Multi Jet Fusion is a powder-based 3D printing process. Due to its high component quality, high throughput, and low unit costs, this additive manufacturing technology is particularly suitable for functional parts and (small) series components. Multi Jet Fusion enables the production of durable and resistant Polyamide 12, Polyamide 12 W, elastic TPU and flexible Polyamide 11 with short lead times, even for higher quantities.
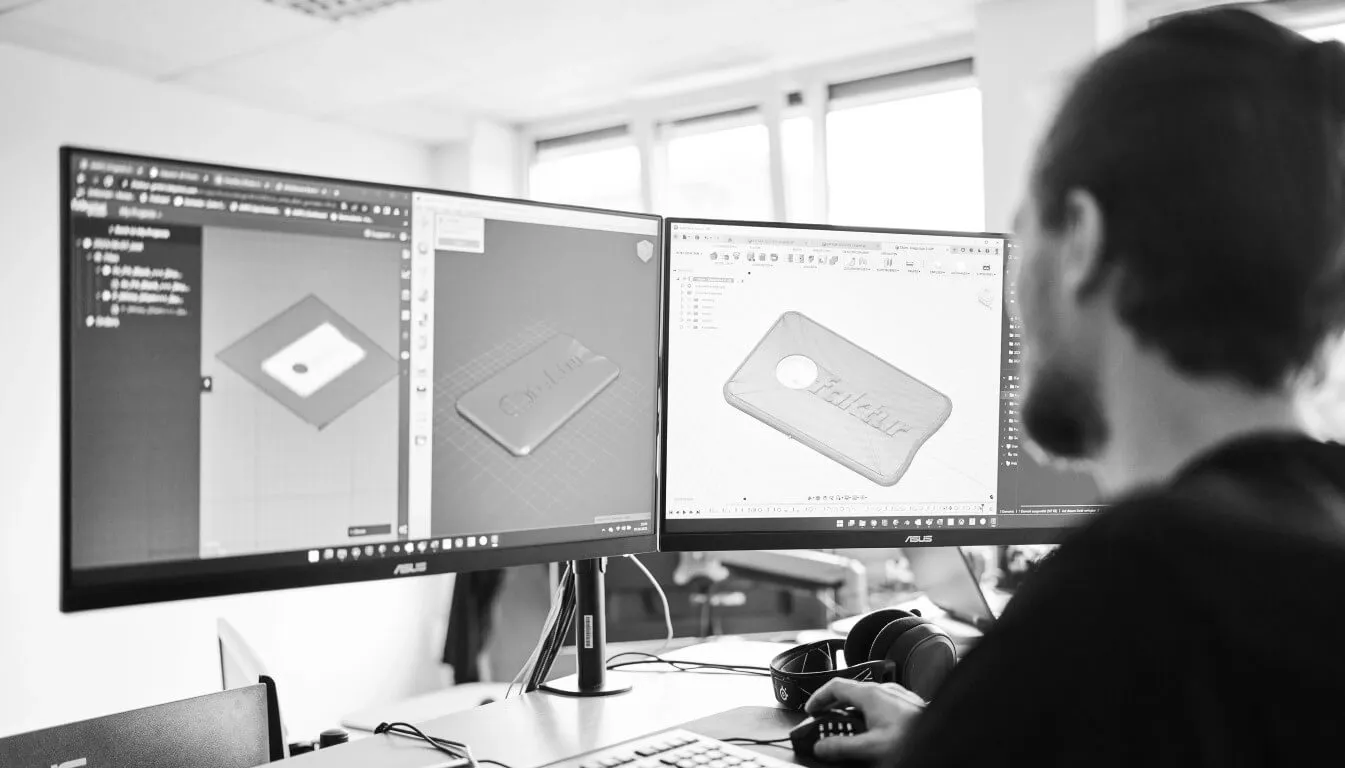

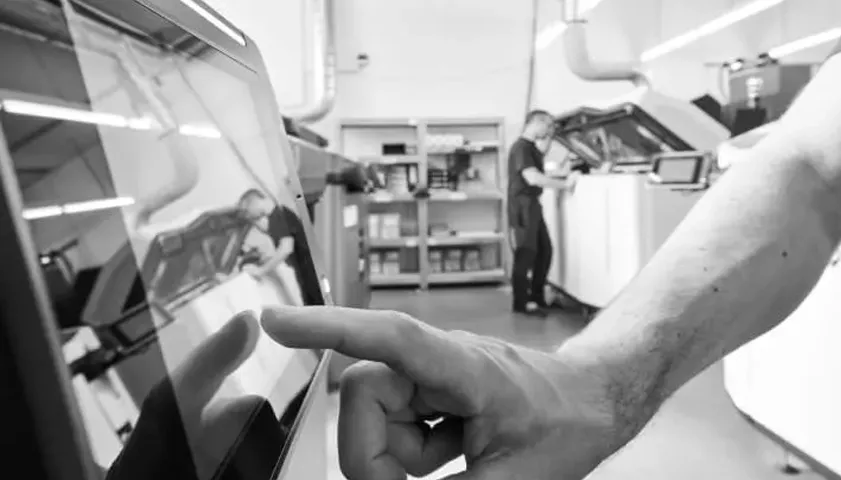
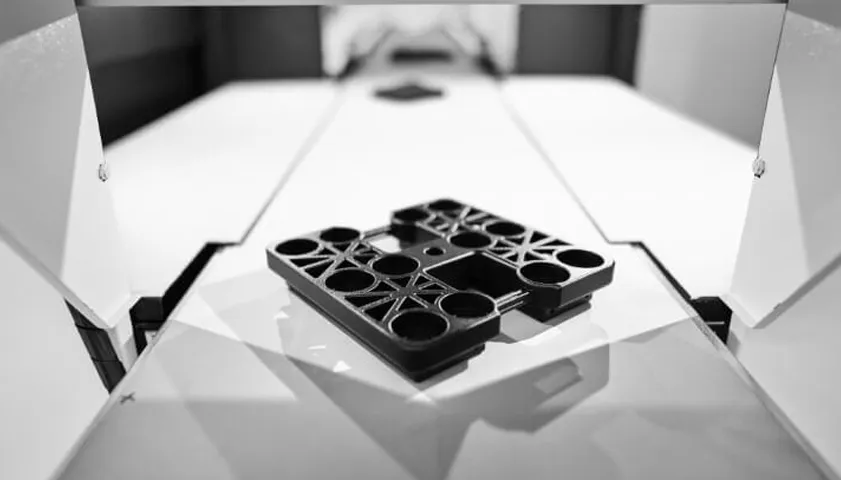
Key Information
Materials
PA 12, PA 12 W, TPU, PA 11
Colors
gray, black, white, colored
Build Volume
min. 10 mm
max. 380 mm
Production Time
Standard: 4 working days
Accuracy
dependent on material
Process Process Chain Applications Post-Processing
The Multi Jet Fusion Printing Process
Multi Jet Fusion is a powder bed-based additive manufacturing process. In the first production step, a closed powder layer is applied. The raw material is white and has an average grain size of approximately 60 µm for polyamide.
