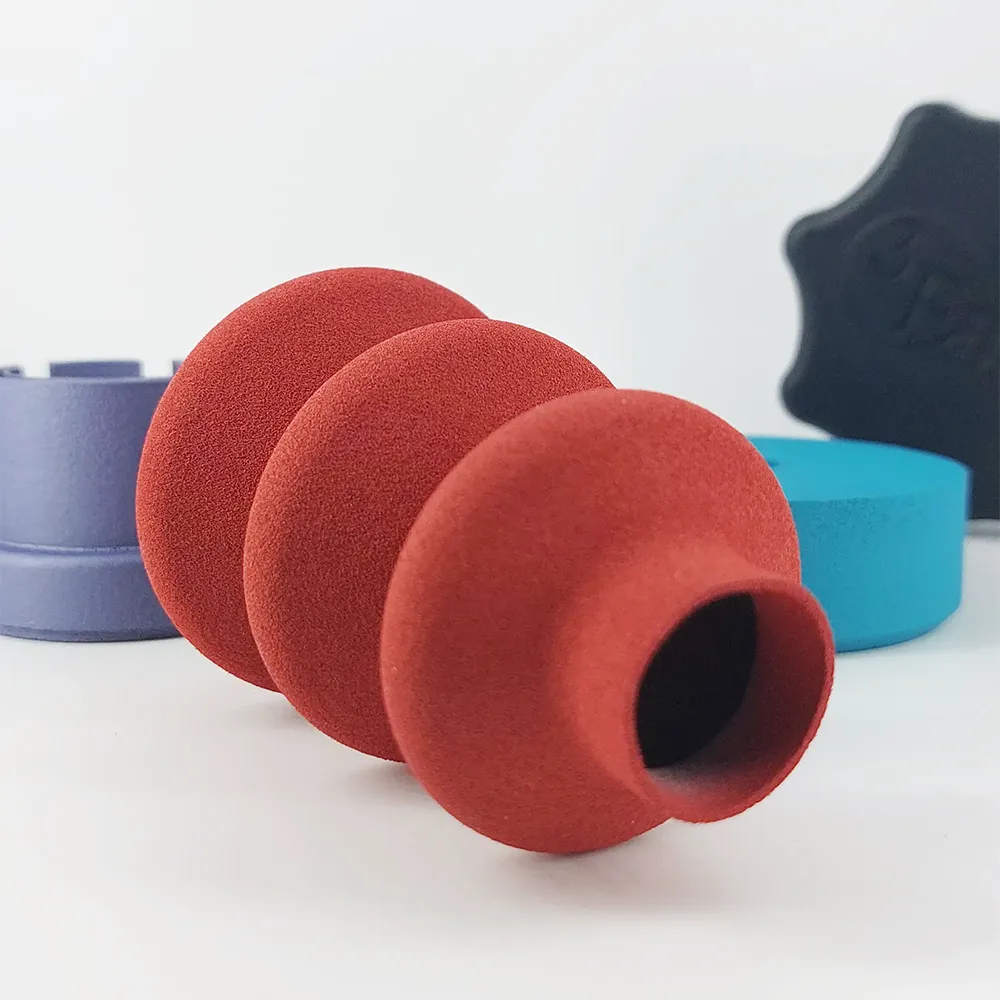
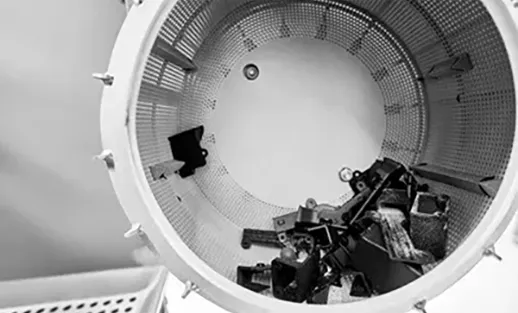
Materials
- PA 12: A high-performance all-rounder plastic, ideal for numerous industrial applications.
- PA 12 W: Similar properties to PA 12 but in a basic white color.
- Ultrasint TPU: An elastic plastic with Shore A 88 – 90. Deviating Shore hardnesses can be achieved by using grid structures.
