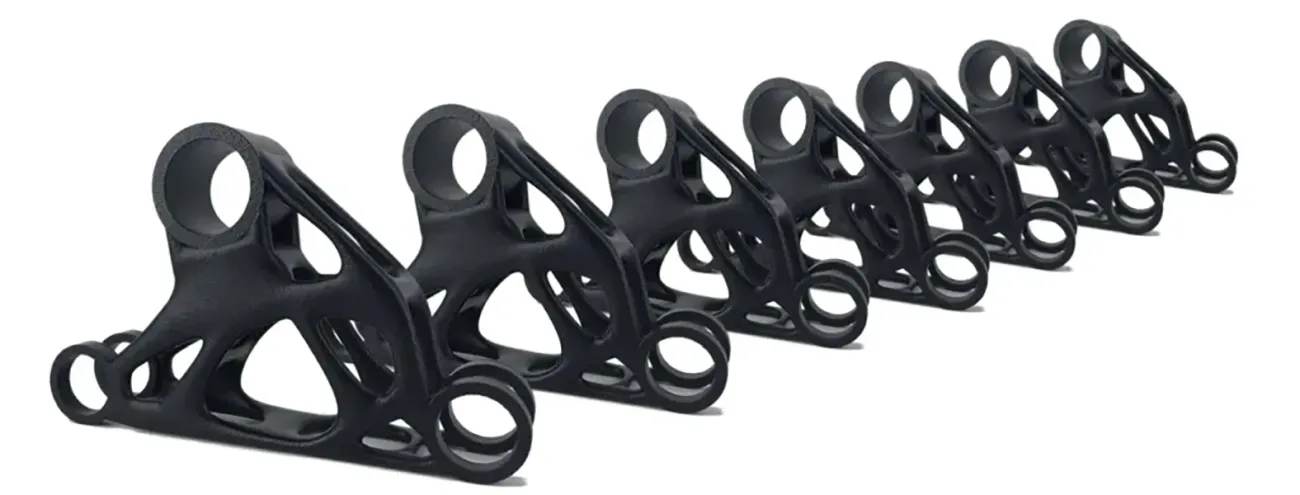
The selective laser sintering (SLS) and Multi Jet Fusion (MJF) are both polymer powder bed fusion processes. In these processes, a powdered polymer is deposited layer by layer and selectively sintered or melted at the desired locations. This creates high-quality, industrial plastic components layer by layer.
Both processes have many similarities, such as:
• Support structures are not necessary, allowing for the production of highly complex geometries
• In a single production cycle, dozens, hundreds, or even thousands of components can be produced as they can be nested together during production
• Both processes can only use semi-crystalline polymers. In practice, these are mostly polyamides, but other polymers such as TPU, TPA, or polypropylene are increasingly being used
However, there are also differences between the processes, which will be discussed in detail below.
Processes | Systems | Materials | Max. Size | Resolution | Colors | Mechanical Properties | Surface Properties | Reproducibility | Piece Cost
Processes
Selective Laser Sintering (SLS)
The laser sintering process follows a relatively simple principle: A thin layer of powder material is applied to a build platform. A laser selectively heats the specified areas in the powder bed, causing the powder particles to “sinter” together. As the material cools, it solidifies, the build platform is lowered by approximately 100 – 120 µm, and the process is repeated until the object is completed.