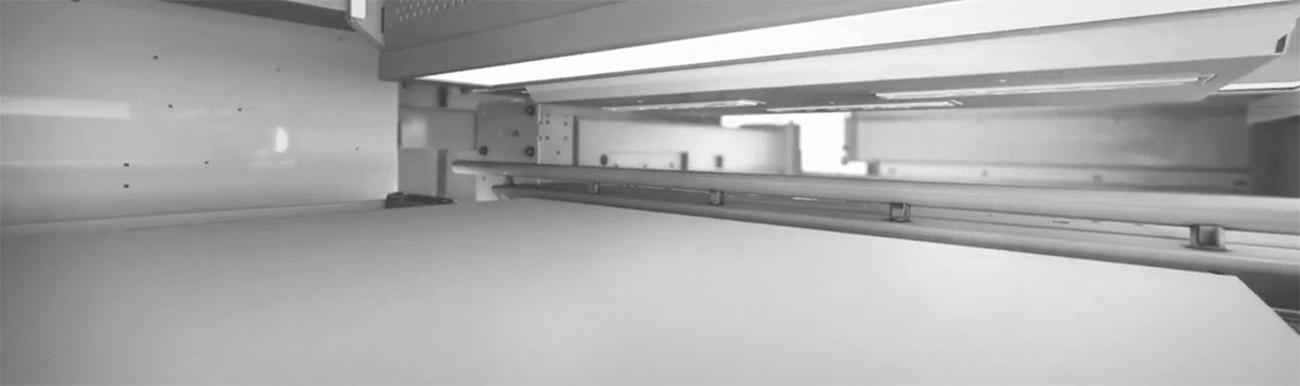
(Source: 3D printing with HP Multi Jet Fusion technology – How it works and potentials)
In the second step, the areas to be melted are printed onto the powder layer using a black liquid or ink called “fusing agent.” The print head contains integrated heat sources (infrared light) that heat the powder bed directly after the ink application. The black areas printed with the fusing agent absorb more energy than the unprinted white areas, causing them to melt and solidify once the heat source is removed.
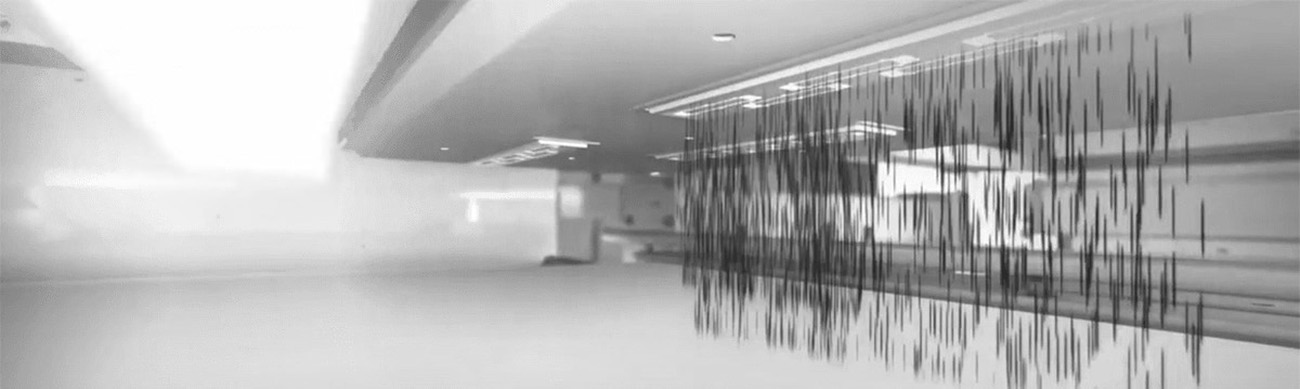
(Source: 3D printing with HP Multi Jet Fusion technology – How it works and potentials)
Another substance called the “detailing agent” is used for isolation. It is applied around the areas printed with the fusing agent. The detailing agent acts as a thermal insulator at the transition areas, maximizing detail resolution.
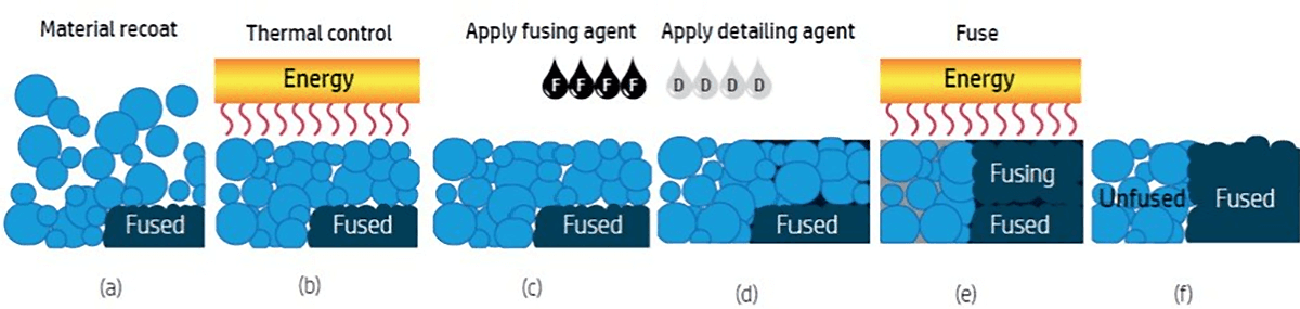
The performance of this system is remarkable. It delivers 300 million drops of liquid per second with an accuracy of 21 µm. Despite its complexity, this technology offers significant advantages:
- Isotropy: Unlike most other additive manufacturing processes, the 3D-printed objects are largely isotropic. This means that the mechanical properties of a component are (largely) independent of its direction.