- PA 11: A flexible engineering plastic for snap-fit connections, orthoses and dynamically loaded components.
Colors
- Color Dyeing: Dyeing of PA12, PA12W, or TPU parts.
- Painting: Coating (wet painting) of additively manufactured parts in standard (RAL) or custom colors.
Surface Finishing
- Shot Peening: This process is used to homogenize the surface and achieve a high-quality tactile feel. It is included in every coloring process.
- Vapor Smoothing: A chemical process for smoothing the surface.
A design specifically tailored to additive manufacturing is usually not necessary or even detrimental in such contexts. With our powder-based additive production technology (Multi Jet Fusion), we can efficiently manufacture products designed for injection molding. However, in certain cases, slight modifications may be necessary. These include:
- Adjusting wall thicknesses that are too thin (e.g., <0.7 mm for PA 12).
- Hollowing out or inserting lattice structures in particularly thick walls (e.g., >10 mm).
- Functional modifications, such as adjusting wall thicknesses for film hinges (possible with PA 12, PA 12 W) or inserting lattice structures to achieve specific Shore hardness values with TPU M95A.
Our service team is always available to discuss potential adjustments with you.
Rapid Prototyping for Conventional Manufacturing Rapid Prototyping for Additive Manufacturing 3Faktur Quality Features
2. Rapid Prototyping for Additive Manufacturing
During the product lifecycle, 3D printing is used at least partially. For an optimal design of the prototypes, two main scenarios can be distinguished: pure additive series production and the so-called hybrid production.
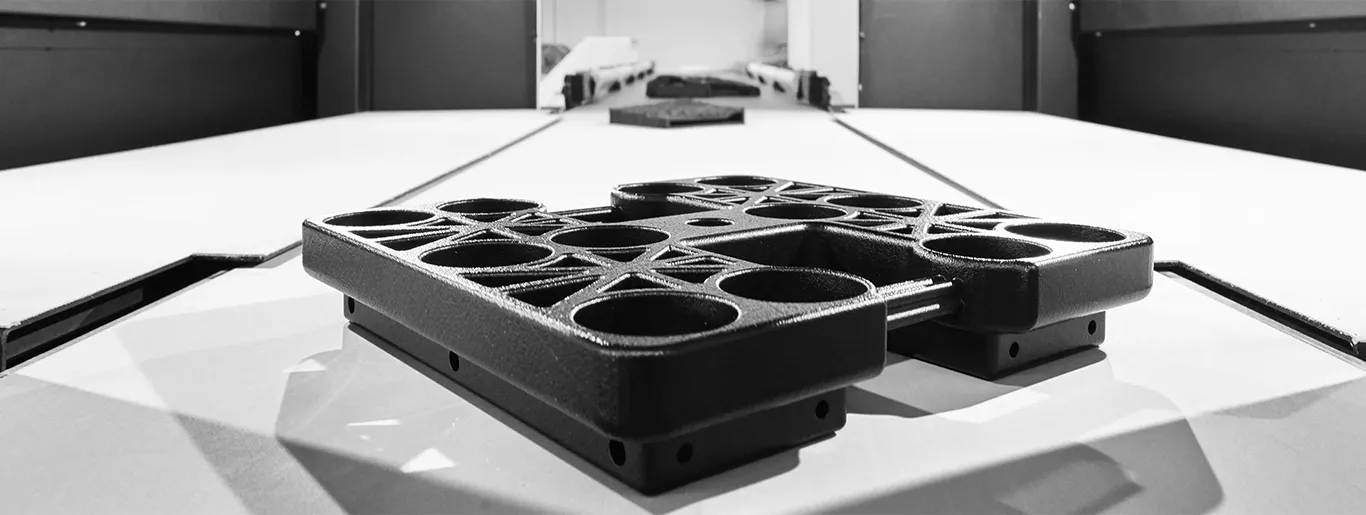
2a. Additive Series Production
In this case, components are additively manufactured throughout the entire product lifecycle. It is often recommended to optimize the design specifically for 3D printing, for example:
- Material reduction: Weight and material can be saved through lattice structures or topological optimization.