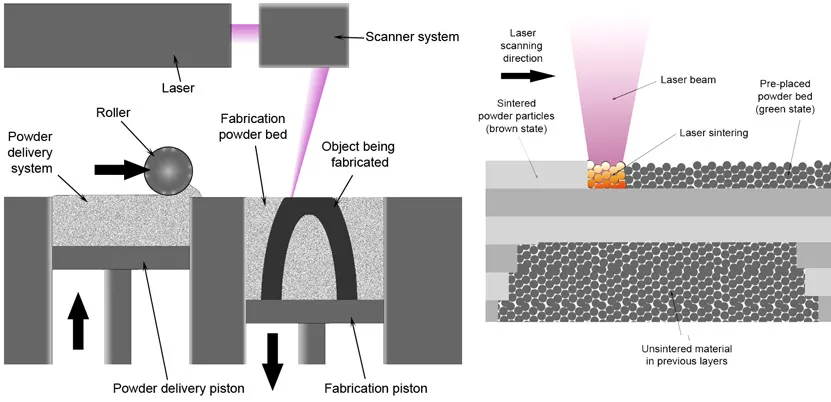
Source: By Materialgeeza – Own work, CC BY-SA 3.0, https://commons.wikimedia.org/w/index.php?curid=4032088
Multi Jet Fusion
A similarity with the laser sintering process is the application of a thin layer of powder onto the build platform. However, instead of using a laser, the Multi Jet Fusion process utilizes print heads. The nozzles of the Jet Fusion 3D printer spray a heat-conductive liquid called “fusing agent” onto the specified areas of the powder determined by the 3D model. The print heads also have heating elements that heat the areas wetted with the fusing agent more intensely than the non-wetted powder areas. As a result, the powder melts at the “printed” locations.
In addition, HP uses a “detailing agent” that is applied around the edges of the object. This agent acts as a heat insulator and prevents the remaining powder material from fusing together. This ensures increased detail fidelity.
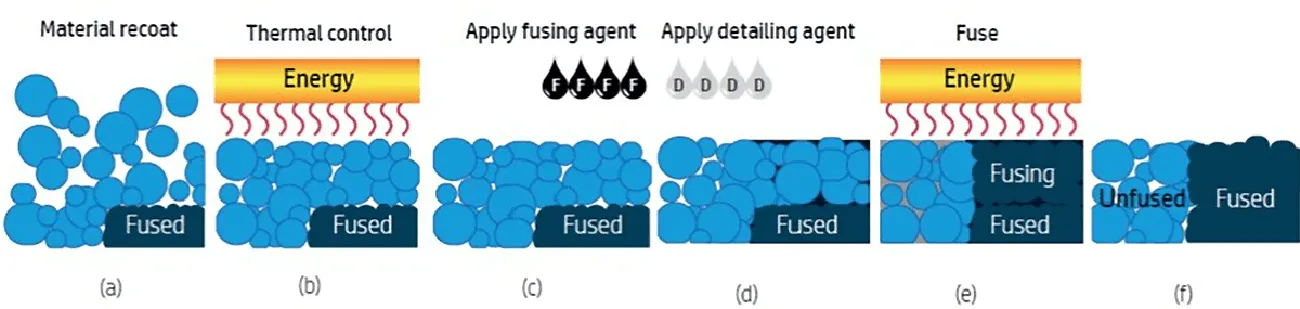
Image source: HP; HP’s White Paper on Multi Jet Fusion Technology
Systems
Selective Laser Sintering (SLS)
One of the central differences between MJF and SLS is the variety of available systems. In the field of laser sintering, there are already dozens of providers offering both industrial and semi-professional systems. The market leader in the industrial systems segment is EOS, known for widely used models such as the compact Formiga, which allows for high resolutions despite its smaller build volume (~250 mm). In addition, there are the 39x systems, which boast larger build volumes. Other industrial providers include 3D Systems, Prodways, and Farsoon. In the semi-professional sector, there are smaller devices offered by companies like Formlabs or Sintratec.
Due to the 30-year presence of this technology in the market, there is a wide variety of device technologies, including older systems. Therefore, not all “laser-sintered parts” are equal, and the quality can vary significantly from one provider to another.
Multi Jet Fusion (MJF)
With the introduction of MJF, HP was the first to enter the market and has since dominated this technology segment. There are two other providers of similar technologies: Voxeljet with the HSS process and Stratasys with the SAF process, although both are still relatively rare in the industrial environment.