- Speed: Typically, we produce 180 to 200 components in a print run of 12 hours. This makes MJF one of the most productive additive manufacturing processes, with an average of 3 to 4 minutes per component.
- Resolution: Thanks to the small droplets, the Multi Jet Fusion system achieves a resolution of 1,200 dpi along the X-Y axis. The fast printing process also enables the cost-effective use of smaller layer heights, as low as 80 µm.
- Density: The “agents” cover the entire model area and fuse uniformly. After fusion, the components have nearly 100% material density, with only the surface being slightly porous. Through surface sealing with vapor smoothing, the components can be fully sealed and used in gas and liquid handling systems.
Process Process Chain Applications Post-Processing
Process Chain
Industrial additive manufacturing involves numerous process steps before and after the actual 3D printing. Each of these steps is optimized for quality. An overview of these steps can be found on the “Certified Additive Manufacturing at 3Faktur” page.
We maintain one of the most comprehensive process chains for this technology throughout Europe. In addition to the mentioned systems, we work with numerous other components in the periphery, such as industrial climate and ventilation technology, measuring instruments, and proprietary IT systems for production control and automation of business and production processes.
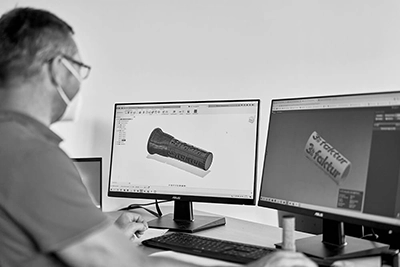
1 / Data Verification: The CAD data is individually checked for producibility, and any possible improvements are discussed with our customers.
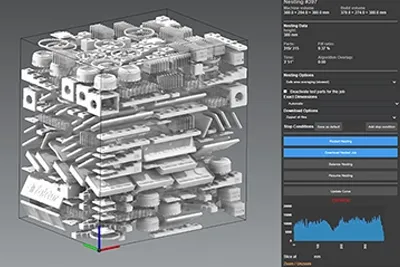
2 / Data Preparation: Each component is individually oriented, and all production steps and parameters are defined. After this process, the components are nested, meaning they are nested within each other. This creates the so-called print job, which is then transferred to the machine.
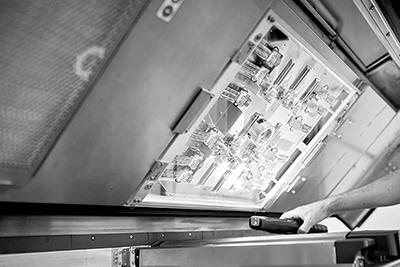
3 / 3D Printing: The actual 3D printing process takes approximately 12 to 16 hours, depending on the material and machine. We use four HP Multi Jet Fusion 3D printers (2 x 4210, 2 x 5210 und 1 x 5420 W).
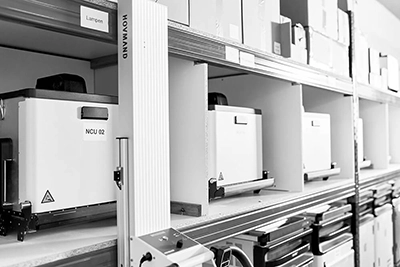
4 / Cooling Phase: After printing, the build units are removed from the printer and slowly cooled for 48 to 72 hours from temperatures above 150°C to 22°C. This reduces component damage such as shrinkage, warping, and surface defects.