- Functional integration: This involves developing multifunctional components that previously consisted of multiple parts, such as:
- Consolidation of parts, for example, through joints or film hinges, to reduce assembly costs.
- Integration of channels for fluid or gas control.
- Introduction of movable elements to avoid subsequent mechanical components.
We are happy to support you in the optimization process. For more information on design optimization for additive manufacturing, please refer to our resources.
2b. Hybrid Production
Primarily produced through injection molding, a part is additively manufactured during the product lifecycle. Examples of use cases include:
- Bridge Production: Additive manufacturing bridges the gap while optimizing the injection molding tool.
- Peak/Upside Production: Additive manufacturing is used when demand exceeds the forecast, and additional capacity can be provided through 3D printing.
- Customization: For product variations in smaller quantities where injection molding would be uneconomical.
- Spare Parts: Instead of traditional inventory management, spare parts can be printed on-demand.
For these cases, 3D printing adjustments are recommended. However, the extent of adjustments depends on the strategy implemented in the product lifecycle:
- Replication of Injection Molding Design: The 3D-printed component resembles the injection-molded one. This solution is often used for invisible or non-stressed parts, considering that the surface structure and potentially the material may differ. It is frequently employed in the spare parts sector.
- Compromise Solution: The design functions well in both injection molding and 3D printing. This often involves specific surface structures (e.g., “leather texture”) that can be created in both processes, thereby concealing any differences. This is particularly effective in Bridge or Upside Production scenarios.
- Parallel Solutions: Separate designs for both processes. For example, additive manufactured versions may include integrated components that consist of multiple parts in injection molding. This approach offers flexibility throughout the entire lifecycle, whether it is in Bridge Production, Upside Production, or the realm of spare parts.
Choosing the best design approach for a hybrid supply chain is not trivial. We are here to provide you with advisory support.
Rapid Prototyping for Conventional Manufacturing Rapid Prototyping for Additive Manufacturing 3Faktur Quality Features
Why Rapid Prototyping with 3Faktur?
3Faktur is a service provider for the additive manufacturing of industrial plastic components. Since 2014, we have been manufacturing 3D-printed parts with the highest quality standards for over 2,000 customers from various industries, including machinery and plant engineering, robotics, medical technology, automotive, orthotics, and many others.
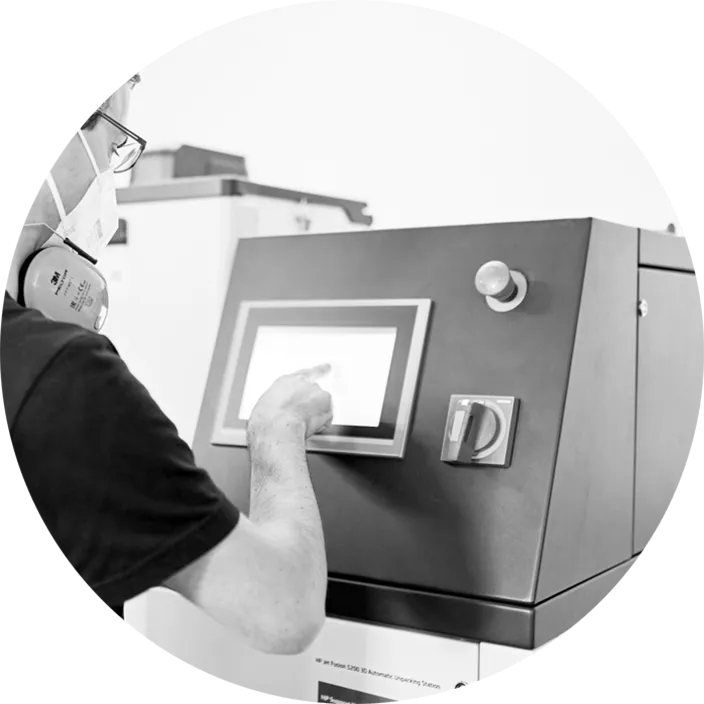
Component De-Powdering
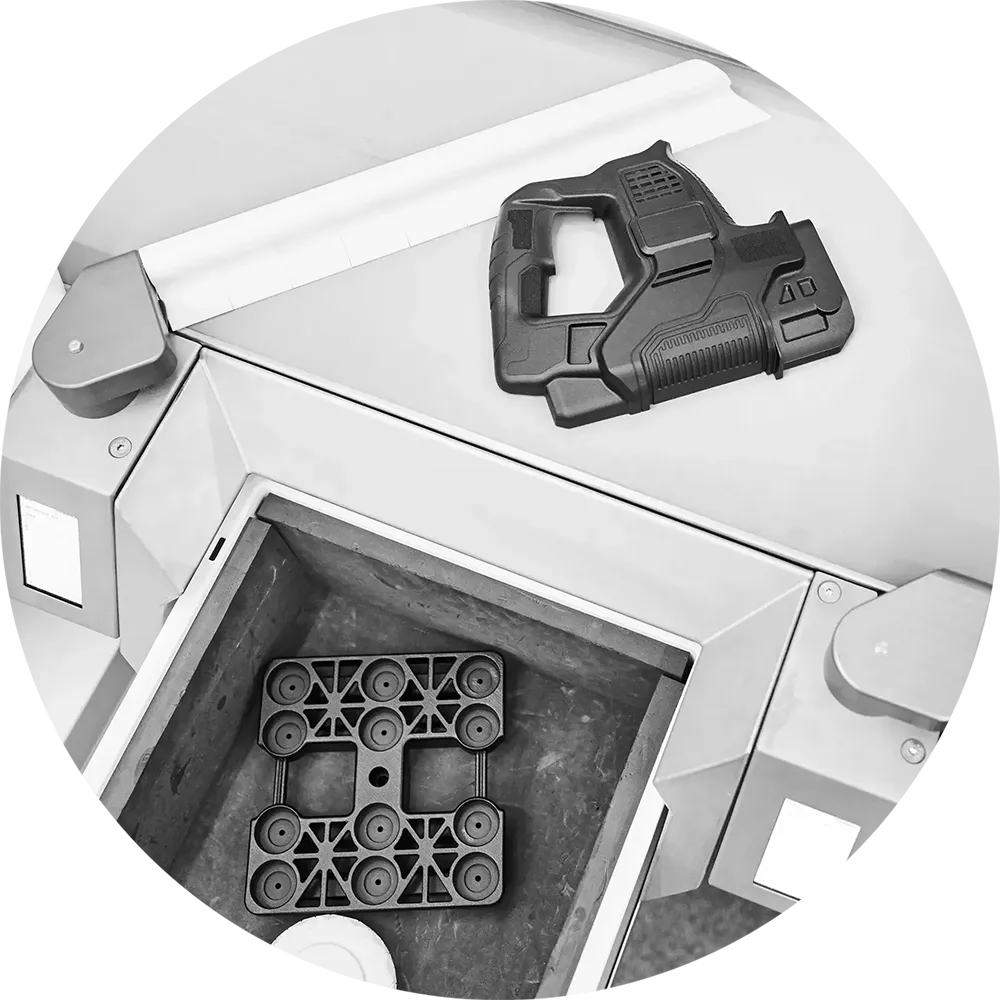
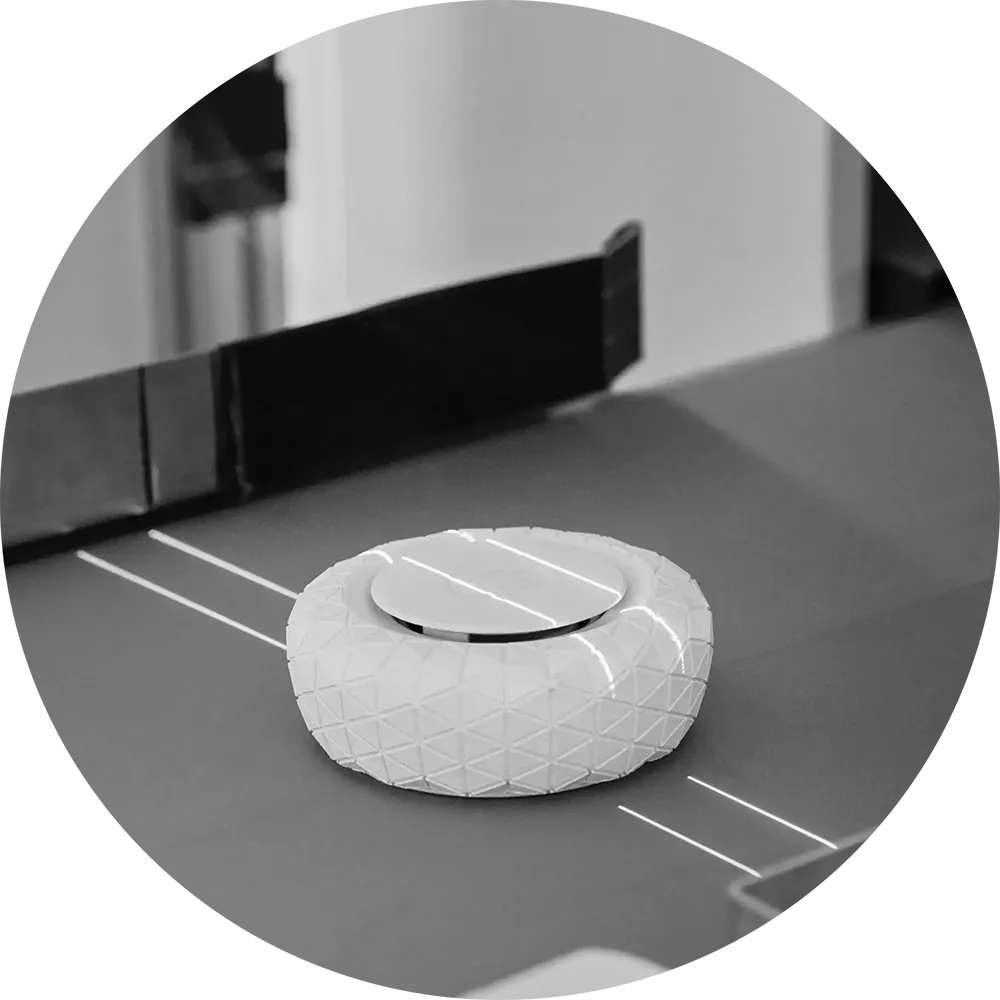
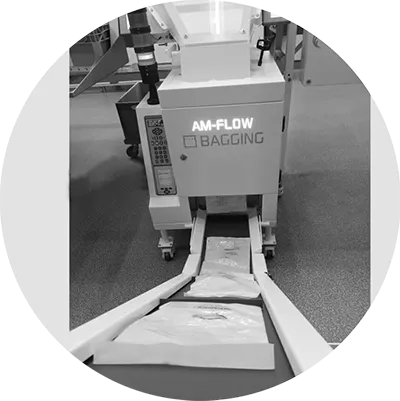