MJF systems are now in their second generation. HP started with the 42 series system and introduced an advancement, the 52 series, to the market in less than four years. In terms of dimensional accuracy and mechanical properties, both systems are comparable, but the 52 series technology is significantly more powerful due to shorter production cycles.
In the past, HP also had smaller systems (540 & 580) that were capable of producing fully colored parts. However, this technology has been discontinued by HP.
Materials
Selective Laser Sintering (SLS)
Both SLS and MJF processes use semi-crystalline polymers. For more details, please refer to the Polymers for 3D Printing (only in german) page. In practice, the market is mainly dominated by polyamides, particularly polyamide 12, although polyamide 11 is also used. PA6 production is also possible with laser sintering technology, which requires higher process temperatures. For elastomers, TPU is commonly used in SLS. There are also some highly specialized materials available in the market, such as flame-retardant, ESD-compliant, or fiber-reinforced materials.
One significant advantage of SLS is that the materials can be easily exchanged, and there are “open systems” available in the market where custom materials can be tested and implemented. However, using “non-standard” materials may affect replicability.
Multi Jet Fusion (MJF)
Although the material range for Multi Jet Fusion is smaller, the advantage is that all materials are either supplied directly by HP or certified by HP through an elaborate process. This ensures outstanding material consistency. The material range includes polyamide 12, 11, TPU from Lubrizol and BASF, polypropylene from BASF, and an elastic TPA from Evonik.
Maximum Size of Produced Components
Selective Laser Sintering (SLS)
Due to the range of systems available, there is no universally applicable statement. Semi-professional systems usually have smaller build volumes, sometimes below 150 mm. On the other hand, the largest systems on the market can have build volumes of up to 1,000 mmSure! Here’s the translation:
Multi Jet Fusion (MJF)
The 42 and 52 series systems have a build volume of 380 x 284 x 380 mm.
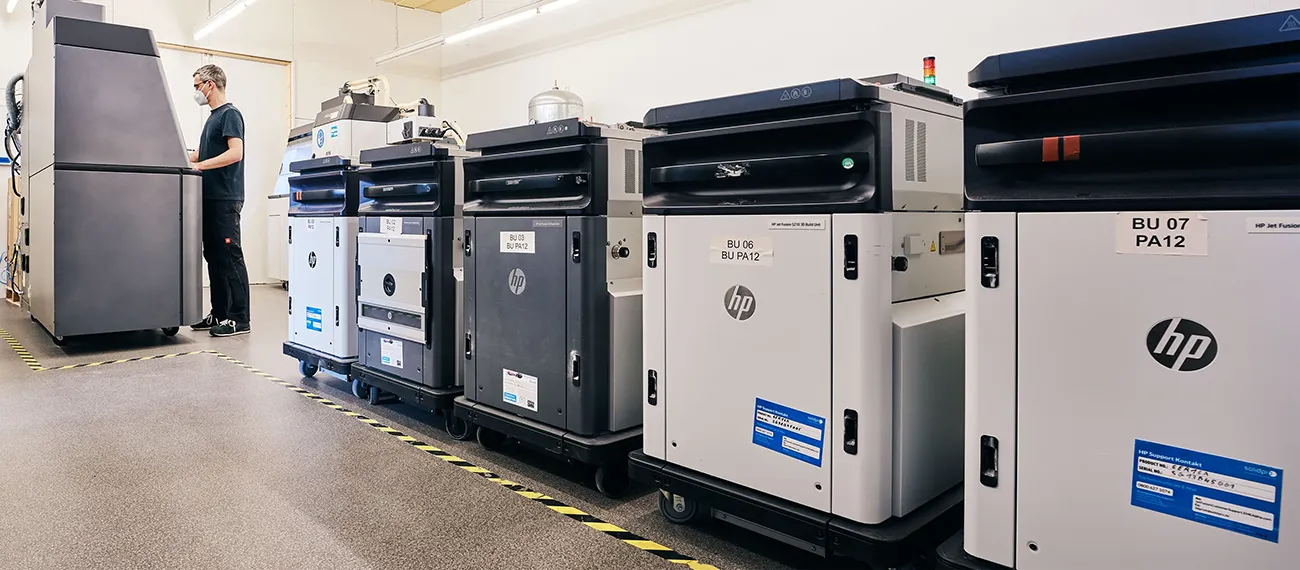
Mobile construction rooms of MJF plants at 3Faktur
Resolution
Selective Laser Sintering (SLS)
The resolution in SLS is influenced by various factors, including layer thickness, spot diameter of the laser used, laser scan strategy, and the grain size of the material. There are significant differences between individual systems. Smaller industrial systems typically offer high resolution, provided that the material allows for it. An example is the Formiga by EOS, which generally offers high resolution and can achieve very fine details in the FDR (“Fine Detail Resolution”) version. Systems with larger build volumes often use larger spot diameters and layer thicknesses to enable efficient production speeds, which may result in less optimal display of fine details or smaller components.