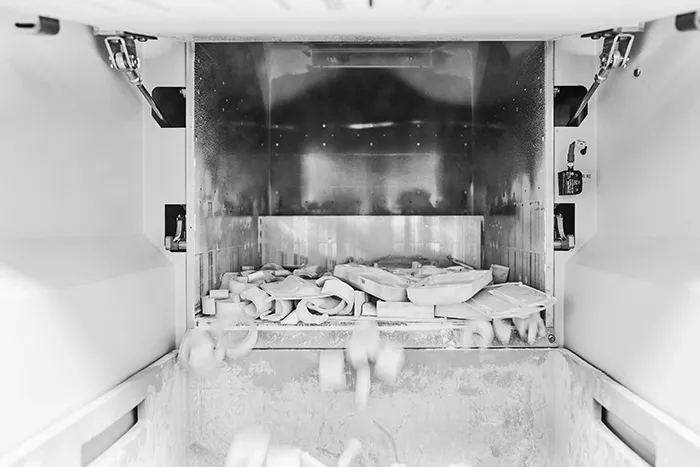
5 / Unpacking: After printing, the build chamber is filled with powder. The components need to be removed from this so-called “powder cake.” This process step is now mostly automated.

6 / Cleaning: Due to the high temperatures, residual powder is “melted” onto the components. This is mechanically and largely automated through glass bead blasting (two blasting cabinets from MHG: 1 x Cleaning SMG 160; 1 x Shot Peening SMG 50).
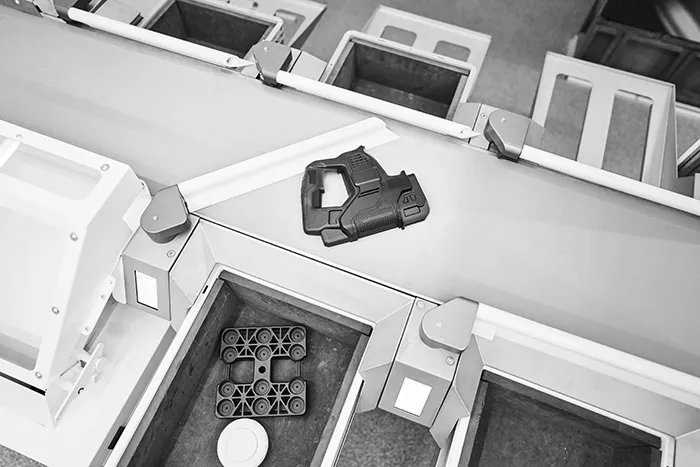
7 / Sorting: Multiple dozens to thousands of components are produced in each print job. For quality reasons, it is useful to mix different parts. Assigning them to the subsequent steps or orders after printing is a very labor-intensive process that we solve with the help of state-of-the-art AI-based automation technology (automatic component recognition, sorting, and packaging system by AM-Flow).
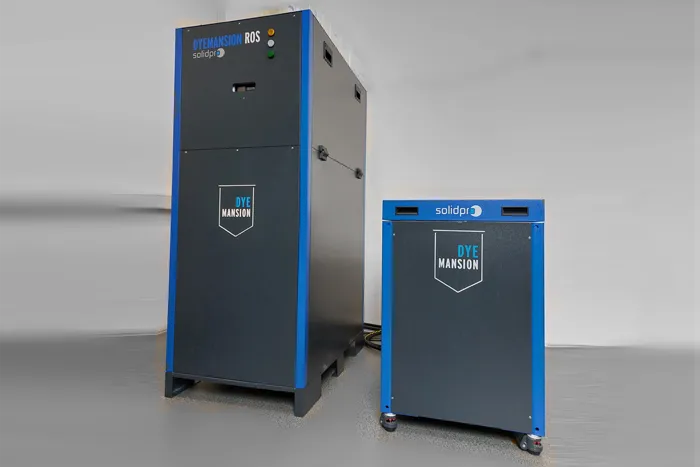
8 / [Optional] Dyeing: Black components undergo immersion dyeing. The white components (PA 12 W) are dyed in the DyeMansion system.