- Specialization in Additive Series Production: 3Faktur has primarily focused on additive series production. This means that all processes, technologies, and expertise are specifically tailored to this type of manufacturing. Such a focus ensures that you receive prototypes that already meet the requirements of series production.
- Highest Quality Standards at Every Step: Whether it’s a prototype or a serial product, quality is paramount at 3Faktur. This commitment is reflected in every detail and every production step.
- Maximizing Additive Advantages: If additive components play a role in your product lifecycle, we can leverage our strengths and provide you with customized solutions.
- Extensive Experience: With the experience of manufacturing hundreds of thousands of 3D-printed components annually, we are your ideal partner. Especially in industries such as industrial, automotive, healthcare, or high-quality consumer products, where quality, replicability, and precision are crucial.
Choose 3Faktur as your partner for rapid prototyping and benefit from our industry-specific expertise and unwavering focus on quality.
Further Information:
- Consultation: Contact our customer service
- How to Order with 3Faktur: Order process
- Production Technology: Learn more about the Multi Jet Fusion process
- Available Materials: Overview of materials
- Post-Processing Options: Overview of surface finishing and color options
- Helpful Links:
Design Guidelines: Comprehensive compendium on minimum requirements and optimization strategies for additive manufacturing.
Frequently Asked Questions: FAQs for technical and administrative inquiries.