Multi Jet Fusion (MJF)
A significant advantage of MJF technology lies in its significantly increased production speed. This allows for reducing the layer thickness to a minimum (typically 80 µm) without compromising production efficiency. This characteristic, combined with the extremely high resolution of the print heads at 1,200 DPI, enables MJF devices to achieve levels of detail that are otherwise only attainable with the best SLS systems. The average powder grain sizes are comparable to standard SLS materials (e.g., PA2200) and typically range from 50-60 µm.
Colors
Selective Laser Sintering (SLS)
Most SLS systems print based on a white base material that can be colored after the printing process. In SLS, it is possible to dye the raw material, with black being a common choice. This color often has a technological background. For example, cost-effective laser sintering systems like Formlabs mostly use diode lasers, which require black powder as the base material. The same applies to the FLIGHT technology primarily used by Farsoon, where a fiber laser is used to enable significantly higher production speeds. Black raw material is technically advantageous for a fiber laser as well.
Multi Jet Fusion (MJF)
In the original version of the MJF process, the base material is white, while the fusing agent is black. This results in the internal parts of the components being completely black, while a slight white component remains on the surface (residual unsintered material). As a result, the components appear gray and somewhat heterogeneous. Typically, after printing, a dyeing process is performed to give the components a homogeneous color and complete blackness. Since the beginning of 2023, a new device variant, the HP 5240, also allows for the printing of fully white components. In comparison to most laser-sintered components, these components exhibit a more homogeneous white color even with thin wall thicknesses (the latter are often translucent in SLS). Additionally, they offer significantly increased stability against UV radiation, both in terms of color stability (no yellowing, as is common in SLS) and mechanical properties. This demonstrates a significantly reduced decrease in mechanical properties under UV exposure compared to common SLS materials.
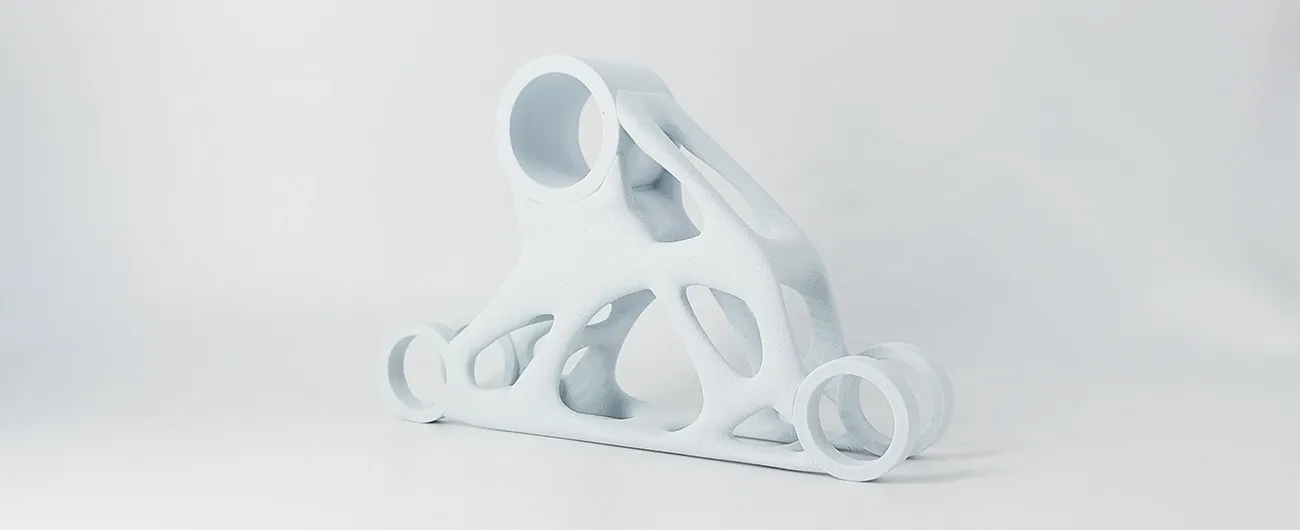
White component made of PA 12 W printed using the Multi Jet Fusion process.