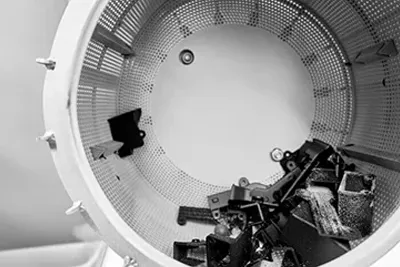
9 / [Optional] Shot Peening: All black components undergo a second blasting process with a different blasting medium that compacts the surface (“shot peening” or “shot blasting”). The process takes place in an optimized blasting cabinet, partially automated.
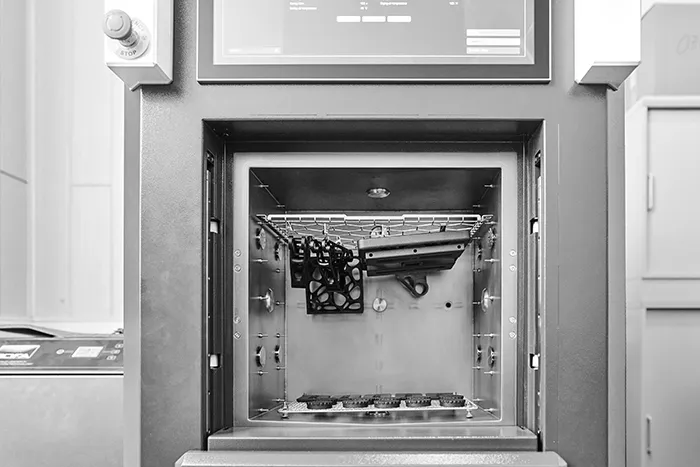
10 / [Optional] Vapor Smoothing: On request, a chemical smoothing process can be performed to obtain a smooth, pore-free surface. (AMT SF 50 vapor smoothing system).
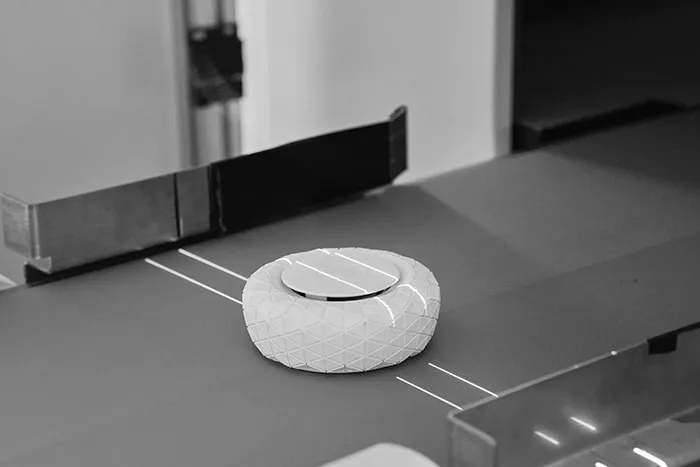
11 / Quality Control: Quality control is one of our most time-consuming processes. In addition to the actual components, process accompanying samples are produced and evaluated in each cycle. This allows us to intervene early, for example, in case of impending consumable wear, and ensures the highest possible replicability.
