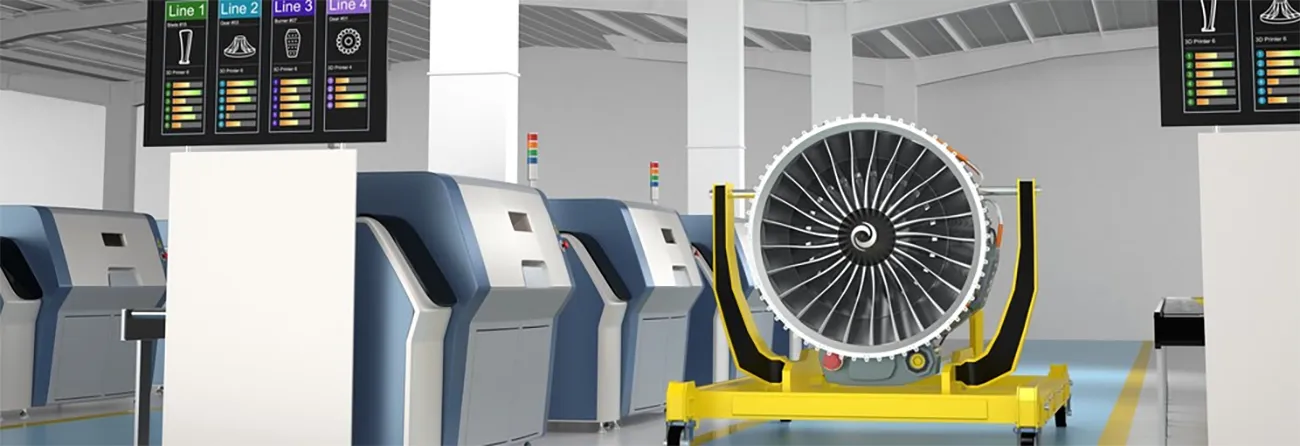
Until now, industrial manufacturing has been based on four main components: raw materials, machines/tools, production, and the principle of economies of scale. Infrastructure and time have largely been aligned with production processes. In modern manufacturing, the insights of Henry Ford have often been followed. He revolutionized mass production with the introduction of the “assembly line,” significantly reducing the production time of individual products.
With the widespread adoption of 3D printing technologies, another revolution seems to be on the horizon. 3D printing has the capability to reduce the required number of assemblies and minimize the need for welding components together, resulting in significant time savings and cost reduction.
In the following article, you can read about the impact and possibilities of 3D printing for integrated manufacturing.
What is Integrated Manufacturing?
Integrated manufacturing is the endeavor to minimize the necessary steps for producing a product. This process begins with the design/creation of a product or its components. Engineers/designers strive to 3D print the parts (even if they consist of multiple elements) as a single object, eliminating the need for assembly. The resulting savings in production time also lead to a significant reduction in production costs.
Popular examples of using 3D printing to streamline manufacturing steps include chains, undercutting components, and now gears, which can be 3D printed as a single piece.
Rethinking Production
Of course, production savings do not materialize out of thin air. Reducing production time requires increased time investment in the design/product development phase. However, this investment generally pays off. The creation of integrated assemblies is fundamentally possible with a wide range of 3D printing materials and processes. However, the process is somewhat more challenging for processes that require support structures (FFF, SLA, Polyjet) compared to powder-bed-based processes (Multi Jet Fusion, Colorjet, SLS, SLM). For the former, support structures must be removed to obtain a functional component, which needs to be considered in the part design and choice of 3D printing material.
Here are some design tips to consider (detailed guidance can be found on our material pages):
- Be clear about the physical properties your component must have.
- Find out which material possesses the required properties for your product/application.
- After selecting a 3D printing material, follow the design guidelines on the material pages.
Where 3D Printing is Already Used in Manufacturing
With the growing use of metals in 3D printing, more traditional industrial companies are also becoming interested in this technology. In the aerospace and automotive industries, a paradigm shift has already begun, with more companies adopting 3D printing to reduce development times and costs.
- Siemens was able to reduce the development time of their gas turbines by a remarkable 90% through the use of 3D printing technologies. 3D printing also allows Siemens to manufacture spare parts “on demand.” You can read more about it in Siemens’ press release.
- US-based company Local Motors has successfully produced a functional car with only 49 parts using 3D printing, whereas a traditionally manufactured car requires about 5000-6000 parts.
- General Electric managed to reduce the number of non-moving parts for a turboprop engine from 900 to 16, resulting in a weight reduction of 35%, thanks to 3D printing.
- Opel took a slightly different approach, using 3D printing for the production of tools and reducing the production costs by 90%. More information can be found here.
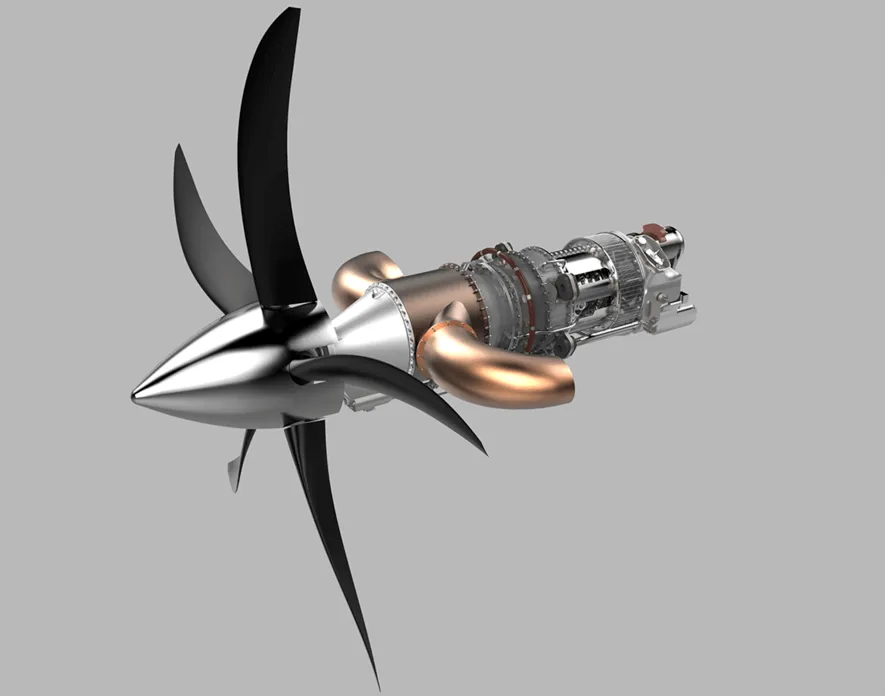
Image: Turboprop Engine/GE Aviation
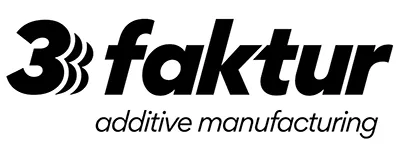
About 3Faktur: 3Faktur specializes in 3D printing, rapid prototyping, and rapid manufacturing. We utilize HP’s Multi Jet Fusion technology and offer various materials for prototyping and series production. If you have any questions about your project, feel free to contact us.