Mechanical Properties of the Produced Parts
Selective Laser Sintering (SLS)
The mechanical performance of the components is strongly influenced by the material used and the equipment. In semi-professional systems where a diode laser is used, the mechanical strength of the components is often limited. Additionally, with older systems that have accumulated many operating hours, a decrease in the mechanical stability of the produced components is frequently observed.
Another SLS-specific characteristic is the high refresh rate, which refers to the ratio of new to reused raw material per printing process. In laser sintering, this value is typically 50% (i.e., a 1:1 ratio of new and recycled powder). When the proportion of new powder is reduced in production, the mechanical strength of the printed part significantly decreases.
Multi Jet Fusion (MJF)
Due to the limited number of systems and the low refresh rate of only 20%, the mechanical strength of the components remains constant. Issues can arise when users print too many components simultaneously, leading to a “high packing rate.” The resulting higher process temperature can accelerate powder aging, which also reduces the mechanical strength of the components. To avoid this problem and ensure consistent material quality, 3Faktur implements strict controls.
On average, components produced with MJF have higher material density and are therefore at the upper end of the technically achievable range, considering the same polymer.
Surface Properties of the Produced Components
Selective Laser Sintering (SLS)
The surface quality in SLS, similar to the level of detail, depends on various factors, including the material grain size and layer thickness. Coarser grain size and larger layer thickness can result in inferior surface quality. This is highly dependent on the specific system and material used. Good surface quality can also be achieved at lower process temperatures, although it may lead to reduced mechanical properties. This is sometimes the case with very cost-effective systems: the components may “look good,” but they exhibit reduced durability.
Multi Jet Fusion (MJF)
The surface quality in MJF is consistently high and represents the upper limit of what is achievable in powder-based printing. This is due to factors such as the fine grain size of the powder used, the high resolution of the print heads, and the thin layer thickness.