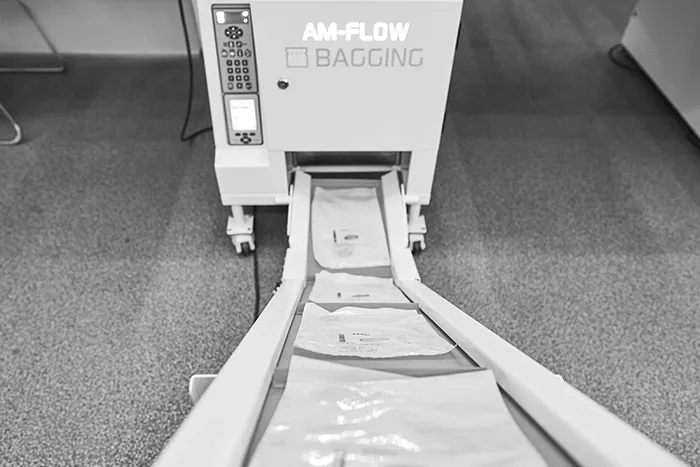
12 / Packaging & Shipping: After approval of the components, the final assignment, packaging, and shipping take place. We have also automated the assignment and part of the packaging with the “AM Bagging” system.
Process Process Chain Applications Post-Processing
Applications
Multi Jet Fusion enables the additive manufacturing of stable, durable plastic components. The applications span across all industries, including:
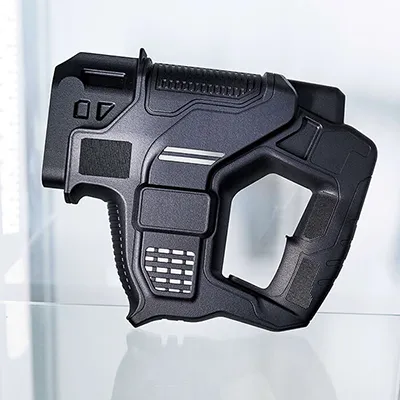
Housings
Mechanically, thermally, and chemically resistant housings can be produced quickly and efficiently.
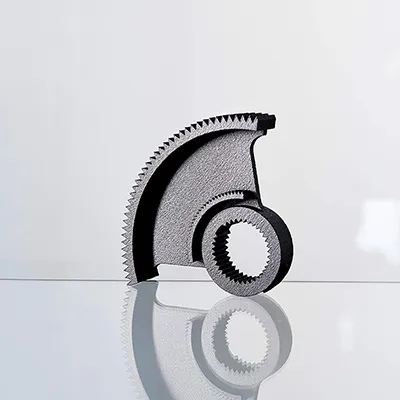
Structural Elements
Components from the “inner workings” of machines and systems can be manufactured with highly complex geometries.
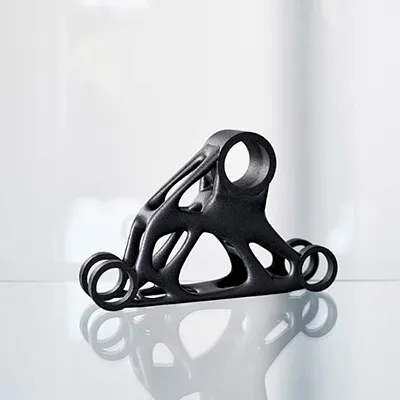
Weight-optimized or topology-optimized components
Multi Jet Fusion is ideal for lightweight construction due to the ability to print undercuts and lattice structures.
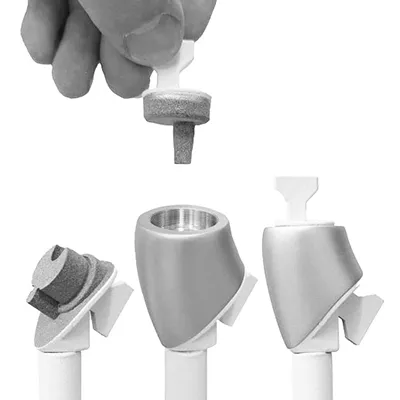
Fixtures
Stable materials with infinite geometric complexity: Multi Jet Fusion is excellent for building fixtures.
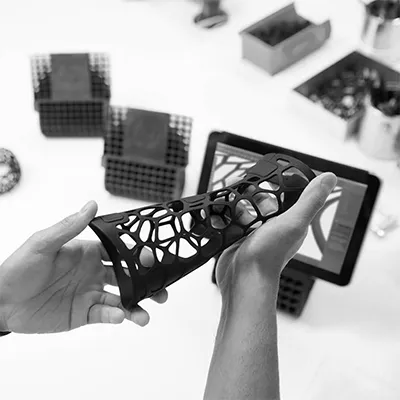
Orthoses
The TPU material, in particular, is widely used in the production of patient-specific orthoses.