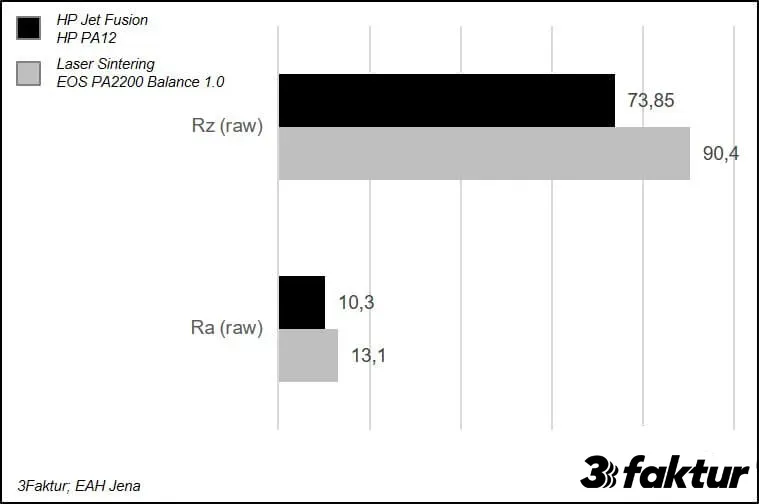
Source: 3Faktur & Ernst-Abbe University Jena
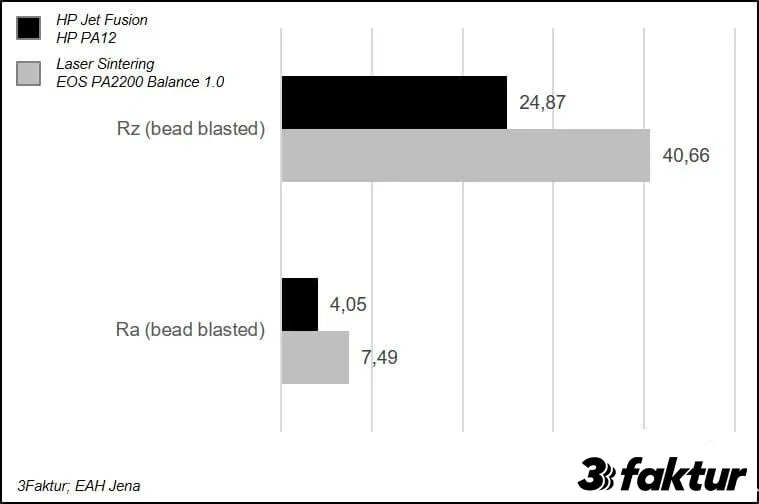
Source: 3Faktur & Ernst-Abbe University Jena
Reproducibility of Production
Selective Laser Sintering (SLS)
In high-priced, industrial-grade systems from reputable manufacturers such as EOS, reproducibility is ensured. However, with cheaper or older systems, the quality can vary significantly.
Multi Jet Fusion (MJF)
The MJF process was designed by HP for industrial production rather than prototyping. Therefore, high reproducibility is achieved with well-maintained equipment.
Unit Costs
Selective Laser Sintering (SLS)
As with all other factors, a consideration of the system/material combination is necessary here. Lower prices may indicate the following situations:
• System age: Older, fully depreciated systems can often produce at a very low cost. However, depending on maintenance and laser lifespan, the quality and/or reproducibility of results may be compromised.
• System quality: The use of sub-industrial systems or systems from lesser-known or niche providers can also offer lower prices. However, the quality should be carefully evaluated as it may not meet industrial standards.
• Material quality: Opting for material from niche providers or a lower refresh rate can result in cost savings at the expense of part quality.
With modern, well-maintained industrial systems and common materials such as PA2200 from EOS or DuraForm from 3D Systems, and using recommended refresh rates, high quality can be achieved. However, there may be cost disadvantages with the SLS process:
• Depreciation: The cost of the systems is often similar to that of MJF systems. However, the printing speed is reduced, leading to higher depreciation per part.
• Refresh rate: While the MJF process requires only 20% new powder per print, the SLS process uses 50%. Therefore, the material cost per print is significantly higher. SLS benefits from the ability to achieve a higher packing density, but this usually cannot compensate for the additional powder cost.
Multi Jet Fusion (MJF)
Due to the high performance of the 3D printer, extensive and partly automated processes in the MJF method, as well as low material consumption, this process usually offers cost advantages compared to similar SLS systems.
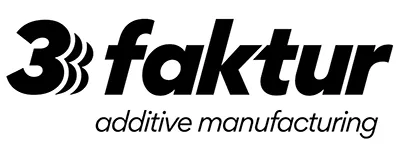
About 3Faktur: 3Faktur specializes in 3D printing, rapid prototyping, and rapid manufacturing. We utilize HP’s Multi Jet Fusion technology and offer various materials for prototyping and series production. If you have any questions about your project, feel free to contact us.