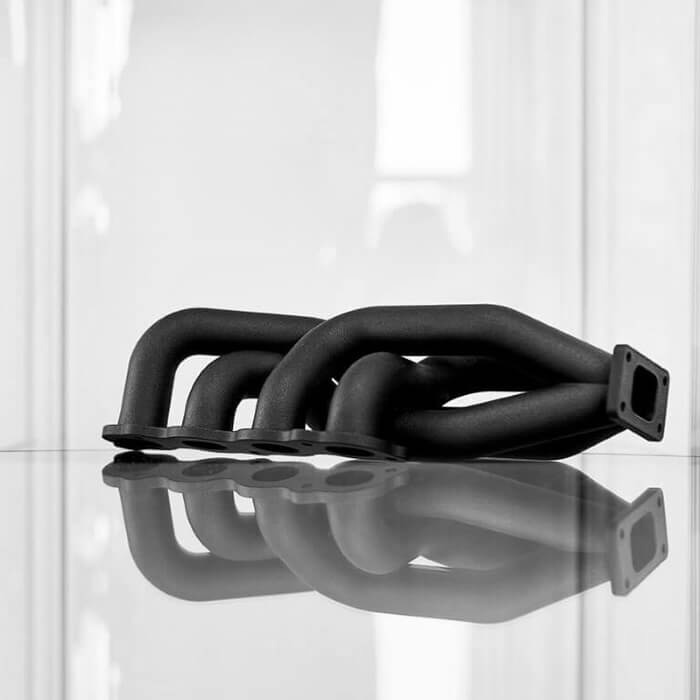
Gas and Fluid-Carrying Components
Through finishing with vapor smoothing, completely sealed components can be created.
Process Process Chain Applications Post-Processing
Post-Processing
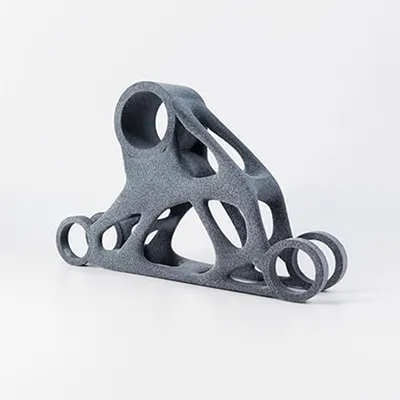
Unprocessed
Gray parts used for non-visible components.
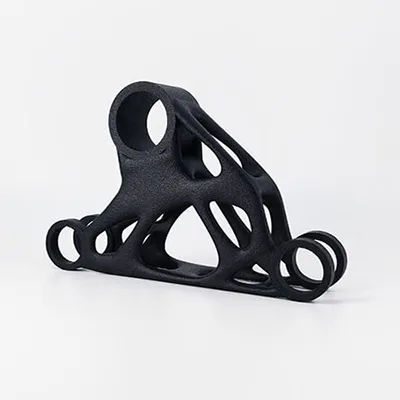
Black Dyeing & Shot Peening
Colored and surface-treated parts used primarily for visible components.
More information about Dyeing
More information about Shot Peening
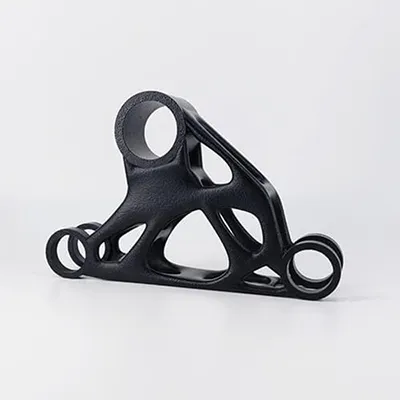
Vapor Smoothing (Chemical Smoothing)
Black dyed, chemically smoothed, and sealed surfaces for numerous applications.
More information about Vapor Smoothing